Plastic Solenoid Valves Overview
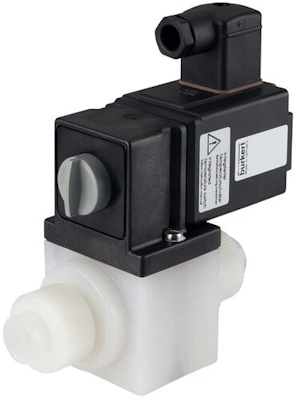
Figure 1: PVC solenoid valve
Plastic solenoid valves are lightweight, cost-effective, and corrosion-resistant. They are commonly used in water treatment, irrigation systems, and general-purpose fluid control applications. Understanding their material properties, compatibility, and operational limits ensures reliable performance and prevents system failures. This article explores the features of plastic solenoid valves.
Table of contents
View our online selection of plastic solenoid valves!
Advantages
- Corrosion resistance: Plastic body solenoid valves are inert to many corrosive media. They are ideal for aggressive environments, including marine and biotechnology applications.
- Material properties: A wide range of plastics ensures compatibility with various chemicals. Options like PTFE offer non-stick properties ideal for food and beverage applications. Refer to our chemical compatibility chart to choose a plastic compatible with the specific chemicals in the application.
- Low-medium pressure and temperature: Plastic materials are ideal for low to medium pressure, such as 10-20 bar (150-300 psi). They operate typically from 60 to 80 𐩑C (140 to 176 𐩑F). However, special plastic materials can handle higher temperatures (see below).
- Lightweight: Plastic valves are significantly lighter than metal valves. This simplifies installation, reduces shipping costs, and minimizes stress on piping systems. Plastic valves are ideal for portable and space-constrained applications.
- Cost-effective: Plastic solenoid valves are generally more affordable than metal valves. This is beneficial for large-scale applications, such as agricultural irrigation systems.
- Insulation properties: Plastic valves provide natural electrical insulation, reducing interference and preventing heat transfer, which is essential in automotive and medical applications.
Read our solenoid valve overview article for more details on the design, operation, and types of solenoid valves.
Applications
Water treatment and management
Plastic solenoid valves are ideal for chlorinated water and chemicals, complying with EPA standards. This makes them suitable for:
- Swimming pools
- Drinking water systems
- Residential and commercial irrigation
- Water softening systems
Chemical processing
These valves withstand exposure to potent chemicals, harsh acids, and bases. This ensures reliable performance in critical chemical processes where precision is crucial.
Aquariums and aquaculture
Plastic solenoid valves are crucial for managing water flow, oxygenation, treatment, and filtration in aquariums and aquaculture. They resist saltwater and biological materials, helping maintain optimal conditions for marine life.
Food and beverage industry
Plastic solenoid valves are ideal for accurately dispensing additives and using advanced food and beverage industry brewing methods. Ensure the plastic is food-grade and complies with FDA, NSF, or EU food safety standards.
Agriculture and irrigation
Plastic solenoid valves are widely used in agricultural irrigation systems. They are ideal for controlling water flow and fertilizers in drip and sprinkler systems. They are budget-friendly and easy to maintain, hence, popular for large-scale agricultural operations.
Material properties
Table 1: Material properties of plastic solenoid valves
Material | Chemical resistance | Temperature tolerance | Mechanical strength | Applications |
Polyvinyl chloride (PVC) | Excellent resistance to acids, alkalis, and salts. Limited resistance to solvents and aromatic hydrocarbons | Typically up to 60 𐩑C (140 𐩑F) | Good tensile strength and rigidity | Water treatment, irrigation systems, and general-purpose fluid control |
Polypropylene (PP) | Superior resistance to a wide range of chemicals, including acids, alkalis, and organic solvents | Can withstand temperatures up to 90 𐩑C (194 𐩑F) | High impact resistance and flexibility | Chemical processing, food and beverage industry, and pharmaceutical applications |
Polyvinylidene fluoride (PVDF) | Excellent resistance to chlorine, bromine, and other halogens, as well as strong acids and bases | Can operate at temperatures up to 80 𐩑C (176 𐩑F) | High tensile strength and abrasion resistance | High-purity applications, semiconductor manufacturing, and aggressive chemical environments |
Polytetrafluoroethylene (PTFE)/Teflon | Unmatched resistance to almost all chemicals, including strong acids, bases, and solvents | Can handle temperatures up to 90 𐩑C (194 𐩑F) | Low friction coefficient and excellent non-stick properties but relatively low mechanical strength | Extreme chemical environments, high-temperature applications, and non-stick requirements |
Polyamide (Nylon) | Good resistance to oils, greases, and hydrocarbons, limited resistance to acids and alkalis | Typically up to 120 𐩑C (248 𐩑F) | High mechanical strength and excellent wear resistance | Automotive parts, industrial components, and consumer goods |
Polyphenylene sulfide (PPS) | Excellent resistance to chemicals, including acids, alkalis, and organic solvents | Can withstand temperatures up to 100 𐩑C (212 𐩑F) | High mechanical strength and dimensional stability | Electrical components, automotive parts, and chemical processing equipment |
Polyether ether ketone (PEEK) | Excellent resistance to a wide range of chemicals, including acids, bases, and organic solvents | Can operate at temperatures up to 90 𐩑C (194 𐩑F) | Exceptional mechanical strength and high-temperature stability | Aerospace, medical devices, and high-performance industrial applications |
Note: The temperature at which a valve operates is influenced by its design, the materials used, thermal expansion, and the heat tolerance of its electrical components. Always consult the manufacturer's specifications to ensure the valve suits your application.
Limitations and considerations
While plastic solenoid valves have many benefits, their limitations must be considered when choosing them for specific applications. For more information, read our solenoid valve selection guide for more details on how to choose a solenoid valve for an application.
- Temperature and pressure limitations: Plastic solenoid valves typically have lower temperature and pressure tolerances than metal valves.
- For example, PVC valves operate up to 60 𐩑C (140 𐩑F), while polyamide can handle up to 120 𐩑C (248 𐩑F). Composite materials and plastic-metal hybrids can help in high-pressure applications.
- UV degradation: Plastics like PVC can become brittle with prolonged UV exposure. For outdoor use, use UV-stabilized plastics or apply protective coatings. Always consult manufacturer specifications for UV resistance.
- Mechanical wear and tear: Plastics offer good chemical resistance but are less durable than metals against mechanical wear.
- Material compatibility: Plastic valves are chemically versatile but can degrade with certain substances. Ensure the plastic and internal parts are compatible with the intended media to avoid leaks or failure.
FAQs
What are plastic solenoid valves used for?
Applications requiring chemical resistance, cost efficiency, and a lightweight design use plastic solenoid valves. Common applications are water treatment, irrigation, and the food and beverage industries.
Can a plastic water solenoid valve handle chlorinated water in swimming pools?
Plastic water solenoid valves are corrosion-resistant and can effectively handle chlorinated water in swimming pools.