Modulating Valve - How They Work
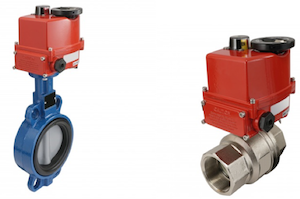
Figure 1: Modulating butterfly valve (left) and modulating ball valve (right)
A modulating valve is a control valve that can be fully open, fully closed, or in-between open and closed allowing a partial flow. They are often automated with an actuator in combination with the valve. Common valve types are: globe valve, disc valve, and quarter-turn valves (butterfly valve or ball valve). To accomplish modulation, the actuator uses a feedback system to give feedback on the valve’s position to the operator. Modulation of the valve position regulates the flow rate, which is often used to control secondary parameters such as temperature, level, or concentration. Figure 1 shows the example of a modulating butterfly and ball valve.
Table of contents
View our online selection of electric valves for modulation!
What is modulation?
Certain electrical valve actuators are capable of carrying out modulating control, which is often referred to as a DPS (digital positioning system). It is able to accurately position the valve anywhere between the fully open and fully closed position (i.e. between 0° to 90°). This is necessary for applications that require a variation in flow rate. Typically, modulation is achieved using a control loop system and a positioning circuit board (PCB) placed in the actuator.
It works by comparing the input position (desired position) to the physical position of the output shaft (actual position). The output shaft’s location is fed back to the PCB board by a potentiometer that is driven by the output shaft. The PCB board then compares the two positions, and if there is a difference it considers this an ‘error’. To correct the error, the control unit will operate the valve until it reaches the desired position (within a tolerance). The control signals are typically either 0-10 V DC or 4-20 mA. A 0 V DC or 4 mA signal completely closes the valve while a 10Vdc or 20mA would completely open it. Any signal between these would cause a corresponding partially opened or closed position. An example would be a 6mA signal that would result in a 12° turn.
An example of an application that requires modulation is in HVAC systems. If the desired input temperature is different than the actual temperature, the actuator will open or close the valve more to increase/reduce the flow of the conditioned air.
Modulating butterfly valve
Butterfly valves provide good flow control in general. The addition of a modulating actuator to these valves allows the valve to control the flow with even finer precision. The modulating actuator is attached to the valve via the stem which in turn dictates the rotation of the disc at the desired angle (between 0° to 90°).
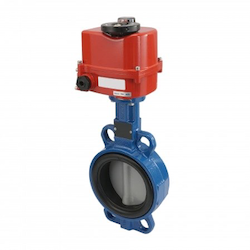
Figure 2: Modulating butterfly valve
Modulating ball valve
Ball valves are generally not used for flow control applications. Therefore, adding on a modulating actuator allows ball valves to be used for such applications. However, it may require some modifications to be effectively used for flow control. The modifications may include using of V-port ball or inserting a trim disc for optimizing flow. Ball valves with actuators are often used in vacuum applications.
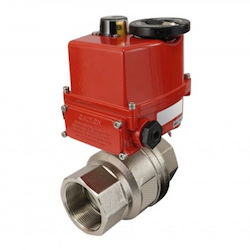
Figure 3: Modulating ball valve
Why is modulation used?
Modulating valves are used in a wide variety of applications because they offer many advantages over a simple on/off control. Some advantages are:
- Precision: The actuator precisely controls the flow by adjusting the amount of flow passing through the valve. This amount can be changed based on the requirement for the application.
- Energy efficiency: The controlled steady run consumes less energy than frequent on/off action.
- Provides remote and automated control.
- Less wear and tear as it doesn’t require a constant on and off action.
There are also a few disadvantages of using a modulation valve such as:
- The actuator can produce heat and may require frequent maintenance.
- Time-consuming compared to a hydraulic or pneumatic actuator.
Modulating valves are commonly used in fluid applications. Some applications using modulating valves are:
- HVAC systems
- Power plants
- Steam supply lines
- Wastewater treatment plants
- Automation industry
- Irrigation systems
FAQ
What does a modulating valve do?
A modulating valve automatically controls the amount of flow in the system. It uses control signals to accurately position the valve at any point between fully open and fully closed (i.e. between 0° to 90°).
How does a modulating gas valve work?
A modulating gas valve is used to control the temperature fluctuation by regulating the gas flow. It is commonly found in residential furnaces. The PCB board in the modulating gas valve monitors the gas input and the temperature control device (thermostat). When more heat is needed, the gas input going to the burner is increased. When less heat is required, the gas input is reduced. Thus, the desired temperature is maintained.
What is a modulating control valve?
A modulating control valve precisely controls the process parameters like pressure, temperature, level, flow rate, etc. and adjusts the input/output positions to receive the optimal result.
What is a modulator valve?
A modulator valve is found in automatic transmissions to shift gears depending upon the load on the engine. Its vacuum line is attached to the intake which measures the amount of vacuum in the system. When the gas pedal is pushed, the throttle plate opens and the vacuum is released. This will cause the modulator valve to downshift the transmission. When the pedal is released to accelerate, the throttle plate closes and the vacuum is increased. This will cause the modulator valve to upshift the transmission.
What is a 2-way modulating valve?
A 2-way modulating valve controls the amount of flow from the input to the output from 0-100%.
What is a modulating actuator?
A modulating actuator is what makes the modulating control valve possible. It is able to open the valve at any position between 0-100% open/closed.