What Are Cavitation & Flashing
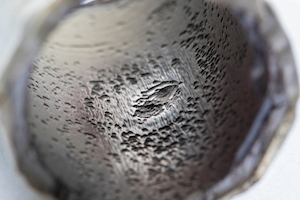
Figure 1: Cavitation-damaged carbon steel tube.
Cavitation and flashing may occur in liquid-media systems that include high-pressure drops. For either phenomenon to occur, pressure in the system must drop below the liquid's vapor pressure. The result is some or all of the liquid phasing into gas bubbles that can potentially cause severe damage, typically in the form of a pit as seen in Figure 1, to the inside of components. This damage can limit a valve's flow control or cause a pipe to leak. Therefore, when designing a liquid-media system, it is essential to understand why cavitation and flashing occur in order to avoid both.
Table of contents
- What is cavitation?
- What is flashing?
- Cavitation & flashing damage
- Predicting cavitation & flashing
- FAQs
What is cavitation?
It's useful to use a water phase diagram to understand how cavitation and flashing occur. As seen in Figure 2, water has three phases: solid, liquid, and gas. Water changes between these phases when there is a temperature or pressure change. The starting point (Figure 2 labeled A) on the diagram shows liquid water. A common household practice is raising the temperature of water to boil it (Figure 2 labeled B). However, without raising temperature, water can change to the gas phase by lowering the local pressure around the water (Figure 2 labeled C). Both temperature and pressure play a significant role in creating cavitation and flashing in liquid transport systems. At high temperatures, minimal pressure losses can lead to cavitation and flashing. Keeping water at normal temperatures does not immediately remedy this problem since large pressure drops are common in systems.
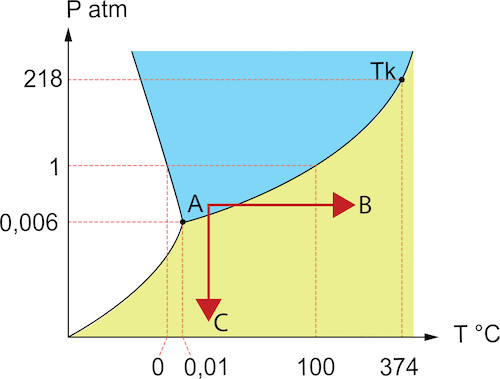
Figure 2: Water phase diagram showing a starting point (A) in liquid that phases to gas at higher temperatures (B) or lower pressures (C). Phase zones: ice (white), water (blue), and steam (yellow).
Cavitation is a two-step process:
- At a constant temperature, some liquid media phases into gas when the media passes through a zone of pressure below the liquid's vapor pressure. Vapor pressure is the pressure at which a liquid phases into a gas.
- When the bubbles pass into a zone of pressure above the vapor pressure, they become unstable and implode.
Upon implosion, a shock wave occurs and extends in all directions. If within one bubble diameter of a boundary (e.g., valve seat, pipe wall, and pump impeller), the force of the shock wave can damage system components. When a bubble implodes near a boundary, the boundary slows the flow on the boundary side of the bubble. So, the liquid opposite of the boundary side of the bubble flows faster, creating micro-jets that impact the boundary, creating a pit. If cavitation occurs, it will sound like a sizzling noise in its early stages. In advanced cavitation stages, though, sounds range from gravelly (medium cavitation) to a loud roar (high cavitation).
Cavitation factors
Beyond a zone of low pressure, four other factors contribute to cavitation:
- Nuclei: Vaporization cannot occur without an interface. For example, the interface for water vapor rising off boiling water is the water's surface. In a closed liquid system, however, nuclei provide this interface. Nuclei are typically free air bubbles found along the boundary (e.g., pipe wall) or trapped in a gap or hole in a suspended solid.
- Ambient pressure: If the liquid pressure immediately around the gas bubbles is above vapor pressure, the bubbles will implode.
- Turbulence: A liquid that passes through an orifice is subject to turbulence, creating eddies, which are circular water currents. The pressure within these eddies is much lower than the surrounding pressure, leading to bubble formation and implosion. Eddies travel through low-pressure separation zones. The size of these zones, and therefore the amount of time eddies spend within them, increases with valve size.
- Pressure recovery: In a typical valve, pressure recovery (i.e., local pressure rising above vapor pressure) occurs immediately after the narrowest flow point (vena contracta). It is common for pressure recovery to go above vapor pressure, leading to bubble implosion. Some valves' design allows pressure recovery to occur further downstream from the vena contracta, so imploding bubbles do not damage valve components.
What is flashing?
Flashing is the beginning stage of cavitation: liquid phasing into gas due to passing through a zone of pressure lower than the vapor pressure. However, the difference between flashing and cavitation is that in flashing, pressure does not recover above vapor pressure, and the bubbles do not implode. However, a valve can become choked due to many bubbles in the flow. Choked means that the flow velocity increases, but the pressure does not decrease. In this instance, water jets flow past the bubbles at high velocities. These jets may impact boundaries, causing damage.
Cavitation & flashing damage
As seen in Figure 1, typical cavitation damage is a cratered surface. These craters form due to the impact of sonic waves and micro-jets. This type of damage is mechanical. Cavitation can also cause chemical corrosion. Typically, an oxide film on the boundary's surface limits corrosion. Weak cavitation may still be strong enough to wear away the oxide film, leading to corrosion damage on the boundary.
The gas-liquid mixture of flashing is abrasive and causes damage similar to the discussion of cavitation corrosion damage in the previous paragraph. Flashing damage leaves behind a smooth and shiny surface.
Reducing damage from cavitation & flashing
The best way to reduce damage from cavitation and flashing is to minimize the potential for either phenomenon to occur. Cavitation is preventable in a few different ways:
- Aeration: Aerating the liquid fills in many voids and may lead to gaseous cavitation. In this cavitation process, bubbles implode slowly. Therefore, violent shock waves and micro-jets do not occur.
- Multiple valves: Use multiple valves, typically two, when a system requires a large pressure drop. Each valve moderately drops the pressure, reducing the chance of pressure in either valve falling below vapor pressure.
- Staged pressure recovery: Certain valves (e.g., some needle valves) have an outlet construction that gradually increases in width. This gradually, instead of all at once, increases the pressure around bubbles that form. In this case, bubbles are less likely to implode near valve components.
If the system factors lead to pressure dropping below a liquid's vapor pressure, there is no way to avoid flashing. However, lining the valve's outlet with a hardened material can protect components. Read more about preventing cavitation and flashing in our cavitation in pumps, valves, and pipes guide.
Predicting cavitation & flashing
Cavitation and flashing are predictable using the Sigma Cavitation Index. Sigma is:
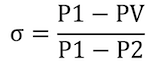
Where:
- PV: The liquid's vapor pressure at flowing temperature
- P1: Upstream pressure
- P2: Downstream pressure
Based on the result of the proportion, the Sigma Cavitation Index seen in Table 1 can help a system designer predict cavitation
Table 1: The Sigma Cavitation Index
σ ≥ 2.0 | No cavitation |
1.7 < σ < 1.7 | A hardened trim can adequately protect a valve. |
1.5 < σ < 1.7 | Minor cavitation. A single-stage trim may adequately protect a valve. |
1.0 < σ < 1.5 | Heavy cavitation is possible. Take cavitation prevention measures. |
σ < 1.0 | Flashing |
Based on the Sigma Cavitation Index, conclude the following:
- The possibility of cavitation reduces as the difference between the upstream pressure and vapor pressure increases. In other words, high-pressure liquid with a low vapor pressure is less likely to cavitate.
- The smaller the difference between the upstream and downstream pressures, the lower the possibility of cavitation.
FAQs
Is cavitation the same as flashing?
No. Flashing is liquid phasing into vapor bubbles, whereas cavitation is liquid phasing into vapor bubbles, followed by the bubbles imploding. The former occurs when the system's pressure drops to below vapor pressure and does not rise again. The latter occurs when the system's pressure drops below vapor pressure and then rises again above vapor pressure.
How can cavitation be prevented?
One method for preventing cavitation is ensuring that the pressure drop through a valve will not drop the local pressure below the liquid media's vapor pressure.