What Is a Latching Relay?
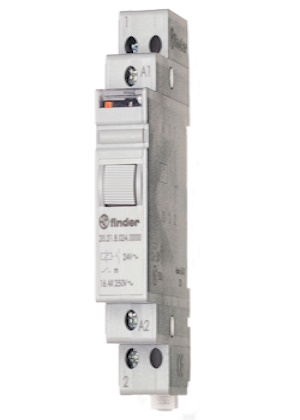
Figure 1: Latching relay
Latching relays maintain their state after being actuated without needing continuous power. This makes them highly efficient for applications where power conservation is crucial. They are characterized by their bistable operation, meaning they have two stable positions: set (on) and reset (off). This article explores the working of latching relays, their advantages, and diverse applications.
Table of contents
- Latching relay understanding
- Features
- Latching relay types
- How latching relay works
- Selection criteria
- Applications
- Difference between latching and non-latching relays
- FAQs
View our online selection of latching relays!
Latching relay understanding
Read our relay types article for more information on the various types of relays.
A latching relay maintains its most recent state or position even when the signal that activated it is no longer present. It can stay in the 'on' or 'off' state without a constant power supply. Once triggered, its position is 'latched' into place. The latching relay can be operated manually, remotely, by impulses, or using different control inputs.
Because of its ability to remain in the last switched position and its operation that is based on short pulses of power, the latching relay is known by several alternative names:
- Memory relay
- Bi-stable relay
- Stay relay
- Impulse relay
Features
Latching relays have several benefits:
- Low energy consumption
- Minimal heat production in relay coil and circuit
- Streamlined switching circuits that necessitate fewer components
- Quick operation and dependable performance, even during power failures
Latching relay types
-
Single coil and dual coil: These are the most common type, using electromagnetism to hold the contacts in their position.
- Single coil type requires a pulse of current in one direction to activate and another in the opposite direction to reset.
- Dual coil type controls one state (activation or reset), independent of polarity (discussed in the next section).
- Magnetic: Magnetic latching relays use permanent magnets to maintain their position after being actuated. They can be either single or dual-coil operated. The permanent magnet holds the armature in the last position it was moved to by the coil.
- Mechanical: Mechanical latching relays use a ratchet and pawl mechanism to maintain the position of the contacts. The relay is set or reset by moving the pawl with a pulse to the coil.
- Electronic (solid-state relays): These are not traditional electromechanical relays but use semiconductor devices to perform the latching function without moving parts. They maintain their state using electronic circuitry rather than a mechanical mechanism.
How latching relay works
The operational mechanism of a latching relay is fundamentally similar to that of a conventional relay, with the key difference being that it does not require a continuous power supply to remain in an energized state. Current pulses are utilized to activate (trigger) and deactivate (reset) the relay, facilitating its transition between states or positions.
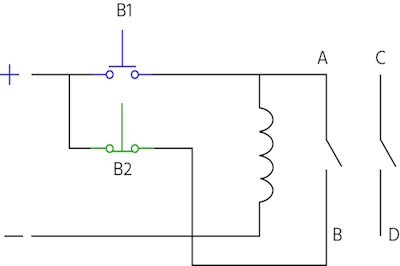
Figure 2: Latching relay diagram showing push buttons (B1 and B2) and contacts (A, B, C, and D)
Figure 2 shows an example of a latching relay circuit. It has two push buttons - B1 to make the circuit and B2 to break it. B1 is the normally open (NO) switch, while B2 is the normally closed (NC) switch. This means that initially, B1 is in an open state, and B2 is in a closed state.
Activating the relay
- Pressing button B1 closes the circuit between the positive terminal, B1, point A, point B, and the negative terminal.
- Current flows through the coil, energizing it. This creates a magnetic field.
- The magnetic field attracts the armature inside the relay. The armature moves, causing contacts A-B and C-D to connect.
Latched state
- Releasing Button B1 does not break the circuit. Even though B1 is open, the current can still flow through the coil via the alternate path: positive terminal, B2, point B, point A, and negative terminal.
- Contacts A and B remain connected, as do C and D. This keeps the coil energized and keeps the relay latched in the activated state.
Deactivating the relay
- Pressing button B2 opens the circuit between the positive terminal and point B.
- The current flow through the coil is interrupted. The magnetic field weakens.
- The armature is released under the spring force. Contacts A and B disconnect, followed by C and D.
- The circuit is broken, and the relay deactivates.
Additional points
- The specific contact configuration (NO/NC) of points A, B, C, and D can vary depending on the relay's design and application.
- Some latching relays have a reset button that can be used to manually deactivate the relay without pressing B2.
Read our relay wiring article for more information on connecting a conventional relay's terminals.
Selection criteria
When selecting a latching relay for an application, it's crucial to consider the specific requirements of the system and the environment in which the relay will operate.
- Mounting method: Latching relays are typically DIN rail- or flush-mounted. A DIN rail-mounted latching relay has a clip or adaptor that snaps onto the rail itself. DIN rail mounting is highly convenient, allowing for easy installation and reconfiguration of the relay. In flush mounting, the device's body is usually attached to the wall or panel, and only the front plate and operational parts are visible and accessible. This method provides a clean and unobtrusive look and can offer some protection against accidental contact or damage.
-
Physical Dimensions
- Width: The width of a latching relay, defined by the number of modular spacings, determines how much space the relay will occupy on a DIN rail or in a control panel. Modular spacing is a standardized unit of measure in electrical installations, with one modular spacing typically being 17.5 mm wide.
- Built-in depth: The built-in depth refers to how far the relay extends into the panel or cabinet once installed. This dimension must be considered to ensure enough clearance behind the relay for appropriate ventilation, wiring, and maintenance.
-
Number of contacts
- Normally open contacts: The number of normally open contacts in a relay defines how many separate circuits can be controlled in their default (unenergized) state. For example, a relay with one normally open contact means that when it is not energized, the contact is open, and no current can flow through it.
- Normally closed contacts: Normally closed contacts are the opposite of normally open contacts; they allow current to flow when the relay is in its default state.
- Change-over contacts: Change-over contacts, also known as Form C or single-pole double-throw (SPDT) contacts, can switch between normally open and normally closed states upon actuation. They provide a way to redirect current from one circuit path to another.
-
Voltage and frequency
- Control voltage: Control voltage (AC or DC) is the magnitude of voltage required to operate the relay's coil. The specified range of control voltage for a relay indicates the minimum and maximum voltages at which the relay can operate reliably.
- Frequency: The specified frequency range (e.g., 50 Hz to 60 Hz) indicates the relay's compatibility with the standard power line frequencies in different regions.
- Supply voltage: Supply voltage refers to the voltage level at which the relay's contacts can switch a load. For instance, a relay with a supply voltage rating of 230 V AC is designed to switch loads that operate at this common mains voltage level seen in many residential and commercial settings.
-
Load rating
- It's important to match the relay's maximum load ratings with the types and configurations of lighting fixtures it will operate. For example, to control a group of incandescent light bulbs that collectively consume 1800 watts, a relay with a maximum incandescent lamp load rating higher than 1800 watts is needed to ensure safe and reliable operation. Similarly, for a fluorescent lighting system with a total load of 450 VA, the relay should have a maximum load rating for fluorescent lamps that exceed 450 VA.
Applications
Normal relays that don't latch are more common than latching relays since many applications require the relay to return to a default state when power is removed. For example, in automotive applications, relays are used to control headlights, wipers, and other electrical components. These relays typically need to return to their default state when the vehicle is turned off. Latching relays, on the other hand, are used in applications where it is necessary to maintain the last state even when power is removed from the coil, such as in memory or state retention applications. By replacing standard mechanical switches with latching relays, there are fewer operational requirements, which enhances reliability and reduces power usage.
Some typical applications of latching relays include:
- Utility meters: Latching relays are often used in electric, gas, and water meters where they can control the supply remotely without needing a constant power supply to the relay coil.
- Battery-powered devices: Devices that run on batteries and need to conserve power, such as portable medical devices, use latching relays to switch circuits on and off without draining the battery to hold the relay in one state.
- Lighting control systems: In smart lighting systems or building automation, latching relays can be used to control the on/off state of lights without requiring continuous power, which can result in energy savings.
- Security systems: Latching relays are used in some security systems to control locks or other security devices, allowing them to remain in the last state during power interruptions.
However, there are some applications where using a latching relay might not be ideal:
- Frequent switching: If the application involves constant switching back and forth, a normal relay might be more efficient. Latching relays excel in maintaining states, not rapid changes.
- Simple on/off control: A normal relay is often sufficient and more cost-effective for basic applications like turning lights on and off.
- High-speed switching: Latching relays can have slightly slower switching times than some high-performance normal relays. A normal relay might be better if the application requires extremely fast switching.
Difference between latching and non-latching relays
Table 1: Latching vs non latching relays
Latching relay | Non-latching relay |
A latching relay will stay in the last position when it was powered last. | A non-latching relay goes back to its regular position. |
Low power consumption, the power needed only during state change | Higher power consumption, the power needed to maintain state |
May have single or dual coil | Typically has a single coil |
Noiseless switching | Noisy |
Often include indicating knobs that are used to control the position of the relay manually. | Do not have a knob feature |
More complex due to state retention | Simpler design |
Expensive | Less costly |
Applications include memory functions and alarm systems | General switching applications |
Read our contactor vs relay article to know more about the differences between relays and contactors and when to choose one for an application.
FAQs
What are latching relays used for?
Latching relays are used to control circuits with minimal power consumption, maintaining their state during power loss and in battery-operated or remote systems.
What is a DC latching relay?
A DC latching relay is a type of latching relay that operates with a direct current (DC) power source.
Where is a latching relay used?
A latching relay is commonly used in battery-powered devices, energy-saving applications, remote control systems, and situations requiring circuit control without a constant power supply.