Integrating Pressure Regulators and Safety Valves In Industrial Systems
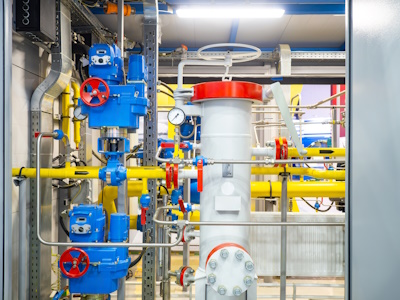
Figure 1: Gas pipelines have pressure regulators and safety valves to maintain safe pressure levels and prevent potential hazards
Integrating pressure regulators and safety valves is crucial for maintaining operational efficiency, preventing overpressure conditions, and ensuring safety in industrial systems. A pressure regulator used in an industry controls the pressure within a system to maintain desired levels, while safety valves release excess pressure and prevent system failures. This article explores the various aspects of integrating pressure regulators and safety valves, providing practical implementation and general maintenance procedures.
Table of contents
- Understanding pressure regulators and safety valves
- Installation best practices
- Typical configuration in an industrial setup
- Integration with control systems
- Maintenance and troubleshooting
- FAQs
View our online selection of pressure regulators and safety valves!
Understanding pressure regulators and safety valves
Pressure regulators
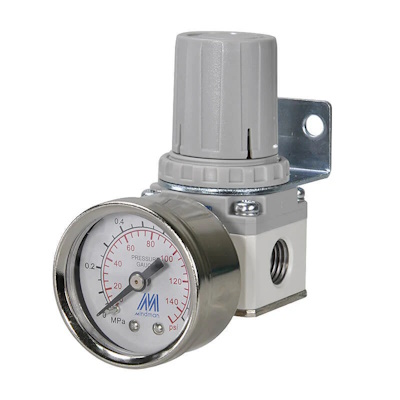
Figure 2: Pressure regulator for compressed air
A pressure regulator controls the pressure of liquids or gasses by lowering a high input pressure to a lower, more manageable output pressure. It ensures a consistent output pressure, even when there are variations in the input pressure, preventing damage to downstream equipment by avoiding pressure spikes. Read our pressure regulator overview article for more details on types of pressure regulators, their applications, and what to consider when choosing between pressure regulators.
Safety valves
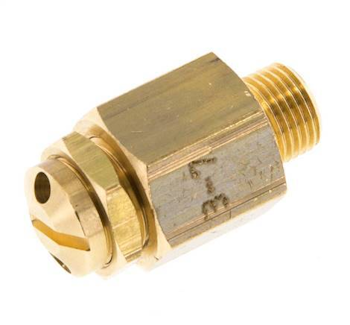
Figure 3: Industrial safety valve for gas
A safety valve is essential for protecting systems from overpressure by quickly opening to release excess pressure when it exceeds the Maximum Allowable Working Pressure (MAWP).
Installation best practices
Pressure regulators
- Upstream of critical equipment: Install pressure regulators upstream of critical equipment or processes that require a stable and controlled pressure. This ensures that the equipment receives a consistent pressure supply, regardless of fluctuations in the upstream pressure.
- Close to the point of use: To minimize pressure drops and response time, place pressure regulators as close as possible to the point of use or the equipment they are protecting.
- Proper Orientation: Ensure the pressure regulator is installed in the correct orientation as specified by the manufacturer to avoid operational issues.
Safety valves
- Downstream of pressure regulators: Install safety valves downstream of pressure regulators. This placement ensures that if the pressure regulator fails or if there is an unexpected pressure surge, the safety valve can relieve the excess pressure and protect the downstream equipment.
- At high points: Install safety valves at the highest points in the system to ensure they vent gas rather than liquid, which is particularly important in systems where both phases are present.
- On pressure vessels and pipelines: Safety valves should also be installed on pressure vessels, boilers, and pipelines to protect them from overpressure conditions.
Typical configuration in an industrial setup
Here’s a brief overview of a pressure reducing station:
- Pressure source: The system starts with a high-pressure source, such as a pump or compressor.
- Pressure regulator: Installed downstream of the pressure source to reduce and control the pressure to the desired level.
- Process equipment: The regulated pressure is then supplied to the process equipment or point of use.
- Safety valve: Installed downstream of the pressure regulator and close to the process equipment to relieve excess pressure and protect the equipment.
For example, in a steam distribution system, a pressure regulator might be installed to reduce the steam pressure from 10.34 bar (150 psi) to 3.45 bar (50 psi) for use in a heat exchanger. A safety valve would then be installed downstream of the pressure regulator, set to open at 4.14 bar (60 psi) to protect the heat exchanger from overpressure.This setting is typically around 20% above the target pressure to ensure safety while avoiding unnecessary release of steam.
Note: In addition to pressure regulators and safety valves, there are other components commonly found in industrial systems, such as pressure gauges, filters, check valves, isolation valves, flow meters, and temperature sensors, which contribute to the overall efficiency and safety of the system.

Figure 4: General arrangement of a self-acting pressure reducing station: High pressure steam in (A), separator (B), condensate (C), pressure regulator (D), safety valve (E), pressure gauge (F), and low pressure steam out (G)
Integration with control systems
Monitoring and data Integration
Install pressure transducers downstream of pressure regulators and safety valves to provide real-time data to the control system, such as a PLC (Programmable Logic Controller) or DCS (Distributed Control System). This continuous monitoring allows operators to track system performance and identify any deviations from the desired pressure.
Manual Adjustment and alarm systems
- Operator interface: The control system can feature an operator interface displaying real-time pressure readings, allowing manual adjustments and responses to safety valve actuations.
- Alarm systems: The system can trigger visual and auditory alarms if pressure deviates beyond set thresholds, prompting operators to take corrective actions.
Documentation and event logging
Operators can document manual adjustments and system conditions in the control system for future reference and analysis. Historical data logged by the control system can be used to perform trend analysis, helping to predict when manual adjustments might be needed and to optimize system performance. For example, a log showing a safety valve opening at 3:15 PM for 30 seconds at 14.1 bar (205 psi) can prompt an investigation into the overpressure cause.
Note: Apart from manual pressure regulators, there are advanced options like smart pressure transducers that enable real-time feedback loops and remote monitoring. These smart devices provide automated adjustments and diagnostics, ensuring precise and dynamic control of system pressure without the need for manual intervention.
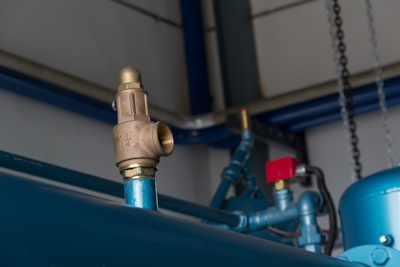
Figure 5: Pressure safety valve installed at discharge of feed gas compressor to protect unexpected pressure spike from the process.
Maintenance and troubleshooting
-
Regular inspections:
- Visual checks: Regularly inspect pressure regulators and safety valves for signs of wear, corrosion, or damage.
- Functional testing: Periodically test the functionality of safety valves to ensure they open at the set pressure.
-
Troubleshooting common issues:
- Pressure fluctuations: If there are pressure fluctuations, check for blockages or leaks in the system, and ensure the pressure regulator is functioning correctly.
- Safety valve actuation: If a safety valve actuates frequently, investigate the cause of overpressure, such as a malfunctioning pressure regulator or a blocked pipeline.
FAQs
What is the primary function of an industrial air pressure regulator?
An industrial air pressure regulator maintains a consistent output pressure from a compressed air system, ensuring optimal performance and safety.
How does an industrial pressure regulator valve contribute to system efficiency?
An industrial pressure regulator valve controls and stabilizes the pressure within a system, preventing pressure fluctuations and enhancing overall efficiency and equipment longevity.