Difference Between Pressure Switch & Pressure Transmitter
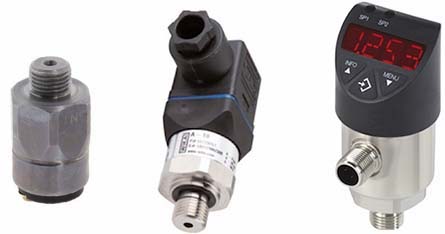
Figure 1: From left to right: a mechanical pressure switch, an analog pressure transducer, and a digital pressure transducer with an integrated pressure transmitter.
Pressure switches, sensors, transducers, and transmitters are widely used across various industries. However, these terms are frequently used interchangeably, leading to confusion when it comes to purchasing specific products. This article aims to clarify the distinctions and similarities between these devices.
Table of contents
- Pressure switch
- Sensor
- Pressure transducer
- Sensor vs transducer
- Pressure transmitter
- Transducer vs transmitter
- Example
- Interchangeability of terms
- Pressure switch vs pressure transmitter
- FAQs
View our online selection of pressure switches and transducers!
Pressure switch
A pressure switch is a mechanical or electronic device that opens or closes an electrical circuit when a certain pressure level is reached. A mechanical pressure switch is shown in Figure 1 (left). Read our pressure switches article for more details on the working, types, and applications of pressure switches.
Applications
Pressure switches are commonly used in:
- Compressed air systems: Pressure switches turn on/off the air compressor at a predesigned value.
- Process equipment: Fluid flow control equipment uses pressure switches to maintain a steady flow rate within the equipment.
- Pumping systems: Pressure switches maintain water levels in a reservoir by activating or deactivating the pumps when needed.
Sensor
A sensor is a device that detects a change in environmental parameters like heat, light, pressure, or moisture. The sensor’s output signal is generally converted to a human-readable display at the sensor location or transmitted electronically after being processed by a controller.
For example, in a mercury-based glass thermometer, the input is temperature. The liquid within the thermometer expands and contracts in response to changes in temperature, causing the level to be higher or lower in the gauge, which is human-readable. If a sensor doesn’t provide a meaningful output on its own, it must be part of a transducer to convert the output into a format that can easily be comprehended.

Figure 2: Sensor definition: physical changes (A), sensor (B), and output signal (C).
Pressure transducer
A transducer is a device that transforms energy from one form to another. A transducer changes a non-electrical signal's physical attributes into an easily measurable electrical signal. For example, a pressure transducer converts pressure applied by mechanical force into electrical energy. The output signal is linear and proportional to the applied pressure.
A transducer consists of a sensor and signal conditioning circuits. A signal conditioning circuit is an electronic circuit that converts the input signal to an equivalent electrical form and conditions it to be strong enough to be processed further. Hence, a transducer functions in two steps: first, by sensing the signal, and second, by conditioning and strengthening it for further processing. Table 1 shows a comparison between sensors and transducers.
For example, a microphone is a transducer that converts sound into electrical signals, amplifies it into the preferred range, and finally alters the electrical signals back into audio signals at the loudspeaker output. Pressure transducers are commonly used to monitor liquid levels in HVAC systems and vehicle brake pressure. Read our pressure transducers article for more details on a pressure transducer’s working, types, and selection criteria.
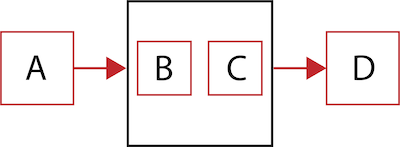
Figure 3: Transducer definition: input signal (A), sensor (B), signal conditioning (C), and output signal (D).
Sensor vs transducer
Table 1: Sensor vs transducer
Parameters | Sensor | Transducer |
Definition | Senses physical changes in the environment. | Senses a physical change and converts it into another form of energy (usually an electrical signal) |
Components | A sensor consists of only the sensing element and no other components. | A transducer consists of the sensor and signal conditioners. |
Complexity | A sensor is less complicated in its performance compared to a transducer. | A transducer transforms a physical quantity into a proportional output signal, making it more complicated. |
Feedback | A sensor measures a physical quantity only, and the unit cannot provide a feedback signal to the system on its own. | A transducer generally provides feedback to the desired system after processing the signal within the signal conditioning unit. |
Dependency | A sensor may not be a transducer. | A transducer always contains a sensor as one of its main components. |
Example | Thermometer, Accelerometer sensor, and proximity sensor. | Potentiometer and strain gauge. |
Pressure transmitter
Pressure transmitters measure a process’ pressure values and amplify them to an equivalent voltage or current. Transmitters are preferred when sending signals over hundreds of kilometers. Pressure transmitters are usually connected to pressure transducers. The transmitter is usually calibrated to generate an output current of 4-20 mA or a 1-5 V voltage, depending on the device type. Table 2 shows a comparison between a transducer and a transmitter.
Transducer vs transmitter
Table 2: Transducer vs transmitter
Parameter | Transducer | Transmitter |
Function | A transducer senses a physical change and converts it into another form of energy, usually an electrical signal. | A transmitter is usually connected to a transducer, and the device amplifies the transducer output to a level that can be transmitted over long distances without distortion. |
Power consumption | Lower operating power and power consumption requirements. | Transmitters consume more power during operation. |
Features | Transducers don’t have advanced options. A transducer’s status cannot be checked remotely. They are not equipped with displays to note the readings. | Transmitters have additional electronic circuitry that makes the output of a sensor or transducer more linear, compensates for noise, and amplifies the signal. Pressure transmitters with a digital display are examples of transmitters with a local display unit. A smart transmitter’s status can be checked remotely using the necessary software. |
Interference | Transducers are equipped with simple signal conditioning units; hence, a transducer’s output signal is more susceptible to interference. | Transmitter outputs are less susceptible to interference, and these signals can be transmitted over long distances without distortion. |
Example
Consider measuring process pressure in the range of 0-50 psi (0-3.4 bar) (Figure 4 labeled A). The pressure transducer (Figure 4 labeled B) performs the initial measurement and converts it into an electrical signal from 0-1.5 mV. The transmitter (Figure 4 labeled C) converts this signal to a standard signal of 1-3 V. For example, the transmitter may be calibrated to generate 1 V if the input pressure is 0 psi and 2 V if the input pressure is 25 psi. The signal from the transmitter is received by a PLC (programmable logic controller) module (Figure 4 labeled D) for further processing.
Note: The values mentioned in the example above are only for educational purposes, and they may not comply with the results of actual experiments.
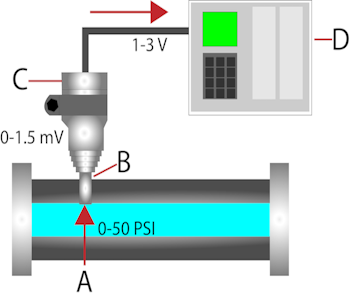
Figure 4: Pressure measurement example
Interchangeability of terms
A switch, sensor, transducer, and transmitter are functionally different components. But, these terms are defined differently across industries. Some companies define transducers as simple analog devices, while transmitters are more complex and output a digital signal. Other companies reserve the term transducer for devices with a voltage signal and transmitter for devices with a 4-20 mA signal. The term ‘pressure sensor’ is broader and can refer to a pressure transmitter/transducer. It can even refer to pressure switches, depending on the source.
Also, there are integrated modules comprising a transducer with a transmitter (and the overall unit may be called a transmitter), or a transducer with a pressure switch. Since these definitions are vague and often used differently across industries, they are often used interchangeably in engineering or industrial environments. Hence, it is always advisable to be specific with these terms to avoid confusion and minimize errors. Also, read the product description carefully before purchasing a transducer, sensor, or transmitter to ensure it meets the application requirements.
Pressure switch vs pressure transmitter
Pressure switches and pressure transducers seem pretty similar at first glance. However, they have very different design principles and are used for different purposes.
Pressure switches are used to operate an electrical circuit when a certain pressure level is exceeded. They directly control a fluid system and can operate without a power supply.
On the other hand, pressure transducers or transmitters emit a continuous signal that indicates the pressure level. They don’t directly control the circuit but provide a signal for a PLC or other control device. They are used for more sophisticated monitoring, predictive analysis, or process control applications. In general, pressure transducers are more expensive than pressure switches.
Table 3: Pressure switch vs transmitter
Feature | Pressure switch | Pressure transmitter |
Function | On/off control based on pressure threshold. | Continuous and precise pressure measurement. |
Output | Digital (typically a relay or contact closure). | Analog (usually 4-20 mA or 0-10 VDC). |
Measurement precision | Limited precision, typically within a setpoint range. | High precision, capable of precise pressure readings. |
Response time | Typically fast response time for switching. | Has a slower response due to signal processing. |
Pressure range | Limited to a specific setpoint range. | Covers a wide range of pressure values. |
Applications | Suitable for basic pressure control and monitoring. | Used for precise monitoring, data acquisition, and process control. |
Cost | Generally lower cost. | Typically higher cost due to precision and features. |
Integration | Easy to integrate into simple control systems. | Requires compatibility with data acquisition systems. |
FAQs
What is the difference between a sensor and a transducer?
A sensor is a device that detects a change in environmental parameters. A transducer consists of a sensor and a signal conditioning unit that converts the input parameter to an equivalent electrical output.
What is a pressure transmitter?
Pressure transmitters measure the process pressure values and amplify them to an equivalent voltage or current. Transmitters are preferred when sending signals over hundreds of kilometers.
When to use a pressure switch or transmitter?
Use a pressure switch when you need a simple on/off control based on a specific pressure threshold, and use a pressure transducer when you require continuous and precise pressure measurement or analog output.