Condensate Drain Valve
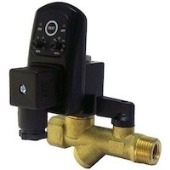
Figure 1: Condensate drain valve
A condensate drain valve is an important part of compressed air systems that removes unwanted moisture and contaminants from the air. By doing this, it helps keep the air clean and dry, which is essential for the system to work well. The valve can drain the moisture without wasting much air or needing to stop the system. This helps protect and extend the life of the compressor and other parts of the system.
Table of contents
- Condensate drain line
- Compressed air
- Moisture in compressed air
- Types of condensate drain valves
- Selection criteria
- Applications
- FAQs
View our condensate drain selection here!
Condensate drain line
The condensate drain line is the component of the condensate drainage system through which the condensate is released to ensure quality and efficient operation. Condensate that builds up in the system can be harmful if not drained properly. The moisture can lead to corrosion or wash away the lubrication required for the equipment to operate. The presence of condensate also affects the quality of dry air supplied to the system. However, the drain line requires the proper sizing of the pipes. Undersized piping can cause blockage in the drain line, also known as air-locking.
Compressed air
Compressed air is the air that is compressed to achieve a higher pressure than atmospheric pressure. Usually, the pressure is 5-8 bar. This compressed air travels through a system of pipes before it is released back to the atmosphere through pneumatic equipment or other applications that use the pressure for a specific purpose. For example, compressed air is used in industrial processes to power pneumatic equipment such as power tools, spray paint, air motors, etc. It is also used in braking systems of trains, buses, and large trucks or to start engines of large ships. It is even used for pneumatic posts, for example, in banks.
Moisture in compressed air
The air that we breathe is not suited to turn into compressed air without being treated first. Atmospheric air is full of pollution. One cubic meter of air can easily contain 100 million airborne particles. They consist of soot, pollen, dust, organic compounds, water vapor, etc. When the air is compressed, the amount of moisture or water vapor increases because water vapor is not compressible. Air compression causes the air temperature to rise significantly.
Therefore, the air is still able to contain the water vapor at that point. But as it begins to cool, the water vapor begins to condensate. The condensate consists of water, compressor oil, dirt, and other contaminants. This mixture of water and contaminants must be drained periodically from the system to avoid damages to equipment and maintain efficient compressed air delivery. Condensation is a serious problem in compressed air systems and is one of the primary reasons for failures and breakdowns.
Types of condensate drain valves
The condensate drain valves can be classified as manual condensate drain valve and automatic condensate drain valve.
Manual condensate drains valves
As the name suggests, manual drain valves operate manually to discharge the accumulated condensation. The primary concerns with manual valves are:
- Operators can forget to drain, causing excess condensate to accumulate in the system.
- Operators can leave them partially open all the time. This method does drain the condensate continuously but leads to continuous waste of compressed air.
Automatic condensate drains valves
Automatic condensate drains function without manual intervention. They operate efficiently to drain condensate from compressed air systems. Most of them are electrically operated, but some can operate without the use of electricity. There are three common types of automatic drain valves:
Electronic timer drains
Electronic timer drains incorporate a solenoid valve and an electric timer. The timer usually has two types of settings:
- ON period: The amount of time the valve needs to stay open.
- OFF period: The time between openings.
Many timers have two rotary control knobs on the face of the timer module. Usually, the ON period can be set from 0 to 10 seconds, and the interval time of the OFF period from 0 to 45 minutes. Other timers have a digital display with push buttons and a more comprehensive range of program settings.
Electronic timer drains are a popular choice, easy to install, cost-effective, and have a reliable operation when installed with an inlet strainer. Upon actuation, the solenoid is energized, the condensate drain opens, and the cycle time begins. At the end of the pre-set "ON" time, the solenoid is de-energized and remains so until the interval time is over.
The timer settings can be adjusted to suit the discharge requirement of the compressed air system. This adjustment ensures minimum loss of air during condensate discharge. The ON time needs to be set long enough to drain all the condensate but short enough not to waste any compressed air. The OFF time needs to be set long enough for some condensate to have accumulated but not too long to avoid problems in the system due to condensation. This requires some initial manual fine-tuning, but it is both effective and reliable once it is set. The use of an inlet strainer on the solenoid valve is highly recommended. This keeps contaminants from clogging the orifice inside the condensate drain and ensures its proper working and longevity. Disadvantages of this drain type are that the valve may not open long enough to eject all the condensate or may stay open too long, wasting compressed air. The oil particles contained in the condensate can change partly because of high velocities and direction changes, forming stable emulsions and causing problems with proper condensate separation and ejection. It is recommended to check the drain settings regularly. Learn more in our pneumatic oil article.
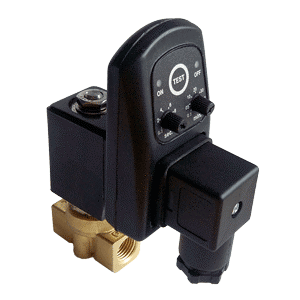
Figure 2: Automatic analog and digital condensate drain valve
Electronic level-controlled condensate drains
These drains are also called "Zero Air Loss" drains and have an electronic capacitive sensor monitoring the condensate level. The electronic capacitive sensor probe placed inside the drain reservoir controls the discharge by initiating the discharge command to a built-in indirect operated solenoid valve. When the condensate reaches the probe, the solenoid valve is actuated and opens. This drains the condensate and as its level drops, the probe senses this and closes the valve again. This cycle is repeated as the condensate level increases and decreases in the reservoir.
This valve avoids the loss of compressed air as the valve closes before all of the condensates is discharged. Electronic sensor drains have few moving parts, which ensures a reliable operation.
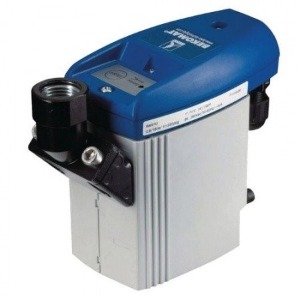
Figure 3: Electronic condensate drain with a capacitive level sensor
Float operated condensate drains
These valves have a simple construction and operate using a float type system. As a certain amount of condensate accumulates, the float automatically operates the condensate draining process by opening and closing the valve.
The float is the main component of the valve. While the collected condensate flows into the drain housing or filter bowl, the float rises. When the condensate rises to a certain level, the drain valve opens and discharges the condensate. These drains operate only when a sufficient quantity of condensate is present. Usually, a manual override is provided which allows for drainage of the system on demand or during cleaning. Most float-operated drain valves leave a small amount of condensate in the reservoir when discharging, which prevents the loss of valuable compressed air.
In most of these drain valves, the float directly operates the discharge valve through a lever mechanism. The disadvantage is that the lever mechanisms force to the valve seal is relatively low, which results in lower reliability. Some drain valves solve this problem by using permanent magnets. In these drain valves, the float mechanism is not directly connected to the valve. Instead, the float mechanism moves a permanent magnet. The valve is closed by a ferromagnetic plunger, which rests on the valve seat, just like in a direct operated solenoid valve. When the condensate level rises, the magnet moves towards the plunger, attracting the plunger towards it to open the valve. As the condensate level drops, the magnet moves away, and the valve closes again. This mechanism provides a more reliable and robust sealing than a traditional float operated drain valve. Float operated drain valves are an excellent choice when no electricity is available.
Selection criteria
The general criteria that influence the selection of the right condensate drain valves are:
- Operating pressure: The valve should be able to operate within the pressure range of the application. The drainage system may not work properly if the pressure required is under or over the valve capacity.
- Temperature: The valve should be able to support the maximum and minimum temperature range of the application.
- Operating environment: It is necessary to understand the ambient condition of the operating environment. The valves type and capacity will depend on the amount and type of condensate (water, water+oil, water+oil+contaminants, etc.) that may generate. The valve must also be able to handle the seasonal fluctuation in humidity.
- Sizing: The size of connection ports and drain line should be compatible with each other to ensure proper drainage.
To learn how to install a condensate drain, and which factors play a role in the installation, read our condensate installation article.
Applications
The condensate drain valves are mostly used in the following applications:
- Used with HVAC systems for residential and industrial purposes. These valves help in draining the condensate accumulated in the air conditioner through the drain line and to the outdoors.
- Used as condensate drain valve for air compressors
- Used with reservoir tanks, air dryers, etc.
FAQs
Where does the condensate line drain?
The drain line should be located at the lowest point of the compressed air system for the condensate to be drained.
How do you clean a clogged condensate drain?
Turn off power, locate the drain, and unclog it with a brush/vacuum or cleaning solution like vinegar. Flush with water to confirm it's clear.
Why does a condensate drain need a trap?
The condensate valve has traps to block the flow of air to allow for the proper condensate drainage.
What happens if condensate line is clogged?
The water stays in the drain line, which can leak or overflow from the drain pan and cause damage to the facility causing molds or water damage. This water in contact with electrical equipment can lead to a fire hazard.