What is a Pressure Gauge?
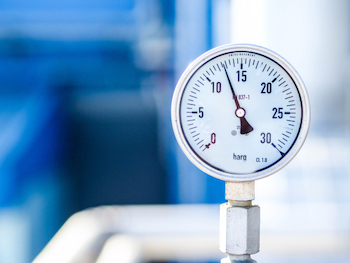
Figure 1: Pressure gauge.
A pressure gauge measures the pressure of a gas or liquid within a system. It monitors the fluid pressure in various applications, such as automotive, aerospace, medical, and manufacturing industries. Measuring the pressure in a system is critical to ensure the consistency of a product and a measure of safety to be aware of leaks or building pressure in a system. Before specifying a pressure gauge, it is vital to understand the basic principles of pressure. This article covers how pressure gauges work and how to select one for an application.
Table of contents
- What is a pressure gauge?
- Types of pressure gauges
- Selection criteria
- Accessories
- Safety and service life
- FAQs
View our online selection of pressure gauges!
What is a pressure gauge?
A pressure gauge is a device that measures the pressure (intensity) of a fluid. It typically consists of a dial or digital display that indicates the pressure, along with a sensor that measures the pressure and converts it into an electrical signal that can be read by the display. Monitoring the pressure value of a hydraulic system keeps a check on the building pressure within the system. A hydraulic system is designed to work in a set pressure range, so it is crucial to ensure that the pressure gauge is rated for the operating range. Pressure gauges typically consist of a pressure-sensitive element (like a bourdon tube or diaphragm) connected to a measuring mechanism and display such as a dial or digital readout. The pressure-sensitive element deforms under the pressure of the gas or liquid, and this deformation is converted into a readable measurement by the measuring mechanism.
To read a pressure gauge, identify the units of measurement and observe the needle's position on the scale to determine the pressure. For digital gauges, simply read the displayed number, ensuring the units are correctly set.
There are three types of pressure: static, dynamic, and total/stagnation pressure. Most commonly, pressure gauges will measure static pressure, which is what this article discusses. Read our article on different pressure forms for a deeper understanding of pressure.

Figure 2: Pressure gauge symbol.
Types of pressure gauges
Pressure gauges can be broadly classified into two main types: analog and digital. Analog pressure gauges are the traditional type, using a mechanical process to measure and display pressure. They are known for their durability and simplicity. On the other hand, digital pressure gauges offer a modern approach, featuring electronic components to provide a precise digital readout. Digital gauges are appreciated for their accuracy, ease of reading, and advanced features such as data logging. Each type has its specific applications, advantages, and considerations for use.
How do analog pressure gauges work?
Many techniques have been developed to measure pressure in a system, and among these techniques, aneroid gauges, also known as analog or mechanical gauges, are the most widely adopted technology.
Analog gauges measure pressure using a metallic pressure-responsive element. This element takes different forms, but its main functioning principle remains the same: flexing elastically under a pressure differential application. The deformation of this element can then be measured and converted into the rotation of a pointer on an analog scale display.
Bourdon tube pressure gauge
A bourdon tube is a flattened thin-wall closed-end tube formed into a C shape or a helix, as seen in Figure 3. As the fluid pressure is applied to the inside of the tube, the oval cross-section becomes more circular and straightens the tube. The tube regains its shape as fluid pressure disappears. The change in the shape of this tube creates a motion pattern at the free end of the tube, which is converted into a pointer rotation with links and gears.
A bourdon tube measures gauge pressure (relative to atmospheric pressure). The bourdon tube is the most commonly used pressure gauge type because of its excellent sensitivity, linearity, and accuracy. Read our article on bourdon tube pressure gauges for more details on the device's operating principle and selection criteria. Bourdon tube gauges come in various designs and specialties to serve various applications. The pressure range of bourdon tube gauges varies from 0 - 0.6 bar (0 - 8.7 psi) to 0 - 1600 bar (0 - 23206 psi) with an accuracy class (discussed later in this article) of typically between 0.1 and 4.0. They are usually made of stainless steel, brass, or monel (nickel alloy). The bourdon tube pressure gauge is the most common and is used in many applications as a medium or high-pressure gauge. Chemical, HVAC, automotive, and aerospace industries use bourdon tube gauges for pressure measurement.
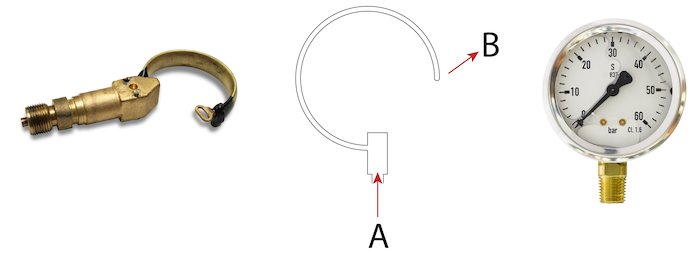
Figure 3: Bourdon tube (left), Bourdon tube working schematic showing the applied pressure (A) and force developed (B) (middle), and the dial (right).
Diaphragm type pressure gauge
A diaphragm pressure gauge uses the deflection of a flexible membrane that separates two environments, as seen in Figure 4. One side of the diaphragm can be exposed to the atmosphere (the gauge pressure is measured in this case), or it can be sealed against a vacuum (in which case absolute pressure can be measured). The diaphragm is often metallic or ceramic, which can be clamped between two flanges or welded. As the pressure builds, it flexes the diaphragm, which can turn this into a dial measurement through gears and linkages. Read our article on diaphragm pressure gauges for more details on the working principle and selection criteria of the device. Diaphragm pressure gauges are suitable for corrosive gasses, liquids, or highly viscous media. The gauge is widely used in chemical/petrochemical, power stations, mining, on and offshore, and environmental technology industries. Diaphragm-type pressure gauge measures pressures between 0 - 2.5 mbar (0 - 0.036 psi) and 0 - 25 bar (362.5 psi), with an accuracy class of typically between 0.6 and 2.5.
Diaphragm pressure gauges have been successfully used by numerous industries for both absolute and differential pressure measurement applications. They are used in applications where high-level purity is desired. It is also suitable for industries dealing with corrosive fluids. Industries like food and beverage, pharmaceutical, petrochemical, and mining use diaphragm-type pressure gauges.
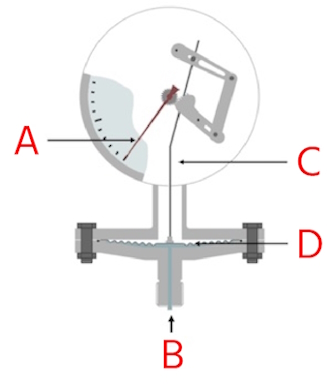
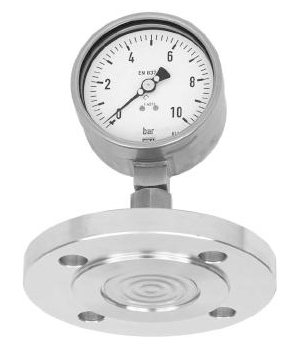
Figure 4: Left: Diaphragm pressure gauge components: pointer (A), pressure inlet (B), link (C), & diaphragm (D) Right: Diaphragm type pressure gauge.
How do digital pressure gauges work?
Digital pressure gauges utilize electronic sensors to measure pressure. These sensors convert the pressure into an electrical signal, which is then processed by the gauge's internal circuitry to display the pressure reading digitally. Digital gauges offer high precision and can include features such as backlight displays, peak pressure recording, and connectivity options for data logging or system integration. For more detailed information on digital pressure gauges, refer to our dedicated article on digital pressure gauges.
Selection criteria
Pressure gauges come in various designs, each of which serve specific applications and industries. Several factors like accuracy, dial size, environment, media, and operating pressure range affect the selection of these devices. Also, there are various applications that pressure gauges are used for, like swimming pool filter gauges, vacuum pressure gauges, compressor gauges, and water pressure gauges. Read our selection tips for pressure gauges to learn more about all the factors that are needed to make a decision on a pressure gauge.
Pressure units
Pressure gauges come in a variety of display units. Table 1 describes the commonly used units in pressure gauges, along with their conversion to their equivalents in Pascals.
Table 1: Common units used in pressure gauges
Pressure units | Pascal (Pa or N/m2) | |
---|---|---|
1 Bar | = 105 | |
1 at (kg/cm2 or kgf/cm2 or Technical Atmosphere) | = 9.80665 × 104 | |
1 atm (Standard Atmosphere) | = 1.01325 × 105 | = 760 Torr |
1 Torr (mmHg or Millimeter of mercury) | = 1.333224 × 102 | |
1 cmH2O (cmWc or Centimeter of water) | = 98.0665 | = 10 mmH2O |
1 mmH2O (mmWc or Millimeter of water) | = 9.80665 | |
1 lbf/in2 (Psi) | = 6.8948 × 103 | = 16 ozf/in2 |
1 oz/in2 (oz/in2) | = 4.30922 × 102 | |
1 inHg (inch of mercury) | = 3.37685 × 103 |
Pressure ranges
European norm EN 837 provides standardized procedures, design requirements, testing and installation guides for commonly used pressure gauges. EN 837-1 and EN 837-3 provide information on the design of dials of concentric scales. Pressure gauges can work with a wide variety of ranges, from low pressure water pressure gauges, to high pressure hydraulic pressure gauges that are often fitted with snubbers. The preferred unit of pressure is the bar, and Tables 2-6 give details on the pressure ranges most commonly used. Please note that it is necessary to confine the normal operating pressure of the gauge to 25 - 75% of the scale. If the process involves pulsation, the maximum operating gauge pressure should not exceed 50% of the full-scale range.
Pressure ranges in bar
Table 2: Pressure ranges (in bar)
0 - 0.6 | 0 -1 | 0 -1.6 | 0 - 2.5 | 0 - 4 |
0 - 6 | 0-10 | 0 -16 | 0 - 25 | 0 - 40 |
0 - 60 | 0 - 100 | 0 -160 | 0 - 250 | 0 - 400 |
0 - 600 | 0 -1000 | 0 -1600 |
Pressure ranges in mbar
Table 3: Pressure ranges (in mbar)
0 - 1 | 0 - 1.6 | 0 - 2.5 | 0 - 4 | 0 - 6 |
0 - 10 | 0 - 16 | 0 - 25 | 0 - 40 | 0 - 60 |
0 - 100 | 0 - 160 | 0 - 250 | 0 - 400 | 0 - 600 |
Vacuum ranges in bar
In vacuum pressure gauges, the pointer rotates in an anti-clockwise direction with an increasing vacuum.
Table 4: Vacuum ranges (in bar)
-0.6 - 0 | -1 - 0 |
Vacuum ranges in mbar
Table 5: Vacuum ranges (in mbar)
-1 - 0 | -1.6 - 0 | -2.5 - 0 | -4 - 0 | -6 - 0 |
-10 - 0 | -16 - 0 | -25 - 0 | -40 - 0 | -60 - 0 |
-100 - 0 | -160 - 0 | -250 - 0 | -400 - 0 | -600 - 0 |
Combined pressure and vacuum ranges in bar
Table 6: Combined pressure and vacuum ranges in bar
-1 - 0.6 | -1 - 1.5 | -1 - 3 | -1 - 5 |
-1 - 9 | -1 - 15 | -1 - 24 |
Nominal size
The nominal size (NS) of a gauge is the diameter of the gauge. The nominal sizes of gauges, according to EN 837, are 40, 50, 63, 80, 100, 160, and 250 mm.
Pressure gauge accuracy
Accuracy classes (KL) determine the maximum margin of error each pressure gauge is allowed to have in terms of the percentage of the maximum scale reading. For example, a pressure gauge with a maximum reading of 10 bar and accuracy class 4 may deviate from the actual pressure by 4% ( 0.4 bar). Another example is a gauge that has a scale of 0-100 bar with an accuracy of 2%. This means that the gauge is accurate to within 2 bars across its full range. Installing a pressure gauge with low accuracy can lead to faulty measurements, and using a gauge with excessively high accuracy increases the cost of purchasing, calibrating, and maintaining that gauge. For more information on calibration, read our article on how to calibrate a pressure gauge.
Table 7: Accuracy class of pressure gauges
Accuracy class | Limits of permissible error (Percentage of Span) |
0.1 | 0.1% |
0.25 | 0.25% |
0.6 | 0.6% |
1 | 1% |
1.6 | 1.6% |
2.5 | 2.5% |
4 | 4% |
Materials
Since pressure gauges use various elements in measuring pressure, it is important to consider the chemical compatibility of materials when choosing the right pressure gauge. Please refer to the chemical compatibility chart.
Types of mounting and connection
- Standard threaded connection: This type of gauge is simply screwed into an available thread. The threads are sealed using a compression seal for tapered threads and an o-ring for parallel threads.
- Integrated pressure gauge: This pressure gauge mounting is accommodated by a female thread.
- Flange pressure gauge: This kind of mounting is offered for those who wish to install the pressure gauge onto a control cabinet.
Accessories
Various accessories can be used with pressure gauges. Common ones are:
-
Seals/gaskets: These ensure a proper seal.
- Flat: The seal is flat and doesn't allow extra rotation of the pressure gauge readout.
- Profile: The seal has a profile to it and allows for a 1/2 or full turn of the pressure gauges readout to ensure proper installation orientation. Profile seals can either be external or internally centered.
- Safety caps: A rubber cap to go over the pressure gauge to add durability and shock absorption.
- Reducers: If the input of the pressure gauge and the output connection size is different, a reducer can be used. It can also be useful if the connection type is different on both (i.e., BSPP and NPT).
- Push-on connectors: Push-on connectors allow a quick and easy way to install or uninstall a hose to the pressure gauge.
- Snubbers: A pressure snubber dampens the effects of pressure spikes and pulses, allowing the pressure gauge to remain readable and extend its service life.
Safety and service life
According to EN 837-2, for safety purposes, a pressure gauge shall be selected with a range such that the maximum working pressure does not exceed 75% of the maximum scale value for steady pressure or 65% of the maximum scale value for cyclic pressure.
When using hazardous pressure media such as oxygen, acetylene, combustible substances, and toxic substances, it is necessary to choose a pressure gauge with additional safety measures, such as a blow-out device on the rear. These safety measures ensure that any leaks or bursting of pressurized components will not injure anyone at the front of the scale.
The entire case of gauges that are prone to constant mechanical vibrations is often filled with oil or glycerin. This would be the case with pressure gauges used in high pressure washers.
In rapidly pulsing pressures, such as gauges placement by reciprocating pumps, an orifice restriction is commonly used to even out the pressure fluctuations and provide an average reading. This increases the lifespan of the gauge by omitting unnecessary wear on the gauge gears. Wear and tear are normal for gauges over time. Read our article on troubleshooting pressure gauges to learn more.
FAQs
What does an industrial pressure gauge do?
It measures the pressure of a gas or liquid in an industrial setting. The device monitors and controls the fluid pressure in a wide range of applications in automotive, aerospace, medical, and manufacturing industries.
How do pressure gauges work?
Pressure gauges consist of a pressure-sensitive element connected to a measuring mechanism and display such as a dial or digital readout. The pressure-sensitive element deforms under the pressure of the gas or liquid, and this deformation is converted into a readable measurement by the measuring mechanism.
What is a natural gas pressure gauge?
A pressure gauge for natural gas measures the natural gas pressure and leak detection. It is usually made of brass or stainless steel.