Pneumatic Cylinder Maintenance
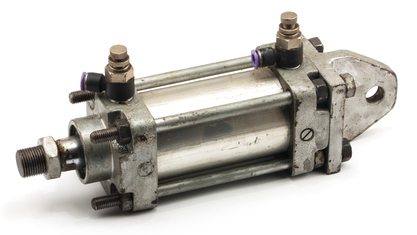
Figure 1: Pneumatic cylinder needing maintanance
Pneumatic cylinders convert compressed air into linear motion. While these cylinders are generally reliable, they can suffer from wear and damage over time, leading to decreased performance and even failure. Proper maintenance, including regular inspection and repair, can help prevent these issues and extend the life of the cylinder. This article explores some of the symptoms of a faulty cylinder, the causes of failure, and the steps involved in repairing or replacing a damaged cylinder. Read our pneumatic cylinder overview article for more information on the design and working of pneumatic cylinders.
Table of contents
- Faulty pneumatic cylinder symptoms
- Typical causes of pneumatic cylinder failure
- Pneumatic cylinder repair
- Pneumatic cylinder preventive maintenance checklist
- Replacing a pneumatic cylinder
- FAQs
View our online selection of pneumatic cylinders
Faulty pneumatic cylinder symptoms
A pneumatic system can encounter a range of issues; it is crucial to identify common indicators that necessitate a pneumatic cylinder repair.
- Slow actuation: Sluggish actuation or failure altogether are clear signs that there is an issue with the pneumatic cylinder. Consistent monitoring of actuation pressure is critical to avoid complete system failure.
- Higher pressure needed for actuation: Typically, a pneumatic cylinder needing higher than normal pressure to actuate is caused by undersized control lines or a faulty metering choke valve that results in insufficient pilot control pressure.
- Hissing sounds: Hissing sounds originating from the air cylinder indicates a system leak caused by a damaged rod seal, worn-out rod, or damaged piston. This leak can cause pressure loss and impede cylinder performance.
- Intermittent start-up: Overloading air cylinders causes stress and higher friction in the seals, leading to intermittent start-up or the bending or breaking of rod ends. Additionally, systems containing energy-absorbing devices or speed-control mechanisms may experience pressure spikes that exceed normal operating pressures, causing the actuator to fall apart.
- Load pulsing: Load pulsing is when the load causes pressure fluctuations in the cylinder's air supply line. These pressure fluctuations can cause problems in pneumatic systems, such as reduced accuracy, slower cycle times, and increased wear on components. Smooth and silent cylinder operation is typical, and any load pulsing suggests the need for repair.
- Premature wear or corrosion: Visible corrosion or premature wear on the cylinder body or end caps is a result of exposure to harsh environmental conditions such as high humidity, heat, or chemicals, which can cause rust, erosion, or pitting, compromising the cylinder's structural integrity and eventually leading to failure.
Typical causes of pneumatic cylinder failure
Side loading
Side loading in a pneumatic cylinder refers to the application of external forces or loads on the piston rod of the cylinder, which are not aligned with the cylinder's axis. When a pneumatic cylinder is designed, it is intended to bear loads in a specific direction along its axis, which is usually aligned with the cylinder's piston rod. However, if a load is applied to the cylinder from a direction that is not aligned with the cylinder axis, it can cause the cylinder to wear out faster or even malfunction. It can cause issues like uneven or accelerated piston rod and bearing wear, seal failure, and cylinder tube scoring (a type of damage that occurs on the inner surface of the cylinder tube due to the presence of foreign particles, corrosive substances, or moisture in the compressed air supply). Sideloading typically arises from improper cylinder installation into the operating system, and prompt repairs are necessary to prevent further damage.
Insufficient lubrication
To avoid problems with a pneumatic cylinder, it is crucial to maintain proper lubrication. Without thorough and constant lubrication, the cylinder's seals will dry out and eventually fail, leading to a potential cause of failure.
Contamination
Contaminants such as particulate matter, oil, water, and other substances can block the operating parts of the cylinder, thereby reducing its functionality and potentially causing total system failure. These contaminants can easily enter the cylinder through the operating environment or the pneumatic air supply, resulting in catastrophic consequences.
Synchronization issues
A system with more than one pneumatic cylinder requires perfect synchronization of each component to operate effectively. To maintain synchronization, various practices and methods must be implemented, and careful monitoring and management are necessary. If the pneumatic cylinders fall out of synchronization, the machine will stop functioning correctly, and the entire system may fail.
Exceeding operational limits
When the pneumatic cylinder is operated outside the intended, optimal performance range, it is subjected to excessive loads that stress its internal components, leading to poor performance and premature failure. Preventative checks and maintenance can help operate within the correct parameters and avoid this issue.
Pneumatic cylinder repair
- Turn off the power supply: Before starting any repairs or maintenance on a pneumatic system, ensure the power supply is turned off, and any remaining compressed air is released. Compressed air in the system can be hazardous and increase the risk of accidents.
- Check the tube, cylinder, and rod seal for rust or damage: The cylinder rod, tube, and seal on the rod are the most susceptible to damage or rust. Therefore, inspect these components thoroughly for any signs of deterioration like visible cracks, corrosion, or damage to the seal. Replace the entire cylinder and mounting parts if the damage is significant. Also, ensure that no dust accumulates on the outer surface of the air cylinder or the mounting bracket. If the damage is minor, it may be possible to repair or replace the damaged components, such as the seal or rod.
-
Lubrication: Check the manufacturer's instructions to see if the pneumatic cylinder requires lubrication. In some cases, extreme environmental conditions, such as high heat or chemical exposure, may require frequent lubrication to prevent damage to the equipment. However, if lubrication isn't necessary, it's best not to use it.
- While inspecting the cylinder and its components, check if the seals are well-lubricated. Apply grease packs to the seals if they are not sufficiently lubricated.
- In general, the following components of the pneumatic cylinder require lubrication:
- Tube gaskets
- Rod seal
- The groove on the piston seal
- The surface of the piston rod
- The outer surface of the piston
- Tube inner surface
- The outer and inner surfaces of the piston seal
-
Repairing cylinder seals: Seals are essential components of pneumatic cylinders that can crack or leak over time, requiring replacement. When replacing seals, it is essential to follow these steps to ensure safe and effective replacement:
- Hold the tube cover securely using a vice, then loosen and remove the rod cover using a spanner.
- Disassemble the cylinder carefully, removing all parts and wiping them clean of grease with a clean cloth.
- Replace the seals with new ones; ensure you install them correctly.
- Reassemble the cylinder, ensuring the tube cover is tightened slightly more.
Pneumatic cylinder preventive maintenance checklist
Wear and tear of a pneumatic cylinder are inevitable. Nevertheless, taking a few simple measures can help prevent early failure, and implementing them consistently and correctly can save time and money.
- Proper Installation: Installing the cylinder correctly will significantly extend its lifespan. Improper tools used during installation can adversely impact the functionality and lifespan of the system. Ensuring that fasteners are properly torqued is crucial to correctly installing tie rods.
- Filters: As specified by the manufacturer, changing filters regularly can help shield the cylinder from contaminants that may cause damage.
- Fittings: It is essential to check for rust or wear on fittings, as many contaminants can infiltrate the pneumatic cylinder from contaminated fittings.
Replacing a pneumatic cylinder
Even with a regular pneumatic cylinder maintenance schedule, its parts occasionally fail and must be repaired or replaced.
- Pneumatic cylinder spare parts like pistons, cylinder bodies, seals, end caps, and mounting hardware can be purchased from the manufacturer and replaced with worn-out ones to ensure optimal performance.
- Pneumatic cylinders designed according to ISO standards can be replaced with any cylinder brand conforming to the same standard. This allows users to choose a pneumatic cylinder based on cost and availability. Read our articles on ISO 15552, ISO 6432, and ISO 21287 for more details on the design features of pneumatic cylinders for various ISO standards.
- Several brands offer repair kits for the cylinders; stock these up and make repairs as quickly as possible. In some cases, pneumatic cylinders can be customized, and a custom-designed cylinder could render the best performance.
However, if there is extensive damage to the cylinder, it's probably time to replace the unit rather than get it repaired. If the problems keep repeating, the pneumatic cylinder may be wrong for the application.
FAQs
Can a pneumatic cylinder be repaired?
Pneumatic cylinders can often be repaired if the damage is not serious. However, if the cylinder is severely damaged, it may not be possible to repair it, and it may need to be replaced.
How do I know if my pneumatic cylinder is bad?
Slow actuation, corrosion, load pulsing, and intermittent start-up are a few signs that the pneumatic cylinder may be bad.