Bearing Failure Symptoms
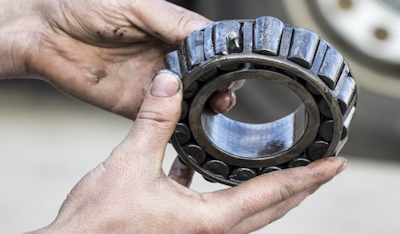
Figure 1: Premature failure of a roller bearing
Bearing failure is a serious issue because spinning components in a machine can come grinding to a halt, leading to significant damage. Fortunately, several common symptoms allow the detection of a bearing failure before it is too late. The first sign of bearing failure is excessive vibration. Following this, the bearing will begin to heat up past acceptable levels and produce excessive noises, either high-pitched or grinding. This article overviews these symptoms, discusses how to analyze them, and provides a few common examples of bearing failure.
Signs of bearing failure
There are five main bearing failure symptoms:
- Temperature: During operation, the bearing's temperature rises above acceptable levels.
- Vibration: Excessive vibration occurs during operation.
- Lubrication: There is an improper bearing lubrication, meaning there needs to be more lubrication, there is too much lubrication, or the wrong lubrication has been used.
- Contamination: The lubricant has become contaminated with foreign particles or substances.
- Noise: There is excessive noise during operation, typically a high-pitched squealing or grinding sound.
Temperature
Bearings heat up during operation. An acceptable bearing temperature for many bearings is 82 °C (180 °F) or lower (please look at the bearing manual for product specific temperature ratings). Because a bearing reduces frictional forces between rotating machine parts, a failing or failed bearing leads to more friction and higher operating temperatures. Therefore, regular temperature testing using temperature sensors, such as an infrared temperature sensor, is necessary. If an abnormal high temperature is detected, it is a sign to replace the bearing before it fails.
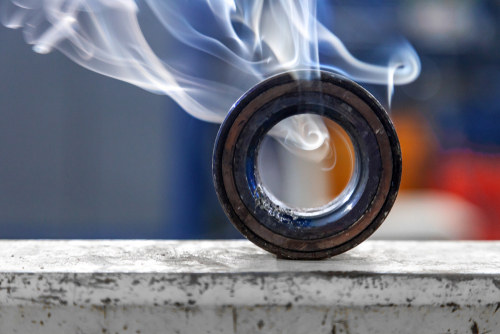
Figure 2: A failed bearing will quickly heat up due to significant friction force increases.
Vibration
Excessive vibration from a failed bearing can be due to a number of reasons. For example, abrasion can damage the raceway causing the rolling elements to bounce around. Slight differences between individual rolling elements caused by machining errors during bearing manufacturing can also cause vibration. There are various tools and methods designed for testing bearing vibration. If you notice abnormal vibration that has increased over time, it is typically a good indicator that the bearing should be replaced. For more information regarding bearing vibration, please read the ISO 15242 standard to learn more.
Lubrication
The most common reason for bearing failure is due to lack of lubrication. Bearings require precise lubrication to operate correctly. The bearing can fail from the following:
- Not enough lubrication can increase friction, leading to excessive wear and heat.
- Too much lubrication can result in an increase in pressure, leading to a seal failure, lubrication leak, and excessive heat generation.
- Wrong type of lubricant can increase friction, leading to excessive wear and heat.
- Contaminated lubricant can increase friction, leading to excessive wear and heat.
Always check the bearing's manufacturer's instructions before conducting any lubrication-related maintenance. Portable grease analysis kits are available to test the lubrication even in remote locations.
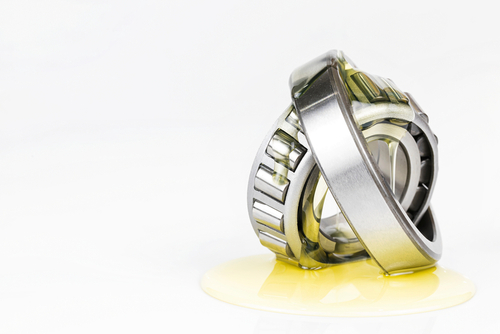
Figure 3: Improper bearing lubrication can lead to bearing failure.
Contamination
Bearing contamination can occur in several ways. One of the most common ways is during relubrication maintenance. Poor seals can allow foreign contaminants to mix with the lubricant. Also, high-pressure washing a bearing can emulsify the lubricant. Ultimately, contaminants lead to abrasion, greatly reducing the bearing's lifetime. If any contaminants are seen while inspecting the bearing, it should be replaced.
Noise
Failing bearings can make unusual noises, such as high-pitched squealing or grinding noises. The best method for using noise to indicate bearing failure is subjective. It's necessary to pay attention to the noises of a properly functioning bearing to know when something sounds wrong.
Ball bearing cage failure
Many ball bearing designs use a cage surrounding the individual rolling elements to keep them aligned. Cage damage leads to cage failure and will quickly lead to overall bearing failure. Ball bearing cage failure typically occurs in four stages:
- Stage 1: There is no noticeable rise in temperature or sound, but the bearing vibrates slightly more than usual. There is little need for concern at this stage.
- Stage 2: Temperature remains normal, but the bearing's sounds during operation rise slightly. Vibrations continue to increase in amplitude.
- Stage 3: The temperature has risen somewhat, and excessive noises are easily heard by ear. At this point, the vibrations increase significantly. Replacing the bearing should occur before going beyond stage 3.
- Stage 4: Temperature and noises increase significantly, and vibrations are severe. At this point, damage to the system is possible.
Bearing failure examples
- AC compressors: AC compressors are an important component of a vehicle's cooling systems. AC compressor bearing failure symptoms are fans blowing hot air only or loud noises when the AC operates. AC compressors typically have double-row angular contact ball bearings or high-load cylindrical bearings.
- Washing machine drum: Washing machine drum bearings are typically ball bearings. Drum bearing failure in washing machines can be identified by grinding noises when the drum spins or the drum excessively moving up and down.
- Centrifugal pump: Centrifugal pumps use a variety of bearings depending on specific design. Bearing failure in a centrifugal pump can often be detected by a loud grinding noise or excessive vibration during operation.
FAQs
What are the first signs of bearing failure?
The first sign of bearing failure is excessive vibration. Following this, the bearing will begin to heat up past acceptable levels and produce excessive noises, either high-pitched or grinding.
What happens when bearings fail?
Bearings lower frictional forces caused by spinning components in machines. Bearing failure quickly increases frictional forces, leading to significant temperature increase and extreme wear and tear.