Needle Valve - How They Work
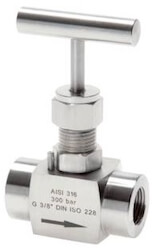
Figure 1: Stainless steel needle valve
A needle valve is used to accurately control flow rates of clean gasses or liquids. Gradual adjustments of the stem and plunger enable smooth flow control. These valves generally have low flow rates and a relatively significant pressure drop from the inlet to the outlet. Standard port sizes for needle valves range from 1/8” to 2” (2 to 12 mm). The most common application of a needle valve is to control gas flow, such as propane in a tank. In this article you will learn how needle valves work, their most common types, selection criteria and more.
Learn about other types of valves in our valve fundamentals article.
Table of contents
- How needle valves work
- Selecting a needle valve
- Needle valve symbol
- Needle valve advantages and disadvantages
- Needle valve applications
- FAQs
View our online selection of needle valves!
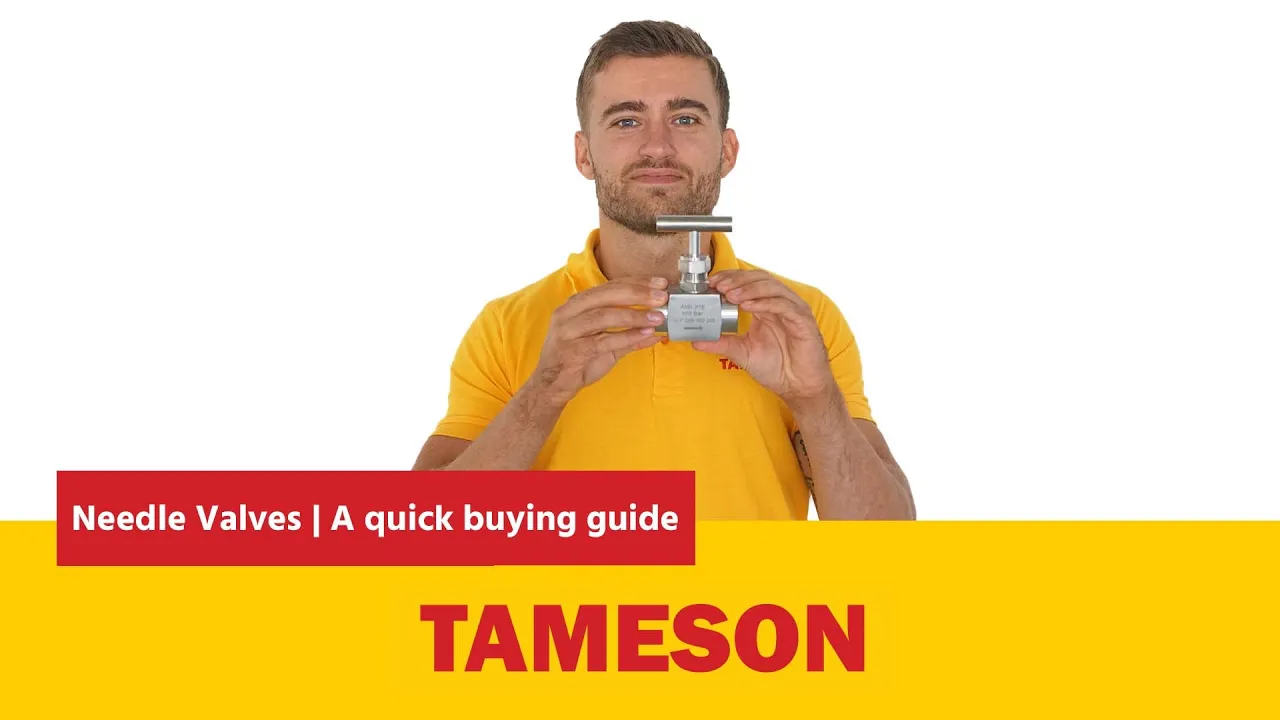
How needle valves work
A manually operated needle valve with a handle or handle wheel is the most common type of needle valve. A needle valve’s plunger has a tapered end that moves up and down to open or close an orifice. Figure 2 shows the cross-sectional view of a manual needle valve. The handle (Figure 2 labeled D) is connected to the plunger, called a stem (Figure 2 labeled E). When the handle turns, the plunger moves up or down through the threads (Figure 2 labeled F). The locking nut (Figure 2 labeled A) prevents the plunger from fully unscrewing. As the plunger moves down, the pointed (tapered) end (Figure 2 labeled G) comes into contact with the valve seat to fully seal the orifice (Figure 2 labeled C). Often, the valve seat is also tapered. This allows for accurate needle valve flow control.
There are various options and sizes available to connect the needle valve to a pipe or hose through the port connection (Figure 2 labeled B) on the input and output such as threaded, flanged, or welded. The bonnet is connected to the valve housing (Figure 2 labeled H), which can be made from different materials like brass or stainless steel.
For an in-depth understanding of different operation types, read our needle valve types article.
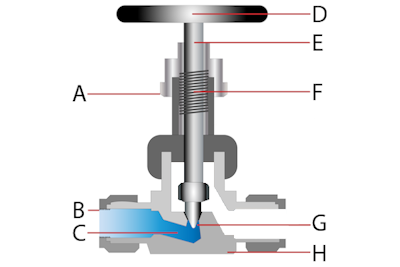
Figure 2: Needle valve cross-section view and components: packing nut (A), port connection (B), orifice (C), handle (D), stem (E), threads (F), tapered end (G), and valve housing (H).
Selecting a needle valve
When selecting a needle valve, four main characteristics and/or application requirements must be considered: material, pressure, size, and temperature.
Material
The most common valve housing materials are stainless steel and brass due to their range of chemical resistance.
Stainless steel
Stainless steel is ideal for environments requiring high corrosion resistance, durability, and strength. Stainless steel needle valve housings are perfect for high-pressure, typically up to 690 bar (10,000 psi) and high-temperature, typically -254 °C to 649 °C (-425 °F to 1,200 °F) applications, especially when using 316 stainless steel, known for its superior resistance to pitting and crevice corrosion in chloride environments. Its non-reactive nature makes it suitable for the food, pharmaceutical, and chemical industries. However, for lower pressures and temperatures, or where corrosion resistance is less critical, materials like brass or plastic may be more cost-effective and lighter alternatives.
Brass
Brass is widely used for needle valve housing in moderate pressure and temperature conditions. Brass needle valves are suitable for hydraulic systems, drinking water, high-temperature applications, and gas piping, typically handling pressures up to 207 bar (3,000 psi) and temperatures from -198 °C to 204 °C (-325 °F to 400 °F). Brass offers excellent machinability for precise manufacturing and tight tolerances and is more cost-effective than stainless steel, making it ideal for less demanding applications. It is suitable for neutral and non-corrosive media, commonly used in drinking water applications. However, brass should not be used for saltwater, distilled water, acids, or chlorides, and is not ideal for highly corrosive environments or very high pressures and temperatures. In such cases, stainless steel or specialized alloys are better due to their superior resistance. Brass is also susceptible to dezincification, a form of corrosion that can weaken the material over time, especially in high-chloride environments.
Pressure
Understanding the application requirements for pressure in a system is crucial for selecting the correct needle valve. The right pressure rating ensures the valve can withstand the system's operating conditions without failure, preventing leaks and maintaining safety. Robust needle valves can handle pressures up to 300 bar (4351 psi) at 20 𐩑C (68 𐩑F).
Port and orifice size
Needle valves are available in a wide range of port and orifice sizes. The connection ports can have male or female ends. Common thread standards used are NPT (National American Pipe Thread), BSP (British Standard Pipe), or metric (ISO standards). The most commonly used needle valves range from 2 to 12 mm (1/8” to 2”). Ensuring the correct port size and orifice size ensures efficient flow and system operation with fewer chances of wear and/or leakage.
Temperature
Needle valves are suitable for both high- and low-temperature applications, but it is essential to specify the valve housing and packing/sealing material appropriately to ensure they can withstand the required conditions. The choice of sealing material is particularly important in extreme temperatures because it ensures the valve maintains its integrity and performance, preventing leaks and ensuring reliable operation under varying thermal conditions.
- NBR (Nitrile Butadiene Rubber) seals are suitable for temperatures ranging from -40𐩑C to 120𐩑C (-40𐩑F to 248𐩑F) and are commonly used in applications involving oils, fuels, and other hydrocarbons.
- Teflon (PTFE) seals can withstand temperatures from -20𐩑C (-4𐩑F) to slightly over 200𐩑C (392𐩑F) and are ideal for applications requiring chemical resistance and high-temperature stability, such as in chemical processing and high-temperature fluid handling.
Needle valve symbol
Figure 3 shows the symbol for a needle valve. The schematic includes the standard 2-way valve symbol with an arrow indicating it is a needle valve.
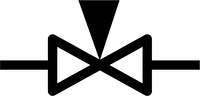
Figure 3: Needle valve symbol
Needle valve advantages and disadvantages
Advantages
- Accurate flow control, especially for applications involving a low flow rate
- Leak-tight shutoff
- Small size
Disadvantages
- High pressure loss because of the high restriction of fluid flow.
- The needle and seat may get damaged if the fluid has suspended solids.
- Examining the needle valve handle does not reveal whether the valve is open or closed.
Needle valve applications
One of the most common uses of needle valves is to monitor gas (e.g., propane) flow in a system. A propane needle valve shuts off the flow accurately and/or controls the flow rate, thereby checking the burn rate for several applications. Needle valves are used extensively in the following areas:
- Needle valves are used in dams, reservoirs, power plants, and water distribution systems for controlling water pressure and flow rate.
- Needle valves are employed in automated combustion control systems to regulate fuel flow.
- These valves are commonly used to shut off a pressure gauge or control the flow rate in flow metering devices.
- Needle valves control the flow of air to cylinders to control piston speed.
Read our article on needle valve applications for a comprehensive list of areas where needle valves are used.
FAQs
What is the function of a needle valve?
A needle valve is used for precise control of fluid flow in various applications, including chemical processing, pharmaceuticals, and instrumentation, where fine adjustments and reliable sealing are essential.
In which applications would you choose a needle valve over a ball valve?
Ball valves are ideal for on-off shutoff applications but are not suitable for throttling. Needle valves are perfect for applications requiring precise fluid control, such as maintaining low fluid flow in a carburetor.