Vacuum Pressure Gauge Guide
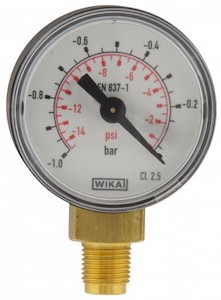
Figure 1: A vacuum pressure gauge
A vacuum pressure gauge measures vacuum pressure, which is lower than atmospheric pressure. It is used in many industrial, laboratory research, and automotive applications. These gauges are essential for processes requiring precise pressure control, such as semiconductor manufacturing or chemical processing. This article covers how vacuum pressure gauges work, their typical applications, and how to select one for an application.
Table of contents
- What is vacuum pressure?
- How does a vacuum pressure gauge work?
- How to select a vacuum gauge
- How to read a vacuum pressure gauge
- What are typical applications for vacuum gauges?
- Accuracy of vacuum gauges
- How to calibrate a vacuum pressure gauge
- FAQs
View our online selection of pressure gauges!
What is vacuum pressure?
Vacuum pressure (Figure 2 labeled C) measures the pressure of a gas in a space where the pressure is lower than atmospheric pressure. It is expressed as a negative gauge pressure, often in units of millimeters of mercury (mmHg) or Pascals (Pa). Other pressures displayed in Figure 2 are:
- Absolute pressure (A): The pressure measured relative to a perfect vacuum.
- Gauge pressure (B): The pressure measured relative to the atmospheric pressure.
- Atmospheric pressure (D): The pressure exerted by the weight of the atmosphere on a given point.
- Absolute zero pressure (E): Absolute zero pressure is a theoretically perfect vacuum.
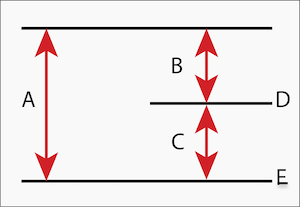
Figure 2: Visualization of pressure types: absolute pressure (A), gauge pressure (B), vacuum pressure (C), atmospheric pressure (D), and absolute zero pressure (E).
Read our article on pressure types for more information on the kinds of pressure and pressure gauges used to measure them.
How does a vacuum pressure gauge work?
The following list explains the various components of a vacuum pressure gauge and how they work together to provide accurate pressure readings.
- A vacuum pressure gauge uses a sensor to measure the difference in pressure between the device and the surrounding atmosphere.
- The sensor, typically a bourdon tube or diaphragm, changes position or shape in response to changes in pressure.
- A mechanical linkage connects the sensor to a pointer on a gauge dial, allowing the user to read the pressure reading quickly.
- The gauge may also have electronic components that convert the sensor's mechanical movement into an electrical signal. The signal can display the vacuum gauge pressure reading on a digital display or send the data to a remote monitoring system.
How to select a vacuum gauge
There is not a single vacuum gauge that is suitable for all vacuum measuring applications. Therefore, it’s necessary to consider the following when determining which vacuum gauge to select for any given application:
- Measuring range: Select a gauge that covers the expected pressure levels in the application. Ensure the range is neither too broad, which can reduce accuracy, nor too narrow, leading to overpressure and potential damage.
- Scale division: The scale division indicates the smallest pressure difference that can be read on the gauge. Choose finer-scale divisions for applications requiring high precision.
- Accuracy Class (EN 837-1): The accuracy class indicates the permissible deviation between the actual and stated pressure, expressed as a percentage of the full-scale range. Select a gauge with a lower rate (higher accuracy) for critical applications requiring high precision (discussed later).
- Connection size: The connection size must match the system with which it will be integrated. Connection sizes 1/8, 1/4, and 1/2 inches are typically available for vacuum gauges.
- Material of process connection: The connection port material is in direct contact with the medium; hence, it should be compatible with the medium to prevent corrosion and degradation. Use our chemical compatibility chart for guidance. Common materials are brass and copper alloy.
- Dry vs liquid damped: Choose a liquid-filled pressure gauge if the application produces heavy vibrations or shocks that can damage the gauge. If heavy vibrations are not expected, a dry pressure gauge is suitable.
- Cabinet material: The cabinet material, which is not in contact with the fluid, should suit environmental conditions. Options are steel, stainless steel, and plastic. Stainless steel is best for corrosive environments, while plastic suits less demanding situations.
- Cabinet diameter: The pressure gauge dimensions must fit the available space. Ensure the gauge is positioned for easy visibility and access for reading and maintenance.
- Connection location: Rear connections are often used for panel mounting, while bottom connections are typical for direct mounting.
- Maximum medium temperature: The gauge must withstand the medium's maximum temperature. Options are available for vacuum pressure gauges that can operate up to 80 𐩑C (176 𐩑F).
- Degree of protection (IP rating): The IP rating specifies the gauge's resistance to dust and water. For instance, an IP65 rating protects against dust and low-pressure water jets, making it suitable for outdoor or harsh environments. Choose a gauge with an IP rating that matches the environmental exposure conditions.
How to read a vacuum pressure gauge
- Identify the major units that have the largest marks on the indicator.
- Find the difference between the major units.
- Count the number of spaces between the major units.
- Divide the difference between the major units by the number of spaces to determine the pressure represented by each space.
Example
Consider a vacuum pressure gauge with major markings at 0.0, 0.5, 1.0 bar, etc. The difference between major units is 0.5 bar. If there are 10 divisions (spaces) between each major unit, each small division represents 0.5/10 = 0.05 bar. If the needle is pointing to the third space after the 0.0 bar mark, the pressure reading is: 0+(3×0.05) = 0.15 bar. The reading should be expressed as a negative value to indicate a vacuum condition.
What are typical applications for vacuum gauges?
- Industrial use: To control pressure in industrial processes like vacuum drying or distillation.
- Pick and place: Vacuum pick-and-place applications are found in many industries, including the automotive, food and beverage, manufacturing, pharmaceutical, chemical, and nautical sectors.
- Medical equipment: In suction devices and vacuum-assisted delivery systems.
- HVAC systems: When installing or repairing a refrigerant circuit, pull a vacuum to evacuate air and matter from the system.
- Research: To measure and control pressure in laboratory experiments. For example, the pressure can be measured in a vacuum to see how materials behave at low pressures.
- Automotive: To monitor vacuum in brake systems with a brake booster, which controls proper power breaking.
- Food processing: To monitor pressure levels in vacuum packaging machines.
- Pharmaceuticals: To monitor pressure levels in vacuum drying and granulation processes.
- Fire service water pump system: Fire services use systems to pump water, typically fitted with special vacuum gauges called compound gauges. Compound gauges can measure positive and negative pressure.
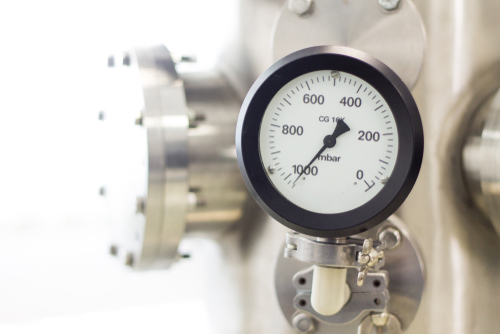
Figure 3: A vacuum pressure gauge on a vacuum chamber in a laboratory.
Accuracy of vacuum gauges
The accuracy of a pressure gauge is defined as the difference between the actual pressure value and the value indicated on the dial. The EN 837 standard establishes accuracy requirements for pressure gauges, which are expressed as accuracy classes. For example, an accuracy class of 2.5 indicates that the indicator may deviate up to 2.5% of the pressure range from the actual value. In the case of a vacuum gauge with a pressure range of 1 bar (15 psi), this would result in a deviation of 0.025 bar. It is important to note that the deviation can occur in either direction. Additionally, it is worth noting that factors such as temperature fluctuations and vibrations can impact the gauge's performance, and even reading the dial can introduce minor deviations in the accuracy.
How to calibrate a vacuum pressure gauge
Like other pressure gauges, calibrating a vacuum gauge requires a calibrator that meets the ISO/IEC 17025 requirements. ISO 3567 details the necessary technical, physical, and metrological criteria. Read our article on pressure gauge calibration for an overview of calibrating a vacuum pressure gauge.
FAQs
How is vacuum pressure measured?
The most common device used to measure vacuum pressure is a bourdon-style manometer.
What is the difference between gauge pressure and vacuum pressure?
Gauge pressure and vacuum pressure are both measured relative to the atmospheric pressure. The difference is that gauge pressure is higher than atmospheric pressure, while vacuum pressure is lower.
Is vacuum positive or negative pressure?
Vacuum pressure is usually expressed as a negative number and measured relative to atmospheric pressure. A negative pressure gauge (a vacuum gauge) measures vacuum pressure.
What is the difference between a vacuum pressure gauge and a compound pressure gauge?
A vacuum pressure gauge measures pressure below atmospheric pressure, while a compound indicator of pressure measures pressure in both positive and negative ranges (high to low pressure).
What is the typical application of a low pressure vacuum gauge?
Low pressure vacuum gauges monitor and control vacuum levels in HVAC systems, laboratory experiments, and industrial processes.