Pneumatic Rotary Actuator - How They Work
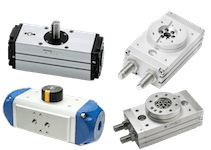
Figure 1: Pneumatic rotary actuators
A pneumatic rotary actuator harnesses compressed air to produce its operational power. Certain models are tailored for remote valve control. The clean, dry air can be supplied by a central compressed air station or, in the case of a compressed gas system, from the process gas itself. The exhaust gas can then be vented into the atmosphere or directed into a downstream lower-pressure process pipeline. These actuators are frequently employed to automate and remotely manage quarter-turn or multi-turn valves, such as ball or butterfly valves.
A pneumatic rotary actuator consists of one or more air chambers with a piston or a bellows diaphragm. Depending on the design, the air pressure forces the piston or the diaphragm to move creating linear or rotary motion. If the created motion is linear, it then internally converts the linear motion to rotational motion. Pneumatic rotary actuators are durable, offer high force relative to their size and can be used in hazardous environments.
Generally, to drive a rotary valve, a rotary actuator is used. However, there are also designs that use pneumatic cylinders, which create linear motion, to generate torque by means of pivot arms or bearings. However, specifying pneumatic rotary actuators for these applications can simplify the design and increase service life. Pneumatic rotary actuators are self-contained, therefore, their parts are not exposed to contaminants and aggressive environments meaning they are less likely to require maintenance over their lifetime.
Buy Pneumatic Rotary Actuator online now!
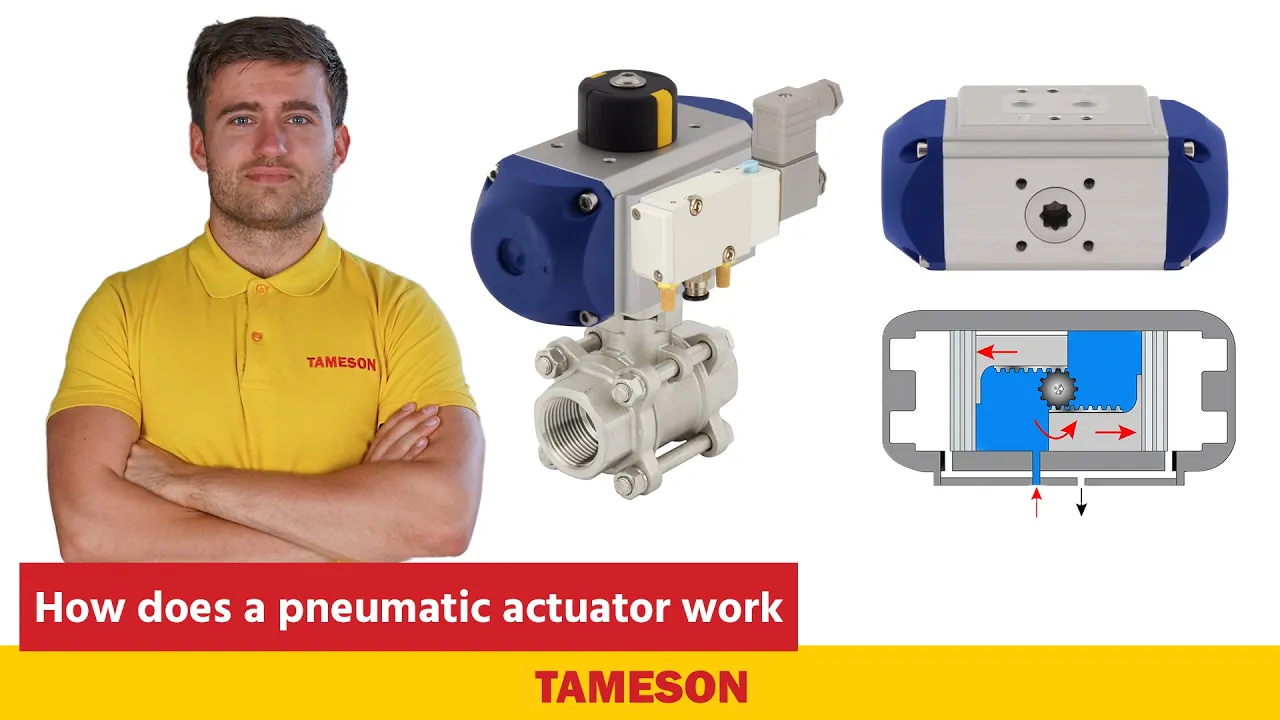
Single acting vs double acting
Pneumatic actuators can be either single acting or double acting. A double acting actuator has air supplied to both sides of the piston. Higher air pressure on either side creates motion to open and close the valve. A single acting actuator on the other hand has air supplied to one side and uses one or more springs to return the piston back to position. A spring return actuator can be designed to be spring-closed or spring-opened. These actuators conserve compressed air, however, double acting actuators provide better control and operate at higher cycling rates. In certain applications it can be an advantage of spring return actuators to return to the base position in case of pressure or power loss.
Design
In pneumatic rotary actuators, the linear force of a piston is converted to torque by mechanisms such as rack-and-pinion or scotch yoke. Vane-type actuators though, can directly produce torque from air pressure.
Rack-and-pinion
A rack-and-pinion, as shown in Figure 2, consists of a circular gear (the pinion) engaged to a linear gear (the rack). When actuated, the piston which is attached to the rack moves linearly. Due to the gear connection to the pinion, it rotates it with the attached output shaft effectively turning the linear motion into rotational.
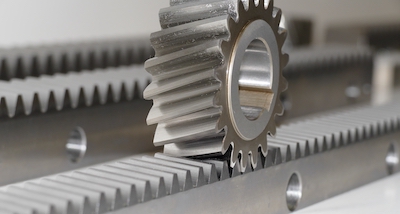
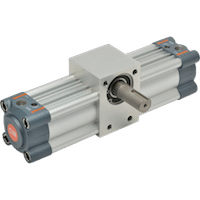
Figure 2: Rack-and-pinion gears on the left and a double acting rack-and-pinion rotary actuator on the right
Often two pistons and racks are installed on the opposite side of each other to double the amount of torque on the pinion as shown in Figure 3. In this double acting actuator, the two chambers on the sides are filled with pressurized air which push the pistons to the center. To return the pistons to the initial position, the chamber in the center is in turn pressurized.
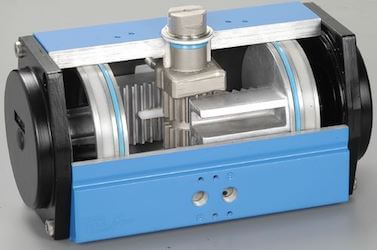
Figure 3: Double acting rack-and-pinion rotary actuators with one rack on the left and one on the right
The rack and pinion design has a fairly high mechanical efficiency. They can product a torque range from a couple Nm to multiple thousands of Nm.
Worn out rack-and-pinion actuators are prone to backlash which is caused by worn down gears and gaps between the gears causing a reduction in accuracy. Where accuracy in positioning is critical, double rack versions are recommended. In comparison to vane-type actuators, rack-and-pinion designs have a larger range of oscillation.
Scotch yoke
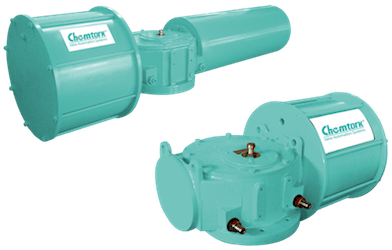
Figure 4: Scotch yoke actuators
In a Scotch Yoke mechanism, the shaft of the piston is engaged with a rotary shaft via a pin and a slot, as shown in Figure 5. The linear motion of the shaft causes the pin to rotate. Scotch yoke actuators can be spring return or double acting. These actuators can also be equipped with two opposing pistons to double the amount of torque on the output shaft as shown in Figure 5 on the right. Scotch yoke actuators are heavy duty actuators producing torques ranging from multiple thousands to hundreds of thousands of Nm.
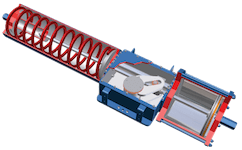
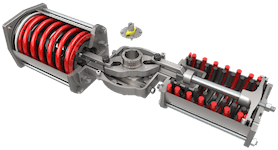
Figure 5: Scotch yoke spring return (single acting) pneumatic actuators
Vane-type
A vane-type actuator shown in Figure 6 has a chamber with a shaft that passes through it and a vane is connected to it. When compressed air is supplied to one side of the vane, the differential pressure causes the vane and the shaft to rotate.
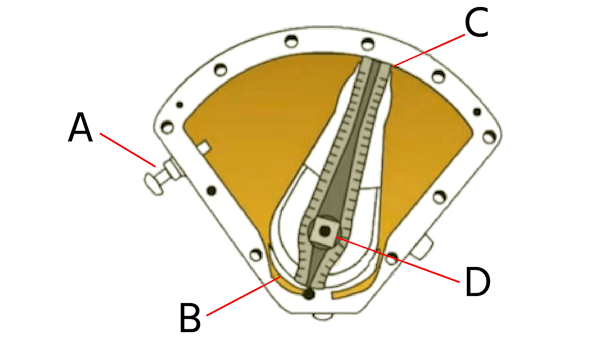
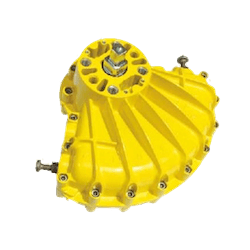
Figure 6: Left: Inside of the chamber of a vane type actuator: stroke adjustment (A), port (B), movable vane (C), and shaft (D). Right: a vane actuator
Vane-type actuators are light duty actuators producing torques ranging from a fraction of a Nm to multiple hundreds. They can be spring return or double acting and come in single vane and double vane configurations. Double vane configurations provide higher torques at the expense of smaller oscillating ranges. The oscillation of double vane actuators varies from 90° to 100° while single vane actuators can have a range of up to 280°.
Selection criteria
The first step in selecting a pneumatic rotary actuator is to figure out the type of actuator best suited for your application. While scotch yoke actuators are primarily used for heavy duty applications, it is wise to consider your options when selecting a rotary actuator for light and medium duty applications.
Rack-and-pinion actuators:
- Advantages:
- Higher mechanical efficiency – 90 to 95%
- Medium duty applications
- High speed actuation
- Larger range of oscillation
- Disadvantages:
- Prone to backlash due to wear
- Slightly more expensive
Vane-type actuators:
- Advantages:
- Typically, more economical in terms of money for torque capabilities
- Light and medium duty applications
- Precise positioning
- Disadvantages:
- Shorter life span in comparison to rack-and-pinion actuators
- Slightly less mechanical efficiency mainly due to leaks around the vane
- Limited range of oscillation
The sizing of the actuator would then be the next step. Pneumatic actuators are often characterized most importantly by the amount of torque they can produce or stop and that leads to the sizing of the actuator. An actuator of a certain size will also likely provide a range of torque depending on the control pressure that is fed to it. Other criteria to consider when selecting a rotary actuator are rotation angle, volume of air needed for the operation, control medium, materials, and interface including output shaft options, flange sizes and pilot air ports.