High-Pressure Compression Fittings
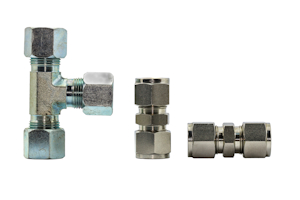
Figure 1: Stainless steel is a common material for compression fittings used in high-pressure applications.
High-pressure compression fittings are essential for the safe and efficient operation of systems with extreme pressures. This connection method is advantageous for its simplicity and convenience, as it does not require soldering and allows for easy assembly and disassembly, making it ideal for plumbing, hydraulic, and gas applications where regular maintenance or adjustments are necessary.
Table of contents
View our online selection of high pressure compression fittings!
What is a compression fitting?
Compression fittings are a type of connector used across various piping and tubing systems. These fittings create a watertight seal by compressing a ferrule against a pipe or tube. When the fitting's nut is tightened, the ferrule, often made of softer metal or plastic, gets squeezed between the nut and the fitting body, which deforms and clings to the tube, ensuring a secure connection. This design avoids soldering, making compression fittings a popular choice for quick and easy assembly in plumbing, hydraulic, and gas applications, particularly where disassembly might be needed for maintenance or adjustments.
Design
Compression fittings designed for high-pressure applications are constructed with robust materials and precise engineering to withstand demanding conditions. They typically feature:
- Heavy-duty bodies: Made of strong metals like stainless steel or brass, which resist the mechanical stresses of high pressure.
- Hardened ferrules: These are often made from materials that are harder than the tubing itself to ensure they can compress and grip the tube without being crushed by the pressure.
- Thicker walls: To manage the strain of high pressures, the components have increased wall thickness, reducing the risk of failure.
- Double ferrule design: Some high-pressure fittings use a two-ferrule system, with the front ferrule creating a tight seal and the back ferrule providing a strong tube grip.
- Precision threads: Finely machined threads ensure a tight and secure screw-on action, crucial for maintaining the integrity of the connection under high pressure.
Learn more in our article that covers the design standards for high-pressure fittings.
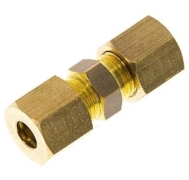
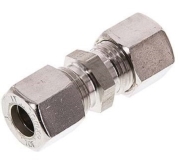
Figure 2: A brass compression fitting that works up to 150 bar (2,175 psi) and a stainless steel compression fitting that works up to 630 bar (9,137 psi).
Applications
High-pressure compression fittings are engineered to maintain a secure, leak-proof connection in systems with significantly high operational pressures. These robust fittings find their applications in several critical fields:
- Industrial hydraulics: Employed in machinery and equipment that utilize hydraulic power, these fittings must withstand the intense pressure exerted by hydraulic fluids.
- Gas transmission lines: Used for natural gas or other high-pressure gasses, these fittings ensure safety and integrity in the distribution infrastructure.
- High-pressure washers: Vital in equipment designed to clean surfaces with pressurized water or cleaning solutions.
- Research laboratories: Utilized in experimental setups where precise control of high-pressure gasses or liquids is necessary for scientific investigations.
- Aerospace and defense: In aircraft and military vehicles, high-pressure compression fittings are used for fuel, oil, and hydraulic systems, where failure is not an option.
These applications demand fittings that provide consistent performance and reliability under high-pressure conditions.
FAQs
What are high-pressure compression fittings?
Compression fittings designed to connect and seal high-pressure fluid systems.
How do high-pressure compression fittings work?
They compress a ferrule onto a pipe, creating a tight seal for high-pressure applications.
What materials are used in high-pressure compression fittings?
Typically made from stainless steel, brass, or other high-strength materials.