Selection Guide For Ball Valves
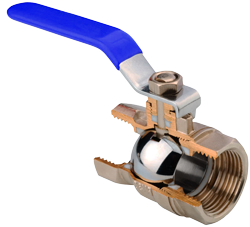
Figure 1: A sectional view of a ball valve
A ball valve is a shut-off valve that uses a rotary ball with a bore to control a liquid or gas flow. The rotary ball is rotated a quarter-turn (90°) around its axis to allow or block the flow through the valve. Ball valves are preferred for their longer service life and reliable sealing property. The wide range of operation types, connection types, circuit functions, housing materials, and other criteria make the valve selection process complex. This article guides through this process to make it easier for our readers.
Table of contents
- Manual or actuated
- Circuit functions
- Flow coefficient (Kv)
- Housing material
- Seal
- Connection types and sizes
- Pressure
- Temperature
- Approvals & standards
- Application example
- FAQs
Check out Tamesons selection of ball valves!
Manual or actuated
Ball valves can be operated manually (Figure 2 left), electrically (Figure 2 center), or pneumatically (Figure 2 right), each with its advantages and disadvantages.
Automatic operation involves choosing between electric and pneumatic ball valves. This decision typically depends on the availability of electricity or compressed air at the installation site and the torque requirements, as pneumatic ball valves offer higher torque and are thus suitable for larger valves. Although electric ball valves have a higher initial cost, they tend to have lower operating costs than pneumatic ball valves.
Manual ball valves are ideal for situations with a low budget, absence of electricity or compressed air, or when automation is not required. However, they are not recommended if the valve needs frequent operation or if the system requires automation.
Read our electric vs pneumatic ball valve article for a more in-depth breakdown.
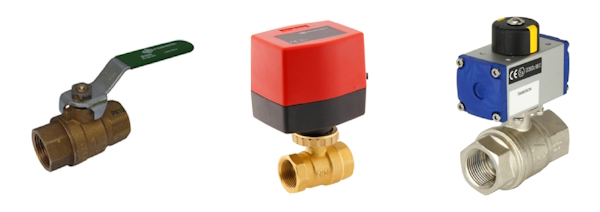
Figure 2: A manual ball valve (left), electric ball valve (center), and pneumatic ball valve (right).
Circuit functions
Ball valves typically have 2-way or 3-way circuit functions:
- 2-way: 2-way ball valves (Figure 4 left) are the most common. These valves provide a straight flow path from input to output.
- 3-way: 3-way ball valves (Figure 4 right) have three ports and are available with either an L or T bore. The L and T designations refer to the design of the internal bore, which will determine the direction of flow. A 3-way ball valve with a T or L port allows mixing, distribution, or redirection of flow direction for different applications. This makes this valve suitable for heating or cooling applications for water, chemicals, and oils.
Read our article on the circuit function of ball valves to learn more about this topic.
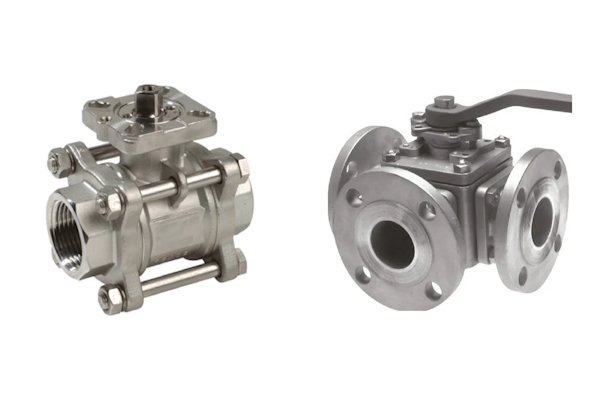
Figure 4: A 2-way ball valve (left) and a 3-way ball valve (right)
Flow coefficient (Kv)
The flow coefficient, or Kv value, is expressed as the flow rate in m3/h of water at 20°C at a pressure drop of 1 bar. The flow coefficient can be calculated as follows:
Where:
- Kv = flow coefficient
- Q = flow rate (m3/hr)
- dP = Pressure differential (bar)
- SG = Specific gravity (water=1)
Use our sizing calculator to find an application's Kv-value and corresponding valve size. Our valves are designated with a Kv value so customers can easily select the correct size.
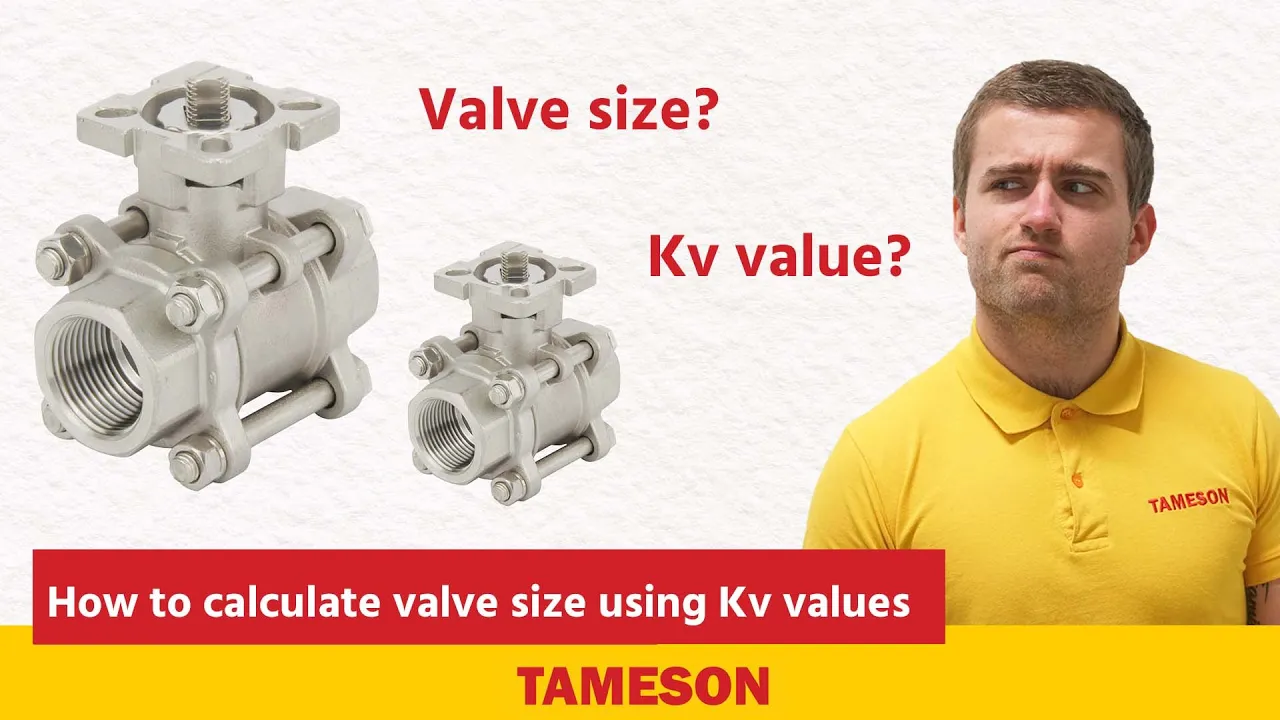
Housing material
The housing material of the valve should be compatible with the fluid media being used for the application. Common materials and their features are:
Brass
- Suitable for neutral and non-corrosive media.
- Brass is versatile, durable and resistant to high temperatures.
- Not suitable for salt water (sea water), distilled water, acids and chlorides.
Stainless steel
- Very good general chemical resistance to almost any medium.
- Very abrasion resistant and resistant to high temperatures and pressures.
- Not suitable for hydrochloric acid, chlorides, bromine and bleach. On the other hand, swimming pool water has a low chloride concentration so the use of stainless steel here is possible.
Plastic
Plastic ball valves are lightweight, easy to install, and offer excellent corrosion resistance, making them ideal for use in corrosive environments. They are cost-effective for many applications but are generally not suitable for high-pressure or high-temperature conditions compared to metal valves.
- PVC (Polyvinyl Chloride): Ideal for water systems, PVC resists acids, bases, and salts, but is not suitable for high temperatures; it is affordable and lightweight.
- PP (Polypropylene): PP offers excellent chemical resistance and handles moderate temperatures, making it suitable for industrial applications.
- PVDF (Polyvinylidene Fluoride): PVDF provides superior chemical resistance and is suitable for higher temperatures, often used in high-purity applications.
- PFA (Perfluoroalkoxy): PFA has outstanding chemical resistance and can handle very high temperatures, making it ideal for corrosive environments.
Seal
Seal materials are crucial for ensuring leak-proof connections and maintaining system integrity in various applications. They are selected based on their compatibility with the media, temperature, and pressure conditions. While some seal materials offer excellent chemical resistance, others are better suited for high-temperature or high-pressure environments.
- PTFE (Polytetrafluoroethylene): Known for its exceptional chemical resistance, PTFE is ideal for use in aggressive chemical environments. It can withstand high temperatures and is often used in applications requiring high purity.
- PA (Polyamide): PA seals offer good mechanical strength and wear resistance. They are suitable for moderate temperature applications and provide a cost-effective solution for many industrial uses.
- EPDM (Ethylene Propylene Diene Monomer): EPDM is excellent for water and steam applications due to its superior resistance to weathering, ozone, and UV exposure. However, it is not suitable for use with oils and hydrocarbons.
- FKM (Fluoroelastomer): FKM seals provide outstanding resistance to high temperatures and a wide range of chemicals, including oils and fuels, making them ideal for demanding applications.
- POM (Polyoxymethylene): Also known as acetal, POM offers good mechanical properties and is resistant to various chemicals. It is suitable for applications requiring low friction and high dimensional stability.
Connection types and sizes
There are different sizes and types of ball valve connections to connect them to a system. The common ones are:
- Standard/Threaded ball valve: Threaded connections (Figure 3 top left) are the most common type of connection used in various temperature and pressure applications.
- Flanged ball valve: Flanged connections (Figure 3 bottom left) join the port to the piping system. These valves are often used on larger-sized pipes. Choosing a flanged ball valve requires consideration of pressure ratings and flange compression class, which indicates the highest pressure it can withstand.
- True union ball valve: True union connections (Figure 3 top center) have a solvent socket connection at each port. The center part of the valve can be easily dismantled and taken off while the valve is installed. This is suitable for quick repair and maintenance in the flow system.
- Compression ring ball valve: Compression ring connections (Figure 3 top right) connect to the piping system by compressing a ring onto the pipe, creating a tight seal. This type is often used for smaller-diameter pipes and is suitable for systems requiring disassembly and reassembly.
- Cutting ring ball valve: Cutting ring connections involve a metal ring that cuts into the pipe when tightened, creating a secure and leak-proof seal. This connection is commonly used in hydraulic systems because it is reliable under high-pressure conditions.
- Hose pillar ball valve: Hose pillar connections (Figure 3 bottom right) are designed for flexible hose attachments, featuring a barbed end (pillar) that allows a hose to be slipped over and secured with a clamp. Typically used in low-pressure applications and systems where flexibility is required.
- Glued sleeve ball valve: Glued sleeve connections involve using an adhesive to bond the valve to the piping system. This type is often used with plastic pipes and is suitable for systems with a permanent, leak-proof connection.
- Welded sleeve ball valve: Welded sleeve connections involve welding the valve directly to the pipe, creating a permanent and robust connection. Suitable for high-pressure and high-temperature applications, it is often used in industrial settings where durability and strength are critical.
To learn more about ball valve connection types read our technical article about ball valve connection types.
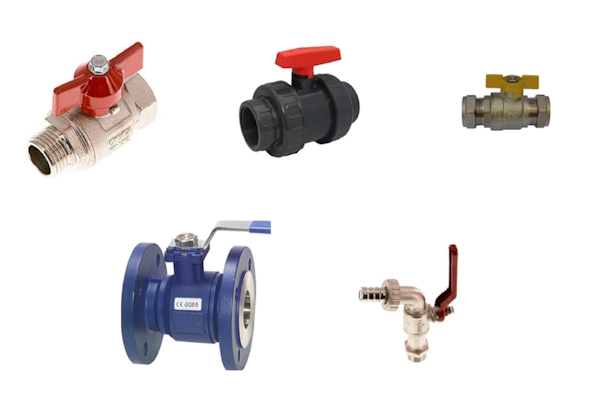
Figure 3: Common ball valve connection types: threaded (top left), true union (top center), compression ring (top right), flanged (bottom left), and hose pillar (bottom right).
Pressure
When selecting a ball valve, it is crucial to ensure that it can withstand the minimum and maximum pressures of your system. Both the housing and seal materials significantly influence the ball valve's pressure range. Stainless steel housings typically offer the highest pressure ratings, followed by brass and plastic materials like PVC.
However, the seal material also plays a critical role. For instance, seals made from FKM (Fluoroelastomer) provide excellent resistance to high pressures and a wide range of chemicals, making them suitable for demanding applications. Always consult the ball valve's datasheet to confirm the specific pressure range for an application.
Temperature
The temperature range a ball valve can handle is determined by both the housing and seal materials. Each combination offers different capabilities:
- Brass ball valve: Typically suitable for temperatures ranging from -20 °C to 160 °C (-4 °F to 320 °F). When paired with PTFE seals, the valve can handle higher temperatures due to PTFE's exceptional thermal resistance.
- PVC ball valve: Generally operates within -10 °C to 60 °C (14 °F to 140 °F). The use of EPDM seals can enhance performance in water and steam applications, although they are not suitable for oils and hydrocarbons.
- Stainless steel ball valve: Offers a broad temperature range from -40 °C to 220 °C (-40 °F to 428 °F). When combined with FKM seals, the valve can withstand even higher temperatures and a wide range of chemicals.
Approvals & standards
Depending on the application, ball valves may need to be made to specific standards or receive approvals from regulatory bodies for particular applications, like drinking water or gas applications.
- Drinking water: WRAS, KIWA, or DVGW approvals
- Gas: DVGW or EN-331 approvals.
- ATEX: The ATEX regulations are two EU directives detailing minimum safety requirements for workplaces and equipment used in explosive atmospheres.
Application example
Residential water lines commonly have ball valves at different points. The following steps outline how to choose a ball valve for this type of application.
- Operation type: Select a manual ball1 valve, as this application requires no automation and can be manually operated.
- Circuit function: Choose a 2-way ball valve with a straight flow path.
- Housing material: Brass housing is suitable due to its compatibility with hot water.
- Seal material: Choose an EPDM seal due to its compatibility with drinking water.
- Connection type size: Choose a standard/threaded ball valve for drinking water applications.
- Flow coefficient (Kv): Calculate the Kv value by knowing the water's inlet pressure, outlet pressure, and flow rate in m3 inside the residence. However, for typical applications like a residential water line, it can often just be sized off the surrounding pipe size rather than the Kv value.
- Pressure: A brass valve can withstand a maximum pressure of up to 80 bar, sufficient for the goal.
- Temperature: Brass valves can operate in temperatures up to 160 °C, which is high enough for residential water systems.
FAQs
What is a ball valve selection guide?
A ball valve selection guide helps choose the right valve based on operation type, connection type, materials, and specifications.
How do you measure ball valve size?
Measure ball valve size by determining the diameter of the pipe or opening the valve will fit, typically in inches or millimeters.
What factors influence ball valve material selection?
Ball valve material selection depends on fluid type, temperature, pressure, and environmental conditions to ensure durability and performance.
How do you choose ball valve seat material?
Choose ball valve seat material based on fluid compatibility, temperature, pressure, and wear resistance for optimal sealing and longevity.