A Complete Ball Bearing Guide
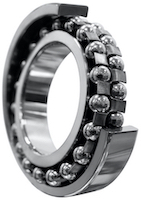
Figure 1: Self-aligning ball bearing
A ball bearing is a circular joint that connects a rotating part to another, usually stationary, part of a machine. It allows the rotating part to provide or receive structural support while significantly reducing the amount of friction caused by the rotation. Figure 1 shows an example of a self-aligning ball bearing.
The most common ball bearing application consists of a rotating shaft that needs support. The shaft fits snugly inside the inner circle, called a race. When pressure is exerted perpendicularly to the length of the shaft, such as the weight of a car pressing down on the car's central axle, the bearing provides support for this weight making it a radial bearing. If the pressure is exerted through the length of the shaft the bearing is an axial bearing.
Table of contents
- Ball bearing components
- Ball bearing types
- Ball bearing replacement
- Ball bearing selection criteria
- Ball bearing uses
- FAQs
View our online selection of ball bearings!
Ball bearing components
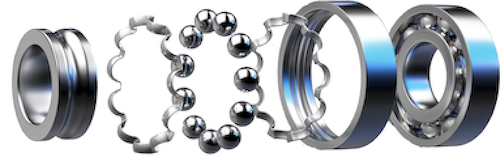
Figure 2: Exploded view of ball bearing
Ball bearings consist of two grooved, circular tracks carved into short, hollow cylinders, called raceways, which sandwich a set of balls, also referred to as the ball bearing rollers. As the inner race rotates, the balls between it and the outer race begin to roll, significantly reducing the friction between them.
These balls are sometimes spaced out from each other by a retainer, also called a cage, which is a series of circular harnesses that go around each ball and connect rigidly to the harness of the next ball, maintaining a fixed distance between them as they roll.
Because the smoothness of the tracks and the balls and their ability to roll freely is what allows the rotation to occur without much friction, debris mustn't be allowed onto the grooved track, where they could stop a ball from rolling or cause scratches or dents, causing the bearing to fail. For this reason, most ball bearings are built with seals or shields that close off the grooved space between the races from the rest of the machine environment. Figure 3 shows various shielded, sealed, and open bearings.
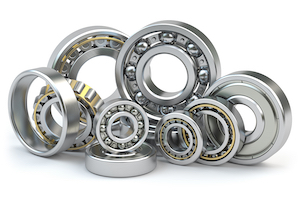
Figure 3: Shielded, sealed, and open bearings
Regardless of whether the bearing is sealed or open, it is typical for ball bearing lubricants, such as grease or oil, to be distributed across the balls and tracks to ensure that the balls rotate freely and allow a temporarily stuck ball to slide smoothly against the grooves.
The outer surfaces of the races may have additional structures, such as screw holes that allow them to attach to other parts of the machine. However, most bearings are secured by C-shaped rings, called snap rings, or are sized so precisely that they fit snugly into their housing and clench tightly to the shaft without the need for additional support.
Ball bearing types
Ball bearings are named according to features of their physical design. By understanding their designs, one can appreciate the logical relationship between the design, the name, and the load-bearing capacity of each of the following types of ball bearings.
Deep groove ball bearings
Deep groove ball bearings have grooves cut more deeply than some alternatives. As a result, the walls of these grooves surround more of each ball.
Because the balls are more fully surrounded, they have more wall-surface against which they can roll and transfer loads in more directions. For example, the pressure exerted through the length of the shaft from the left will be transferred to the left walls of the inner race, which will press on the balls, which will push against the right borders of the outer race, which will finally press against some rigid part of the larger machine. For this reason, a deep groove ball bearing is suitable for bearing axial loads from both the left and right directions, in addition to radial loads. Frequently, they carry both types simultaneously, in which case, we say they are operating as radial-axial bearings.
Angular contact ball bearings
Angular contact ball bearings feature asymmetrical grooves caused by one groove wall being longer than the other. Which division is more extended depends on the other race, with the critical thing being that the longer walls of each race oppose each other. For example, if the left wall of the outer race comes down farther, then the right wall of the inner race should come farther up, and vice versa, such as in Figure 4.
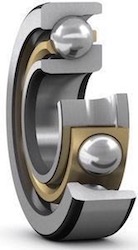
Figure 4: Single angular ball bearing
This allows the bearings to support axial pressure from the length of the shaft in the direction of long-wall opposition. Of course, the inner and outer races still cup the balls from the top and bottom, thereby ensuring that radial pressure is supported. As a result, angular contact ball bearings achieve a radial-axial load-bearing ability similar to deep groove ball bearings, but only in the direction of long-wall opposition.
When the bearings must support axial loads in both directions, a second angular contact bearing is sometimes flipped the other way and installed adjacent to the first one. This allows one bearing to provide long-wall opposition in two directions. However, this arrangement takes up the additional axle and clearance space. A double-row angular contact bearing is often preferred.
A double-row angular contact bearing consists of two rows of balls, separated by a long, inner wall that protrudes from the outer race. Each row of balls is held in place on the other side by a long wall extending from the inner race. Axial pressure from the shaft is exerted, through the balls, to the long inner wall of the outer race, attached to some larger structure of the machine.
As you can see in Figure 5, this design is effectively a system of two single-row angular contact bearings that have been structurally unified and consolidated.
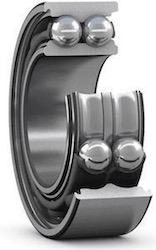
Figure 5: Double angular ball bearing
Thrust ball bearings
Unlike the previously discussed types, which all have inner and outer races, thrust ball bearings have left and right races, whose grooves sandwich the balls from the left and right directions. This makes them better than the others at supporting axial loads because the centers of the tracks, rather than just extra-long walls, hold the balls from those directions, as seen in Figure 6.
However, because the grooves do not extend to surround a significant enough portion of the tops and bottoms of the balls, heavy radial loads are not supportable, and these bearings are liable to collapse if such a force is exerted.

Figure 6: Thrust ball bearing
Single-row thrust bearings
A single-row thrust bearing has just one row of balls and is suitable for applications where axial loads occur in just one direction.
To support rotation, only one of the races attaches to the shaft, while the other has a larger bore diameter, allowing the shaft to pass through it with clearance. When the shaft rotates, the race to which it is attached also rotates, causing the balls to roll between it and the other race, fixed in place on the machine.
When the shaft is attached to the left race, axial pressure is exerted through the shaft and is supported by the balls and race to its right. But, if axial pressure is exerted from right to left, the left race will have no support from the bearing structure and will simply be pushed away from the rest of the bearing, which may break apart.
Double-row thrust bearings
Double-row thrust bearings consist of two rows of balls sandwiched between three races. In this design, the middle race attaches to the shaft, which passes with clearance through the larger bores of the outer races. As a result, axial pressure exerted in either direction is supported by the row of balls and outer race on the opposite side.
Spherical versus flat thrust bearings
The surface of the race that encounters the housing may be flat or spherical. When the surface is flat, it must lie flush against the housing, leaving no room for misalignment between the shaft, the bearing, and the housing. However, when the surface is spherical, it rests in the housing like a ball in a socket, making the shaft slightly misaligned relative to the housing during installation and operation.
Self-aligning ball bearings
Self-aligning ball bearings frequently feature two rows of balls instead of just one, which provides two rows of contact points against the grooves of the races. One of the races holds those rows separately through a dual groove, while the other has one extra-wide track that spans both rows, as shown in Figure 7.
If the angle between the length of shaft and the plane of the bearing shifts slightly away from a perfect right angle, one of the rows of balls will still line up with the center of the groove of the outer race. The alignment provides continuous and robust radial support until the shaft shifts back to its proper right angle.
Bearings with this design are often used when installation conditions make it challenging to achieve a perfect right angle between the shaft and the bearings in the first place. The self-aligning design will successfully support the radial loads with a near-right angle.
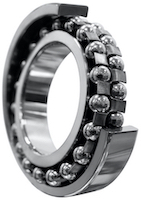
Figure 7: Self-aligning ball bearing
Y-bearings
Y-bearings are ball bearings with an extra-long inner race that extends like a short pipe out of both sides of the bearing. These extensions provide two screw holes to fasten set screws into corresponding screw holes on the shaft. If two sticks were poked through the bearing's screw holes until they touched, they would form a 120-degree angle and might be said to resemble the top of a "Y," which is why these bearings are called Y-bearings. This screw-hole design allows these bearings to be installed on shafts already in place. While this attachment method is convenient, its axial load-bearing capacity is limited.
Thin section bearings
Thin section bearings have particularly thin races, having narrower grooves and accommodating smaller ball sizes. The decreased width and ball size require less material, which reduces the overall weight and size of the bearings, which can result in lower operating costs. However, the smaller ball size makes for less contact area, so the overall load-bearing capacity is limited. Accordingly, thin section bearings are most suitable for precision instruments, where space is limited, and radial loads are not very heavy, such as medical equipment or astronomical machinery.
Ball bearing replacement
When a ball bearing has reached the service life predicted by the work hours formula or shows signs of material degradation, owners should inspect it. Some symptoms of bad ball bearings can be excessive noise or heat. If it is an open bearing, this is accomplished by first assessing the condition of the lubricant, then removing the balls from the races and cleaning the surfaces thoroughly. Finally, owners should carefully wash the surfaces and inspect them for wear or abnormalities. If it is a permanently shielded or sealed ball bearing, users should supply an initial torque and observe the bearing during free rotation. Depending on the outcome of the appropriate inspection, owners should replace the bearing.
Because a ball bearing is a structural joint, its removal often requires temporary support that will hold the parts of the machine that the ball bearing joins. For example, the wheel bearings of a car securely join the central axle to the wheels, holding the car's weight up off the driving surface. First, it is necessary to support the vehicle with a jack or similar support to replace wheel bearings.
Frequently, a secure housing encases the bearing and is attached to the larger machine. Therefore, removing any housing parts is necessary, preventing access to the bearing. In the case of a car, the wheel hub houses the wheel bearing, where a metal guard may cover it. Figure 8 shows a wheel bearing in its housing.
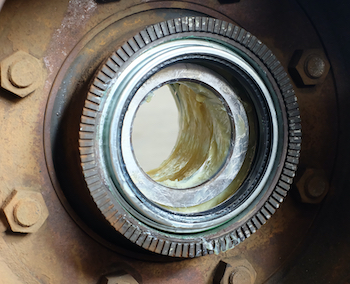
Figure 8: Wheel bearing
Once the bearing is accessible, it must be pressed or pried from its housing. Because it is designed to fit very snuggly, it is usually necessary to use a specialized tool, such as a bearing puller or press, to leverage the bearing against its housing. Alternatively, it may be possible to puncture the seal of the bearing and pry out the inner race, the balls, and then the outer race. Figure 9 shows an example of a bearing puller used in an automotive shop.
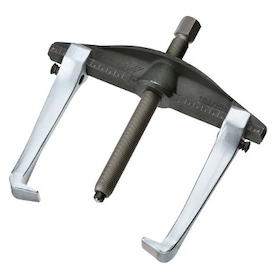
Figure 9: Bearing puller
Once the user has removed the old bearing, they should also clean the inner walls of the housing. They should inspect the entire structure for abrasions, warping, and other kinds of damage that might impair its ability to hold the new bearing securely.
After inspection, the new bearing should be evenly pressed into the housing until it is snug and entirely in place. Next, the owner should replace and secure any covers or housings they removed by sliding the inner race of the newly installed bearing onto a shaft.
If the bearing is not pre-lubricated, it should at this point be lubricated with the correct lubricant. The amount of ball bearing grease or oil to be applied should be carefully determined. Too little will allow excess friction, while too much may cause damaging heat levels to accumulate in the lubricant during operation. Once the appropriate amount of lubricant has been determined, the applicator should be applied to the contact point between the cages and the races.
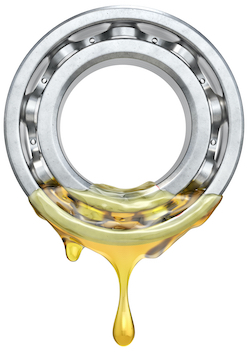
Figure 10: Bearing lubrication
After the bearing is lubricated, ensure that it is rotating correctly. When it is clear that the new bearing is rotating correctly, it is time to remove the temporary support and allow the bearing to bear the machine's load. Once again, users should test the operation of the bearing. After a successful operation is confirmed, the ball bearing has been successfully replaced. Read our mounting, installing, and removing guide for more information.
Ball bearing selection criteria
When selecting a ball bearing, one should first consult official references for the target machine. Checking official references will ensure that the bearing chosen falls within the specifications recommended by the engineers who designed the machine. If this literature is not available, you may find parts suppliers who guarantee the compatibility of their parts. If these options are not available, one should select a bearing according to the following criteria.
Load
The foremost considerations when selecting a bearing are the expected operating load directions and amounts. To determine these, a thorough understanding of the machine, its intended operation, and the relevant physics may be necessary.
If only radial loads are involved, then a standard, inner and outer race bearing may be used. If only axial, then a thrust bearing is likely the best choice. However, deep groove or angular contact bearings are likely necessary if radial-axial loads need to be supported.
When axial loads are involved, it is critical to specify whether they occur in just one or both directions. Single-row angular contact or thrust bearings may be appropriate for single-direction axial loads. But, for axial loads in both directions, double-row angular contact, double-row thrust bearings, or deep groove bearings should be used. Learn more about loads in our bearing overview.
Size
The diameter of its outer race generally specifies the size of a ball bearing, the diameter of its inner race, also called its bore size, and its width.
Outer diameter
The diameter of the outer race should ensure a press-fit into the housing or else to fall within clearance limitations.
Inner diameter
The correct bore size should allow the bearing to clench the shaft tightly through a shrink fit. This process involves carefully heating the bearing, pressing it onto the shaft, and cooling back to size.
Width
The width of the races should fit on the available axle space, between any snap ring grooves or shaft walls that may be present. When axial distance is limited, thin section bearings or proprietary designs may need to be considered.
The range of available ball bearing sizes includes one of the smallest ball bearings globally, with an outer diameter of fewer than 1.5 millimeters. It is so tiny that it can fit comfortably on a grain of rice. This bearing is intended for use in medical or dental equipment, such as a drill, where it might allow a bit to spin rapidly without wobbling as it bores precisely through a tooth or a bone. At the other end of the spectrum is a huge ball bearing with an outer diameter of over 6 feet and a dynamic load rating of over 280,000 lbs.
Shaft alignment
If installation conditions allow for a perfect right angle between the shaft and the plane of the bearing and the shaft is not subject to misalignment during operation, a standard ball bearing should be sufficient. However, a self-aligning bearing should be selected if installation conditions make it challenging to achieve perfect alignment or if the shaft is subject to temporary misalignment during operation. These include double-row self-aligning bearings and bearings with spherical housing washers, such as spherical thrust bearings.
Speed
The average speed at which the bearing will spin during operation is another critical factor that must be determined. This speed can be determined using sensor readings or calculations based on the dimensions of the machine and its production rate.
Material
All else being equal, the conditions in the operating environment and dynamic load capacity should determine the bearing material.
Operating environment
Factors such as debris, corrosive elements, operating temperatures, and the presence of electrical current should have a limiting effect on the material options considered. Users generally prefer ceramics bearings over steel ball bearings in extreme operating temperatures and highly corrosive or electrically-charged environments. Aerospace projects often use this material because of its durability. However, if debris is likely and chipping the ceramics is a concern, a hybrid composition of ceramic balls and steel races may be better.
Dynamic load capacity
The material of the bearing should be selected to ensure a dynamic load capacity that will allow the bearing to achieve a sufficient number of working hours. Stainless steel is the go-to material for heavier loads, requiring greater capacities. Ceramics or the hybrid combination of ceramic balls and steel races are also good options for lighter to mid-range loads.
Sealed versus open
Depending on the machine operating environment, the initial cost of the bearing, and accessibility, a sealed, shielded, or open bearing should be selected. Users should select a sealed or shielded version for environments with significant amounts of debris or bearings that are difficult to access. These provide robust resistance to contamination and lubricant leakage, requiring no maintenance for the life of the bearing.
For more oversized, more costly bearings, operating in environments that are relatively free from debris and that are easily accessible, an open variety may be preferred. Open bearings allow for lubricant to be reapplied on an as-needed basis. By carefully monitoring the condition of the bearing and lubricating it when necessary, these bearings may last significantly longer than their sealed counterparts, whose inaccessible lubricant will eventually degrade.
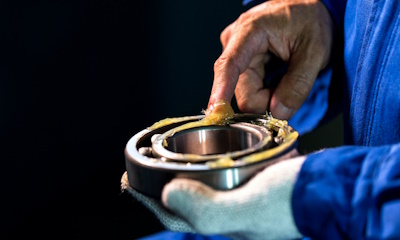
Figure 11: Silicone grease application on a bearing
Quality and cost
The manufacturer's reputation, the quality of the ball bearing, and budget allocations should also be factored into consideration when selecting a suitable bearing.
Ball bearing uses
In addition to examples encountered in the previous sections, there is a wide range of applications for ball bearings. Most devices with engines or other forms of rotation take advantage of the spatial efficiency of rotational motion to convert it into other forms of movement or energy by way of structures that require rolling bearings. Such applications include the following.
- Internal combustion engines: Support rotating output shaft
- Electric motors: Support rotating output shaft
- Gearboxes: Support rotating gear shafts and input and output shafts.
- Centrifugal pumps: Support the rotating shaft near engine output and fan input
- Agricultural equipment: Support the many rotating parts of tractors, plows, and other machines
- Construction: Support many rotating cranes, excavators, compactors, and other machines
There are many more applications. If you can think of a device that has a fast rotating part or a rotating part that supports a heavy load, there is a high probability that you will find at least some models that use ball bearings to facilitate that rotation.
FAQs
If the balls only contact each groove at a single point, how does it bear a heavy load?
When a load is put onto the bearing, the race presses the ball at a single point, causing it to flatten slightly. This flattened area bears the burden in a manner consistent with the laws of physics.
When was the ball bearing invented?
Phillip Vaughn invented the modern ball bearing in 1794. However, the first bearings were used in ancient times in the form of logs rolling underneath a load-bearing platform.
What materials are preferred for ball bearing construction?
The most common material is stainless steel. However, ceramics are preferred for extreme environments, and hybrid bearings, consisting of steel races and ceramic balls, are also widely used.
What types of lubricants are used in ball bearings?
Grease, oil, and synthetic oils are used primarily, though dry lubricants like graphite are also employed. Additionally, solid oil technology has recently emerged as a competitive alternative.
How long will a ball bearing last before it needs to be serviced or replaced?
While environmental factors can affect the service life, a properly selected bearing will provide working hours consistent with the work hours formula discussed in the Selection criteria.
Can you repair a ball bearing instead of replacing it with a new one?
If a ball bearing is not permanently sealed, it may be possible to repair it. However, whether or not you should do so depends on the cost. Larger, more costly bearings are good candidates for repairs.
What is the most recent development in the technology of ball bearings?
Sensors are now being used to monitor bearing operation, and the resulting data help anticipate when maintenance should be performed. Another development is that of superior lubricants.
What are the alternatives to a ball bearing?
Cylindrical, needle, tapered, and spherical bearings are common alternatives. There are also hydraulic and magnetic ball bearings, which use fluid dynamics and magnetism instead of rollers.