Hose Installation Tips and Guidelines
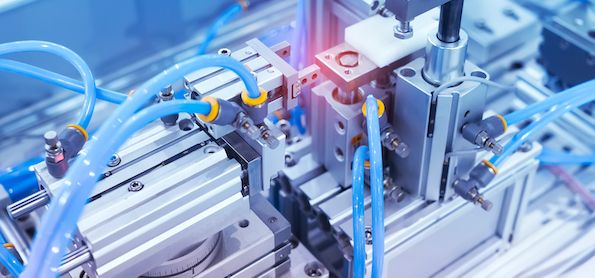
Figure 1: Pneumatic hoses
Hoses offer an easy and cost-effective media transfer solution for many different applications, including hydraulic and pneumatic use. However, proper installation, usage, and care will ensure that your hoses will last significantly longer. In this guide, we offer tips and guidelines for hose installation, some insight on hose maintenance, as well as proper care, storage, and handling procedures for your hoses.
Table of contents
View our online selection of Hoses!
Checkpoints before starting the installation of a hose
Before installing, it is important to verify the hose specifications for the application. The main things to consider are:
- Material selection:Hoses and tubes can be made of various materials, or multiple materials, enabling them to be utilized in many different industries. The chemical resistance of the hose material is among the most critical factors to consider. Make sure to choose the correct hose material for your application by following our hosing and tubing material guidelines.
- Pressure and temperature: Ensure that your hose can operate within an application's pressure and temperature ratings. It is essential to use pressure lines below the maximum operating pressure and ensure any pressure peaks are kept below the burst pressure rating. Considering that temperature will affect pressure (Charles' Law), the temperature rating should be below the median and environmental temperatures. This may lead to lower pressure ratings at elevated temperatures. Your material selection will determine the operating pressure and temperature.
- Length:To avoid unnecessary pressure drops, keep the length of any hose to a minimum. Nevertheless, it must be long enough to prevent tension and provide enough slack to compensate for changes in length caused by temperature, pressure, vibrations, or component movement. It is also important to consider the pressure drop through the hose. Longer hoses will result in a more significant pressure drop.
- Damage: Never use a hose that has any signs of wear. Slices, kinks, or crushed hoses can affect operational pressure rating and service life.
- Couplings and fittings: The types of couplings and fittings used on hoses depend on the application. For Hydraulic hoses, use fittings such as the SAE J514 fittings or other couplings and fittings that are intended for use in hydraulic applications. For pneumatic and gas hoses, there is a huge variety of different couplings and fittings that are suitable for different gaseous media, pressurized air, and much more. Read more about this in our pneumatic couplings guide.
Learn more about how to select a hose by reading our selection criteria for tubes and hoses guide.
Measuring and cutting hoses
While the hose length is not critical in general-purpose or water applications, the hose length is of vital importance when dealing with hydraulic and pneumatic applications. As mentioned above, a hose should be long enough to prevent tension and provide enough slack to compensate for changes in length caused by temperature, pressure, vibrations, or component movement. The following factors define the hose length:
Avoid twists and kinks in the hose
Movement should be restricted to minimize the resultant twisting. This means that the hose should only be able to bend sideways or up and down, not in all directions. Disproportionate bending will bring on stress fatigue in the hose. Rolling and storing hoses correctly will keep damage at a minimum.
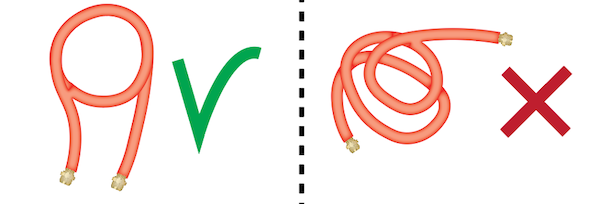
Figure 2: Avoid twisting and kinking of hoses.
Avoid sharp turns behind a coupling
Sharp bends following the couplings will reduce the service life of the hose significantly. There should be at least three to five times the diameter of the hose between the coupling and the bend. For example, a hose has a nominal diameter of 20 mm; there should be no bends behind the couplings within at least 60 to 100 mm behind the coupling. The easiest way to avoid bending behind the coupling is by using a coupling with bend protection.
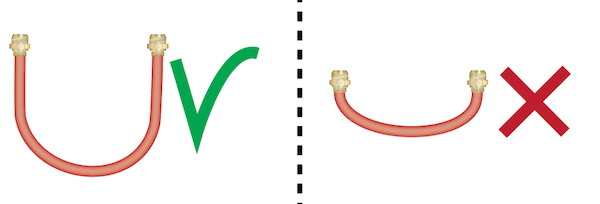
Figure 3: Avoid sharp turns behind a coupling
Avoid strong bends
A hose with major bends can kink and overstress the assembly and the hose could lead to damage and hose failure. Hose assemblies should be long enough and routed so that they do not exceed the minimum recommended bend radius. For tight corners use an elbow fitting. Read our fittings & couplings articles to see what options are available.
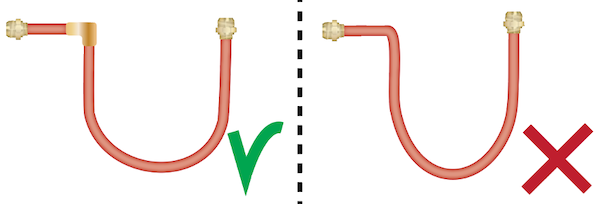
Figure 4: Avoid strong bends and consider installing elbow fittings.
Consider the coupling types
Male threaded ends are measured from the end of their threads. Female threaded and flanged couplings should be measured from the sealing surface area. Couplings with angled ends need to be measured from the center of the sealing surface.
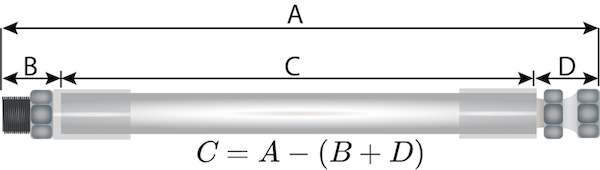
Figure 5: Calculating hose length: Entire assembly length (A), distance from the bottom of the collar to the end of the coupling (B), cut hose length (C), and distance from the bottom of the collar to the internal sealing surface
The process of calculating the hose length should consider the points mentioned above. After this, take the entire assembly length (A), subtract the distance from the bottom of the collar to the end of the coupling or internal sealing surface (B & D) which results in the cut hose length (C). Always allow for some slack in the hose for when it is pressurized, becomes hot, or cold. A good rule of thumb is to add 2-4% of the total calculated hose length. Too much slack will allow for sagging and unnecessary bending.
Avoiding damage to hoses
When installing a hose, it is essential to factor in the various points that can damage the hose and limit the service life. Below you will find the most common causes of damage and some easy solutions to prevent this from happening:
Overbending and bend radius
A bending radius is the minimum distance that a hose can be bent without causing any damage. The simplest solution to make sure that the hose does not exceed the bend radius is to use an elbow piece for large bends. The bend radius of various hoses can be found when purchasing the hose. To learn more, read our article on hydraulic hoses.
Kinking of the hose
Kinking of the hose, which will restrict the flow and increase pressure, can be prevented by using a hose saddle, a U-shaped device the hose is fitted over and which helps lift the hose and prevent kinking.
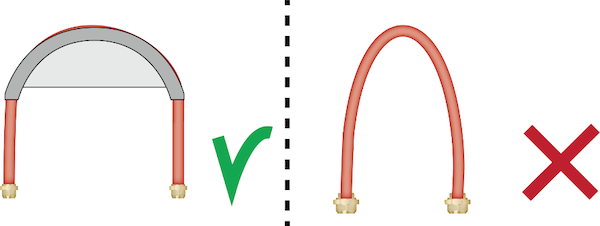
Figure 6: Consider installing a hose saddle to prevent kinking
Preventing torsion on a hose
Torsion, or twisting of the hose, can cause several issues, including complete failure due to stress fatigue in the hose. To prevent torsion from affecting your applications, ensure that the couplings, connections, and bending and flexing occur in one line. An easy way to identify twisting is by looking at the continuous printed line on the hose. If this line is not straight, and is twisted like a candy wrapper, the hose is twisted. This can cause premature failure of the hose.
Sagging of a hose
The sagging of a hose is a common problem when the assembly is installed in a horizontal loop. To prevent sagging, install supports that guide the hose and which prevents any sharp bends from occurring. This can be an adapter as seen in figure 7, or the use of a tool or hose balancer can also be an ideal solution. However, keep in mind that hoses do need some freedom of movement. Allow for slack in the hose so when it is pressurized, the movement of the hose does not cause it to become damaged.
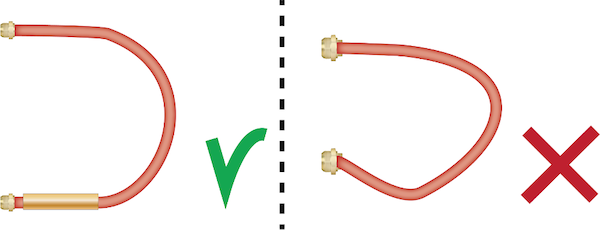
Figure 7: The use of an adapter or hose balancer can prevent sagging of a hose
Avoid abrasive Influences
The outer cover of the hose should not be installed too close to objects with sharp or abrasive surfaces, or too close to other hoses. Direct contact with equipment components, hoses, or material in the operating environment could cause abrasion, which could expose the reinforcement, leading to hose failure.
FAQs
How to identify a twisted hydraulic or pneumatic hose?
If you look at the printed lines on the hose, you will be able to identify twisting easily. If the line isn't straight, the hose is twisted. This can cause premature failure of the hose.
How much slack does a hose need?
When installing hoses, always allow for some slack for when the hose is pressurized, becomes hot, or cold. Typically, allow for 2-4% in addition to the calculated length of the hose.
How can I avoid a hose from bending?
Exceeding the bend radius of a hose can lead to dangerous situations. Install 45° elbow pieces, hose saddles, and adapters to keep a hose from over bending and introducing kinks in hoses.