Heat Exchangers
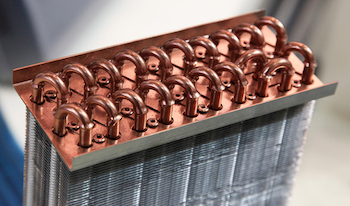
Figure 1: An industrial cooling unit that uses water-to-air heat exchange.
Heat exchangers control temperature exchanges between two fluids (liquid or gas) in a space or a system. Heat exchangers work by facilitating heat transfer for equilibrium, for example, to warm a room with a radiator it gets hot and transfers that heat to the surrounding environment warming up the cold air. This article also describes different types of heat exchangers, their typical applications, and their pros and cons.
Table of contents
- What is a heat exchanger?
- Types of heat exchangers
- Coil design heat exchangers
- Plate design heat exchangers
- Other types of heat exchangers
- Heat exchanger summary table
- FAQs
View our online selection of HVAC valves!
What is a heat exchanger?
A heat exchanger is a device that transfers heat energy. Two fluids (gas or liquid) flow through the heat exchanger; one is hotter than the other. Heat energy has a natural tendency towards equilibrium, so the hotter fluid's heat energy moves towards the colder fluid. The hotter fluid cools down, and the cooler fluid heats up.
Heat exchangers transfer heat using three methods: conduction, convection, and radiation:
- Conduction: When two objects of different temperatures physically touch, heat energy moves from high to low. For example, a hot pot of soup will heat the surface of the table it is on. In industry, devices such as process coolers, ovens, and refrigeration units use conduction.
- Convection: Convection occurs when one fluid carries away the heat energy of another fluid. Blowing on a hot cup of coffee to cool it down uses convection. Industrial convection ovens use convection to circulate hot air for heating, drying, and baking material.
- Radiation: Radiation occurs when an object emits electromagnetic waves. Hotter objects emit more radiation. The most obvious example is the Sun.
Learn more in our overview of water based heat transfer in HVAC systems article.
Types of heat exchangers
The majority of heat exchangers have either a coil or plate design.
- Coil: Straight or curved tubes have a fluid within them. Conduction transfers the fluid’s temperature from within the tube to the tube’s outer wall. A second fluid of opposite temperature then carries the heat away and warms up or cools down in the process. Using Figure 2 as an example, many coil heat exchangers have fins attached to the coil to increase the surface area of heat exchange.
- Plate: The plate design uses conduction through thin plates to transfer heat from a hot fluid to a cooler fluid. The two fluids typically move through the device in opposite directions to enhance transfer efficiency. Plate heat exchangers are suitable for connecting buildings to district heat and cooling centers and connecting elements of an HVAC system.
Coil design heat exchangers
Finned tube coil heat exchanger
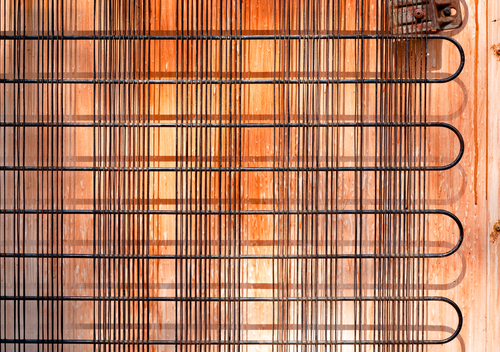
Figure 2: A finned tube coil heat exchanger on the back of a fridge.
A finned tube coil heat exchanger has coiled tubes connected by long thin pieces of metal called fins. Heat in the tubes conducts into the fins, increasing the surface area that a cooler fluid interacts with to move the heat away via convection. As seen in Figure 2, a common example is the finned tube coil on the back of a refrigerator. The heat extracted from the fridge to keep it cool is moved through the tubes. The air behind the fridge moves the heat away from the tubes and fins.
Finned tube coil heat exchangers are also found on:
- Ductwork systems
- Fan coil units
- Air handling units
- A/C evaporators and condensers
- Trench heaters
Trench heater
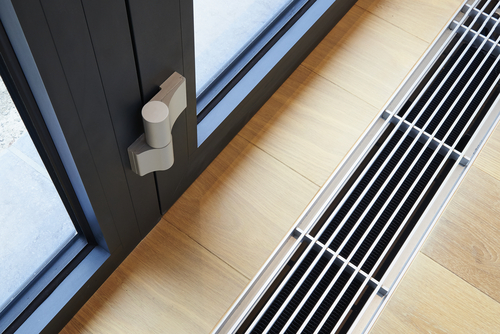
Figure 3: A trench heater in the floor.
As seen in Figure 3, the installation of a trench heater is typically in the floor around the interior perimeter of a building, especially under windows. Trench heaters use a finned tube coil design to prevent heat loss from the floor and condensation on the windows. Hot water flows through the trench heater's tube. The heat from the trench heater transfers to the cold air near the floor. This heated air rises and is replaced by cooler air, creating a convection cycle to heat the space.
Duct electrical heater
A duct electrical heat exchanger uses highly resistant coils that generate heat. Air moving through the duct moves the hot air away from the coils. These heat exchangers are also applicable in furnaces and fan coils. Due to their high heat, duct electrical heat exchangers are only suitable for spaces in which the heat exchanger cannot be accidentally accessed.
Microchannel heat exchanger
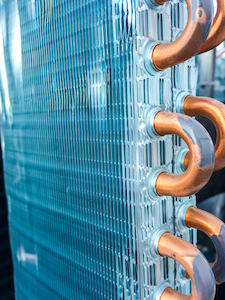
Figure 4: A microchannel heat exchanger.
A microchannel heat exchanger is an improvement on the finned tube coil design. There are more fins on a microchannel heat exchanger, which are much closer together. Some designs have less than a 1 mm distance between fins. This design greatly increases the surface area a cool fluid passes over, transferring the heat elsewhere.
Most convection heat transfer comes from the heat exchanger's fins, which receive heat from the tubes via conduction. Heat transfer from the tubes is much less efficient than from the fins.
Microchannel heat exchangers use refrigerant only and are applicable in:
- Air dryers
- Condensing units
- Residential A/C units
- Air-cooled chillers
Furnace evaporator coil
A furnace evaporator coil works with an air conditioning unit. It has the same working principle as a finned tube coil heat exchanger. An evaporator coil is most applicable for large homes or small commercial buildings to cool down air in a space. Cold refrigerant flows through the evaporator coil's tubes, and warm air from the air conditioning unit flows over the tubes. The air from the unit cools down and flows back into the building's ducts. The tube refrigerant heats up enough to evaporate and flows into a compressor.
Radiator
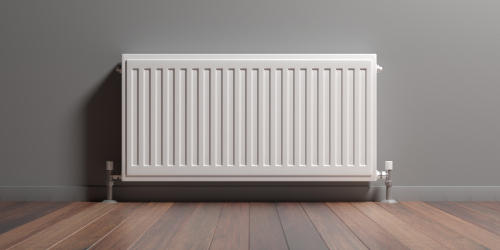
Figure 5: A radiator.
Radiators (Figure 5) are common in North America and Europe. Zone valves control the flow of hot water into the top of the radiator through a narrow tube. The water flows down through multiple vertical tubes across the radiator's width. These pipes are wider than the inlet pipe, which slows down the flow to increase heat transfer efficiency. Through conduction, the radiator heats up the surrounding air. The air around the radiator moves away, making space for cooler air to flow toward the radiator. This creates a convection current that heats the room that the radiator is in.
Water heating element
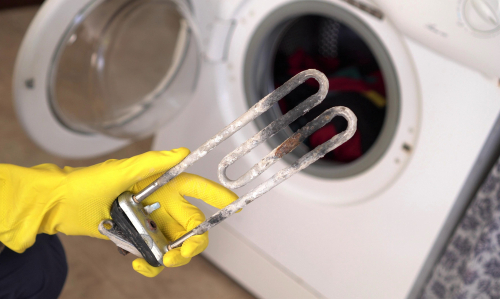
Figure 6: An old water heating element from a washing machine that must be replaced due to calcium buildup.
A water heating element uses electricity or gas to generate heat and heat water in a tank. The water surrounding the element heats up via conduction and rises. Cooler water replaces the warmer water, which creates a convection current within the tank. Water heating elements apply to devices such as washing machines (Figure 6), water heaters, and open cooling tower basins.
Boiler
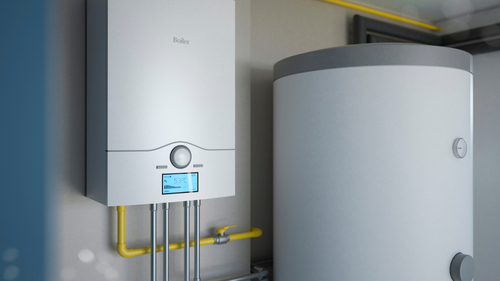
Figure 7: A gas boiler
A boiler uses gas, oil, or coal to heat water or change it to steam. The water circulates through radiators (see radiator section) connected to the boiler. When the water in the system cools down, it returns to the boiler to restart the process.
Chilled beam
A chilled beam heat exchanger has a finned tube coil design and suspends from a ceiling. Cold water flowing through the chilled beam's tubes. Heated air near the chilled beam transfers energy to tubes, which cools the air and creates a convection current to cool a space. There are two types: a passive chilled beam and an active chilled beam.
- Passive: A passive chilled beam does not use a fan to circulate air.
- Active: An active chilled beam has nozzles that channel air across the cold tubes. Active chilled beams more efficiently cool spaces.
Furnace heater
A furnace operates similarly to a boiler. However, it spreads heated air through a space rather than sending hot water or steam to radiators. A typical furnace has a gas-fueled flame that heats a heat exchanger, which heats the air within the furnace. The blower that moves cold air from the building's duct system into the furnace also moves the hot air from the furnace through the duct system. As the hot air fills a space, colder air moves into a return duct, which goes to the furnace to be heated.
Shell and tube heat exchanger
A shell and tube heat exchanger has a large cylindrical shell (Figure 8 labeled A) with tubes (Figure 8 labeled B), or tube nest, inside it. Fluid flowing through the shell is shell-side fluid, and fluid in the tubes is tube-side fluid. As seen in Figure 8, the tubes run straight through the tube from the inlet to the outlet. Other shell and tube designs have tubes bent in a U-shape one or more times. Bent tubes allow fluid in the tubes to make multiple passes through the shell. Baffles (Figure 8 labeled E) inside the shell force shell-side fluid to flow through the entirety of the shell for maximum heat transfer efficiency. Tube sheets (Figure 8 labeled G) support the tubes in the shell.
Fluid in the tubes heats or cools fluid in the shell, or vice-versa, depending on the application. A common example from the petroleum industry is hot oil in the shell and cold fluid in the tubes. Cold fluid flowing from the tube inlet (Figure 8 labeled C) to the tube outlet (Figure 8 labeled F) cools hot oil flowing from shell inlet (Figure 8 labeled H) to shell outlet (Figure 8 labeled D).
The operation of shell and tube heat exchangers depends on their flow type:
- Counter: Figure 8 is an example of counterflow. Shell-side and tube-side fluid moving in opposite directions is the most efficient at heat transfer.
- Parallel: In a parallel flow shell and tube heat exchanger, shell-side and tube-side fluid enter on the same side and move in the same direction. The heat change for each fluid is proportional.
- Cross: The two fluids flow perpendicular to one another in a cross-flow shell and tube heat exchanger. Typically, the two fluids are in different states. An example of this is a steam condenser. Hot steam in the shell turns cooler water into steam, which is then absorbed into the initial steam supply.
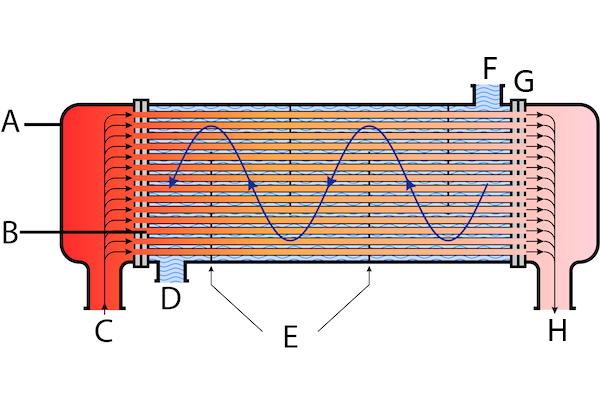
Figure 8: A typical shell and tube heat exchanger: shell (A), tubes (B), tube-side fluid in (C), shell-side fluid out (D), baffles (E), shell-side fluid in (F), tube sheet (G), and tube-side fluid out (H).
Plate design heat exchangers
Plate heat exchangers connect buildings to district cooling and heating networks. These heat exchangers require less space than other heat exchangers (e.g., shell and tube heat exchangers) that produce similar thermal exchange outputs. The plate heat exchanger uses multiple plates pressed into a plate stack by clamping bolts. As seen in Figure 9, gasket plate heat exchangers have rubber gaskets that control the flow of fluid over the plate (see gasket plage heat exchanger section below). The plates rest on a guide bar to ensure that they properly align. Finally, the plate stack has a fixed cover and a moveable cover. The input and output ports are on the fixed cover. The moveable cover allows for easy removal, addition, or maintenance of plates.
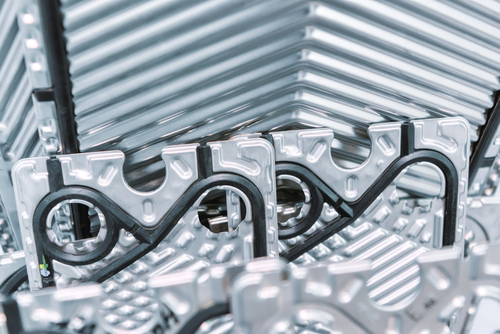
Figure 9: Two plates with rubber gaskets that surround their left ports. Fluid cannot flow past those gaskets. Consecutive plates have these gaskets on alternate ports.
Another important design feature of the plate heat exchanger is the grooves on each plate's surface. The grooves play three essential roles:
- Surface area: The corrugations increase the surface area of each plate, which increases the heat transfer rate.
- Stiffness: The corrugations increase the stiffness of each plate, allowing for thinner plates, which have a higher heat transfer rate.
- Turbulence: The corrugations create a turbulent flow, which increases the heat transfer rate and helps prevent fluid from sticking to the plates.
There are single-pass and multi-pass plate heat exchangers. With single-pass, the hot and cold fluids pass through the plate stack only once. With multi-pass, the fluids pass through multiple times. While multi-pass allows for finer temperature control, it also requires that inlets and outlets be on opposite sides of the plate stack. Therefore, single-pass plate heat exchangers are more common because they are easier to assemble and disassemble.
Gasket plate heat exchanger
Plate heat exchangers typically use counterflow due to its efficiency. The gaskets on each plate alternate positions. For example, if cold fluid entering the heat exchanger flows across the first plate, the next plate it will flow across is the third. Hot fluid will flow across the second and fourth plates, and so on.
Brazed plate heat exchanger
Brazed plate heat exchangers work similarly to gasket plate heat exchangers. The brazed plates are joined together using a filler metal, such as a thin copper sheet between each plate. During manufacturing, the brazed plate heat exchanger is heated to a temperature high enough to melt the copper but not the plates, which are stainless steel. A brazed plate's advantages over a gasket plate are that they are less likely to leak, are more compact, and are slightly more efficient. However, the entire unit requires replacement if a brazed plate heat exchanger is damaged.
Welded plate heat exchanger
A welded plate heat exchanger has plates that are welded together. The advantage of this plate heat exchanger over the others is that it can operate at higher temperatures and pressures. Therefore, welded plate heat exchangers are most suitable for industrial applications.
Micro plate heat exchanger
Micro plate heat exchangers are either gasket or brazed type. A micro plate heat exchanger’s key advantage is the corrugation design on each plate. Traditional plate heat exchangers use a fishbone or chevron design, whereas micro plate heat exchangers use many small dimples. The dimples allow fluid to move over the plate more evenly and increase turbulence, providing more efficient heat transfer.
Ducted plate heat exchanger
A ducted plate heat exchanger is part of an air handling unit that drives central air conditioning. This plate heat exchanger's design uses the heat of the exhaust air to ensure that the fresh air coming into the space is warm instead of cold. Hot exhaust air flows through plates oriented diagonally to other plates with fresh cold air flowing through them.
Shell and plate heat exchanger
A shell and plate heat exchanger combines the working principles of a shell and tube heat exchanger with a plate heat exchanger. The plates inside the shell are circular and have a top and bottom port hole. The plates are welded together into a plate stack. The heat exchanger works with a countercurrent flow. Hot fluid enters the shell-side and flows over and down the plates without leaking into them. Cold fluid enters the plate-side and flows between the plates.
Other types of heat exchangers
Rotary wheel heat exchanger
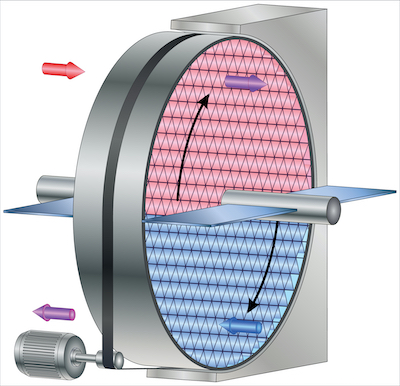
Figure 10: A rotary wheel heat exchanger with hot exhaust air (top) and cold fresh air (bottom).
A rotary wheel heat exchanger is similar to a duct plate heat exchanger because it uses hot exhaust air to cool fresh air. Hot exhaust air (Figure 10 top) heats a portion of the wheel's surface. This heated surface rotates to the intake channel (Figure 10 bottom) to heat the fresh air. A motor and belt power the wheel's rotation past two channels.
Heat pipe
A solar water heater (Figure 11) is a common application for heat pipes. An individual heat pipe has a glass tube that seals a copper tube within. The copper tube heats up under the Sun, and the glass tube prevents the heat from escaping. A seal on the heat pipe keeps the water mixture within the pipe at low pressure. This allows the mixture to vaporize into steam at lower temperatures. The steam moves to the top of the heat pipe, which connects to the main pipe that holds every heat pipe in the system. The heat at the top of the heat pipe transfers to cold water that flows through the main pipe, heating the water.
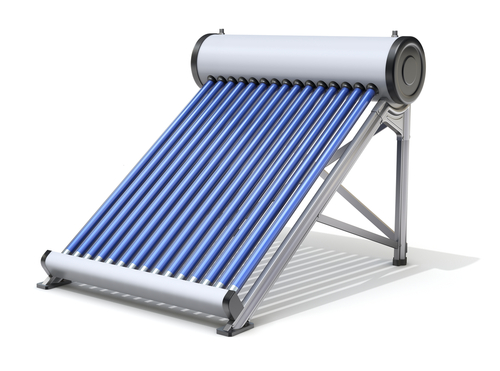
Figure 11: A solar water heater.
Heat sink
A heat sink has long, narrow fins mounted on a base that sits close to a heat source. The heat from the source conducts into the base of the heat sink and then dissipates through the fins. Air or liquid moves across the fins of the heat sink to move heat away via convection. As seen in Figure 12, a common example is a heat sink on a computer processor.
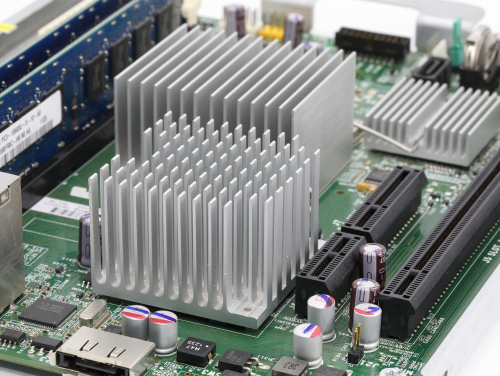
Figure 12: A heat sink cools a computer processor.
Heat exchanger summary table
Heat Exchanger | Type | Basic Operation | Example application(s) | Advantages and disadvantages |
Finned tube coil |
Coil |
Air pushes heat from hot tubes connected by thin metal plates | Back of fridge
Duct systems Heat pump |
Efficient at transferring heat to air. Not ideal for transferring heat between liquids. |
Trench heater | Heat from tube and fins keeps floor warm and condensation off windows | Interior floor of building under windows | Applcable with any floor finish material. | |
Duct electrical heater | Air pushes heat away from electrically heated coils | Space heating
Heat moving gas streams |
Provide uniform heating across an air stream from in a duct but are not easily accessed | |
Microchannel | Similar to finned tube coil but thin metal plates are closer together, enhancing heat transfer efficiency | Heat pump
Aircraft gas turbine engine |
More efficient than standard finned tube but fluids moving through experience a higher pressure drop | |
Furnace evaporator coil | Refrigerant in tubes cools warm air coming from an air conditioning unit | Air conditioning | Increase air cooling but require careful maintenance | |
Radiator | Hot water or steam flows through tubes to heat the air around the radiator and create a convection current in the space | Space heating | Cleaner and safer than ducted heating. As efficient as ducted heating.
However, a boiler costs more to replace than a furnace. |
|
Water heating element | An electrically heated tube heats water in a tank | Washing machine | Low upfront costs and safe. High operation costs and slow heating time. | |
Boiler | Gas, oil, or coal heats water that is supplied to radiators | Home and small commercial space heating | Energy and cost-efficient but high upfront costs | |
Chilled beam | Cold water in a tube cools warm air at the top of a space | Cool large or small spaces
Schools Hospitals |
Reduce floor space requirements but have higher operating costs from pumping | |
Furnace | A gas-fueld flame heats tubes that then heat the surrounding air that will go into a building’s ducts | Home heating | Dependable heating and low maintenance. Electric furnaces are expensive to operate and gas furnaces have dangerous risks. | |
Shell and tube | Tubes in a cylindrical container heat or cool fluid in the container | Cool oil | Can operate at higher temperatures and pressures than plate heat exchangers and have a lower pressure drop. However, not as efficient as plate heat exchangers. | |
Gasket |
Plate |
Rubber gaskets control hot and cold fluid flow to exchange heat between thin metal plates | Water heater
Heat pump isolation |
Easier to assemble, disassemble, and clean than other plate types. Not as efficient as other plate types. |
Brazed | Similar to gasket but plates are brazed together | Condenser
Evaporator Oil or gas cooler |
More efficient than gasket types but the entire plate stack must be replaced. | |
Welded | Similar to gasket but plates are welded together | High pressure and temperature Industrial heat exchange | Can work at higher temperatures and pressures than other plate types but the entire plate stack must be replaced. | |
Micro | Plates have more surface area and fluid is more evenly distributed across the plates | Same as gasket and brazed | More efficient than gasket and brazed. | |
Ducted | Hot exhaust air and cold supply air flow in channels diagonal to one another | Air handling units | Moisture does not transfer between fluid streams | |
Shell and plate | Fluid in a cylindrical shell flows over a stack of circular plates welded together that a different fluid can flow through | Higher temperatures and pressures than shell and tube | More efficient than shell and tube but the entire plate stack must be replaced | |
Rotary wheel |
Other |
Hot exhaust heats part of a rotating wheel, which then moves into a channel to warm cold supply air | Air heat recovery in ventilation system | Can handle larger air volumes but moisture moves between the two fluid streams |
Heat pipe | A low pressure water mixture vaporizes and moves up a tube to heat a channel of cold flowing water | Solar water heater | Cost efficient operation but high upfront costs | |
Heat sink | Heat transfers into the heat sink’s base and dissipates through fins attached to the base | Electrical components | Copper heat sinks conduct heat better than aluminum heat sinks. However, they also cost and weigh more. |
Read our portable heaters and radiant floor heaters articles for more information on the working of each type.
FAQs
What type of heat exchanger is the most efficient?
In general, plate heat exchangers are more efficient than coil heat exchangers. However, the most efficient heat exchanger for an application depends on the application.
What is a heat exchanger used for?
A heat exchanger uses a hot or cold fluid to heat or cool another fluid. In many applications, this allows temperature control without undesirable mixing of fluids.
What are the advantages of a heat exchanger?
Most heat exchangers do not need additional devices to operate, such as an air compressor.