Globe Valve Materials
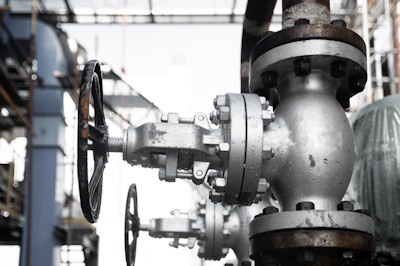
Figure 1: Stainless steel globe valve for steam
Selecting the correct globe valve material plays a crucial role in their performance and suitability for specific applications. By understanding the properties and benefits of different materials, one can select globe valves that not only meet the operational requirements of their systems but also offer longevity and reliability. Globe valves offer a range of material combinations tailored to meet specific requirements, like cost-effectiveness, corrosion resistance, or sustained performance under high-pressure conditions.
Table of contents
- Globe valve body materials
- Stem, seat, and disc materials
- Wear and erosion
- Sealing and leakage
- Globe valve material specifications and standards
- Design considerations
View our online selection of globe valves!
Globe valve body materials
The valve body, the primary structure of the globe valve, is subjected to the internal pressures of the system and must be robust enough to withstand the operating environment. Materials for the valve body are selected based on factors such as strength, corrosion resistance, and cost:
- Carbon steel: A popular choice for industrial applications due to its ruggedness and cost-effectiveness. Carbon steel offers a good balance between durability and price, making it suitable for a wide range of globe valve applications where extreme corrosion resistance is not a primary concern. The material is suitable for moderate to high temperatures and pressures, typically up to 800°F (427°C) and 1980 psi (136 bar), depending on the specific grade.
- Cast iron: Utilized in less demanding applications, cast iron provides adequate strength for lower pressure and temperature conditions. Its lower cost makes it an attractive option for systems where cost is a significant factor. Cast iron is generally suitable for temperatures up to 450°F (232°C) and pressures up to 250 psi (17.2 bar).
- Stainless steel: Chosen for environments where corrosion resistance is paramount. Stainless steel is ideal for applications involving aggressive media or in industries such as food processing and pharmaceuticals, where cleanliness and non-reactivity are crucial. Stainless steel can handle temperatures up to 1000°F (538°C) and pressures up to 3000 psi (207 bar), depending on the alloy.
- PVC: PVC globe valves offer excellent corrosion resistance, are lightweight and cost-effective for handling corrosive materials. However, they are not suitable for high-temperature or high-pressure applications. Also, they have lower mechanical strength and thermal stability compared to metals. PVC is suitable for temperatures up to 140°F (60°C) and pressures up to 232 psi (16 bar).
- Forged steel: Forged steel globe valves are ideal for high-pressure and high-temperature applications due to their superior strength and durability. The forging process results in a denser, more uniform material structure, offering enhanced mechanical properties and resistance to impact and thermal fatigue. Forged steel is capable of withstanding temperatures up to 1050°F (566°C) and pressures exceeding 6000 psi (414 bar), depending on the grade.
Read our chemical resistance guide for more information on the compatibility of materials with various media.
Stem, seat, and disc materials
The stem and disc are critical moving parts of a globe valve, responsible for the actual control of fluid flow. Material selection for these components is essential for ensuring the valve's functional integrity and longevity.
- Stem materials: Typically made from stainless steel, the stem must resist corrosion and wear, especially since it is in constant motion against the packing material to prevent leaks. Stainless steel's resistance to galling and seizure under these conditions makes it an ideal choice.
-
Seat materials: The seat and disc come into direct contact with the fluid and must be made from materials that can withstand the fluid's properties, including corrosiveness and abrasiveness.
- PTFE (Teflon): Excellent chemical resistance, low friction, good for non-abrasive fluids.
- RTFE (Reinforced PTFE): Improves wear resistance compared to virgin PTFE for slightly abrasive fluids.
- Metal: Various grades of stainless steel or bronze offer good wear resistance and high-temperature capabilities for harsher globe valve applications.
-
Disc materials: Globe valves offer various disc designs:
- Plug type disc: Offers maximum erosion resistance with its long and tapered design, making it suitable for applications where erosion is a concern. Stainless steel is widely used for plug type discs, offering excellent erosion resistance due to its durability and corrosion resistance.
- Composition disc: Features a flat seat for moderate throttling but is not recommended for high-pressure applications due to its non-aerodynamic surface. Brass or bronze provides a good balance between cost and performance for composition discs.
- Ball (conventional) disc: Provides a thin contact area that allows for good seating and moderate throttling. Ceramics are often used to make ball discs.
Typically, in cast iron globe valves, the disc and seat ring are often made of bronze, while in more demanding applications involving carbon steel or stainless steel valve bodies, the trim material is usually stainless steel. Read our chemical resistance guide for more details on the compatibility of various materials with different media.
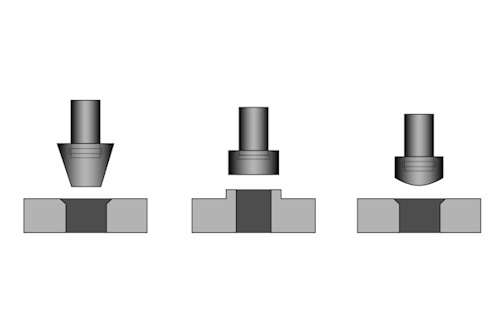
Figure 2: Globe valve disc types: Plug disc (left), composition disc (middle), and ball disc (right)
Wear and erosion
- Hardfacing materials: In applications where globe valves are exposed to high velocity or abrasive media, hardfacing materials like Stellite are applied to disc and seat surfaces. This significantly enhances wear resistance, extending the valve's service life in demanding conditions.
- Erosion resistance: Erosion resistance is critical for globe valves in steam service, where the velocity of steam can cause rapid material degradation. Selecting materials with high erosion resistance like hardened stainless steel, stellite and nickel alloys ensures the valve's durability and operational efficiency.
Sealing and leakage
- Soft seating materials: For applications requiring tight shut-off, globe valves use soft seating materials such as PTFE. These materials offer superior sealing capabilities at lower temperatures, making them ideal for precise flow control applications where leakage must be minimized.
- Emission standards: Material selection in globe valves also addresses environmental concerns, particularly in minimizing fugitive emissions. Compliance with standards like ISO 15848 or API 622 is essential, with certain materials offering reduced leakage rates and improved environmental performance.
Globe valve material specifications and standards
- ASTM and ASME standards: Materials used in globe valve construction are subject to rigorous standards to ensure they meet the required mechanical and chemical properties for safe and efficient operation. ASTM International provides specifications for material composition and properties, while ASME standards, particularly ASME B16.34, detail the application of these materials in valve design, including pressure and temperature ratings. Adherence to these standards guarantees that globe valves can withstand the demands of their intended applications.
- NACE MR0175/ISO 15156 compliance: For globe valves used in oil and gas applications, especially where sour service conditions are present, materials must comply with NACE MR0175/ISO 15156. This standard addresses the selection of materials resistant to sulfide stress cracking in corrosive environments, ensuring the longevity and reliability of valves in harsh conditions.
- Lead free globe valves: Essential for adhering to health and environmental safety standards in potable water systems, lead-free globe valves are made from materials that meet strict lead content regulations. The American National Standards Institute (ANSI) and the National Sanitation Foundation (NSF), particularly through the NSF/ANSI 61 and NSF/ANSI 372 standards, set the criteria for lead-free water system components.
Design considerations
Globe valves can feature a single-seat design with a disc that moves in and out of the flow path or a double-seated design that reduces the hydraulic load on each disc, beneficial for larger valves or those under high pressure. Additionally, the choice between a conventional design, where the process media directly contacts the disc, and a cage-guided design, which isolates the disc from pressure and deflection, depends on the application's specific requirements. However, cage-guided designs are not suitable for viscous media due to the risk of clogging. Cage-guided designs demand materials that can endure rapid flow dynamics and turbulence without degrading, like stainless steel or Hastelloy.