Solenoid Valves & Power Supply Voltage
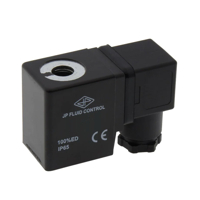
Figure 1: 24V DC solenoid valve coil
Solenoid valve voltage is the electrical voltage needed to energize the solenoid valve coil, creating a magnetic field that moves a plunger or armature to open or close the valve. Solenoid valve coils are available in various voltage ratings; these ratings must match the power supply to ensure proper functionality and longevity. It is crucial to consider what happens when using voltages of different ratings, as mismatched voltages can lead to performance issues or damage. This article explores the importance of voltage considerations, including voltage tolerance, frequency matching, and best practices for selecting and troubleshooting solenoid valve coils.
Table of contents
- Considerations for solenoid coil design parameters
- Are solenoid valve coils interchangeable?
- Practical examples for understanding solenoid valve voltage
- Troubleshooting and best practices
- FAQs
View our online selection of solenoid valves!
Considerations for solenoid coil design parameters
A solenoid valve operates by using an electromagnetic solenoid coil to control the movement of a valve mechanism, thereby regulating the flow of fluids through it. A solenoid coil has a wire, typically made of copper or aluminum, wound around a hollow core. These coils can operate with either direct current (DC) or alternating current (AC) and are available in various voltage ratings, with 6V, 12V, 24V, 120V, and 220V being the most common. Low-voltage coils (less than 24 volts) are typically used for smaller applications such as home appliances, automotive systems, and small-scale automation equipment, while higher-voltage coils (over 24 volts) are suited for industrial applications and heavy machinery.
Under and over voltage in solenoid valves
The nominal or operating voltage, which is the voltage required to actuate (shift) the valve, is usually printed on the solenoid valve body or coil.
Under voltage
Applying less than the nominal voltage can lead to a slower "on" response time or prevent the valve from actuating altogether. For solenoid valve coils, there is typically a working voltage range of ±10% of the rated voltage. For example, if the rated voltage is AC 220V, the minimum working voltage would be approximately 198V AC. Using a voltage that is too low can cause several issues:
- The spool or plunger cannot pull in, leading to coil burnout
- Slower response time of the valve
- Excessive noise from the coil
- Overheating of the coil
In case of these symptoms, use a multimeter to check the supply voltage to the solenoid valve coil. If the supplied voltage is close to the rated voltage, the coil may be at fault and should be replaced.
Over voltage
Applying more than the nominal voltage results in overvoltage, which can speed up the "on" response time of the valve. This can cause the spool or plunger to move quicker, which might be a desired effect. However, this does not necessarily mean the overall system will actuate faster, but rather that there is less time between the coil being energized and the change in flow path. However, excessive overvoltage can permanently damage the coil.
Excessive overvoltage can lead to several critical issues:
- Coil burnout: Rapid overheating can quickly lead to coil failure.
- Increased thermal waste: Higher power consumption generates excessive heat, degrading coil components.
- Reduced lifespan: Continuous overvoltage exposure shortens the valve's lifespan.
Manufacturers typically advise never to exceed the specified voltage limits. Overvoltage in the range of 50-100% above the nominal voltage can be tolerated only for a very brief period, usually a second or so. Prolonged exposure to such high voltage levels will almost certainly result in rapid coil burnout.
Frequency considerations for AC coils
AC solenoid coils are designed to operate at specific frequencies, typically 50Hz or 60Hz. The frequency affects the inductive reactance of the coil, which in turn influences the current flow and magnetic field strength. Using a coil designed for 50Hz on a 60Hz supply, or vice versa, can lead to inefficient operation, increased heat generation, and potential damage.
For example, a solenoid coil rated for 230V, 50Hz should not be used with a 230V, 60Hz power supply without verifying compatibility. The higher frequency (60Hz) will reduce the inductive reactance, potentially increasing the current through the coil and causing overheating. Manufacturers often specify dual-frequency ratings (e.g., 230V, 50/60Hz) to indicate compatibility with both frequencies.
Cost
The cost of building a system using a DC (direct current) supply is generally higher than one using an AC (alternating current) supply. This is because the operating current for a DC supply is higher than that for an AC supply, necessitating additional measures to prevent voltage drops on the return line.
Inrush current and holding current
AC solenoids often experience a high inrush current followed by a lower holding current. If the spool or plunger jams, the constant high current can damage the coil through overuse or overheating, a condition known as coil "burnout." This issue is almost exclusive to AC coils and may result from a fault in the valve, such as a jammed spool or plunger, rather than a fault in the coil itself.
Are solenoid valve coils interchangeable?
AC vs DC solenoid coils
AC solenoid coils are powered by alternating current, which switches polarity multiple times per second. They often include a shading ring to prevent vibrations and humming caused by the zero-crossing of AC current. AC solenoids are commonly used in industrial applications where high power and rapid response are required. On the other hand, DC solenoid coils are powered by direct current, providing a steady magnetic field. Their design is simpler than AC coils as they do not require shading rings. DC solenoids are typically used in applications requiring precise control and lower power consumption, such as automotive systems and small appliances.
Interchangeability considerations
- Voltage compatibility:
- Matching voltage: Ensure the replacement coil matches the voltage rating of the original coil. For example, a 24V DC coil should replace another 24V DC coil.
- Current differences: AC coils have higher impedance due to inductive reactance, which means using an AC coil with a DC supply without adjusting the voltage can lead to overheating and damage.
- Physical dimensions: The replacement coil must physically fit the solenoid valve assembly. This includes matching the core diameter, length, and mounting configuration.
- Electrical characteristics:
- Impedance and resistance: AC coils have different impedance characteristics compared to DC coils. Using an AC coil in a DC circuit or vice versa without proper adjustments can lead to improper operation or damage.
- Shading rings: AC coils often include shading rings to mitigate vibrations. DC coils do not have this feature, so using a DC coil in place of an AC coil might result in operational issues.
For example, replacing a 24V AC coil with a 24V DC coil in a solenoid valve designed for AC operation can cause the valve to malfunction due to the lack of a shading ring in the DC coil, leading to vibrations and noise. Similarly, using a 24V DC coil in place of a 24V AC coil without adjusting the voltage can result in excessive current flow, potentially burning out the coil.
In short, while solenoid valve coils can be replaced, they are not universally interchangeable between AC and DC types without careful consideration of voltage, physical dimensions, and electrical characteristics. Always ensure compatibility to maintain the proper function and longevity of the solenoid valve.
Practical examples for understanding solenoid valve voltage
Using a 110V power supply for 120V solenoid valve
When considering the compatibility of a 110V power supply with a 120V solenoid coil, it is essential to evaluate the voltage tolerance of the coil. Assume the 120V coil has a voltage tolerance of ±10%. This means it can operate safely within the range of 108V to 132V. The 110V power supply falls within this range (108V to 132V), making it technically compatible. However, operating the coil at 110V, which is near the lower end of its tolerance range, may result in slightly reduced performance. The magnetic field generated may be weaker, leading to slower actuation times or reduced force.
Note: Always check the manufacturer's recommendations for the voltage tolerance for the particular solenoid. This ensures compatibility and prevents potential damage or malfunction.
Using a 24V DC power supply for 12V DC solenoid coil
Using a 24V DC power supply with a 12V DC coil presents significant challenges due to the overvoltage condition.
- Overvoltage risk: Applying 24V to a coil rated for 12V exceeds the coil's voltage tolerance, leading to excessive current flow, overheating, and potential coil damage or failure.
- Current increase: The coil's resistance is designed for 12V operation. Doubling the voltage will double the current, resulting in a fourfold increase in power dissipation (P = V^2/R).
To safely use a 24V power supply with a 12V coil, a voltage regulator or DC-DC converter should be employed to step down the voltage from 24V to 12V. Also, implementing a current-limiting circuit can protect the coil from excessive current during transient conditions.
Troubleshooting and best practices
When troubleshooting solenoid valve coils and ensuring best practices, it is essential to be aware of common symptoms of incompatibility and follow guidelines for selecting the right coil and power supply.
Common symptoms of incompatibility
- Overheating: Excessive heat generation can indicate voltage mismatch or insufficient current handling.
- Erratic operation: Inconsistent actuation or failure to actuate can result from improper voltage or frequency.
- Noise and vibration: Unusual sounds or vibrations may signal electrical or mechanical incompatibility.
Tips for selecting the right coil and power supply
- Match voltage and current type: Ensure the coil's voltage rating and current type (AC or DC) align with the power supply.
- Check voltage tolerance: Verify that the power supply voltage falls within the coil's specified tolerance range.
- Consider frequency for AC coils: Ensure the power supply frequency matches the coil's design (e.g., 50Hz or 60Hz).
FAQs
Are solenoid valve coils AC or DC?
Solenoid valve coils can be either AC or DC, depending on the application and design requirements.
How to test a 12V solenoid coil?
Apply 12V to the coil and measure resistance with a multimeter. Check for continuity and ensure resistance matches manufacturer specs.