Valve Fundamentals: An Introductory Guide
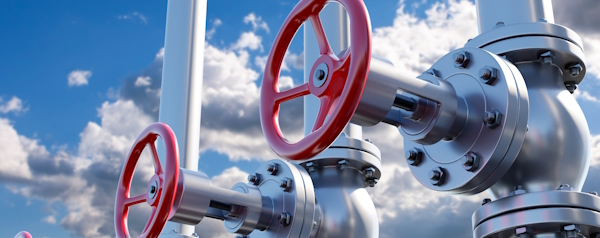
Figure 1: Valves control, direct, or regulate flow.
Valves are designed to allow, prevent, or limit fluid flow within piping systems effectively. These devices play vital roles in systems, from managing pressure to safeguarding against leakage. Understanding various valve types assists in selecting the appropriate valve for specific applications, ensuring efficient operation and system longevity. This article discusses the fundamentals of valves, exploring their definitions, roles in different systems, and material considerations crucial in the selection process.
Table of contents
View our online selection of valves!
What are valves?
Valves are mechanical devices capable of controlling, directing, or regulating the flow of fluids—liquids, gasses, or slurries—by opening, closing, or partially obstructing passageways within a system. These devices are essential in countless industries, such as oil and gas, water treatment, chemical processing, and domestic plumbing. The essential components include the body, bonnet, actuator, packing, seat, and disk, each playing critical roles in the valve's operation.
Primary functions of valves
- Regulating flow: Valves maintain optimal flow rates within a system, preventing aberrations affecting system performance.
- Isolation and safety: They isolate certain sections of a pipeline for maintenance or repairs and protect over-pressurized zones by releasing excess pressure.
- Backflow prevention: Certain valves ensure unidirectional flow, preventing contamination or potential system damage.
Table 1: Types of Valves - Functions and Applications
Valve type | Function(s) | Applications | |
---|---|---|---|
Solenoid valve | ![]() |
Regulating flow, isolation and safety | Automated control systems, irrigation systems, fluid power systems |
Ball valve | ![]() |
Regulating flow, isolation and safety | Oil and gas pipelines, chemical processing, water treatment |
Butterfly valve | ![]() |
Regulating flow, isolation and safety | HVAC systems, water distribution, food and beverage processing |
Directional control valve | ![]() |
Regulating flow | Hydraulic and pneumatic systems, industrial machinery |
Gate valve | ![]() |
Isolation and safety | Water supply systems, wastewater treatment, oil and gas industries |
Check valve | ![]() |
Backflow prevention | Pumping systems, water and wastewater systems, chemical processing |
Needle valve | ![]() |
Regulating flow | Precision flow control in instrumentation, fuel regulation systems |
Angle seat valve | ![]() |
Regulating flow, isolation and safety | Steam and hot water applications, food and beverage processing |
Pinch valve | ![]() |
Regulating flow | Slurry handling, mining operations, wastewater treatment |
Globe valve | ![]() |
Regulating flow, isolation and safety | Steam applications, fluid control in chemical processing, HVAC systems |
Safety valve | ![]() |
Isolation and safety | Pressure relief in boilers, chemical plants, oil and gas industries |
Pressure relief valve | ![]() |
Regulating flow, isolation and safety | Overpressure protection in pipelines, pressure vessels, and compressors |
Coaxial valve | ![]() |
Regulating flow, isolation and safety | High-pressure applications, chemical processing, oil and gas industries |
Zone valve | ![]() |
Regulating flow | HVAC systems, zoned heating and cooling systems, irrigation systems |
Industry standards
Industry standards play a crucial role in ensuring the quality, safety, and performance of valves used across various applications. Recognized organizations develop these standards, which manufacturers, engineers, and end-users widely adopt to ensure consistency and reliability in valve design, fabrication, and testing. Some of the most prominent standards organizations include the American Society of Mechanical Engineers (ASME), the American Petroleum Institute (API), and the International Organization for Standardization (ISO).
How to select a valve
Selecting the right valve for a specific application is crucial to ensure efficient operation, system longevity, and safety. Several factors must be considered during the selection process to match the valve's capabilities with the system's requirements. Below are key considerations to guide the selection of an appropriate valve:
Application requirements
Understanding the application's specific needs is the first step in valve selection. This includes identifying the valve's primary function, such as regulating flow, isolation, safety, or backflow prevention. The operating conditions, such as pressure, temperature, and flow rate, must also be considered to ensure the valve can handle the system's demands without compromising performance or safety.
- Solenoid valve: Ideal for automated control of fluid flow, often used in applications requiring quick response and remote control.
- Ball valve: Best for basic on/off control with minimal pressure drop, suitable for isolation purposes.
- Butterfly valve: Suitable for on/off and throttling control in large diameter pipes, offering a compact design and quick operation.
- Directional control valve: Used in hydraulic and pneumatic systems to direct the flow of fluid to different paths.
- Gate valve: Primarily used for isolation, providing a straight-line flow with minimal restriction when fully open.
- Check valve: Designed for backflow prevention, allowing flow in one direction only.
- Needle valve: Ideal for precise flow control and throttling applications, often used in instrumentation.
- Angle seat valve: Suitable for high flow rates and frequent operation, often used in steam and aggressive media applications.
- Pinch valve: Best for handling slurries or fluids with suspended solids, as it provides full bore flow and minimal turbulence.
- Globe valve: Excellent for throttling and flow regulation, providing good control over flow rate.
- Safety valve: Designed to release pressure automatically to prevent system overpressure, ensuring safety.
- Pressure relief valve: Similar to safety valves, used to protect systems from excessive pressure by releasing fluid.
- Coaxial valve: Used for rapid switching and compact installations, often in pneumatic systems.
- Zone valve: Typically used in heating and cooling systems to control the flow of water or steam to different zones.
Size
The size of the valve is critical for ensuring compatibility with the piping system and achieving the desired flow characteristics. The valve size should match the pipe diameter to minimize pressure drop and maintain efficient flow. Additionally, the valve's flow coefficient (Kv or Cv) should be evaluated to ensure it meets the system's flow requirements.
To follow along with a good example of how to size a valve, read our article on how to size a ball valve.
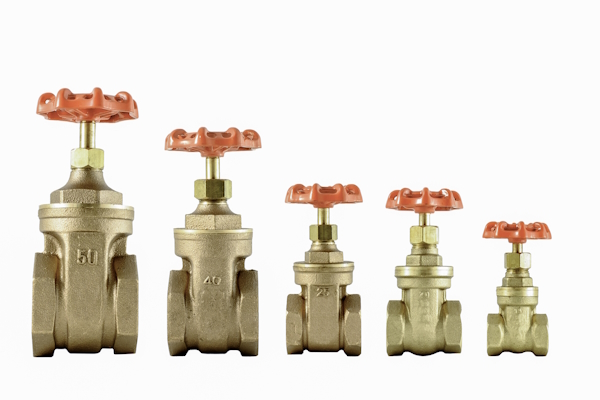
Figure 2: Selecting the right size for a valve ensures optimal flow.
Material compatibility
Material compatibility is essential to prevent corrosion, wear, and potential failure of the valve. The valve materials must be compatible with the fluid being handled, considering factors such as chemical composition, temperature, and pressure.
Common valve body materials include stainless steel, brass, PVC, and cast iron, each offering different levels of resistance to various environmental and chemical conditions. Common valve seal materials include EPDM, PTFE (Teflon), NBR, and FKM.
Learn more about material compatibility in our article on chemical resistance of materials.
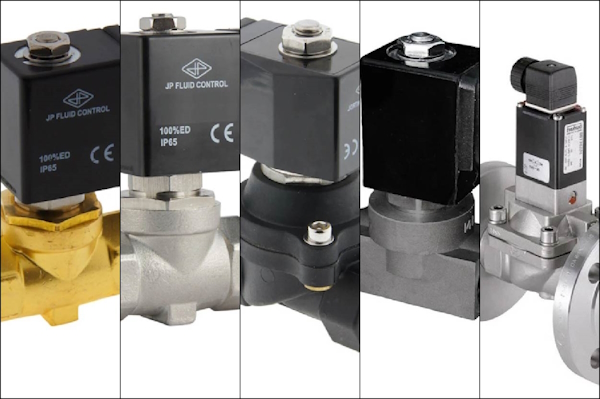
Figure 3: Valves come in a wide variety of materials. Solenoid valves from left to right: brass, stainless steel, PVC, aluminum, and cast iron.
Maintenance needs
Maintenance requirements and ease of access should be considered to ensure long-term reliability and cost-effectiveness. Some valves may require regular maintenance or replacement of components, such as seals or packing. Selecting a valve with a design that facilitates easy maintenance can reduce downtime and operational costs.
FAQs
What is a valve?
A valve is a device that regulates, directs, or controls the flow of fluids by opening, closing, or partially obstructing passageways.
What are the types of valves?
The types of valves include gate, globe, ball, butterfly, check, and diaphragm valves, each serving different functions in fluid control.
Why are valves important in piping systems?
Valves are crucial in piping systems for managing fluid flow, pressure, and preventing leaks, ensuring efficient and safe operation.