Ball Valves For Vacuum Applications
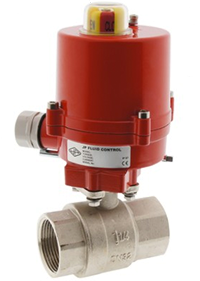
Figure 1: A 2-way brass electric ball valve suitable for vacuum applications
Vacuum ball valves are often used to keep the 'negative' vacuum pressure in the chamber or pipe and as a channel for the vacuum generators or pumps in vacuum conditions. Vacuum conditions are used in industrial applications for pick-and-place systems, and research laboratories. A suitable vacuum ball valve should have very tight sealing properties in the shut-off position, quick response time, and the ability to operate at pressure differences between the sides of the valve. In some vacuum applications, the valve should operate at sub-zero conditions, too.
View our online selection of ball valves!
Ball valve characteristics for vacuum applications
-
Vacuum ball valves can be actuated manually, electrically, or pneumatically and are available in materials such as brass, stainless steel, or plastic, with options for 2-way or 3-way ports.
-
Known for their durability and reliability, ball valves can withstand thousands of operational cycles with little to no maintenance.
-
Ball valves are quarter-turn valves that rotate 90° from open to closed positions, making them fast-acting. When connected to a pneumatic actuator, they can achieve the full 90° rotation in less than a second.
-
The hollow ball within the valve is held in place by a seat, typically made of Teflon, which provides a positive shut-off seal when there is a pressure difference across the valve. This design allows ball valves to open at high-pressure differences without a pressure-balancing mechanism.
-
They can operate at sub-zero temperatures and are available in compact sizes, which is advantageous for vacuum applications requiring smaller valves.
-
The hollow, straight-through design of ball valves ensures no flow resistance.
Applications of vacuum ball valves
Vacuum ball valves are used in a wide range of applications:
-
Plastic molding process and vacuum tubes
-
In the bake-out process for the artificial acceleration of the process of outgassing
-
A vacuum ball valve with pneumatic actuators is used in robotics to pick and drop objects.
-
Semiconductor processing, vacuum engineering, freeze-drying, and fusion research.
-
Medical applications like radiotherapy, radiosurgery, radiopharmacy, and other medical processes require suction.
-
They control gas flow into a chamber, leak testing, vent gases, etc.
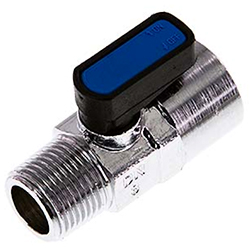
Figure 2: A ¼ inch vented mini brass ball valve suitable for vacuum applications.
Selection criteria
When selecting a vacuum ball valve for your application, consider the following criteria to ensure optimal performance and compatibility:
-
Operation: Decide on the type of operation: manual, electric, or pneumatic, based on control requirements. Manual operation is simple and cost-effective, electric operation allows for remote control, and pneumatic operation is suitable for rapid cycling.
-
2-way or 3-way: Determine whether a 2-way or 3-way valve is needed for the application. For 3-way valves, choose between L-port and T-port designs based on the required flow path. An L-port is suitable for diverting flow, while a T-port can either mix or divert flow.
-
Flow rate (Kv): Ensure the valve can handle the system's required flow rate. If the valve's flow capacity is insufficient, it may cause pressure drops. Conversely, an oversized valve can lead to poor control and increased costs.
-
Materials: Vacuum ball valve housing can be made of stainless steel, brass, or plastic.
-
Stainless steel: Offers excellent corrosion resistance, high strength, and can withstand high temperatures up to 200 𐩑C (392 𐩑F). Suitable for demanding environments and high-pressure applications up to 63 bar (913 psi). But, it can be costly and heavy.
-
Brass: Provides good corrosion resistance and is cost-effective. It is suitable for moderate pressure applications up to 55 bar (798 psi) and temperatures up to 120 𐩑C (248 𐩑F).
-
Plastics (PP, PVDF, PFA): These materials offer excellent chemical resistance and are lightweight. They are suitable for lower pressure applications up to 10 bar (145 psi) and temperatures typically up to 90 𐩑C (194 𐩑F), with a few capable of over 150 𐩑C (302 𐩑F).
-
Typical seal materials are Teflon (PTFE), FKM (FPM), and EPDM. Read our chemical compatibility guide for more information on the compatibility of different materials with various media.
-
Connection type and size:
-
Choose the appropriate connection type, such as flanged, solvent socket, BSP, or cutting ring, to ensure compatibility with existing piping. Flanged and cutting ring connections are recommended for high vacuum pressure levels due to their strong sealing capabilities, which help prevent leaks. For moderate vacuum pressure levels, BSP and solvent socket connections can be used, but they require careful sealing to maintain vacuum integrity. Learn more in our article about ball valve connection types.
-
Connection sizes range from ⅛ to 4 inches, depending on the valve type and material. Proper sizing is crucial to avoid leaks and ensure a secure fit.
-
-
Vacuum level: Select a valve that can handle the required vacuum level, such as -0.9, -0.99, or -0.98 bar. These values indicate the degree of vacuum the valve can maintain, with higher negative values representing stronger vacuums. This is crucial for applications requiring precise vacuum control to prevent leaks or damage.
-
Valve bore: The time desired to achieve a vacuum determines the size of the vacuum ball valve bore. Full bore valves allow maximum flow with minimal pressure drop, while reduced bore valves may be more cost-effective for lower flow applications.
-
Approvals: Ensure the valve has the necessary approvals for your application, such as those for drinking water, gas, or ATEX for explosive environments.
-
Additional considerations:
-
For electric valves, consider the voltage requirements, with typical values being 12V AC/DC, 24V AC/DC, 120V AC, and 240V AC, as well as the operating time, which ranges from 8 to 58 seconds. Incorrect voltage can damage the actuator.
-
For pneumatic valves, determine the operation type, such as double acting, spring closed, or spring open, and ensure the actuator torque is sufficient, up to 103 Nm, to prevent improper valve operation.
-
For more information on how to select the right ball valve for your system, read our ball valve selection article.