Air Compressor Oil
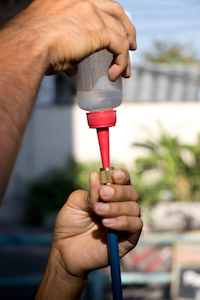
Figure 1: Filling compressor lubricant into an air compressor’s hose.
Air compressor tool oil goes into the compression chamber to cool the machine. It provides sealing and sufficient lubrication to the moving parts and aids noise dissipation. There are oil-free air compressors as well. This article explores the various types of air tool oil, their features, benefits, and viable substitutes. Read our pneumatic tool oil article for more information on the importance of oil in pneumatic tools.
Note: Currently we do not sell any lubricants.
Table of contents
- Air compressor tool oil
- Oil-injected air compressor working
- Selecting the right oil for the air compressor
- Air compressor oil substitutes
- Lubricated air compressor maintenance
- FAQs
Air compressor tool oil
Pneumatic air compressor oil greases the mechanical components, preventing damage from overuse. Depending on the viscosity and additives, there are two types of oil for air compressors:
- Mineral oil: Petroleum refining produces mineral oil. This oil is cheaper than synthetic oil and is suitable for medium and light-duty work at home that doesn’t require regular compressor use.
- Synthetic oil: Synthetic oil is created in laboratories using a synthetic base. It protects the machine from overheating and lets the compressors work more smoothly and quietly. Synthetic oil can be used with a wider temperature range than mineral oil. Industrial air compressors that function more frequently use synthetic oil.
Some air compressors require oil for lubrication, whereas others do not.
- Lubricated compressors: Lubricated compressors require oil to keep the machine running smoothly.
- Oil-free compressors: Oil-free air compressors either have no mechanical contact inside the compression chamber or do not need alternate materials to protect the compressor without lubrication. Most oil-free compressors use materials like water or Teflon to ensure the smooth running of the compressor.
Oil-injected air compressor working
Oil is added to the compression element in a rotary screw oil-injected air compressor. The air compressor design varies slightly between manufacturers, but the essential parts and the principles remain the same.
- The screw element at the air end sucks in the air from outside through the air inlet filter. The filter removes the dust and dirt from the incoming air, protecting the screw element from damage.
- An inlet valve opens and closes to control airflow to the screw element. When the valve opens, the compressor is in the ‘loaded’ condition, where the equipment compresses air and pumps it into the compressed air system. When the inlet valve is closed, it shuts off the air supply to the compressor.
- The screw element works like a pump, compressing the air. During this step, the user injects oil into the screw element. The air gets hot as it is compressed; the oil cools the air and lubricates the clearances between the screws. The output of this stage is a mixture of compressed air and oil.
- The compressed air and oil mixture leaves the screw element through a one-way valve. The valve ensures that the oil does not flow back into the compressor element through the exit pipe when the compressor stops.
- Most of the oil is separated from the compressed air in a separator tank using centrifugal force. The bottom of the tank collects the separated oil.
- The separated oil is hot, and an oil cooler cools it. A thermostatic valve controls the amount of cooling required.
- The oil then flows through a pneumatic oil filter that removes all the dirt and dust collected in the oil.
- The oil cycles back into the compressor element for further use.
- Clean and compressed air then passes through a minimum-pressure valve. The minimum pressure valve is a spring-loaded valve that opens at a specific pressure (approximately 2.5 bar or 36.2 psi). The valve ensures there is always a minimum pressure inside the compressor.
- The compressed air is very hot at this point (about 80 degrees Celsius or 176 degrees Fahrenheit). The compressed air passes through an after-cooler that lowers the air temperature to 25 - 40 degrees Celsius (77 - 104 degrees Fahrenheit).
- Cooling the compressed air condenses a lot of water vapor inside the after-cooler. This water mixes along with the compressed air. The mixture travels through a moisture or condensate trap that separates the water from the compressed air. A hose drains out the separated water, and the compressed air finally leaves the compressor.
Selecting the right oil for the air compressor
Apart from protecting the mechanical components and the motor, using the right oil on the air compressor has significant benefits.
- Oxygen decrease: Additives within the pneumatic compressor oil slow down the acidification and oxygenation processes.
- Enhance the lifespan: Selecting the right pneumatic air line oil can reduce unexpected machine breakdowns and protect internal elements during stationary movements.
- Viscosity in cold temperatures: Certain oil types fail to do their job once the temperature drops, but air compressor oils maintain their low viscosity even at low temperatures.
- Anti-foaming abilities: Air bubbles rising to the oil surface produces foam. This exposes more of the oil’s surface to oxygen, thus increasing oxidation. Without anti-foaming additives, the foam saturates the oil, decreasing the compressor’s lifespan. This is because saturated oil creates a pressure drop that leads to increased energy consumption.
- Demulsification: Air compressor oil contains additives that improve water separation. This protects the compressor from water and oil emulsions.
Reciprocating and rotary screw air compressors can run with various oil products. But, manufacturers recommend using synthetic oil as they do not contain sulfur or additives that can lead to unwanted buildup on valves. There are multiple benefits of using synthetic oil for rotary screw air compressors.
- Less oil consumption: Synthetic oil consumption happens at a lower rate; hence, the oil can be added less frequently.
- Longer lifespan: Synthetic oil can improve the lifespan of a rotary air compressor by approximately eight thousand hours.
- Fewer deposits: Synthetic oils significantly reduce deposits such as sludge and varnish that can negatively affect the compressor’s performance and cause premature wear and tear.
Synthetic oil has multiple advantages on reciprocating air compressors.
- Less accumulation of carbon: Synthetic oil reduces the amount of carbon accumulating on the valves and reduces feed rates drastically.
- Extended lifespan: Synthetic oil prevents premature wearing out of packings and piston rings, thus increasing the compressor's lifespan.
- Safer operation: The flashpoints and auto-ignition temperatures are significantly higher for synthetic oils
Which air compressor oil is best?
The choice of oil for an air compressor depends on the type of compressor, its life cycle, and its application. Both mineral and synthetic oil are suitable for air compressors.
- In general, compressors with small or medium dimensions that work more frequently use mineral oils. Compressors used at home mostly use mineral oil.
- Compressors used in industrial or professional applications use synthetic oil as it provides better protection against overheating.
Air compressor oil substitutes
There are some acceptable alternatives if a user cannot use the oil made specifically for the air compressor. However, it is always recommended to use the manufacturer's recommendation to ensure optimal device performance.
- Hydraulic oil: Hydraulic oil is an acceptable substitute for air compressor oils. The oil has a low viscosity in lower temperatures, meaning it flows freely, given its low density. Also, hydraulic oil doesn’t oxidize, preventing compressor parts from rusting.
- Motor oil: Motor oil contains certain detergents that function well on internal combustion engines. However, these detergents cause excessive carbon buildup, which can be harmful. Hence, use non-detergent motor oil on an air compressor.
- Automatic transmission fluid: Automatic transmission fluids (ATF) primarily find application in car transmission, but certain kinds can be used in air compressors. The fluids reduce wear and tear, cool components, and resist breakdown. However, most ATFs do not function well with compressors and may cause damage.
Lubricated air compressor maintenance
Use the correct oil
Always choose an oil that matches the air compressor installation, as it ensures the compressor runs smoothly and efficiently over time.
Check for air and oil leaks
Conduct leak detection surveys to quickly identify air or oil leaks in a compressor system, as these leaks can drastically reduce the system efficiency.
Airend inspection
The airend, or air end, of a compressor generally lasts up to 44000 hours if maintained correctly. Poor lubrication, overheating, corrosion, and condensation damage the airend resulting in its breakdown or malfunction. Regularly inspect the air end for any issues to diagnose a problem early on.
Check hoses periodically
Inspect the compressor hoses regularly and ensure they are not corroded or cracked, as it can cause leaks.
Drain condensation from air receiver tanks
Drain the receiver tank regularly to keep it clean and ensure smooth operation. Moisture buildup can damage the compressed air output.
Check air filters
A poorly managed air filter allows dirt and dust particles from the outside into the device. This forces the compressor to work harder to intake air. Replace the air filter in the case of dust buildup.
FAQs
What are the differences in pneumatic air tool oils?
Mineral oil is produced from petroleum refining, and it is much cheaper than synthetic oils. Synthetic oil is created in laboratories using a synthetic base. Mineral oil is used in light-duty air compressors for residential applications, whereas synthetic oil is mostly used in industrial applications.
What is the difference between air tool oil and compressor oil?
Air tool oil is very thin, and the oil cannot meet the demands of the air compressor.
Can I use motor oil in pneumatic tools?
Use motor oil that doesn’t have detergent additives. Detergents present in the oil cause excessive carbon buildup, which can be harmful to the machine.
Can I use regular oil in my pneumatic compressor?
Use mineral or synthetic oils for the air compressor to improve its efficiency. Always refer to the manufacturer’s handbook for the type of oil compatible with the system.
Do all pneumatic nailers need to be oiled?
Oil all pneumatic nailers (except oilless nailers) regularly for better performance.