ATEX FAQ
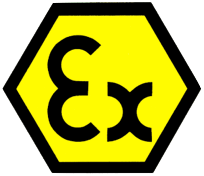
Figure 1: ATEX symbol
ATEX certification guarantees that equipment and protective systems designed for use in potentially explosive environments comply with crucial health and safety standards. It safeguards workers and protects property in explosive atmospheres. This article offers a thorough collection of frequently asked questions and their answers regarding ATEX.
Table of contents
- What does ATEX stand for?
- Why should products and systems have ATEX certification?
- Where is ATEX applicable?
- What is an explosive atmosphere, and why is it dangerous?
- What is an ATEX zone?
- How do ATEX classifications affect the selection of equipment?
- What are the specific ATEX compliance responsibilities for employers?
- What are the key components of an ATEX-compliant product label?
- Can I assemble two or more ATEX-certified products?
- Can I repair ATEX-certified products?
- What information, instructions, and training are required for employees?
- What is the difference between ATEX and IECEx certifications?
- What is an EPD?
What does ATEX stand for?
ATEX is an acronym derived from the French phrase 'Appareils destinés à être utilisés en ATmosphères EXplosives,' which translates to 'equipment intended for use in explosive atmospheres.'
Why should products and systems have ATEX certification?
ATEX certification is mandatory to ensure that equipment and protective systems are suitable for use in potentially explosive environments to safeguard the workplace. The certification process often involves an independent third-party organization that conducts testing. Some equipment can be self-certified by the manufacturer, which includes providing technical documentation and ensuring the equipment meets ATEX requirements. Certified equipment is marked with 'CE' to indicate compliance with European regulations and 'Ex' to signify that it meets the specific requirements of the ATEX directive. Read our article on ATEX directives for valves for more information on the importance of ATEX directives in valves and fittings.
Where is ATEX applicable?
ATEX regulations are crucial in environments with potential explosions due to ignitable dust, vapors, or gasses. This encompasses workplaces that handle or store flammable or explosive substances such as petrol, liquefied petroleum gas (LPG), paints, varnishes, and solvents. Examples of industrial settings include the ones that utilize flammable materials or produce combustible dust clouds, such as those in chemical processing plants, paint spray operations, flour mills, and milk powder drying facilities. Additionally, certain types of dust that have the potential to form an explosive mixture with air, such as those generated from milling and sanding operations, are also considered flammable substances.
What is an explosive atmosphere, and why is it dangerous?
An explosive atmosphere refers to a mixture of air and flammable substances in the form of gasses, mists, dust, or vapors that have the potential to ignite and cause a fire or explosion. While an explosive atmosphere does not necessarily lead to an explosion, if ignition occurs, the flames can propagate rapidly through the mixture.
In confined spaces, such as within plants or equipment, the fast spread of flames or the sudden increase in pressure due to the heat of combustion can result in an explosion. This is because the confined space restricts the expansion of the gasses produced by combustion, leading to a rapid buildup of pressure that can have destructive effects.
What is an ATEX zone?
An ATEX zone is a specific area within a workplace that, under the ATEX directive, must be classified according to the likelihood and duration of an explosive atmosphere. The classification helps determine the necessary precautions for safety and the type of equipment that can be used within that area. For gasses, vapors, and mists, the zones are defined as follows:
- Zone 0: Zone 0 applies to places where an explosive atmosphere consisting of a mixture of dangerous substances in the form of gas, vapor, or mist is present continuously or for long periods.
- Zone 1: Zone 1 is for areas where an explosive atmosphere is likely to occur occasionally during normal operation.
- Zone 2: Zone 2 is for areas where an explosive atmosphere is not likely to occur in normal operation and, if it does occur, will only be present for a short period.
For dust and fibers, the zones are similarly classified:
- Zone 20: Zone 20 contains a cloud of combustible dust in the air that is present frequently or for extended periods.
- Zone 21: Zone 21 contains a cloud of combustible dust in the air that may occur occasionally during normal operation.
- Zone 22: Zone 22 contains a cloud of combustible dust in the air that is not likely to occur in normal operation but, if it does occur, will only be present for a short period.
How do ATEX classifications affect the selection of equipment?
ATEX classifications directly impact the selection of equipment used in hazardous areas. Equipment and protective systems intended for use in explosive atmospheres must be designed and constructed to prevent the ignition of the explosive atmosphere. They are categorized into different groups and categories based on the zone they are designed for and the level of protection they offer.
- Group I equipment is intended for use in underground parts of mines, and those parts of surface installations of such mines are liable to be endangered by firedamp and/or combustible dust.
- Group II equipment is intended for use in other places endangered by explosive atmospheres.
Within these groups, equipment is further categorized into categories (M1/M2 for mines and 1/2/3 for other industries) based on the level of safety they provide.
- Category 1 equipment offers the highest level of protection and is suitable for use in Zone 0 (gas/vapor) or Zone 20 (dust) environments, where an explosive atmosphere is present continuously or for long periods.
- Category 2 equipment is suitable for Zone 1 or Zone 21, and Category 3 equipment is designed for Zone 2 or Zone 22, where an explosive atmosphere is less likely to occur.
What are the specific ATEX compliance responsibilities for employers?
Under the ATEX Directive, employers have several duties to manage and mitigate the risks associated with fire and explosions in workplaces where flammable substances are present. These duties include:
- Risk assessment: Identify ignition sources and evaluate the risk of explosive atmospheres.
- Explosion protection document: Record risks and preventive measures in a formal document (discussed later in EPD section).
- Safety measures: Implement technical or organizational measures to minimize explosion risks.
- Training: Train workers on risks, safe practices, and emergency procedures.
- Area classification: Classify and mark areas where explosive atmospheres may occur.
- Equipment selection: Use CE-marked equipment suitable for the classified zones' risk levels.
What are the key components of an ATEX-compliant product label?
An ATEX-compliant product label provides essential information about the equipment's suitability in hazardous areas. Figure 2 shows the main components of an ATEX label:
- The CE marking (A) indicates that the product conforms to all applicable EU directives, including ATEX.
- The identification number of the notified body (B)
- The Ex symbol (C) signifies that the product is designed for explosive atmospheres.
- Equipment group (D)
- Equipment category (E)
- The gas and/or dust group (F) shows the nature of the hazardous substance the equipment is designed to work with (e.g., G for gas, D for dust).
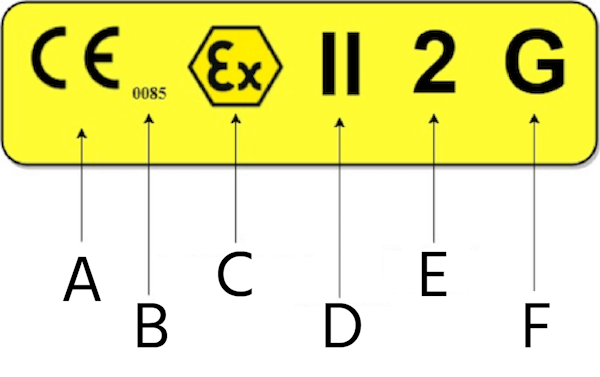
Figure 2: ATEX label: CE mark (A), notified body identification number (B), Ex symbol signifying the product's application in explosive atmosphere(C), equipment group (D), equipment category (E), and gas (G)
Can I assemble two or more ATEX-certified products?
Yes, as long as each product involved in the assembly is ATEX-certified. This can be the case for assembling a solenoid valve and a coil, a pneumatic valve and a CNOMO interface solenoid valve. It is important to check the continuity of the earthing. Earthing is necessary for all equipment in an assembly.
Can I repair ATEX-certified products?
Repairs on ATEX-certified products can be done by replacing old or broken parts with new ones that match or are very similar, without altering the product's function. This process doesn't require additional safety assessments. Spare parts for ATEX products can be purchased and maintenance can be performed according to the provided instructions. Individuals conducting repairs on ATEX products must be knowledgeable about explosion risks and have appropriate training.
It's important to ensure that the manufacturer's safety labels are still accurate after repairs. A label indicating that the product has been repaired should also be added.
What information, instructions, and training are required for employees?
The Safety, Health & Welfare at Work Act 2005 and the Safety, Health & Welfare at Work (General Application) Regulations 2007 mandate that employees must receive comprehensive information, guidance, and training regarding the hazards that exist in their workplace, as well as the measures that have been put in place for prevention and protection. Also, workers must be trained on the necessary precautions and procedures to protect themselves and their colleagues from the risk of explosions.
What is the difference between ATEX and IECEx certifications?
IECEx is the International Electrotechnical Commission's system for certifying equipment according to standards for use in explosive atmospheres, focusing on facilitating international trade. Unlike ATEX, which is specific to the European Union, IECEx certification is recognized globally. The main differences between ATEX and IECEx are:
- Jurisdiction: IECEx is international, while ATEX is specific to the EU, although it is often voluntarily adopted by companies outside the EU.
- Standards: ATEX requires compliance with its essential health and safety requirements (EHSRs), while IECEx strictly adheres to International Electrotechnical Commission (IEC) standards.
- Certification bodies: ATEX certifications are issued by notified bodies within the EU, known as ExNBs, which provide EU Type Examination Certifications. IECEx operates through a single international process managed by the IECEx Management Committee, with IECEx certification bodies and labs issuing Certificates of Conformity recognized worldwide.
What is an EPD?
An explosion protection document (EPD) is a safety document outlining the risk assessment results for work activities in flammable or explosive atmospheres. It outlines the minimum requirements for improving the health and safety protection of workers potentially at risk from explosive atmospheres.
The purpose of an EPD is to formalize the assessment of risks associated with explosive atmospheres and to document the measures in place to ensure workplace safety. The document should include key elements:
- Zone identification: Define areas where explosive atmospheres may occur
- Risk assessment: Evaluate the likelihood and impact of potential explosions
- Control measures: Document measures to prevent and mitigate explosive atmospheres
- Equipment listing: List compliant equipment used in explosive zones
- Safety coordination: Describe coordination among employers for safety
- Emergency procedures: Outline actions and evacuation plans for explosion incidents
- Training: Specify worker training on risks and safety precautions
- Maintenance schedules: Include regular maintenance and inspection plans