Angular Contact Bearing Guide
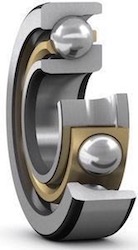
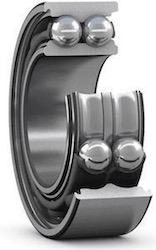
Figure 1: Single angular ball bearing (left) and double angular ball bearing (right)
Angular contact bearings have inner and outer raceways that are slightly offset, resulting in the balls mounting at an angle, making them suitable for radial and axial loads. The angular contact ball bearing advantage is that the axial load-carrying capacity increases as the contact angle increases. This article covers the design and operation of these bearings, their different types, and their applications.
Table of contents
View our online selection of angular contact bearings!
What is an angular contact ball bearing?
Angular contact ball bearing components
As seen in Figure 2, an angular contact ball bearing has the following components:
- Outer and inner rings (A & B): The inner ring fits over the shaft that the bearing connects to. The outer ring is the bearing's exterior. It contains and protects the bearing's components.
- Raceways (C): Angular contact bearings have inner and outer raceways. The outer raceway is asymmetrical to form the inclined contact angle.
- Balls (E): The rolling elements are spherical. They move along the raceways to reduce friction in the bearing.
- Cage (D): The cage is a separator in the raceway to keep the balls evenly spaced.
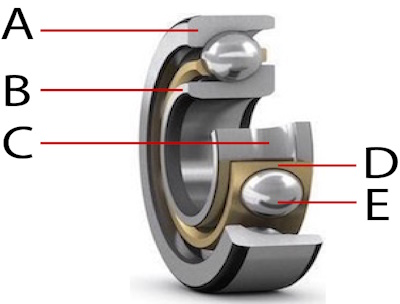
Figure 2: An angular contact bearing's key components: outer ring (A), inner ring (B), raceway (C), cage (D), and ball (E).
How angular contact bearings work
An angular contact bearing has an inner and outer raceway and spherical rolling elements rolling between the raceways. As seen in Figure 2, the raceways tilt towards the axial direction, so the contact angle between the balls and the raceways is inclined. This allows angular contact bearings to handle axial and radial loads at the same time.
Typical angular contact bearings are constructed to have a 15° to 25° contact angle between the raceway and rolling elements. The higher the contact angle, the higher the axial load the bearing can support.
Angular contact bearings can only support axial loads in one direction. Therefore, it's common practice to use a pair of these bearings mounted next to each other with the raceways tilting in opposite directions. An alternative is to use a double-direction angular contact valve, which is essentially two bearings joined together.
Radial load vs axial load support
Angular contact bearings are designed to handle combined radial and axial loads. Radial loads are perpendicular to the shaft and axial loads are parallel to the shaft. Read our complete rolling bearing guide to learn more about load types.
Applications
Because they can bear heavy loads, angular contact bearings are used for heavy machinery and agricultural equipment. These bearings help run pumps, electric motors, gearboxes, steel mills, windmills, conveyors, and other high-speed applications.
Types of angular contact bearings
Single-direction angular contact ball bearings
The sections above have primarily dealt with single-direction angular contact ball bearings. To summarize and add to that discussion:
- Contact angle vs load capacity: The higher the contact angle, the higher the axial load the bearing can handle. Conversely, higher contact angles lead to lower radial load capacity.
- Contact angle vs speed: While increasing the contact angle increases the axial load that the bearing can handle, it also reduces the max speed that the bearing can operate at.
- Load direction: Single-direction angular contact ball bearings can only handle axial loads in a single direction.
- Cost: Less expensive than a double-direction angular contact ball bearing.
Single-row angular contact ball bearing mounting positions
The single-row bearing must be preloaded in the direction of the contact angle, as it can only handle axial loads in that direction. Two single-row bearings can be fitted in back-to-back, face-to-face, or tandem arrangements:
- Back-to-back: Back-to-back mounted angular ball bearings (Figure 3 labeled A), the most common mountain method, can accommodate both radial and axial loads in any direction. The distance between the bearing center and the loading point (Figure 3 labeled D) is larger than other mounting methods. Therefore, the back-to-back mounting style can handle large momentary and alternating radial load forces.
- Face-to-face: Face-to-face mounted angular ball bearings (Figure 3 labeled B) can handle radial and axial loads in either direction. Due to the smaller distance between the bearing center and loading point, momentary and alternating radial force capacity is lower. Face-to-face arrangements can handle more misalignment than back-to-back arrangements.
- Tandem: A tandem mount (Figure 3 labeled C) can accommodate single-direction axial loads and radial loads. Because both bearings receive the loads on the axis, they can handle heavy axial loads.
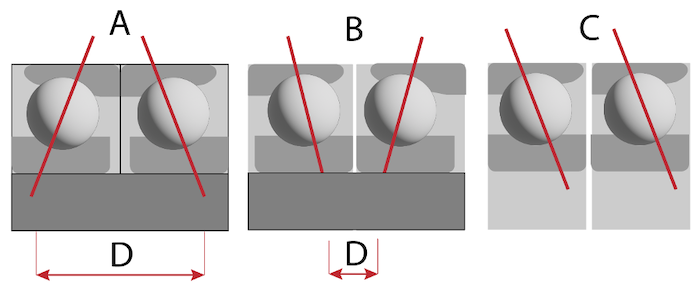
Figure 3: Single-row angular contact bearing mounting methods: back-to-back (A), face-to-face (B), tandem (C), and the distance between the bearing center and loading point (D).
Double-row angular contact ball bearings
The double-row angular contact ball bearing (Figure 4) is similar to two single-row bearings arranged back-to-back. In addition to radial and axial loads, they can absorb tilting moments. The advantages of double-row contact bearings include:
- Long-term cost: While typically more expensive than single-row bearings, double-row bearings can be more economical in the long run.
- Axial space: These bearings take up less axial space, which is useful when there is not enough space for two single-row bearings.
- Load accommodation: These bearings accommodate radial and axial loads, as well as tilting moments.
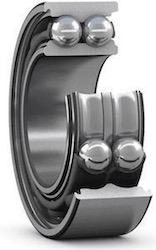
Figure 4: Double-row angular contact ball bearing
Four-point contact ball bearings
A 4-point contact ball bearing is similar to a single-row angular ball bearing. It consists of an outer race that is flanked on both sides. The inner race is also flanked on both sides with a split in the middle and steel balls circled by a cage. The flanks, or flanges, are symmetrical, unlike single and double angular contact bearings.
There are several advantages of four-point contact ball bearings:
- The split inner raceways of four-point contact ball bearings allow for easy mounting and dismounting of the bearing for maintenance.
- The recess in the inner raceway allows for better oil flow.
- These bearings work in a similar fashion to double-row or two single-row mounted angular contact bearings but take up less space.
- Allows for loads in both axial and radial directions.
- High load-carrying capacity due to a relatively higher number of balls than other ball bearings.
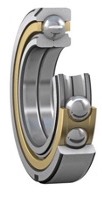
Figure 5: Four-point contact ball bearing
Selection criteria
Angular contact bearings are chosen when both radial and axial loads need to be supported. Consider the following when selecting angular contact bearings:
- Shaft diameter: The diameter of the shaft will determine the necessary inner diameter of the bearing.
- Bearing outer diameter: Determine if the bearing's outer diameter is suitable for the space where the bearing will be installed.
-
Seal type: Should the bearing be open, shielded, or sealed?
- Open: Open bearings have no protection against the environment, but they also have the lowest coefficient of friction. These are best for clean environments.
- Shielded: Shielded bearings have some protection against contaminants in the environment but have lower max speed requirements than open bearings.
- Sealed: Sealed angular contact bearings have complete protection against the environment but have the lowest max speed. Also, they are difficult to maintain, meaning a user is likely to replace a sealed bearing rather than try to repair it.
-
Direction: Angular contact bearings can be single- or double-direction depending on the application's load requirements.
- Refer to the single-row angular contact ball-bearing mounting positions section above to determine if mounting two single-direction bearings side-by-side is the best option for a given application.
FAQs
In which direction do angular contact bearings provide load capacity?
Single-row and tandem ball bearings provide one-directional thrust for axial loads. The contact angle guides the direction, which also determines the gradient of the combined load.
Do angular contact bearings need preload?
To remove excess play during bearing installation, users sustain a load pressure called preloading. Angular contact bearings require preload because they have to work in the pre-defined direction for axial loads.