Differential Pressure Switches - How They Work

Figure 1: Differential pressure switch
Differential pressure switches are critical components in monitoring and controlling the pressure difference between two points in an HVAC system. These switches monitor air filters, control fan speeds, maintain proper duct flow, and operate variable air volume (VAV) systems. They function by taking pressure readings from both before and after devices, such as air filters or fans, and comparing these readings. This comparison allows them to effectively monitor the performance of these devices and notify the operator of any issues that could be negatively affecting the system's pressure or airflow. This article discusses the role of differential pressure switches in an HVAC system, their working principle, and selection criteria.
Table of contents
- What are differential pressure switches
- Differential pressure switches for an HVAC system
- Differential pressure switch working principle
- Selection criteria
- Installation and calibration
- FAQs
View our online selection of differential pressure switches!
What are differential pressure switches
Differential pressure switches detect the difference in pressure between two points. These devices are equipped with two ports, each connected to a different source of pressure. They monitor the pressure differential between these two locations.
When the pressure differential reaches a certain threshold, the switch's internal diaphragm deflects and makes contact, either completing or interrupting a circuit. This action triggers an action (like an alarm) to notify the user of the change in pressure. The pressure switch's setpoint can be predetermined or adjusted on-site according to the user's needs.
Differential pressure switches for an HVAC system
Differential pressure switches play a crucial role in measuring air flow rates and pressures within ducts and rooms in an HVAC system. They minimize energy costs while ensuring the system operates within required parameters. Additionally, differential pressure sensors enhance room comfort and safety. Differential pressure switches measure and monitor four critical aspects of an HVAC system:
- Volume
- Channel pressure
- Room pressure
- Filters
Volume
Differential pressure switches regulate the amount of air flowing through the system. By measuring pressure, these sensors can adjust the position of dampers within a closed-control circuit, facilitating demand-controlled ventilation. This capability allows for precise control over air volume, significantly improving the system's ability to manage air flow efficiently.
A pressure switch elevates the precision of volume control within the HVAC system. By providing accurate measurements, these switches ensure that the system can adjust airflow dynamically, responding to the immediate needs of the environment and its occupants.
Channel pressure
A differential pressure switch can monitor the pressure variations in ventilation ducts and accordingly adjust the power of the fan. This ensures a consistent airflow throughout the space, despite the fan not operating at a constant power level.
Room pressure
In basic air-conditioned environments, maintaining uniform pressure across different parts of a room is essential, and differential pressure switches are key to achieving this. For instance, clean rooms require a maintained overpressure to block the infiltration of contaminated air. Similarly, hospital rooms and laboratories often necessitate a continuous negative pressure to prevent the escape of germs and hazardous substances into surrounding areas.
Filters
Differential pressure switches can measure the drop in pressure across an air filter. When the pressure drop indicates that the filter is clogged or otherwise compromised, the switch triggers a notification to replace the filter. This ensures that the system continues to operate efficiently and maintains air quality.
Moreover, some advanced differential pressure monitors go a step further by being able to detect specific issues with the filter, such as tears. This capability not only prompts timely maintenance but also helps in diagnosing the exact problem with the filter, ensuring that the HVAC system remains in optimal working condition and continues to provide clean, filtered air to the environment.
Differential pressure switch working principle
The working principle of a differential pressure switch is based on the detection and response to the difference in pressure between two points. This device employs a combination of mechanical and electrical components to monitor and control pressure levels in industrial fluid and gas systems.
- Sensing element: The sensing element can be a diaphragm, capsule, bourdon tube, or bellows. This element reacts to pressure differences between two points connected to the switch. For instance, when pressure is applied, a diaphragm will deflect, a capsule will compress, a bourdon tube will change shape, and the bellows will expand. This physical movement is the initial step in the operation of the switch.
- Spring mechanism: The movement caused by the sensing element is counteracted by a spring, known as the range or stable spring. This spring is calibrated to offer a specific resistance to the movement of the sensing element. The tension or compression of the spring can be adjusted to set the differential pressure range that the switch will respond to. Essentially, the spring determines at what pressure difference the switch will activate.
- Microswitch activation: The movement from the sensing element, opposed by the spring, is transferred through a connecting rod to a microswitch. The microswitch converts the mechanical movement into an electrical action. When the pressure difference reaches a predetermined level, the movement is sufficient to actuate the microswitch. This action can either open or close electrical contacts within the switch, leading to the activation or deactivation of a circuit.
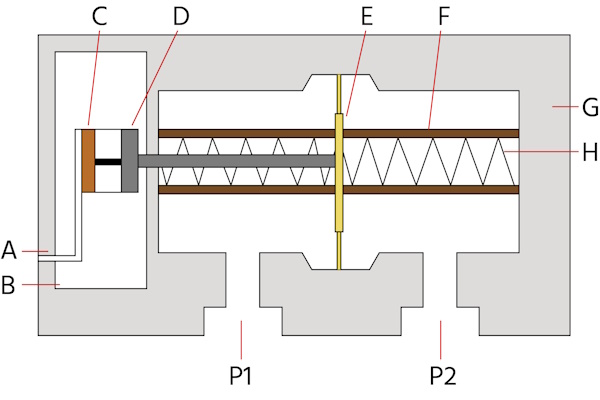
Figure 2: General differential pressure switch diagram: Setpoint screws (A), scale for setpoint adjustment (B), microswitch (C), connecting rod (D), elastic diaphragm (E), contoured metal bolsters (F), switch case (G), range spring (H), high process pressure (P1), and low process pressure (P2)
Selection criteria
When selecting pressure switches and sensors, consider the following:
- Measuring Range, Sensitivity, and Pressure Tolerance: Choose a switch with a suitable measuring range for the expected system pressures, ensuring it includes both the lower and upper limits. Additionally, the maximum pressure rating of the switch must exceed the highest pressure anticipated in the system to ensure durability and safety.
-
Electrical Compatibility and Operational Conditions:
- Electrical Requirements: Ensure the switch supports the maximum contact voltage and load the system requires, preventing electrical overload or failure.
- Temperature and Environmental Resilience: The switch should operate reliably within the highest temperature expected in the application. It must also have an appropriate degree of protection (IP rating) for its operating environment, safeguarding against dust, water, and other environmental factors.
-
Connection and Physical Dimensions:
- Connection Type: The type of connection (e.g., hose pillar) should be compatible with the system for a seamless installation.
- Physical Fit: Consider the switch's height, width, and diameter to ensure it fits within the allocated space in the system.
-
Additional Features:
- Display and Readability: Determine if a display is necessary for the application for direct pressure reading or system monitoring. Even if the switch lacks a display, assess other means of readability or monitoring that might be required.
- Switch Steps and Explosion-proof Design: The number of switch steps should align with the control needs, offering the right balance between simplicity and control complexity. For applications in hazardous environments, ensure the switch is rated as explosion-proof if necessary.
- Comprehensive Performance Criteria: If the application operates in units other than the standard (e.g., Pa instead of bar), verify the switch's specifications in these units. Also, consider the differential range or switch hysteresis to prevent frequent switching, which could lead to wear or system instability.
Installation and calibration
- Installation: A differential pressure switch installation process typically involves mounting the switch in a location where it can accurately sense the pressure difference between two points, such as across a filter, fan, or pump. The preferred installation orientation for these switches is vertical, with downward-facing pressure connections. Mounting the pressure switch in an inverted position is strictly prohibited, as this can lead to inaccurate readings and potential system failures. Always refer to the manufacturer's wiring diagram and installation instructions to ensure correct setup.
- Calibration: Calibration ensures the differential pressure switch operates accurately at the desired setpoint. To calibrate a differential pressure switch, apply known pressures to the high and low-pressure ports and adjust the knob until the switch actuates at the correct pressure difference.
Read our HVAC instruments article for more information on the various instruments used for control and monitoring an HVAC system.
FAQs
Where are explosion-proof differential pressure switches used?
Explosion-proof differential pressure switches are used in hazardous areas like oil refineries, chemical plants, and gas stations.
What is the role of a differential pressure switch on a furnace, chiller and boiler?
In furnaces, differential pressure switches monitor airflow; in chillers, they check refrigerant flow; and in boilers, they maintain water levels and steam pressure.
What is an adjustable differential pressure switch?
An adjustable differential pressure switch allows the user to set the pressure difference at which it activates or deactivates.