Check Valve Materials
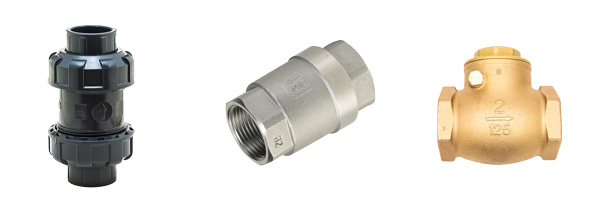
Figure 1: Check valves come in many materials including plastic (left), stainless steel (middle), and brass (right).
The material for check valves is crucial as it affects their performance, durability, and suitability for specific applications. These valves are essential components in various fluid systems. They allow fluid flow in one direction while preventing backflow. This article explores the different materials used in check valves and offers guidance on selecting the appropriate material.
Note: The inner components (e.g., disc and spring) are not always made of the same material as the body. Remember this when selecting a valve to ensure the internal component materials will be suitable for the application. Read more about compatibility in our chemical resistance of materials guide.
Learn more about check valves in our check valve overview article.
Table of contents
View our online selection of check valves!
Body materials
Stainless steel check valves
Stainless steel check valves are favored for their excellent corrosion resistance, strength, and durability. They are particularly well-suited for harsh environments and applications involving corrosive fluids. For valves, stainless steel 304 or 316 are typically used.
304 vs 316
-
304 stainless steel
- Applications: Commonly used in general-purpose applications, including food processing, brewing, and water treatment.
- Advantages: Offers good corrosion resistance and strength at a relatively lower cost.
- Limitations: Less resistant to chlorides and saline environments compared to 316 stainless steel.
-
316 stainless steel
- Applications: Ideal for marine environments, chemical processing, and pharmaceutical industries.
- Advantages: Enhanced corrosion resistance, especially against chlorides and industrial solvents.
- Limitations: Higher cost compared to 304 stainless steel.
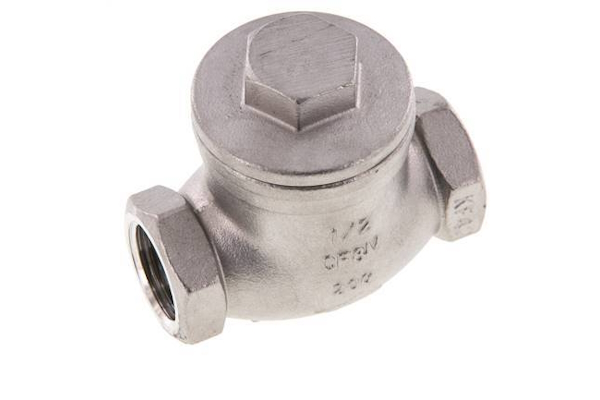
Figure 2: A stainless steel swing check valve
Steel check valves
Steel check valves are known for their high strength and ability to withstand high pressures. They are often used in industrial applications where durability is critical.
- Applications: Used in oil and gas, power generation, and high-pressure steam systems.
- Advantages: High strength and cost-effective for non-corrosive environments.
- Limitations: May require protective coatings to prevent rust and are not suitable for corrosive environments without such coatings.
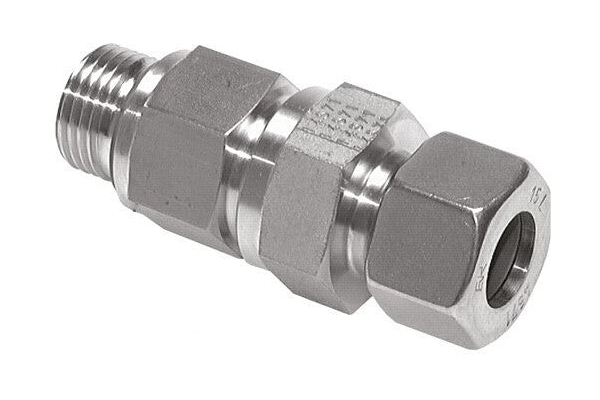
Figure 3: A steel check valve with cutting ring connections.
Brass check valves
Brass is a versatile material for check valves, providing good corrosion resistance. It is commonly used in plumbing and water systems.
Types of brass
-
Standard brass
- Applications: Used in water systems, HVAC, and low-pressure applications.
- Advantages: Good corrosion resistance and easy to machine.
- Limitations: Not suitable for highly corrosive environments or high-pressure applications.
-
Chromed brass
- Applications: Decorative plumbing and fixtures.
- Advantages: Enhanced corrosion resistance and aesthetic appeal.
- Limitations: Primarily used for aesthetic purposes, not for high-pressure or highly corrosive environments.
-
Red brass
- Applications: Potable water systems and applications requiring higher corrosion resistance.
- Advantages: Improved corrosion resistance due to higher copper content.
- Limitations: More expensive than standard brass.
-
Nickel-plated brass
- Applications: Functional and decorative applications, including plumbing and fixtures.
- Advantages: Additional corrosion resistance and a shiny finish.
- Limitations: Primarily used for aesthetic purposes, not for high-pressure or highly corrosive environments.
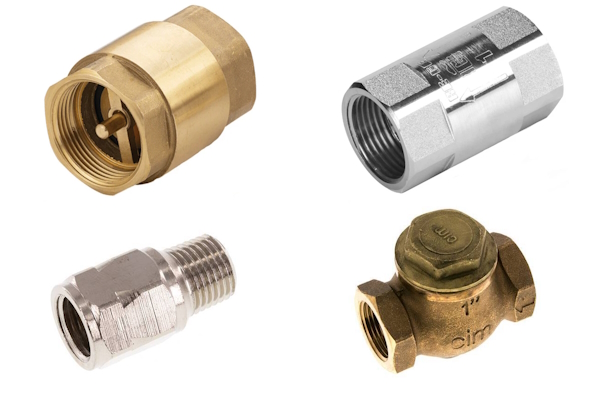
Figure 4: There are different types of brass check valves: standard brass (top left), chromed brass (top right), nickel-plated brass (bottom left), and red brass (bottom right).
Plastic check valves
Plastic check valves offer a cost-effective and versatile solution for various applications. Their lightweight design and resistance to corrosion make them ideal for use in environments where metal valves might fail.
Types of plastic
-
PVC (polyvinyl chloride)
- Temperature range: PVC check valves are generally suitable for temperatures up to about 60 °C (140 °F).
- Applications: In addition to water and wastewater applications, PVC check valves are commonly used in irrigation systems, aquariums, and swimming pools.
- Advantages: They are lightweight, easy to install, and have a long service life in non-extreme conditions.
- Limitations: PVC can become brittle at low temperatures and is not suitable for applications involving high temperatures or pressures.
-
Polyamide (nylon)
- Temperature range: Nylon check valves can typically withstand temperatures up to 90 °C (194 °F).
- Applications: These valves are used in automotive, industrial, and consumer products where durability and impact resistance are important.
- Advantages: Nylon is known for its toughness, wear resistance, and ability to withstand repeated stress.
- Limitations: Nylon can absorb moisture, which may affect its mechanical properties over time.
-
Polypropylene
- Temperature range: Polypropylene check valves can handle temperatures up to 82 °C (180 °F).
- Polypropylene check valves rated with FDA approval can only handle temperatures up to 40 °C (104 °F)
- Applications: Due to their inert nature, they are ideal for chemical processing, laboratory equipment, and food and beverage industries.
- Advantages: Polypropylene is resistant to a wide range of acids, bases, and solvents, making it suitable for corrosive environments.
- Limitations: It has a lower impact strength compared to other plastics.
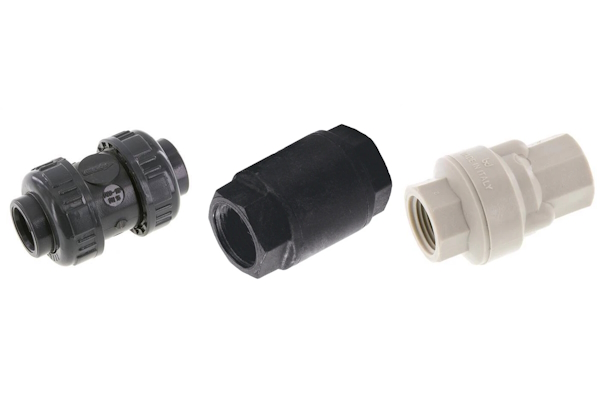
Figure 5: Plastic check valves: pvc (left), polyamide (middle), and polypropylene (right).
Body material comparison and selection guide
Check valves of different materials can be suitable for the same application. Table 1 provides some guidance on different application types and what materials can be used for them.
Table 1: Selecting material based on key application factors
Application need | Recommended material | Key features |
Corrosive environments |
Stainless steel (316) | Enhanced corrosion resistance, ideal for marine, chemical, and pharmaceutical industries. |
Stainless steel (304) | Good corrosion resistance for general-purpose applications like food processing and water treatment. | |
Red brass | Higher corrosion resistance for potable water systems. | |
Polypropylene | Resistant to acids, bases, and solvents, suitable for chemical processing and labs. | |
High-pressure applications |
Steel | High strength, cost-effective for oil, gas, and power generation in non-corrosive environments. |
Stainless steel (316) | Suitable for high-pressure applications needing corrosion resistance. | |
General plumbing/water |
Brass (standard) | Good corrosion resistance and machinability for water systems and HVAC. |
PVC | Lightweight, easy installation for water, wastewater, and irrigation systems. | |
Aesthetic/Decorative |
Chromed brass | Enhanced corrosion resistance and aesthetic appeal for decorative plumbing. |
Nickel-plated brass | Shiny finish and additional corrosion resistance for decorative applications. | |
Temperature sensitive |
Nylon (polyamide) | Durable and impact-resistant, withstands up to 90 °C (194 °F), suitable for automotive and industrial. |
Polypropylene | Handles up to 82 °C (180 °F), ideal for food and beverage industries. | |
Cost-effective solutions |
Plastic (PVC) | Cost-effective for non-extreme conditions, ideal where metal valves might fail due to corrosion. |
Steel | Cost-effective for high-pressure applications in non-corrosive environments. | |
Brass | Brass is more cost effective than stainless steel |
Seal materials
Table 2 provides an overview of the common seal materials used with check valves. It's important to note that the seal material's temperature rating is typically what controls the overall valve's temperature rating. This is because seals typically have lower temperature ratings than the body materials. However, in the case of plastic check valves, it's likely that the body material will control the valve's overall temperature rating.
Table 2: Common materials for check valve seals
Seal material | Explanation | Used with body material(s) |
EPDM | Suitable for water, steam, and some chemicals; temperature range: -40 °C to 150 °C (-40 °F to 302 °F) | Standard brass, stainless steel 304, pvc, polypropylene |
NBR (Nitrile) | Good for oils and fuels; temperature range: -30 °C to 120 °C (-22 °F to 248 °F) | Standard brass, nickel-plated brass, chromed brass, stainless steel 304, steel, polyamide |
FKM (Viton) | Excellent chemical resistance and high-temperature stability; temperature range: -20 °C to 200 °C (-4 °F to 392 °F) | Standard brass, nickel-plated brass, stainless steel 304, stainless steel 316, pvc |
Metal | High durability and temperature resistance; suitable for high-pressure applications | Standard brass, steel |
Teflon (PTFE) | Excellent chemical resistance; temperature range: -200 °C to 260 °C (-328 °F to 500 °F) | Red brass, stainless steel 316 |
FEP (Fluorinated Ethylene Propylene) | Similar to PTFE but with better transparency; temperature range: -100 °C to 205 °C (-148 °F to 401 °F) | Stainless steel 316 |
FAQs
What materials are check valves made of?
Check valves are made out of plastics or metals, such as PVC, brass, stainless steel, and steel.
What is better - a plastic or metal check valve?
Plastic check valves resist corrosion and are cost-effective for low-pressure applications, while metal valves offer durability and handle higher pressures and temperatures.