Sanitary Diaphragm Valves
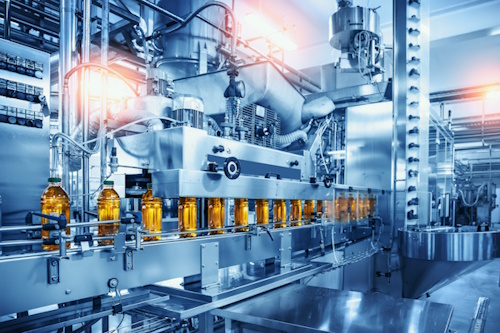
Figure 1: Sanitary diaphragm valves are used in food and beverage industries for their contamination-free processing and easy sterilization.
Sanitary diaphragm valves are essential components in controlling the flow and maintaining the purity of fluids in sectors demanding high hygiene standards, such as the pharmaceutical, biotechnological, and food and beverage industries. These valves utilize a flexible diaphragm that separates the flow of fluids from the operating mechanism, ensuring contamination-free operation. This article explores the specifics of sanitary diaphragm valves, exploring their applications, design features, and the regulatory standards they adhere to, to ensure they meet the stringent requirements of sanitary industries.
Sanitary diaphragm valve applications
Sanitary diaphragm valves are used in various industries where hygiene and cleanliness are paramount.
- Food and beverage processing: Used for transferring various food and beverage products like milk, wine, beer, juices, and syrups.
- Dairy processing: Ideal for handling milk, cream, cheese whey, and other dairy products.
- Pharmaceutical production: Suitable for sterile environments and handling sensitive pharmaceutical solutions.
- Biotechnology applications: Used in bioreactors, fermentation tanks, and other equipment for sterile media transfer.
Read our diaphragm valve overview and diaphragm valve applications articles for more information on the working and typical applications of conventional diaphragm valves respectively.
Design features of sanitary diaphragm valves
The design of sanitary diaphragm valves makes them particularly suited for these applications:
-
Material selection:
- Valve body: Primarily uses 316L stainless steel for its superior corrosion resistance against harsh cleaning solutions and the products themselves (e.g., acidic fruit juices, caustic cleaning agents). Other options include Hastelloy for extreme chemical resistance or titanium for biocompatibility.
- Diaphragm: FDA-compliant elastomers like EPDM (ethylene propylene diene monomer) or PTFE (polytetrafluoroethylene) are popular choices. EPDM offers good chemical resistance and steam sterilization compatibility, while PTFE has excellent chemical resistance and high-temperature tolerance. Alternative materials like FFKM (perfluoroelastomer) provide even broader chemical resistance for specific applications
- Surface finish: Internal surfaces are polished to a high finish to minimize microbial growth and facilitate easy cleaning and sterilization. Electropolishing removes microscopic imperfections and creates a smooth, ultra-clean surface that minimizes bacterial adhesion and simplifies cleaning.
- Ra values: "Ra," or Arithmetic Mean, measures the average value of the surface's peaks and valleys, with lower numbers signifying a smoother finish. Surface roughness is measured in micrometers (µm). Sanitary diaphragm valves typically have Ra values less than 0.8 µm to promote easy cleaning and reduce bacterial harborage points.
- Self-draining capability: The design of hygienic diaphragm valves often includes self-draining features to prevent fluid retention and microbial growth.
- Angled valve bodies: Specific designs have a slight angle to the body, ensuring complete drainage and eliminating fluid pockets where bacteria can grow.
- Internal chamfers: Chamfered edges on internal surfaces prevent fluid pooling and promote complete evacuation during cleaning cycles.
- Weir design: Many sanitary diaphragm valves utilize a weir design, which reduces dead legs and areas where bacteria can harbor, making them preferable over other valve types for sanitary applications. The weir configuration facilitates smooth flow, reducing turbulence and minimizing product build-up on internal surfaces.
- Crevice-free design: Minimizes potential hiding spots for bacteria and simplifies cleaning procedures.
- Minimal gaskets and seals: Utilizes minimal gaskets and o-rings, reducing potential hiding spots for bacteria and simplifying cleaning procedures.
- Streamlined flow path: The flow path is designed with smooth curves and minimal protrusions to prevent product build-up and enhance cleanability.
- Sanitary bonnet enclosure: In specific designs, the bonnet area is fully enclosed and sealed to prevent any ingress of particulates, fluids or atmosphere into the upper valve body.
- Clean/Sterilized ports: Ports built into the diaphragm valve body allow for CIP spray balls or SIP connections to reach all interior surfaces for cleaning and sterilization.
-
Sanitary valve connections:
- Clamp: Tri-clamp connections offer a leak-proof seal, easy disassembly for cleaning, and a smooth internal surface for optimal flow.
- Flange: Flanged connections are suitable for high-pressure applications and provide a secure, permanent joint. Sanitary flanges have a smooth finish to minimize areas for product build-up.
- Weld: Butt welds offer a permanent, leak-proof connection ideal for high-pressure and high-purity applications. However, this option requires specialized welding equipment and expertise.
Read our diaphragm valve actuation article for more information on the various actuation mechanisms for diaphragm valves.
Certifications and regulations
Diaphragm valves must comply with several certifications and regulations to ensure they meet the rigorous standards required for sanitary applications,
- FDA compliance: Materials that come into contact with the product must be FDA approved, ensuring they are safe for use in food, pharmaceuticals, and other consumable products.
- USP Class VI: USP Class VI certification ensures that the materials used do not leach harmful substances into the product, making them suitable for pharmaceutical applications.
- 3-A sanitary standards: 3-A sanitary standards apply to dairy and food processing equipment, ensuring that equipment can be adequately cleaned and sanitized.
- EHEDG certification: EHEDG certifies that the valve design adheres to the highest hygienic requirements, ensuring minimal risk of contamination.