Butterfly Valve vs Ball Valve
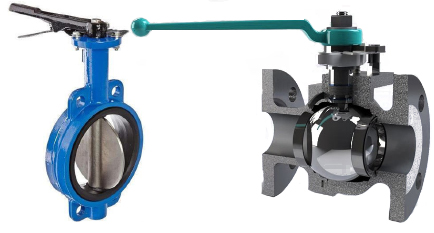
Figure 1: A butterfly valve (left) and a ball valve (right)
Choosing the correct valve for your application is an important task when designing a process system. A valve's properties and characteristics determine its suitability for a particular application. However, for some applications, multiple different valve types may work.
Both butterfly valves and ball valves offer unique benefits, so choosing between them in certain processes is not a hard choice. It can be problematic when a process requires valve characteristics that both valves have. This article delves into a deeper understanding of the butterfly valve vs ball valve in order to pick the correct valve.
Check out Tamesons selection of butterfly valves and ball valves!
What makes butterfly valves and ball valves comparable?
In terms of operation mechanisms, both valves are arguably the simplest of the valve types available. They are extensively used in domestic, commercial, and industrial applications for flow control of fluids across a wide range of temperatures and pressures. They are quarter-turn rotary valves (90° turn from fully closed to fully open). Both valve types can be controlled manually, with an electric actuator or with a pneumatic actuator. Butterfly and ball valves are relatively cheap, easy to maintain, reliable, and have a longer life expectancy than other valve types.
These similarities do not mean the valves are interchangeable in all process functions. Instead, it suggests and corroborates why we need to take a closer look at the valves' characteristics and for which applications to use each valve.
Understanding the butterfly valve
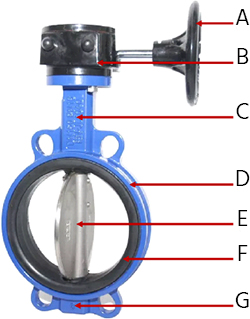
Figure 2: Components of a butterfly valve: handwheel (A), gearbox (B), stem (C), body (D), disc (E), seal (F), & packing (G)
A butterfly valve has a disc (Figure 2 labeled E) driven by a lever or handwheel (Figure 2 labeled A). When closed, the disc is perpendicular to the pipe flow direction. A seal (Figure 2 labeled F) which seats within the valve body (Figure 2 labeled D) ensures a tight closure with the valve disc. There is a near linear relationship between a butterfly valve's stem (Figure 2 labeled C) position and flow rate. The butterfly valve can be controlled manually, electrically, or pneumatically.
At larger diameters, butterfly valves are generally regarded as cheaper than ball valves. They have the least amount of parts and are relatively lightweight, requiring less support. The weight advantage of butterfly valves to ball valves can be significant at larger pipe diameters. There is a higher probability of leakage at high-pressure differences between the sides of a butterfly valve disc and the seal compared to a ball valve. Also, in applications with large pipe diameters, this high-pressure difference makes it difficult to open the valve, thereby requiring a bypass valve to balance both side’s pressure before the valve can be opened.
There is a pressure drop across the butterfly valve as the disc remains inside the flow even when fully open. This hinders using butterfly valves in process streams that need to be pigged, such as in the oil and gas industry. Butterfly valves are typically ON/OFF valves and are not suitable for precise fluid flow control.
Understanding the ball valve
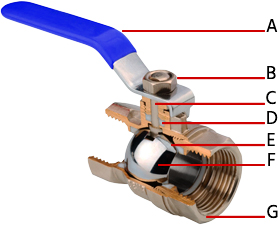
Figure 3: Components of a ball valve. Handle (A), Handle screw/bolt (B), Shaft (C), Packing (D), Seat (E), Ball (F), Body (G)
A ball valve has a hollow spherical ball (Figure 3 labeled F) that is pivoted at one or both ends. The top end of the ball is attached to a shaft (Figure 3 labeled C), which is rotated by a handle (Figure 3 labeled A) to change the valve position to open or close. When fully open, the hole in the ball lies parallel with the pipe flow direction. The ball rests on a seat (Figure 3 labeled E) inside the valve body (Figure 3 labeled G). The ball valve can be controlled manually, electrically, and pneumatically.
Ball valves can also have three-way or four-way flow directions in a T or L shaped bore. Learn more about a ball valve’s flow characteristics in our technical article on controlling fluid flow with ball valves.
The bore in a ball valve can vary from a size smaller than the pipe diameter (reduced port or reduced bore), a size equal to the pipe diameter (full port), or a V-port design. The design of the ball does affect flow characteristics. A ball valve can have a pressure drop across the valve in a reduced port ball valve or almost zero pressure drop in a full port ball valve, while a V-port design is ideal for stable flow control.
Unlike butterfly valves, ball valves have zero leakage when fully closed. The fluid pressure upstream of the valve pushes the ball against the seal, ensuring a positive shutoff position. Ball valves will easily open at a high-pressure difference on both sides of the valve and therefore do not require a pressure-balancing bypass.
Advantages and disadvantages
Though butterfly valves and ball valves share some similarities, they have distinct differences that may have an advantage over the other in specific applications. Below is a comparison showing the valve characteristics of each valve and their advantage against the other.
Table 1: Ball valve vs butterfly valve
Butterfly valve | Ball valve | |
Weight | Lighter weight even at larger pipe diameters | Very heavy at larger pipe diameter and may require support |
Installation space | Requires smaller installation space | Requires larger space than a butterfly valve |
Size | Suitable for larger pipe diameter (above DN 150), particular due to lightweight | Better suited for smaller pipe diameter (below DN 50) |
Leakage | Prone to leakages at a high-pressure difference | Provides tight seal even at a high-pressure difference |
Cost | Cheaper than a ball valve, particularly for larger sizes | More expensive compared to a butterfly valve |
Flow control | Suitable for ON/OFF control but can be used for proportional control. | Functions well for both ON/OFF and modulating control |
Flow restriction | Valve disc restricts flow creating a pressure drop. | Full port ball valves have no pressure drop. |
Connection style | It has a flange style with a lug or wafer design | A wide array of connection types with threads or flanges |
Selection criteria
The following criteria can be considered before selecting between a butterfly valve and a ball valve:
- Application: Butterfly valves are commonly used in water-based processes such as sewages, beer and soda production, etc. They are popular in chemical, agricultural, waste treatment plants, and food industries, partly because they are easy to clean. Ball valves can handle both liquid and gases with some solid particles (slurry). They are common in process plants, power plants, petroleum refining, oil, and gas exploration as they can be pigged for cleaning.
- Flow capacity: Butterfly valves can provide a larger flow capacity as they are readily available at a larger pipe diameter than a ball valve.
- Sealing: Ball valves provide a tight seal in process applications that require zero leakages when shutoff.
- Operating condition: Ball valves can operate up to 1,000 bar and 400 degrees celsius. Butterfly valves typically operate at a lower pressure (less than 50 bar) and temperature (less than 250 degree celsius).
- Flow regulation: Both valve types can be used for on/off control and proportional control, but ball valves are typically used for proportional due to better flow regulation.
- Ports: A butterfly valve can only have two ports, while a ball valve can have more than two ports.
Conclusion
A good understanding of the process requirements and the characteristics of the butterfly valve vs. ball valve helps select the correct valve. Multiple process requirements such as the operating pressure, the accuracy of control, and the type of fluid need to be considered and will define the valve that is best suited. In some applications, both valves may be sufficient, and the choice may be between the cost and maintainability of the valves. In other applications, the pipe diameter may be the only parameter that decides which valve can be used.