Thermowell
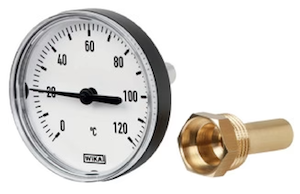
Figure 1: A bimetallic thermometer and a brass thermowell
A thermowell is a tube that shields temperature sensors, such as bimetallic thermometers or resistance temperature detectors, from the extreme conditions of industrial processes. These protective tubes are used in pipes, tanks, and reactors. Thermowells protect against heat, pressure, corrosive substances, and physical stress and allow for easy removal, replacement, or maintenance of the temperature sensor. This article further discusses the design, advantages, and disadvantages of thermowells and how to select them for an application. Read our article on bimetallic thermometers for an example of what thermowells protect.
Table of contents
View our thermowell and bimetallic thermometer selection here!
Thermowell design
Thermowell shape
There are three main types of thermowell designs: straight, tapered, and stepped. The different designs play important roles in different processes to ensure effective temperature measurement and sensor protection.
- Straight thermowells: Straight thermowells have a consistent diameter along their entire length. This thermowell shape is suitable for moderate processes with low pressure-induced stress.
- Tapered thermowells: Tapered thermowells have a linearly reducing diameter from the base to the tip. This shape is suitable for vibration resistance and stress from high-pressure and high-velocity flow applications.
- Stepped thermowells: The diameter of stepped thermowells changes abruptly at certain points along the tube's length. This design is a middle ground between the straight and tapered designs.
Thermowell shape advantages and disadvantages
Advantages | Disadvantages | |
Straight |
|
|
Tapered |
|
|
Stepped |
|
|
Thermowell connection types
The type of connection between the thermowell and the process system (e.g., pipes, reactors, and tanks) depends on the process' conditions, temperature, pressure, and application requirements. The four common connection types are threaded, welded, flanged, and socket welded.
- Threaded: Threaded thermowells have external threads on the base that screw into the process system. This connection type is for low- to medium-pressure applications.
- Welded: Welded thermowells are permanently welded to the process system. The connection is strong, secure, and leak-proof. This connection type is suitable for high-pressure and high-temperature applications.
- Flanged: Flanged thermowells use standard flanged connections to connect to the system. These are suitable for a variety of application parameters, including high-pressure and corrosive applications.
- Socket welded: Socket welded thermowells are welded into a socket in the process system instead of directly to the system. This connection type is suitable for medium- to high-pressure applications.
Thermowell connection type advantages and disadvantages
Advantages | Disadvantages | |
Threaded |
|
|
Welded |
|
|
Flanged |
|
|
Socket welded |
|
|
Thermowell advantages and disadvantages
Advantages
- Sensor protection: Thermowells protect temperature sensors from the process media that may have high pressure or temperature, or corrosive substances. This leads to increased sensor lifetime.
- Maintenance: Threaded and flanged thermowells allow for easy removal, replacement, or maintenance. This prevents downtime, enhances productivity, and reduces maintenance costs.
- Variety of materials and designs: Due to the variety of materials and designs, thermowells are available for a large variety of industrial applications.
Disadvantages
- Reduced response time: Because the thermowell adds a layer between the media and the sensor, the measurement response time is reduced. This can be mitigated using tapered and stepped thermowells.
- Additional cost: Thermowells add to the overall cost of the temperature measurement system.
- Vibration or fatigue failure: High-velocity fluid flow conditions can damage thermowells. Tapered thermowells are the most resistant to these vibrations.
- Installation: Specifically welded and socket-welded thermowells require extra skill and time to install.
Selection criteria
When selecting a thermowell, consider the following criteria:
- Process conditions: The thermowell needs to withstand the process' temperature and pressure. Check the temperature and pressure rating of a thermowell before selecting it.
- Material: Common thermowell materials include stainless steel, Inconel, and Hastelloy. When choosing a material, consider chemical compatibility, temperature resistance, and mechanical strength.
- Design and shape: Tapered and stepped thermowells are better suited for high-stress and high fluid flow applications. Straight thermowells are suitable for moderate process conditions.
- Connection: Threaded and flanged connections are relatively easier to install but also provide leak paths. Welded and socket welded connections are better for high-pressure applications but cannot be easily removed and replaced.
- Immersion length: The thermowell covered sensor should be fully submerged in the process media without touching the walls of the process system.
- Response time: Ensure the thermowell's response time is suitable for the application. Thinner-walled thermowells (tapered or stepped) typically have faster response times.
FAQs
What are thermowells used for?
Thermowells fit around temperature sensors to protect them from the process' conditions.
How many types of thermowells are there?
Thermowells can have a straight, tapered, or stepped shape. They can connect to the process system with a threaded, flanged, welded, or socket welded connection.