Check Valve Installation
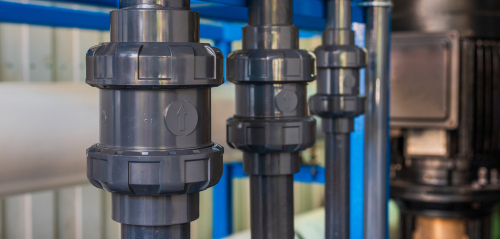
Figure 1: Check valve
Check valves are installed in critical locations to prevent backflow. They are commonly used in plumbing systems to prevent fluid backflow and to protect sensitive equipment, compressors, pipes, and pumps. However, these check valves cannot function properly if they are installed incorrectly. Installation errors can lead to valve leakage and failure, compromising the integrity of the entire piping system. This article discusses the check valve’s installation position and process in detail.
Table of contents
- Check valve purpose
- Check valve installation guidelines
- Check valve installation in vertical pipe runs
- How to install a check valve
- Check valve maintenance
- How to fix check valves
- FAQs
View our online selection of check & ball valves!
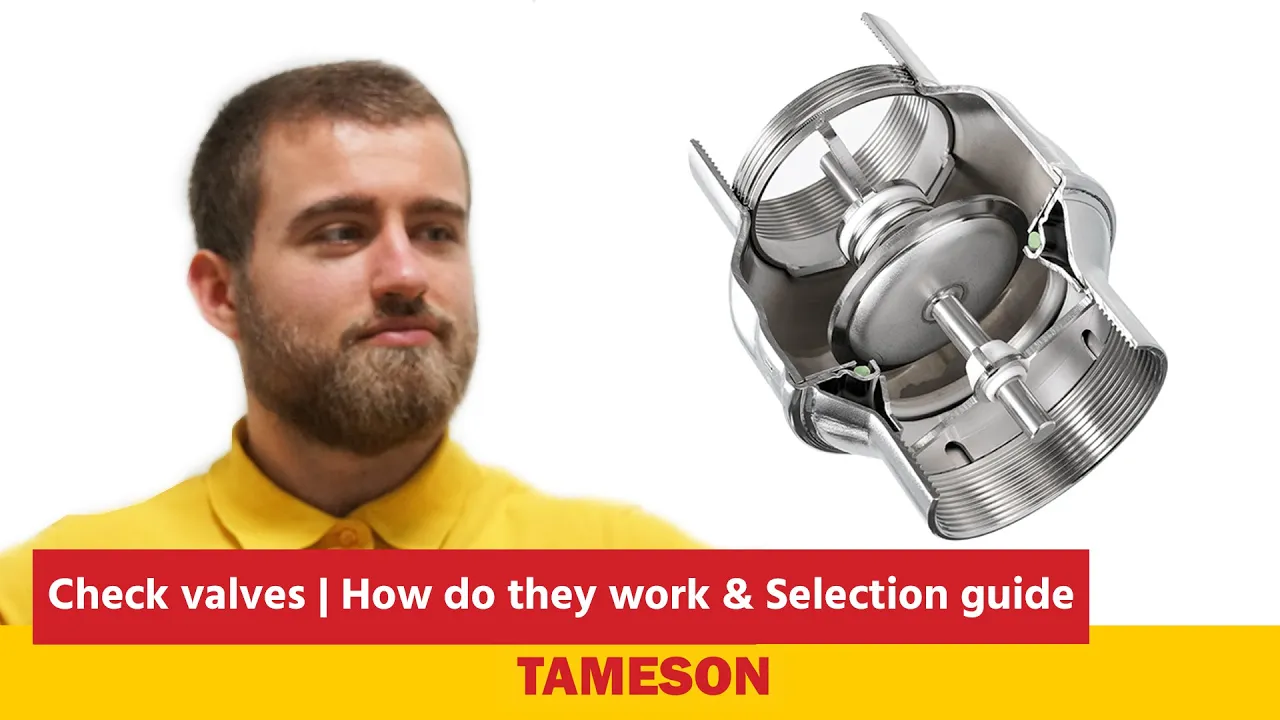
Check valve purpose
A check valve lets the media pass through in one direction but prevents its flow in the opposite direction. Installing the right check valve can prevent serious issues like water hammers and safeguard the entire process and equipment installed in piping. One of the most common residential examples of check valve installation is for plumbing. A check valve will allow dirty water or sewage to leave the residence through pipes, but prevent it from coming back up from the main discharge back into the house.
Table 1: Comparison of Different Check Valves
Feature/Criteria | Lift check valves | Swing check valves | Spring-loaded check valves | Ball check valves | Y-shape check valves | Sanitary check valves |
---|---|---|---|---|---|---|
Operation | Disc lifted by fluid flow, closes by gravity or back pressure | Hinged disc swings open with flow, closes when flow reverses | Spring mechanism compresses to open, expands to close | Ball moves away from seat to allow flow, returns to seat to block reverse flow | Y-shaped body with disc | Designed for hygienic applications, often with a spring-loaded disc |
Advantages | Good sealing for high-pressure applications | Low pressure drop Suitable for fluids with suspended solids | Fast response to flow changes Can be installed in any orientation | Simple design, reliable operation Can handle viscous fluids | Compact design Low pressure drop | Easy to clean Suitable for food and pharmaceutical industries |
Limitations | Lift check valve pressure drop is higher due to disc lifting Limited to horizontal installation Sensitive to debris, which can obstruct disc movement | Generally limited to horizontal installation Slower response, allowing potential backflow before sealing | Higher cost due to spring mechanism Potential for spring wear in high-cycling applications | May not seal well with low back pressure Limited to certain orientations | Not suitable for high-pressure applications Limited to specific flow conditions | Higher cost Requires regular maintenance to ensure hygiene |
Ideal applications | Clean fluid systems with consistent flow | Water and wastewater systems with large volumes and suspended solids | Systems requiring quick response and versatile installation | Pumping systems, wastewater applications | Low-pressure steam and gas systems | Food, beverage, and pharmaceutical processing |
Installation flexibility | Limited (horizontal only) | Limited (primarily horizontal) | High (any orientation) | Moderate (depends on design) | Moderate (depends on design) | High (often designed for easy disassembly) |
Cost | Moderate | Low | Higher | Low to moderate | Moderate | Higher |
Maintenance | Low to moderate, depending on debris exposure | Low | Moderate to high, due to potential spring wear | Low | Low to moderate | Moderate to high, due to hygiene requirements |
Check valve installation guidelines
It is critical to employ the best practices for check valve installation to reap the full benefits of the valve. Mistakes during installation can reduce the efficiency of the valve or even cause substantial damage to the equipment. Some key factors to check are:
- Selection: Choose the check valve according to the pipe’s size, media compliance, and flow rate. Choosing the wrong valve can result in premature wear and tear and component failure.
- Positioning: Keep an eye on where the check valve is installed within the piping. Always ensure that the valve is approximately five pipe diameters away from tees, elbows, or other valves that can cause turbulence. As discussed in the next section, all check valves may not function in a vertical piping run.
- Orientation: Note the arrow on the check valve that points towards media flow. The arrow indicates the proper positioning of the check valve relative to the pipe’s flow, as seen in Figure 2. The arrow is normally printed on a separate tag or permanently marked on the valve body.
- Pipeline level: Tilting disk and swing check valves have their seating surfaces machined on a 5-degree inclined plane relative to the valve centerline. If the pipeline angle exceeds 5 degrees, the disk may not touch the seat, so the check valve may leak. However, axial flow check valves do not have this problem as they function through an internal spring.
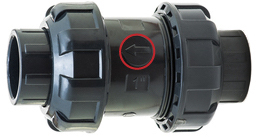
Figure 2: Check valve; The highlighted arrow shows the direction of media flow
Check valve installation in vertical pipe runs
A horizontal pipe is always preferred while installing a check valve as it rules out the effect of gravity. Not all check valve styles are suitable for vertical flow directions. There are several applications within buildings and towers, where several applications like sump pumps and mine dewatering require vertical runs to move the fluid vertically up or down.
Swing (flapper) check valve installation
If a swing check valve is installed on a vertical pipe where the flow is upwards against gravity, the disk may slam against the seat when the flow stops, potentially leading to water hammer. If the flow is downwards as in the case of boiler supply lines and mining applications with limited spacing, the swing check valve will always be open and hence does not deliver its function. Therefore, swing check valves are not preferred in vertical pipe runs and these valves are installed horizontally in most cases.
Spring-assisted check valve installation
Spring-assisted axial-flow silent check valves perform well in vertical piping locations. These valves depend on the spring’s potential energy to close the valve. Therefore, the valve closes independently without waiting for the fluid to force its way back into the piping. The strong spring of an axial flow check valve ensures the valve closes before the reverse flow happens, thereby eliminating the water hammer; hence, axial flow check valves are preferred in vertical pipe runs.
How to install a check valve
Valve size and type
Measure the pipe to which the check valve is to be attached and get a check valve that fits the diameter. Also, select a check valve type according to the application. There are threaded valves, socket valves, and various materials like PVC, brass, and stainless steel used to manufacture the valve.
Check valve and pipe evaluation
Look inside the valve and check for foreign particles within the valve as these particles can obstruct the smooth flow of media through the valve. Check uneven edges, scratches, or anything that could prevent the check valve from sealing properly. For example, in the case of swing valves, move the flapper by pushing it away from the seating surface to ensure it moves freely. Also, ensure that the pipes are clean and free of debris before installing the check valve.
Check valve placement
An arrow on the valve indicates the flow direction; hence, position the valve accordingly on the pipeline (horizontal or vertical). Ensure that the main water supply is turned off during the check valve installation process.
Attaching the check valve
Attach the check valve to the pipeline. Depending on the check valve type, it can be either screwed to the pipe or simply secured together using a wrench until the parts are sturdy and secure.
Testing the check valve
Turn on the main water supply and let the fluid pass through the installed check valve to test its functionality. If the water gets blocked during testing, double-check the direction in which the valve is installed. If the check valve leaks or any other issue comes to the surface, the user can troubleshoot using the tips mentioned in the next section.
Check valve maintenance
Check valves do not require much maintenance, but they can be kept working more effectively by checking them consistently for leaks, rust, debris, and optimum flow.
- Clean the check valve thoroughly when it is ready for maintenance; The cleaner, the better.
- Lubricating the check valve surface and rotating it slightly can keep it working optimally for an extended period.
- Try to abide by the valve manufacturer’s valve maintenance instructions. This is particularly helpful if the manufacturer has special requirements.
How to fix check valves
Check valve leaking
Loose bolts or a damaged gasket can cause a check valve to leak from the surface. Tighten the bolts and check if that solves the problem. If not, replace the gasket on the valve.
If the check valve leaks water in a closed position, it indicates damage inside the valve. In this case, clean the internal parts and check for damage. If there is damage to the flap, spring, or ball (depending on the type of check valve used), try replacing the specific part as needed. If there is damage to the valve body, replace the entire check valve.
Check valve doesn’t open
If the check valve doesn’t open, it may be due to some kind of obstruction within the valve. In this case, uninstall the valve and disassemble the valve to evaluate it. Cleaning the valve thoroughly should clean the debris and allow the water to pass through.
FAQs
Is it necessary to install a check valve?
Yes, a check valve is necessary to prevent backflow at various locations within a piping system.
How to install a check valve?
A check valve can be either screwed to the pipe or simply secured together using a wrench until the parts are sturdy and secure.
Can a check valve be installed horizontally?
Yes, a check valve can be installed in both vertical and horizontal pipe runs. However, swing check valves are preferred only in horizontal pipe runs, whereas spring-assisted check valves can be installed in both pipe configurations.