Electric Diaphragm Valve - How They Work
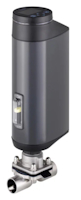
Figure 1: A stainless steel, electrically actuated diaphragm valve
Electric diaphragm valves control the media flow through it using a flexible diaphragm that moves up and down via an electric actuator to allow or block the flow. They are characterized by their resilience to corrosive and viscous media, suitable for slurry media, and prevent build-up of particles (e.g. silt) from the fluid. They are commonly used in chemical processing, water treatment, and pharmaceutical applications. This article discusses the operational mechanics of electric diaphragm valves and the key features of the Burkert type 3323 electric diaphragm valve.
View our online selection of diaphragm valves!
Key features
Electric diaphragm valves offer several key benefits for fluid control applications across various industries. Their main features include:
- Increased precision: Allows for finer control over valve positioning, leading to more accurate flow regulation.
- Enhanced safety: Minimizes the need for manual operation, reducing exposure to hazardous environments and improving personnel safety.
- Operational efficiency: Automation reduces the time and labor needed for manual adjustments, enhancing process efficiency.
- Remote operation: Enables valves to be controlled from a distance, allowing for flexible system design and quicker response to system changes.
Read our diaphragm valve overview and diaphragm valve materials articles for more information on the working and common materials used in diaphragm valves respectively.
Operation
Electric diaphragm valves operate through a series of steps that translate an electrical signal into precise control of fluid flow.
- Electrical signal transmission: The process starts with an electrical signal from a control system (PLC, DCS) reaching the valve's control module. This signal specifies the desired valve position (open, close, or specific position for throttling).
-
Actuator activation: The control module interprets the signal and activates the appropriate actuator type:
- Solenoid valve: For on/off applications, a solenoid valve receives the signal and energizes. A magnetic field within the solenoid attracts a plunger, which in turn opens or closes a pilot valve. The pilot valve then directs the media to either side of a diaphragm chamber, forcing the diaphragm to move and open/close the valve.
- Electric motor: For modulating (throttling) applications, a DC motor or stepper motor receives the control signal. The motor's direction and speed are controlled electronically to precisely position a screw mechanism or gear train within the actuator.
-
Movement transfer: Depending on the actuator type:
- Solenoid: The movement of the pilot valve spool translates to a pressure differential in the diaphragm chamber, causing a linear displacement of the diaphragm.
- Electric motor: The motor's rotation is converted into linear movement through a lead screw, crank mechanism, or gear train. This linear motion is then transferred to the diaphragm assembly.
-
Diaphragm actuation (Opening/Closing):
- Closing: The actuator applies force, pushing the diaphragm against the valve seat to create a seal and stop flow.
- Opening: The actuator reduces force, allowing the diaphragm to move away from the seat, opening the valve for media flow.
- Flow regulation: In modulating valves with electric motors, the precise positioning of the diaphragm allows for controlled flow rates. The control system continuously adjusts the motor's position based on process feedback to maintain the desired flow rate.
Table 1: Solenoid vs electric motor characteristics for diaphragm valve actuation
Feature | Solenoid valve | Electric motor |
Actuation principle | Electromagnetic force on plunger operated pilot valve | Electronic control of motor rotation |
Suitable for | On/Off control | Modulating (throttling) control |
Benefits | Simple design, fast response, lower power consumption | Precise flow control, suitable for throttling, control flexibility |
Drawbacks | Limited to on/off, pressure dependent | More complex design, slower response, higher power consumption |
Burkert Type 3323 electric diaphragm valve
The Burkert Type 3323 (Figure 1) is a solenoid-operated 2/2-way diaphragm valve designed for on/off control of fluids.
Key features and specifications
- Actuation: Electrically controlled linear actuator with ball screw mechanism. This allows for use in hygienic or harsh environments and offers fast movement (up to 4 mm/s) to the open or closed position.
- Valve body: 2-way design with optimized flow path and minimal dead space, enabling high flow rates and suitability for various applications.
- Safety: Optional energy storage ensures the valve reaches a safe position (open or closed) in case of power failure.
- Position indication: A 360° LED light ring provides visual indication of the valve's current state (open/closed).
- Diaphragm protection: Adjustable driving force on the actuator protects the diaphragm from damage.
- Durability: The valve has a high IP rating (IP65/IP67) for effective protection against dust and water ingress. It is also suitable for use in hazardous environments with ATEX certification.
- Diagnostics and connectivity: Offers optional diagnostic functions and fieldbus connection for integration with control systems.
- Material compatibility: Available with wetted surfaces in various finishes (Ra ≤ 0.38 µm - 1.6 µm) to suit different fluid types. Option for electropolished finish for enhanced hygiene.
- Size options: Comes in a range of nominal diameters (DN 06 - DN 100) to accommodate different flow requirements.
-
Compatibility and integration: The Type 3323 can be combined with several Burkert devices like:
- Type SV02 diaphragms for enhanced sealing
- Type ME61 EDIP process displays for operational monitoring
- Industrial ethernet and Fieldbus gateways for network connectivity
- Type 8098 FLOWave SAW flowmeter for precise flow measurement
Read our diaphragm valve applications article for more details on the various applications of electric diaphragm valves.