Pressure Gauge Maintenance And Troubleshooting
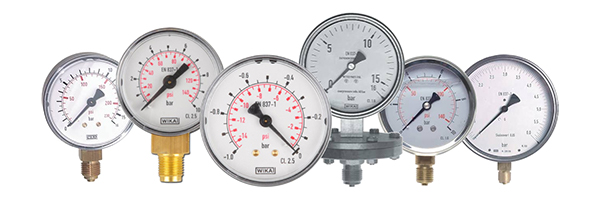
Figure 1: Pressure gauges come in various sizes, scales, and connection types.
Pressure gauges require regular maintenance to ensure they provide accurate and reliable pressure readings. Maintenance on pressure gauges is ordinarily minimal, aside from periodic calibration. They are used in a wide variety of residential and industrial processes, so knowing how to maintain and troubleshoot them for proper system operation is important.This article discusses some of the critical steps that should be taken to maintain pressure gauges, how to test them, and ensure that they continue to function correctly.
Table of contents
- Calibration standards
- Selecting a pressure range
- Factors that negatively impact pressure gauges
- FAQs
View our online selection of pressure gauges!
Calibration standards
The National Institute of Standards and Technology (NIST), a non-regulatory agency in the USA, sets the standards for pressure gauge calibration.
- Traceable calibration: Traceable calibration ensures a measurement device or instrument is calibrated to a known standard.
- Accuracy: Choose a calibration gauge with at least four times greater accuracy than the tested pressure gauge. Additionally, the pressure ranges of the calibrator and tested gauge should match. However, a digital pressure testing device with a range that falls within the acceptable error rate can also be used.
- Frequency: Determine the frequency of calibration by considering factors such as the application for which pressure is measured, how precise the measurement needs to be, and other factors that contribute to a pressure gauge's lifespan, like vibration, pulsation, pressure spikes, pressure cycles, temperature, and environmental conditions.
Selecting a pressure range
Consider the working pressure and the maximum system pressure while choosing the operating range of a pressure gauge. The maximum pressure refers to the highest pressure the gauge may be exposed to, while the operating pressure is the average pressure it will experience continuously. To ensure accurate readings, the operating pressure is recommended to fall within the middle of the gauge's range. For example, if a system has a working pressure of 3 bar (43.5 psi) and a maximum pressure of 6 bar, an ideal pressure gauge would have a range of 0 - 6 bar (87 psi). It is crucial that the pressure never exceeds the maximum reading on the gauge, as doing so can result in inaccurate readings, system leaks, and a shortened gauge life. If necessary, install a pressure relief valve to make it easier to read the dial indicator and to prevent the instrument from coming into contact with excessive pressure. Read our pressure gauge selection article for more details on selecting pressure gauges for an application.
Factors that negatively impact pressure gauges
Factors that negatively impact pressure gauges are:
- Vibration
- Pressure spikes, pressure cycling, and pulsation
- Temperature
- Compatibility of wetted parts
- Improper installation
This section covers these factors and also proposes solutions.
Vibration
Vibrations are the primary reason for pressure gauge failure in manufacturing facilities. These vibrations make it difficult to read the pressure gauge’s pointer. Also, the vibrations gradually damage the pointer mechanism over time, leading to inaccurate readings.
Solution
Use a liquid-filled dial to dampen the needle's vibrations and lubricate internal parts. Read our article on liquid-filled pressure gauges for more details. An alternative is positioning the gauge further from the vibration source by utilizing a diaphragm seal with a capillary connection. The diaphragm seal can be installed in various locations within the system, and it also offers the possibility of remote monitoring.
Pressure spikes and pulsation
Vibration is the continuous oscillation of mechanical parts in a system. In contrast, pulsation is a regular occurrence of rapid pressure increase of the media.
Solution
- Check the operating range of the gauge first if the system encounters frequent pulses or pressure cycling in the application. An easy way to detect pressure spikes in a system is to use a gauge equipped with a maximum pressure pointer. When left on a system, this will indicate the maximum pressure displayed over time. Another option is to use a digital gauge with logging capability.
- As with mechanical vibration, using liquid-filled cases helps reduce pressure spikes in a system. Use protective devices like socket restrictors. This compact device is equipped with a tiny opening that slows down and controls the pressure of the media before it reaches the gauge. Restrictors are affordable and can be easily installed into the system. Many compressed gas regulators have a restrictor already integrated into the bore.
- For more severe pulsations, a snubber or needle valve can be used.
- Snubbers act similarly to restrictors but offer a more comprehensive range of material options, aperture sizes, and pressure ratings. Snubbers are also less likely to become clogged and can be easily adjusted on-site through interchangeable pistons or adjustment screws.
- Needle valves also regulate the flow of the media, reducing the impact of pulsations. They are frequently found in pump discharge and boiler house applications.
Temperature
Exposing a pressure gauge to temperatures below or above the pressure gauge manufacturer's specifications may damage the gauge.
Solution
- Always consult the manufacturer's requirements for maximum ambient temperature and maximum media temperature to verify that the pressure gauge will not be exposed to temperatures beyond its top ratings.
- A diaphragm seal equipped with a capillary tube allows for measuring pressure at a distance from extreme temperatures. The longer the capillary tube length, the more heat is dissipated before the media pressure reaches the gauge.
- Attach cooling adapters to the pressure gauges. The fins in these adapters are effective at radiating and dissipating heat. Use siphons, cooling towers, and similar devices to reduce the media temperature if necessary.
Compatibility of wetted parts
Wetted parts are the components of a sensing device on the measurement side that contact the liquid media. The internal wall thickness of pressure gauges is thinner than many system components and more susceptible to leakage in the presence of even mildly corrosive media.
Solution
- Always ensure that the wetted parts are compatible with the liquid being measured. Use our chemical compatibility charts to verify that the gauge material is compatible with the media.
- Refer to the wetted parts of the pressure gauge and the process media used in the system. Whenever a compatibility chart indicates a rating less than the highest possible (usually ‘A’ or ‘+’), choose another wetted part with the highest resistance to the process media.
- A pressure gauge is typically only made of one of three wetted materials: copper alloy, 316 stainless steel, or Monel alloy. Use a diaphragm or chemical seal when there is a demand for different wetted parts. A diaphragm or chemical seal isolates the gauge's internal parts and the process media. Also, it is crucial to install a steam siphon in front of a gauge installed in the steam service, regardless of the wetted parts. This helps prevent damage to the gauge’s internals.
Installation
Damages caused during installation are a common reason for premature pressure gauge failure. Always install pressure gauges with a wrench; never turn them by hand. Read our article on pressure gauge operation and installation for more details on installing a pressure gauge.
FAQs
Why is my air pressure gauge not working?
Air pressure gauge failures can be due to multiple reasons like pulsation and vibration, extreme system temperatures, corrosion, clogging, and overpressure.