Clamping Cylinders - How They Work
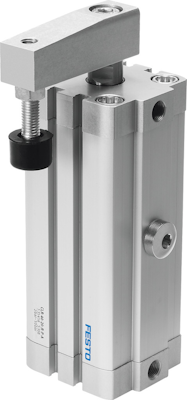
Figure 1: Festo linear/swivel clamping cylinder
Clamping cylinders are used to hold or clamp a workpiece either directly through a pneumatically operated clamping element or via kinematic mechanisms. When inactive, the clamping element moves out of the working area. Clamping pneumatic cylinders can achieve very high holding forces with minimal energy input due to their kinematic design. These cylinders replicate the gripping action performed by humans and are typically not used on its own; it is combined with various types of equipment or mechanisms. It can be mounted on pneumatic slide rails, robotic arms, and other motion mechanisms to move objects from one location to another.
When to choose different clamping cylinders
Festo clamping cylinders are categorized into three types: clamping modules, linear/swivel clamps, and hinge cylinders. Here's a brief overview of each type:
- Clamping modules: Ideal for tight spaces and harsh environments, suitable for flat and linear clamping tasks with moderate forces. They are used in electronics manufacturing, automotive assembly, and packaging machinery.
- Linear/Swivel clamps: Suitable for versatile clamping with linear and swivel motions, suitable for welding applications and compact spaces. They are used in metalworking, woodworking, and PCB manufacturing.
- Hinge cylinders: Designed for high clamping forces and welding processes, particularly in automotive and industrial applications. They are used in automotive manufacturing, heavy machinery assembly, and industrial welding stations.
How air clamp cylinders work
The main parts of a clamping cylinder are:
- Cylinder body: The main housing that contains all internal components. The housing is typically made from materials like aluminum or steel for durability.
- Piston and piston rod/Diaphragm: The piston moves within the cylinder body, driven by compressed air. The piston rod extends out of the cylinder to apply clamping force to the workpiece. In certain models, a diaphragm replaces the piston. When air pressure is applied, the diaphragm expands, exerting force on the clamping area.
- Air inlet/outlet ports: The inlet and outlet ports allow compressed air to enter and exit the cylinder, controlling the movement of the piston or diaphragm.
- Seals and bearings: Ensure airtight operation and reduce friction between moving parts, enhancing the cylinder's efficiency and lifespan.
Working process
- Air supply: Compressed air enters the cylinder through the inlet port.
- Piston movement: For traditional cylinders, the compressed air pushes the piston, causing the piston rod to extend and apply clamping force. In diaphragm-based clamping modules, the air pressure causes the diaphragm to expand, exerting force on the clamping area.
- Clamping action: The piston rod or diaphragm applies force to the workpiece, holding it securely in place. The clamping force can vary depending on the cylinder type and operating pressure.
- Release: When the air pressure is released or redirected to the opposite side of the piston, the piston rod retracts, or the diaphragm returns to its original position, releasing the clamping force.
Festo clamping modules
Figure 2: Festo rectangular (left) and round (right) diaphragm clamping cylinders
Clamping modules are extremely flat diaphragm actuators with short strokes, suitable for a wide range of clamping tasks. Their flat design allows them to be used in tight spaces where other clamping cylinders might not fit. They can achieve clamping forces of up to 1640 N. Available in both round and elongated designs, they can handle both flat and linear clamping tasks. The hermetically sealed design makes them ideal for harsh, dusty environments. The clamping module EV is a short rodless cylinder with a diaphragm. It is single-acting, has a reset function, and is hermetically sealed.
Festo clamping module EV features
These modules are single-acting. The air pressure is applied to a diaphragm within the module, which then exerts force on the clamping area. The clamping modules EV are available in two main versions: rectangular and round. Each version comes in various sizes and stroke lengths, catering to different application needs.
- Rectangular modules: Rectangular modules are ideal for heavy-duty, high-force applications with versatile mounting needs and space constraints.
- Round modules: Round modules are suitable for applications requiring rotational symmetry, ease of integration, and lighter weight.
Table 1: Rectangular and round clamping module features
Feature | Rectangular clamping modules | Round clamping modules |
Available sizes | 10x30 mm, 15x40 mm, 15x63 mm, 20x75 mm, 20x120 mm, 20x180 mm | Ø12 mm, Ø16 mm, Ø20 mm, Ø25 mm, Ø32 mm, Ø40 mm, Ø50 mm, Ø63 mm |
Stroke lengths | 3 mm, 4 mm, 5 mm | 3 mm, 4 mm, 5 mm |
Pneumatic connection | M3, M5 | M3 |
Operating pressure | 2 to 6 bar (29 to 87 psi) | 6 bar (87 psi) |
Ambient temperature range | -20 to +40 °C | -10 to +40 °C |
Clamping force range | 95 N to 1690 N (at 6 bar) | 55 N to 1660 N (at 6 bar) |
Product weight range | 20 g to 270 g | 11 g to 100 g |
Accessories | Foot mounting (HBEV), Pressure plate | Pressure plate |
Application flexibility | Suitable for heavy-duty and space-constrained applications | Ideal for applications requiring rotational symmetry |
Note: The module does not have built-in position sensing or cushioning. Also, the single-acting design may not be optimal for very high-speed clamping and unclamping cycles.
Festo linear/swivel clamps
Linear/swivel clamps (Figure 1) combine linear and swivel movements, allowing tools to be inserted and removed beyond the clamping range. This means that the clamp can move directly towards the workpiece to secure it and then swivel out of the way when the clamping action is not needed. These clamps are versatile and can reliably clamp various workpieces, including wood, sheet metal, and printed circuit boards. They generate clamping forces of up to 1600 N and clamping strokes of up to 50 mm, making them suitable for welding applications.
The linear/swivel clamp CLR combines swiveling and clamping in a single step. The swivel direction is adjustable, allowing adaptation to specific conditions. The CLR is available with a clamping finger accessory and dust and welding spatter protection.
Linear/swivel clamp CLR
Key features
- Dual motion: Combines linear and swivel motion of the piston rod, allowing workpieces to be inserted and removed beyond the clamping range.
- Swivel options: Available in right, left, or straight swivel directions. The swivel direction can be adjusted even after installation.
- Protection: New variants include dust and welding spatter protection.
- Compact design: Suitable for tight installation spaces.
- ISO compatibility: Hole pattern corresponds to ISO 21287, allowing the use of standard accessories.
- Easy assembly: Female threads in the bearing and end caps facilitate easy assembly.
- Clamping finger: Available as an accessory, can be freely adjusted across a full 360° and includes a plug-on rubber cap to protect sensitive surfaces.
- Repairable: Can be repaired using a set of wearing parts.
- Accessories: Compatible with various accessories such as tubing, flow control valves, and push-in fittings.
Technical specifications
- Linear stroke: Available for diameters of 40 mm and above.
- Piston diameters: Range from 12 mm to 63 mm.
- Clamping stroke: Available in 10 mm, 20 mm, and 50 mm.
- Operating pressure: 2 to 10 bar.
- Ambient temperature: -10°C to +80°C.
- Corrosion resistance: Class 2 to Festo standard 940070.
- Materials: High-alloy stainless steel for piston rod, coated wrought aluminum alloy for bearing and end caps, and nitrile rubber/polyurethane for seals.
Festo hinge cylinders
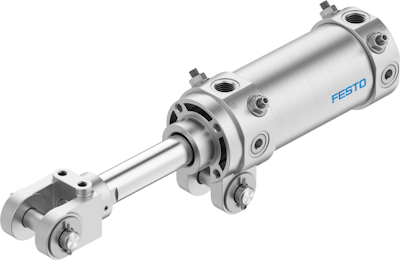
Figure 3: Festo hinge cylinder
Hinge cylinders feature a rod clevis at the end of the piston rod and a hinged fork at the bearing cap, simplifying mounting in clamping devices. An optional clamping unit can prevent the piston rod from slipping when unpressurized. These cylinders generate clamping forces of up to 3016 N and are particularly suitable for clamping components during welding processes, ensuring secure and reliable clamping.
The Festo hinge cylinder DW includes integrated restrictors and end-position cushioning, making it ideal for clamping components in welding processes. The hinged fork on the bearing cap facilitates easy mounting. In the Asian market, the DW is the automotive standard for body-in-white production.
Hinge cylinder DW
Key features
- Welding clamping: Designed for clamping components during welding, ideal for automotive and industrial applications.
- Easy mounting: Swivel bearing on the bearing cap simplifies installation.
- Integrated flow control: Built-in flow control ensures precise speed regulation.
- End-position cushioning: Integrated pneumatic cushioning at both ends for smooth operation and reduced impact.
- Rod wiper seal: Protects against welding spatter, enhancing durability.
- Position sensing options: Multiple options including sensor rails and proximity switches (SMT-8M or SDBT-BSW).
- Flexible pneumatic connection: Rc or G thread connections available on three sides.
- Standards compliance: Meets Asian automotive standards for car body production.
- Customizable rod clevis gaps: Different gaps available to suit specific applications.
- Robust construction: Made from high-quality materials like cast steel and anodized aluminum.
Technical data
- Piston diameters: 50 mm, 63 mm, 80 mm
- Stroke length:
- Standard: 50, 75, 100, 125, 150 mm
- Variable: 10 to 200 mm
- Operating medium: Compressed air to ISO 8573-1:2010 [7:4:4]
- Operating pressure: 1 to 10 bar
- Ambient temperature: -10 °C to +60 °C
- Corrosion resistance class: CRC 0 (No corrosion stress)