Composite Hoses vs Rubber Hoses
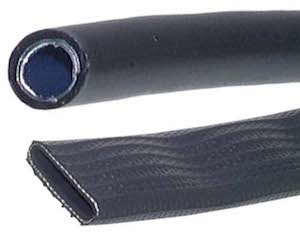
Figure 1: A high-quality Polyethylene (PE) aluminum composite hose with a PE interior lining (left) and an NBR (nitrile rubber) hose (right).
In industrial fluid transfer systems, correctly selecting between composite and rubber hoses is crucial for ensuring efficiency, durability, and safety. Composite hoses weigh less, are more flexible, and have greater chemical resistance than rubber hoses. Conversely, rubber hoses cost less and are less likely to break under pressure. This article offers guidance on selecting between them and which applications they are suitable for.
Composite hose design
Composite hoses are made of multiple layers of thermoplastic fabrics and films. A wire holds these layers together. A typical composite hose has the following layers:
- Inner: The inner layer's material must be compatible with the media flowing through the hose. The inner layer is typically made of rubber, thermoplastic, or PTFE.
- Reinforcement: The reinforcement layer strengthens the hose and adds stability. It is typically made of polyester, aramid fibers, or polyamide.
- Barrier: This layer prevents interaction between the environment and the media flowing through the hose. It is typically aluminum foil, nylon, or polyester film.
- Outer: The outer layer protects the internal components from damage. It's typically made of PVC, rubber, or polyurethane.
Rubber hose design
There are two general designs for a rubber hose, a homogenous design (contains only the rubber hose without other layers) and a three-layer design:
- Inner: The inner layer is rubber tubing that the media flows through. This layer is resistant to any damage the media may cause.
- Middle: The middle layer is a braided or knit wire that spirals or wraps around the inner layer. This reinforces the hose.
- Outer: The outer layer protects the internal layers from the environment.
Selection guide
Composite and rubber hoses have specific benefits and disadvantages. The following is a general comparison to consider when selecting a hose for an application. Hoses from specific manufacturers may differ slightly.
- Flexibility: The layers in a composite hose slide over one another when the hose moves. This makes a composite hose more flexible than a rubber hose.
- Weight: A composite hose can be up to 30% lighter than a similarly sized rubber hose.
- Cost: A rubber hose is less expensive than a similarly sized composite hose.
- Chemical resistance: Composite hoses are more chemically resistant than rubber hoses and, therefore, more suitable for hazardous media applications.
- Abrasion resistance: The layers of a composite hose are made of various materials that typically make a composite hose more resistant to abrasion than a rubber hose.
- Crush resistance: Rubber hoses are more resistant to collapse under pressure than composite hoses.
- Temperature resistance: Composite and rubber hoses can be designed for various minimum and maximum temperatures.
- Permeation: Composite hoses are generally less permeable than rubber hoses.
- Availability: In general, rubber hoses are more available and easily sourced than composite hoses.
- Sizing: Rubber hoses come in a larger variety of sizes than composite hoses.
Applications
Composite hoses
- Ship-to-ship/ship-to-shore: Composite hoses can withstand the harsh marine environments of ship-to-ship and ship-to-shore applications. For example, a composite hose is ideal for transferring fuel from the shore to a ship.
- Tankers: Composite hoses can transfer various products (e.g., chemicals, petroleum products, and acids) transported by road and rail tankers.
- Industrial plant: Composite hoses transfer chemicals and other hazardous materials within a plant. For example, a composite hose can transfer media from a storage tank to another application.
Rubber hoses
- Food processing: Food-grade silicone rubber hoses are often used in food processing applications. This rubber hose style meets food quality standards demanded by regulating bodies such as the FDA. Also, rubber hoses for food processing applications must have thick enough walls to prevent kinking while maintaining flexibility.
- Automotive: Rubber hoses with oil and grease resistance are common in vehicle fuel systems.
- Pharmaceutical: Silicone rubber hoses are excellent for pharmaceutical applications if they meet the following requirements: temperature stable, odorless, inert, non-toxic, and chemical resistant.
- Agriculture: Rubber hoses are suitable for agricultural applications such as transferring grain, feed, and other solids.
Read our articles on hydraulic, flat, and gas hoses for more details on hoses for various applications.
FAQs
What is a composite hose used for?
Composite hoses excel in applications that transfer hazardous materials, such as petroleum products.
What is a composite hose?
A composite hose is a lightweight, flexible hose constructed of several layers. This type of hose is valued for its flexibility and light compared to rubber hoses.