Fluid Control Fittings - How They Work
Fittings are components used to connect sections of pipe, tube, or hose in a system. They ensure a secure and leak-proof connection between different parts of the system, allowing for the efficient flow of liquids or gases. They are common in water, pneumatic, and hydraulic systems and generally designed specifically for one of those application media types. There are various types of fittings, which can be classified based on application, size, threading, configuration, shape, material, threading type, connection type, etc. making certain fittings better suited for specific applications. Therefore, it is important to understand your application and media to select the best-suited fitting. A fitting can also be referred to as coupling, adapter, connector, or a union. At Tameson, we break down our fitting selection into three main categories:
- Hose and pipe connector: These fittings connect directly to a hose or pipe and connect it to another hose, pipe, or fluid component. They typically do not have threads on at least one of the ports.
- Threaded fitting: These fittings have a threaded connection on the port(s) to connect it to another threaded component, like a pipe or component.
- Coupling: These fittings typically exist of two parts that together form a connection and are typically designed to be periodically connected and de-connected by the user. Examples of couplings are garden hose quick connectors or pneumatic couplings.
View our online selection of fittings!
Table of contents
- Push-in fittings
- Push-on fittings
- Couplings
- Water fittings & couplings
- Pneumatic fittings & couplings
- Hydraulic fittings & couplings
- Other fitting articles
Push-in fittings
Push-in fittings, also known as push-to-connect fittings, are used to connect hoses to compressed air systems. They provide a leak-free, easy, and quick connection and they typically have 1 to 6 connection ports. They are installed and uninstalled by hand. To install, you push the hose into the release ring-end of the fitting until it hits the end. To uninstall, you push the release ring inward towards the fitting and pull the tubing out. It uses lock claws to keep the tubing in place, so a firmer tubing is desired to ensure a proper seal. For an in-depth overview of push-in fittings, please read our technical article dedicated to push-in fittings. View our online selection of push-in fittings.
Push-in fittings with 1 connection point
These fittings have one connection port, so they end the flow of the air. View our online selection of push-in fittings with 1 connection point.
Plug for push-in fittings
A plug is used to seal a pneumatic push-in fitting and is installed & uninstalled in the same manner. View our online selection of plug for push-in fitting.
Cap fittings
A cap fitting is used to terminate a pneumatic hose with a plug-in fitting. View our online selection of cap fitting.
Push-in fittings with 2 connection points
Two connection fittings have a single push-in type port and a single-threaded (male or female) or push-in type secondary port. The air flows from the inlet port to the outlet port. View our online selection of push-in fittings with 2 connection points.
Straight push-in male thread fittings
Straight fittings connect a hose in a straight line with a male threaded secondary port. View our online selection of straight push-in male thread fittings.
Straight push-in female thread fittings
Straight fittings connect a hose in a straight line with a female threaded secondary port. View our online selection of straight push-in female thread fittings.
Inner hex straight fittings
Inner hex straight fittings have a male threaded secondary port and an inner-hexagonal connection. Inner hex straight fittings have a male threaded secondary port to connect it to a valve and/or a component. The inner-hexagonal can be tightened after the threaded connection is made and a hex key can come in from the push-in fitting side to tighten the threads. View our online selection of inner hex straight fittings.
Elbow fittings
Elbow fittings connect hoses at 90 or 45-degrees to change the direction of airflow. They have a male or female threaded secondary port. Normal elbows have arms that are the same length, whereas long elbows will have one longer arm. View our online selection of elbow fittings.
Union straight fittings
Union straight fittings have a push-in type connection at each end to connect two hoses in a straight line. Unequal union straight fittings have different diameter ports to connect hoses of different sizes. View our online selection of union straight fittings.
Union elbow fittings
Union straight fittings have a push-in type connection at each end to connect two hoses in a straight line. Unequal union straight fittings have different diameter ports to connect hoses of different sizes. View our online selection of union elbow fittings.
Plug-in straight fittings
Plug-in straight fittings connect hoses in a straight line, whereby, one port uses a push-in type connection and the secondary port uses a stem or “plug-in type connection. Typically, the stem is inserted into an existing push-in fitting. View our online selection of plug-in straight fittings.
Plug-in elbow fittings
Plug-in elbow fittings connect hoses at 90-degrees using push-in and plug-in type connection ports. View our online selection of plug-in elbow fittings.
Push-in fittings with 3 connection points
Three connection fittings have two push-in type ports and one threaded or another push-in type port. The fitting can have either two inlets and one outlet to increase pressure, or one inlet and two outlets to decrease pressure and make two airflows. View our online selection of push-in fittings with 3 connection points.
Union Tee fittings
Union Tee fittings form a “T shaped junction to connect three equal diameter hoses using a push-in type connection at all ports. Unequal Union Tee fittings are also available to connect a smaller diameter hose to two larger diameter hoses. View our online selection of union Tee fittings.
Union Y fittings
Union Y fittings form a “Y shaped junction to connect three equal diameter hoses using a push-in type connection at all ports. Unequal Union Y fittings are also available to connect a smaller diameter hose to two larger diameter hoses. View our online selection of union Y fittings.
Push-in orifice fittings
These consist of a push-in fitting on one side and a threaded fitting with an orifice on the other side. The orifice reduces the size of the tube thus controlling the airflow to the desired rate. These fittings can be used to throttle, bleed and vent a pneumatic system. They are also known as flow control orifices, precision orifice valves, and flow restrictors.
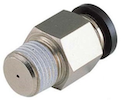
Push-in check valves
These valves ensure that the air goes freely only in one direction while preventing it in the opposite direction. The valve has a spring-loaded poppet pressed against the base of the orifice. When the air comes in on the poppet side, at a pressure higher than the valve’s cracking pressure, it compresses the spring, opening the orifice allowing air to move through. When it comes from the spring side it will press the poppet against the orifice’s base and block the passage. The symbol engraved into the valve’s body indicates the direction of the air flow. In this case, the air flows freely from the threaded port to the push-in fitting. Read our check valve article to learn more about this functionality. View our online selection of push-in check valves.
Push-in orifice check valves
These valves consist of an orifice fitting and a check valve combination. On one side they have a push-in fitting and on the other a threaded port with a check valve in it. The orientation of the check valve within it dictates which flow is metered. If the flow is metered entering a cylinder it is a meter-in valve and if it is metered exiting the valve it is a meter-out valve. Read our check valve article to learn more about this functionality.
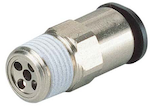
Needle valves with push-in fittings
These valves are used to shut off or control the airflow by changing the size of a valve’s orifice. The size of the orifice is regulated by adjusting the needle manually. When you screw the needle in, it reduces the volume of the airflow, unless you screw it in completely which would shut it off. The flow rate can be adjusted during the airflow. To secure the needle in the desired position tighten the locknut. These valves affect the airflow in both directions and are useful in low flow rate applications. Read our needle valve article to learn more about this functionality.
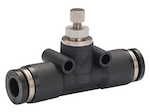
Push-in flow control valves
These valves are designed to control the flow rate in one direction and allow a free airflow in the opposite direction. They consist of a needle and an orifice check valve combination, which provides them with both of their functions. The needle valve provides the throttling function while the orifice check valve ensures that the flow is affected in only one direction. The orientation of the check valve within the flow controller dictates which flow is metered, which can be seen on the valve’s housing. If the flow is metered entering a cylinder it is a meter-in valve and if it is metered exiting the valve it is a meter-out valve. Read our needle valve article to learn more about this functionality. View our online selection of push-in flow control valves.
Push-in quick exhaust valves
These valves consist of an inlet, an outlet, and an exhaust port. The inlet and the outlet ports are connected to the pipeline. The valve’s diaphragm element allows the free flow from the inlet to the outlet port, but not in the opposite direction. When the medium returns to the outlet port it is immediately exhausted through the exhaust port thus providing faster piston movement for example. This quick exhaust function allows systems to free themselves from used compressed air without returning it to the solenoid valve. The exhaust port is usually equipped with a silencer, while some models have a needle in the exhaust port to regulate the airflow at the exhaust thus affecting the speed of an actuator.
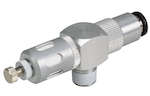
Push-in shut-off hand valves
These valves are designed for shut-off control of the airflow. To operate the valve, use a quarter-turn handle. Turning the handle 90 degrees opens or closes the valve by moving a spool, which has lands and valleys, upward or downward. The land is a thicker part of the spool, which closes the valve and prevents the flow while the valleys allow the airflow when they are positioned between the ports. These valves can be two or three-directional. The three-directional valves have a residual pressure release function. This means that they vent out the compressed air after closing, which relieves the system of the built-up pressure. The two-directional valves do not have the relief function, which is useful in applications that need to keep the residual pressure. View our online selection of push-in shut-off hand valves.
Push-in mechanical valves
These valves control the direction of the flow with a spool. The spool closes or opens desired ports which block or allows the flow through them. The number of ports varies and some products have an option of adjusting the ports’ direction by rotating them independently. Pushing the pin moves to spool downwards to close the valve if it is normally open or opens it if it’s normally closed. The spool consists of lands and valleys. The land is a thicker part of the spool, which closes the valve and prevents the airflow while the valleys allow the airflow when they are positioned between the ports.
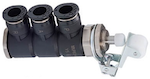
Ball valves with push-in fittings
These valves provide shut-off control of the flow by rotating the ball. The ball has a bore drilled through it and by turning the handle 90 degrees the valve closes or opens. Read our ball valve article to learn more about this functionality. View our online selection of ball valves with push-in fittings.
3/2-way ball valves with push-in fittings
The 3/2-way ball valve designed for directional control of the airflow. Turning the handle 90 degrees directs the flow through the two desired ports at a time. Read our ball valve article to learn more about this functionality.
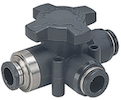
Pneumatic flow control valves with push-in fittings
These valves reduce the inlet pressure (threaded) side and release it to the outlet (push-in fitting) side. The threaded side contains an orifice check valve, which directs the flow to a poppet. This poppet is attached to an adjusting spring which is compressed by an adjusting needle thus setting the desired output pressure rating. The check valve provides pressure control from the inlet side to the outlet side while allowing a free, unmetered airflow in the opposite direction. These valves are usually placed between a directional control solenoid valve and a flow control valve thus providing the flow controller with only as much compressed air as needed. They reduce the supply pressure on the retracting stroke, which conserves the compressed air. View our online selection of pneumatic flow control valves with push-in fittings.
Pressure regulators with push-in fittings
These regulators are designed to keep the outlet pressure at the desired value, encase the inlet pressure were to rise above this set value. This allows for easier and more accurate pressure control. To learn more about pressure regulators go to our pressure regulator article. View our online selection of pressure regulators with push-in fittings.
Pressure gauges with push-in fittings
Insert the tube in the push-in fitting and the gauge will show the system’s pressure rating. To learn more about pressure gauges go to our pressure gauges article. View our online selection of pressure gauges with push-in fittings.
Push-on fittings
Not to be confused with push-in fittings, push-on fittings are also used to provide leak-free connections. They require no tools for installation. They can be used for hard or flexible tubing. The image shows a common push-on fitting with an O-ring for a better seal, but it can also be designed with a tapered thread or hose pillar. They are available in a broad range of configurations, material (typically nickel-plated brass), maximum pressure, and sizes. It is important to ensure that your hoses inner and outer diameter matches the diameters of the push-on side of the fitting. View our online selection of push-on fittings.
Hose barbs
Hose barbs, also called hose tail barbs, are used to connect flexible hoses to components. Ideal for applications where the flexible hose or tube needs to be routed around tight turns. They consist of a male or female threaded section and a barbed tube (a long-tapered cone with ridges). While the threaded section connects to the component, the hose is connected to the barb. It is important to ensure that the diameter of the barb you are selecting is compatible with the inner diameter of your hose for a leak-free connection. For high-pressure applications (or re-assurance), it is recommended to secure the hose to the barb with a hose clamp in order to prevent the hose from disconnecting or leaking. Hose tail barbs come in varying sizes, maximum pressures, and are typically made of plastic, (nickel-plated) brass, or stainless steel. View our online selection of hose barbs.

Compression fittings
Compression fittings offer a convenient way to securely connect pipes together (typically gas or water applications) without soldering. Compression fittings consist of an outer compression ring and an inner compression ring. For water applications, brass or nickel-plated brass are often used, but other material options like PVC or stainless steel are available for other media (chloride solutions or corrosive media). It is important that the inserted pipe is free of burrs, cut straight, and sanded smooth for proper sealing. To learn how to cut a pipe read our pipe cutting article. To install, slide the nut over the end of the pipe and then slide the ring over the end. Insert the pipe into the compression fitting and tighten the nut firmly with two wrenches. However, be careful not to over-tighten. These fittings should not be re-used, because the inner compression ring deforms during compression. View our online selection of compression fittings.
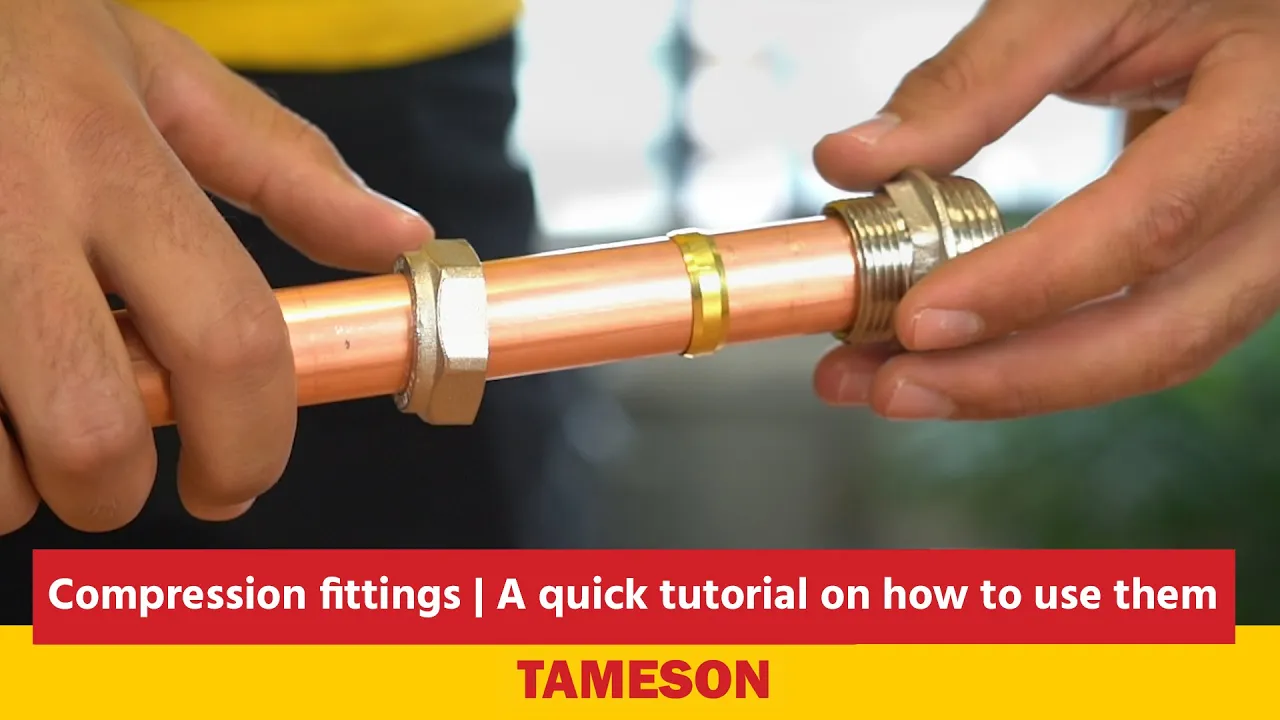
Cutting rings
Cutting rings are used to provide a safe connection between a tube and the coupling. They provide a good seal and easy assembly of a hydraulic pipe system. To install, the cutting ring and swivel nut are inserted into the steel tube. During assembly, the edges of the cutting ring meet the outer surface of the tube and positions itself by cutting into the tube (but not piercing through). This provides proper sealing and increases safety for high operating pressure. They are available in various sizes, pressure ranges, and materials depending upon your application. View our online selection of cutting rings.
End caps & plugs
Plugs, also referred to as a cap, only have 1 port, so they are used to close off ports for permanent setups or for maintenance, inspection, or repairs. A practical example of using a plug is closing off unused ports in a manifold block. It is necessary to close off pipe ends with plugs to avoid spillage, drainage, or a loss of system pressure. Common plugs are threaded into the pipe and tightened with a hex key (Allen wrench). Varying material options are generally available depending on the application. View our online selection of end caps & plugs.
Double nipples
A double nipple is a short length of pipe with male threads at both ends. The threads may be parallel or tapered and are used to connect two female threaded pipes/fittings together or to convert a pipe’s female end to a male end. The two ports can also be of different sizes to be used as an adapter. The most common double nipple design is often referred to as a hex nipple since it has a hexagonal section in the center to tighten/loosen with a wrench. Other types of double nipples include a barrel nipple (unthreaded mid-section) and a close nipple (threaded throughout). Varying material options are generally available depending on the application. View our online selection of double nipples.
Sockets
A socket is a female-threaded short length of pipe of uniform cross-section. It is used to connect two male threads of the same size together. Sockets vary in size and should be selected based on the size of the male threads they are to connect. Varying material options are generally available depending on the application. View our online selection of sockets.
Reducer rings
A reducer ring has a smaller female threaded connection port and a larger male threaded connection. It has male threads on one side and female threads on the other with a hex used by a wrench for tightening or loosening the component. They come in varying pipe sizes, amount it reduces, maximum pressures, and material depending on the application. View our online selection of reducer rings.
Reducing adapters
A reducing adapter has a smaller male threaded connection port and a larger female threaded connection. They come in varying pipe sizes, amount it increases, maximum pressures, and material depending on the application. View our online selection of reducing adapters.
Swivel joints
Swivel joints are used in applications that require a movable or rotational piping system between flow lines. They can sustain repeated rotational movements, thus reducing stress on the hose and improving efficiency. They can rotate 360-degrees in 1, 2, and/or 3 planes. The end connection for the swivel joint may be threaded, beveled or flanged. Features like size, material, and maximum pressure are available in a wide range depending upon the application. View our online selection of swivel joints.
Manifolds
Manifolds are designed to be used in hydraulic applications for distributing fluids or gases from one source to multiple lines. Manifolds typically consist of 1 inlet port and multiple outlet ports. The size of the inlet and outlet and the number of outlet ports required should be given thorough consideration while selecting the manifold. They are available in a wide range of sizes, outlet port numbers, and connection types as per the requirement of your application. Generally, available materials include aluminum, stainless steel, brass, copper, and plastic. View our online selection of manifolds.
ORFS (o-ring face seal)
O-Ring Face Seal (ORFS) fittings provide a connection between the tube and O-ring ports. They are generally designed for high-pressure hydraulic applications. A rubber O-ring is inserted into the circular machined groove in the fitting body. When the O-ring is compressed against the flat face of the female fitting, a tight seal is formed which eliminates the risk of leakage. These fittings are available in a wide range of configurations, materials, sizes, and maximum pressure. Read our hydraulic fitting article. View our online selection of ORFS (o-ring face seal).
Threaded pipes
A threaded pipe has the same size male threads on both sides. They are typically not very long and only used for extending an existing pipe system and connect two female threaded connection points together. Typically, the threads do not extend the whole length of the component and it is smooth in between the threads. It is important to know your media to select the right material for the threaded pipe, but common materials are brass, stainless steel, and zinc-plated steel. View our online selection of threaded pipes.
Angled fittings
An angled fitting allows a connection to be made between two components that are not aligned in a straight line. The angled fitting has two connection points that are at either a 45 or 90-degree angle from one another. The connection points can have male or female threads. Common materials are brass, stainless steel, nickel-plated brass, and cast iron. View our online selection of angled fittings.
Tee fittings
Tee fittings have 3 connection ports and form a "T" shape. Each connection port can have either male or female threads. Depending on which ports are chosen to be inlets/outlets, the fitting can be used for mixing or distributing the media. Therefore, it is important to connect them properly and to select the correct materials. View our online selection of tee fittings.
Y fittings
Y fittings have 3 connection ports as well and form a "Y shape. Each connection port can have either male or female threads. Depending on which ports are chosen to be inlets/outlets, the fitting can be used for mixing or distributing the media. Therefore, it is important to connect them properly and to select the correct materials. View our online selection of Y fittings.
Cross fittings
Cross fittings have 4 connection ports and form a cross shape. Each connection port can have either male or female threads. Depending on which ports are chosen to be inlets/outlets, the fitting can be used for mixing or distributing the media. Therefore, it is important to connect them properly and to select the correct materials. View our online selection of cross fittings.
Couplings
Compressed air couplers are quick-release couplings for compressed air systems. These fittings make it easy to connect or de-connect pneumatic lines while they are under pressure. They exist of two parts: the plug (or nipple) and the socket. They are ideal when you want to regularly (de-)connect different air tools to the compressed air supply. There are many different standards of plug profiles worldwide, so it is important to check if the plug and socket are compatible. The image shows examples of air couplers with the nipple component on top and the socket component on the bottom. They come in varying connection types & sizes, maximum pressures, and material depending on the application. More in-depth information can be found in the air couplings article. View our online selection of couplings.
Hose connectors
A hose connector is typically used to connect a hose to a water tap or hose appliance, like a sprinkler. The male threaded portion can thread into your appliance or water tap and the o-ring nipple side is used to plug into a coupling. They can come in varying pipe sizes, maximum pressures, and material depending on the application. View our online selection of hose connectors.
Water fittings & couplings
For fittings and couplings that are used for water applications, the material of the fitting is especially important. Certifications are available, like NSF, KIWA, or DVGW for example to show the product is safe for water applications. Brass, composites, stainless steel, and plastic can be effective solutions for drinking water applications. For non-drinking water, plastic is often a cost-effective solution. If lead contamination is of concern, lead-free brass is typically more common than a composite or stainless-steel alternative. View our technical article on fluid control components for drinking water applications for more information.
Pneumatic fittings & couplings
For fittings and couplings that are used for pneumatic applications, the pressure and connection style of the fitting are especially important. Ensure that the fitting has a maximum pressure at or above the system’s max pressure to ensure that the fitting doesn’t fail or leak during operation. The connection style is also important and is related to if it is a permanent or semi-permanent fixation (a threaded hose tail barb) or if it will be disconnected regularly (air coupling).
Hydraulic fittings & couplings
For fittings and couplings that are used for hydraulic applications, it depends on the type and conditions of the media. Therefore, the fittings material is especially important, but also the max pressure. Ensure that the material is resistant to the type of hydraulic fluid and that the max pressure is at or above the system’s max pressure to ensure that the fitting does fail or leak during operation. For more information, read our hydraulic fitting article.
Other fitting articles
Are you looking for a different fitting not discussed in this article? Read our other fitting & coupling articles:
- Push-in fittings
- Pneumatic Coupling - How They Work
- Hydraulic Fitting Types and Applications
- Couplings
- A Guide To Camlock Couplings
- Storz Coupling Guide
- How to Distinguish JIC and AN fittings
- JIC fittings and the SAE J514 standards