Needle Valve Types
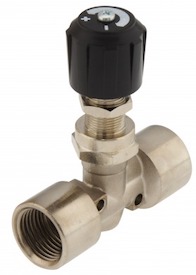
Figure 1: Needle valve
There are three general needle valve designs: straight, angle, and multiport. In addition, needle valves can operate manually, electrically, pneumatically, or hydraulically. This article examines all these types of needle valves to help users understand how they work and how to choose the best type of needle valve to suit an application. Read our comprehensive needle valve article for a further look into needle valve operation, applications, and selection process!
Table of contents
- Straight needle valve vs angle needle valve
- Multiport Needle Valve
- Automated Needle Valve
- Needle valve stem tips
- FAQs
View our online selection of needle valves!
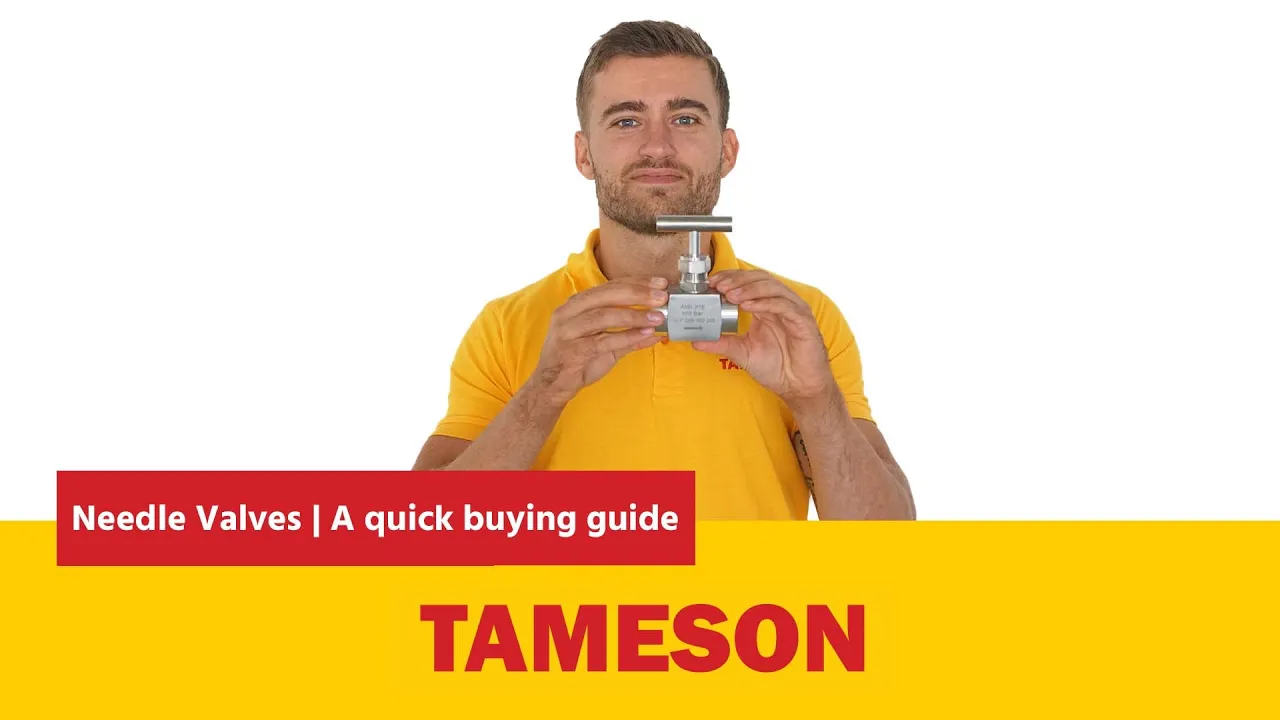
Straight needle valve vs angle needle valve
The naming of straight and angle needle valves refers to the orientation of the inlet and outlet ports in relation to one another. A straight needle valve has an inlet and outlet in a straight line (180° from each other), allowing for a straight flow through the valve. An angle needle valve has an inlet and outlet at 90° from one another.
Due to the internal design, the flow through a straight needle valve takes a zigzag path, otherwise known as a tortuous path. This means there is a higher pressure drop through the valve than an angle needle valve, which has the flow moving at a 90° angle.
Similarities
- Size: Needle valves are small. DN25 (33.4 mm) is typically as large as they get for most applications.
- Stem design: Typically, needle valves have a tapered stem end that perfectly fits in the valve seat. Also, many needle valves have a rising stem.
- Stem stop: Both valve types may have a stopper that prevents the stem from fully coming out of the valve body. A needle valve without a stopper is not for use with hazardous media.
- Operation: The further a needle valve opens, the less pressure drop occurs.
- Media: Clean media is necessary. Solids and slurries can easily get stuck in a needle valve.
-
Applications: Both types of needle valves can continuously modulate flow. Common applications are:
- Controlling the flow rate in metering devices.
- Controlling water pressure and flow rate in dam, reservoir, water distribution, and power plant systems.
- Controlling airflow to pneumatic cylinders to control the piston’s speed.
- Controlling fuel flow in automatic combustion control systems.
Differences
Flow path
A straight needle valve has what is known as a tortuous flow path (Figure 2), meaning the flow turns multiple times between inlet and outlet. An angle needle valve’s flow path is not tortuous and takes a nearly 90° turn from inlet to outlet (Figure 3).
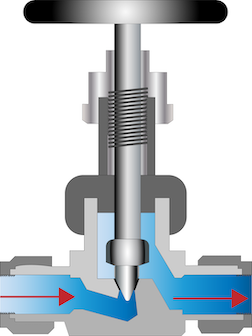
Figure 2: Flow path of a straight needle valve.
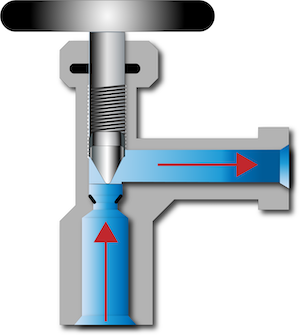
Figure 3: Flow path of an angle needle valve.
Pressure drop and cavitation
A straight needle valve has a significantly higher pressure drop than an angle needle valve. Therefore, straight needle valves are more susceptible to cavitation and flashing than angle valves. These two phenomena occur when a zone of pressure forms that is lower than the liquid’s vapor pressure and a portion of the liquid phases into gas. The difference between the two phenomena is that cavitation reverses (gas turns back into liquid when pressure rises) while flashing does not (gas remains gas).
Whether cavitation or flashing, there is potential for gas bubbles to rupture and cause shock waves which, if near valve components or walls, can cause severe damage over time.
Installation
As discussed above, needle valves are small and do not take up much installation space. Choosing between the two comes down to the system they are needed for. An angle valve has an extra functionality of working as an elbow.
Multiport needle valve
Multiport needle valves have the standard inlet port and multiple outlet ports, commonly two outlet ports but occasionally more depending on the application. The extra outlet port(s) allows the installation of various instruments, typically pressure reading devices.
For example, a pressure gauge can install directly into the multiport needle valve. The primary benefit of this setup is that the number of installation points in the piping is smaller, reducing the potential for leaking or failure at a connection point.
Automated needle valve
Automated needle valves can operate either hydraulically, electrically, or pneumatically. A benefit of using an automated valve is not needing an operator present. However, additional equipment will be necessary for each type of automated valve. Electrically actuated valves require electricity, pneumatic needle valves require a pneumatic system, and hydraulic valves require a hydraulic system and electricity. Temperature and flow sensors typically control the actuators of automated needle valves. Since needle valves are multi-turn valves, meaning that the valve stem needs to rotate more than 360° to fully open or close the valve, this needs to be considered for the actuator type. Some actuators are suitable for quarter-turn valves only (valves that open or close by turning the stem only 90°).
Electronic needle valve
An electric motor or solenoid can electronically actuate a needle valve. A solenoid setup requires a DC power source and a pulse-width modulation (PWM) controller. A PWM controller receives a specific DC voltage and rapidly shuts it on and off, which proportionally inputs the voltage into the solenoid. So, the solenoid can proportionally move the needle valve’s stem between on/off rather than simply having only on or only off.Depending on the motor, an electric motor requires DC or AC voltage to operate. It controls a gearbox that moves the needle valve’s stem between fully open and fully closed, allowing the stem to stop at any point.
Pneumatic needle valve
A pneumatically actuated needle valve typically uses a pneumatic rotary actuator for operation. Pneumatic actuators can be either quarter-turn or multi-turn; a needle valve requires a multi-turn actuator. A pneumatic rotary actuator can be a piston or diaphragm directly mounted onto a manual needle valve. These actuators are available in air-to-open (normally closed) and air-to-closed (normally open) configurations. Clean air from a central compressed air system is required to operate these valves.
Selecting the proper pneumatic actuator for a manual needle valve depends on the valve’s size, system pressure, and air pressure available. Different valve manufacturers have different specifications for these three criteria. It is important to consult the valve’s data sheet before purchasing to determine if it is correct for an application.
Hydraulic needle valve
A hydraulically actuated needle valve works similarly to a pneumatically actuated needle valve. However, instead of using compressed air to move a piston or diaphragm, the system uses hydraulic fluid (typically oil). By utilizing hydraulic fluid, which is non-compressible and allows for forcue multiplication, hydraulic actuators allow for more force to be transmitted to the needle valve.
Hydraulic actuators supply a large amount of force through force multiplication and are stable due to the fluid’s non-compressibility. A hydraulic actuator is ideal when a large amount of force is necessary to operate the valve, for example, when used in the main steam system of a nuclear power plant.
A typical hydraulic piston setup consists of a cylinder that contains a spring, a piston connected to the valve stem, and a supply and return line for the hydraulic fluid. The piston divides the cylindrical chamber into two parts, upper and lower. The spring is in the upper section, and the hydraulic fluid is supplied to and returned from the lower chamber.
With no hydraulic fluid in the lower chamber, the needle valve is fully closed. Hydraulic fluid supplied to the chamber will act against the spring force, raise the piston, and open the valve. Controlling the amount of fluid added to the lower chamber allows precise control of the needle valve’s opening between fully closed and fully open.
Needle valve stem tips
The needle valve’s tip depends on whether the valve is general service or severe service.
General service needle valve
A general service needle valve has packing high up on the stem, so the stem interacts with the media. The three stem tips available are regulating, vee, and soft seat.
- Regulating: Regulating stem tips have the best regulation properties. Due to its finer threads, the valve’s stem needs to turn more to open or close the valve.
- Soft seat: Soft seat stems resist dirty media that may damage other stem types.
- Vee: Vee stems are needle valves' most common stem types. They have better regulating properties than soft seat, but worse than regulating stem types.
Severe service needle valve
A severe service needle valve has packing above the threads and a union bonnet to prevent accidental disassembly. The primary stem type used with this valve is a blunt and ball type. A blunt and ball stem tip is round on the bottom. It turns on the stem as the stem moves down into the seat. So, the stem does not grind into the valve seat and cause damage.
Read our needle valve applications article to know more about the various applications of needle valves.