Air Preparation In Pneumatic Systems
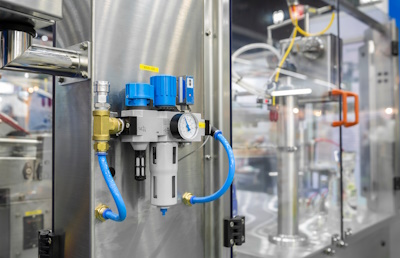
Figure 1: Compressed air filter regulator lubricator
Compressed air in pneumatic systems often contains moisture and contaminants and may be at an unsuitable pressure for direct use, potentially damaging downstream equipment. To condition the air, it passes through filters, regulators, and lubricators, which clean it and adjust the pressure. This article examines the components of air preparation, their functions, and selection criteria.
Table of contents
- Compressed air preparation in a pneumatic system
- Particles in compressed air and their consequences
- Air preparation units in a pneumatic system
- How to choose the right air preparation unit
View our online selection of FRLs and pneumatic mufflers!
Compressed air preparation in a pneumatic system
Compressed air is air kept at a pressure above atmospheric level. It is a vital energy source in pneumatic systems for various industrial applications. Compressed air preparation begins with ambient air (Figure 2 labeled A), which is drawn into a compressor (Figure 2 labeled B) that pressurizes it and sends it to a reservoir (Figure 2 labeled C) for storage. To ensure the air is clean and dry, it passes through a refrigeration dryer (Figure 2 labeled D) that removes moisture. Then, it passes through air preparation (Figure 2 labeled E) components to remove impurities and maintain sufficient pressure (discussed later). Finally, the prepared air is supplied to the machine (Figure 2 labeled F) through pipes.
The compressed air travels through various devices, pipes, and fittings that can introduce contaminants. Additional air preparation at the point of use is essential, especially over long distances or in environments prone to moisture and particulate accumulation.
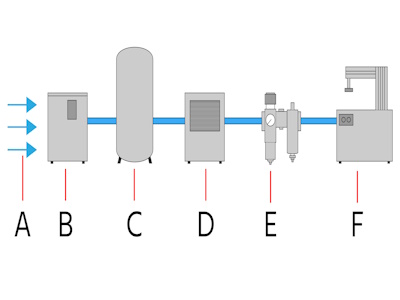
Figure 2: Pneumatic air preparation system components: ambient air (A), compressor (B), reservoir (C), refrigeration dryer (D), air preparation (E), and machine (F).
Particles in compressed air and their consequences
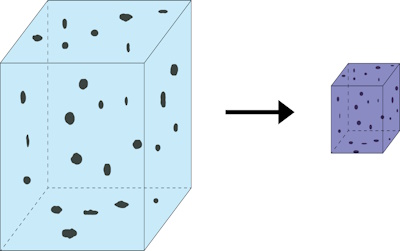
Figure 3: The contaminants' concentration increases many times over when the air is compressed
One cubic meter of air from the environment has many components that can cause issues in pneumatic systems. These include:
- Dirt particles: Dirt particles could be as many as 180 million particles ranging from 0.01 micrometers to 100 micrometers in size.
- Water: The amount of water varies with temperature, but at 50 𐩑C (122 𐩑F), there can be approximately 80 grams of water.
- Oil: There can be up to 0.03 milligrams of oil.
- Chemical contaminants: Chemical contaminants include harmful substances like lead, cadmium, iron, mercury, and others.
Table 1 discusses the consequences of these particles in compressed air. Cleaning compressed air is crucial to prevent damage and ensure the components work smoothly. Also, different industries and specialized applications may have their standards for how clean the compressed air should be.
Table 1: The particles in compressed air and their consequences
Particles | Direct consequences | Long term consequences |
Solid particles: Solid particles such as dust, rust flakes, or metal shavings created during manufacturing or other processes. | Buildup and wear and tear from parts rubbing together, for example, between the wall of the cylinder and the seal on the piston. |
|
Water: Atmospheric air always has some moisture in it. | Rusting of components which creates rust particles that can lead to mechanical damage or clog narrow passages where fluids pass through. | |
Oil: Even in compressors that don't use oil, tiny oil droplets from the air that's pulled in can leave behind traces of oil contamination. | Particle clumping leading to blocked cross-sections. Additionally, oil can cause elastomers, such as those in the seals to swell up. |
Air preparation units in a pneumatic system
Air preparation units typically refer to the various components installed along the system to prepare and maintain the compressed air quality before it reaches the point of use. The main units are discussed below.
FRL
An FRL unit is a modular compressed air conditioning system consisting of a filter, regulator, and lubricator. designed to remove contaminants, adjust pressure, and add lubricant to compressed air in pneumatic systems. Although these components are frequently integrated into a single system, they can also be found as separate units, such as just a regulator or a combined filter regulator. Modern pneumatic systems, equipped with self-lubricating components, often do not need lubricators.
Filter
A filter eliminates contaminants like dust, water vapor, and oil present in the compressed air. In some systems, multiple filters are needed due to various needs:
- The system must eliminate contaminants from the pipes or condensation that occurs during transit before the air reaches each piece of equipment.
- Different control or regulation devices need air of varying levels of cleanliness.
- Certain applications, like food packaging, demand more than standard filtration. Here, activated carbon filters are necessary; the air must pass through fine filters before reaching them.
Pneumatic systems typically use filter elements that can capture particles between 5 to 50 micrometers (µm) in size. To achieve air quality that meets the ISO 8573-1:2010 [7:4:4] standard, the following criteria must be met:
- Particle concentration: 5-10 milligrams per cubic meter (mg/m³)
- Filter fineness: 20-50 µm
For higher standards, the design must adhere to the ISO 8573-1:2010 [6:4:4] specification:
- Particle concentration: No more than 5 mg/m³
- Filter fineness: 5 µm
Filter elements must be replaced regularly because they become clogged with pollutants over time, leading to reduced airflow. A drop in air pressure can be identified by measuring the difference in pressure before and after the filter. As a filter element gets dirtier, the pressure drop across the filter increases (typically equal to or slightly less than 0.5 bar), indicating the level of blockage in the filter element.
Regulator
A pressure regulator manages compressed air pressure in a pneumatic system, ensuring that downstream equipment receives air at the correct pressure. The network typically provides pressure ranging from 6 to 10 bar (87 to 145 psi), which can fluctuate based on how much air is used. To use compressed air effectively, each piece of equipment should have its necessary pressure set using a separate pressure regulator.
Lubricator
A lubricator adds precise amounts of oil into the compressed air stream. Mechanical component manufacturers aim to create products that don't need any additional lubrication. This is achieved by using appropriate materials, selecting the right sealing systems, minimizing friction, or providing the product with enough permanent lubrication at the time of purchase. Special greases are made for this purpose, intended to remain in the valves or cylinders indefinitely. To prevent the lubricant from being washed out, it's important to use dry air, as moisture can harm the lubricant. This wash-out effect also occurs with lubricators, so it's crucial to ensure that lubricators never run out of lubricant.
Pneumatic silencer
A pneumatic silencer (muffler) is a device attached to the exhaust port of a pneumatic system component, such as a valve or cylinder, to reduce the noise created by escaping compressed air. It works by allowing the air to expand and slow down before it is released into the atmosphere, which diminishes the noise level. Some silencers can also trap or filter out contaminants from the exhaust air.
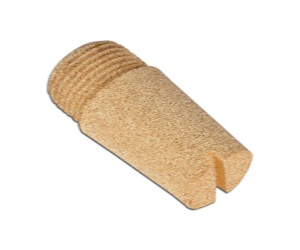
Figure 4: Pneumatic silencer
Aftercoolers
Aftercoolers cool the air after it has been compressed and before it enters the air dryer, which helps remove moisture.
Air dryers
Aftercoolers can take out about 85% of the moisture from the air from a compressor. To remove even more moisture, air dryers are used after the aftercoolers, especially when it's important to keep the air from getting too wet as it moves through the pneumatic system. This is critical in applications that require very dry air, such as in processes sensitive to moisture, to prevent corrosion or to ensure the proper functioning of pneumatic equipment.
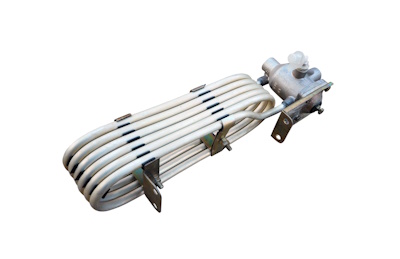
Figure 5: Air dryer for pneumatic system
Drains
Drains remove any accumulated condensate from various points in the pneumatic system, especially from the air receiver and filters.
How to choose the right air preparation unit
Proper air preparation for a device that uses compressed air involves three main factors:
- Purity of compressed air
- Adequate flow rate
- Optimum working pressure
Suitable compressed air purity
Clean air helps the pneumatic system last longer and work efficiently, and it meets the rules for certain industries, like food production. ISO 8573-1:2010 standard sets the purity of compressed air.
- The purity class is determined by three factors - solid particles, water, and oil.
- For each category of these contaminants, the standard specifies the maximum amount of contamination allowed in the compressed air.
The higher the class number, the less pure the air needs to be. Manufacturers of pneumatic components like valves and cylinders give the air purity level needed for their equipment to work properly. Different applications need different levels of clean compressed air to work well.
For example, if a pneumatic system specifies a requirement for compressed air quality as 'Class 2.4.1,' it means:
- For solid particles (first digit), Class 2: The air should have no more than 100,000 particles/m³ of size ≥ 1 micron, 1,000 particles/m³ of size ≥ 5 microns, and 10 particles/m³ of size ≥ 10 microns.
- For water (second digit), Class 4: The air should have a pressure dew point no higher than +3 °C, which limits the amount of water vapor that can condense into liquid water at a given pressure.
- For oil (third digit), Class 1: The air should contain no more than 0.01 mg/m³ of oil.
Sufficient flow rate
Sufficient flow rates are necessary to ensure proper operation and speed of components, for example, to ensure the cylinder pistons move at the speeds they're supposed to.
The flow rate is mostly decided by the size of the openings in the parts and how they're designed. If the parts are designed similarly, bigger ones will allow more airflow. However, the flow rate can change based on the application of these parts. For instance, filters naturally resist airflow and can reduce the flow rate.
Issues such as flow restrictions, leaks, and long pipe runs can cause significant pressure losses. To minimize this, it's recommended to maintain an input pressure to the machine's air preparation system that is 10-20% higher than the operating pressure and to consider upsizing the supply pipes if necessary.
If the right parts are chosen for the job, but the system still isn't getting enough airflow, check the following factors:
- Are the connection points for the air supply undersized?
- Are there issues caused by the long airlines, having too many branches, or tight bends?
- Are the inside surfaces of the airlines rough or dirty?
- Are there any undetected leaks in the system?
The right operating pressure
The operating pressure should match the pressure needed to move the pneumatic parts. Proper pressure ensures the system has enough power to operate.
Each device that uses compressed air is designed to work best within a specific range of pressure. If the pressure is too low, the system won't work as well as it should. If the pressure is too high, it can cause parts like seals to wear out faster, use more energy, and make a lot of noise. So, it's important to consider possible pressure drops when figuring out the right pressure. These pressure drops can happen due to:
- The devices that use the air, like valves, filters, and dryers.
- Long pipes, branches, too tight bends, rough inside surfaces, and dirt in the pipes.
- Undetected leaks.
A pneumatic element's maximum pressure depends on several parameters, like the housing material and the springs used for adjustment.