Needle Valve Installation and Maintenance
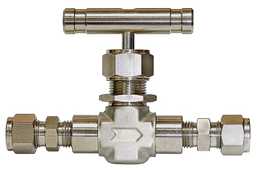
Figure 1: Needle valve
Needle valve installation and maintenance can be straightforward and smooth processes. There are different methods for needle valve installation, depending on the valve's connection type. Needle valve maintenance involves periodic inspection and attention given to the needle valve's internal components. This article aims to outline the common methodologies used to install and maintain needle valves.
Table of contents
- What is a needle valve?
- How to install a needle valve
- Needle Valve Maintenance
- Periodic Inspection
- Troubleshooting
- Packing gland adjustment
- Packing replacement
- Disassembled valve inspection
- Needle valve lubrication
- FAQs
View our online selection of needle valves!
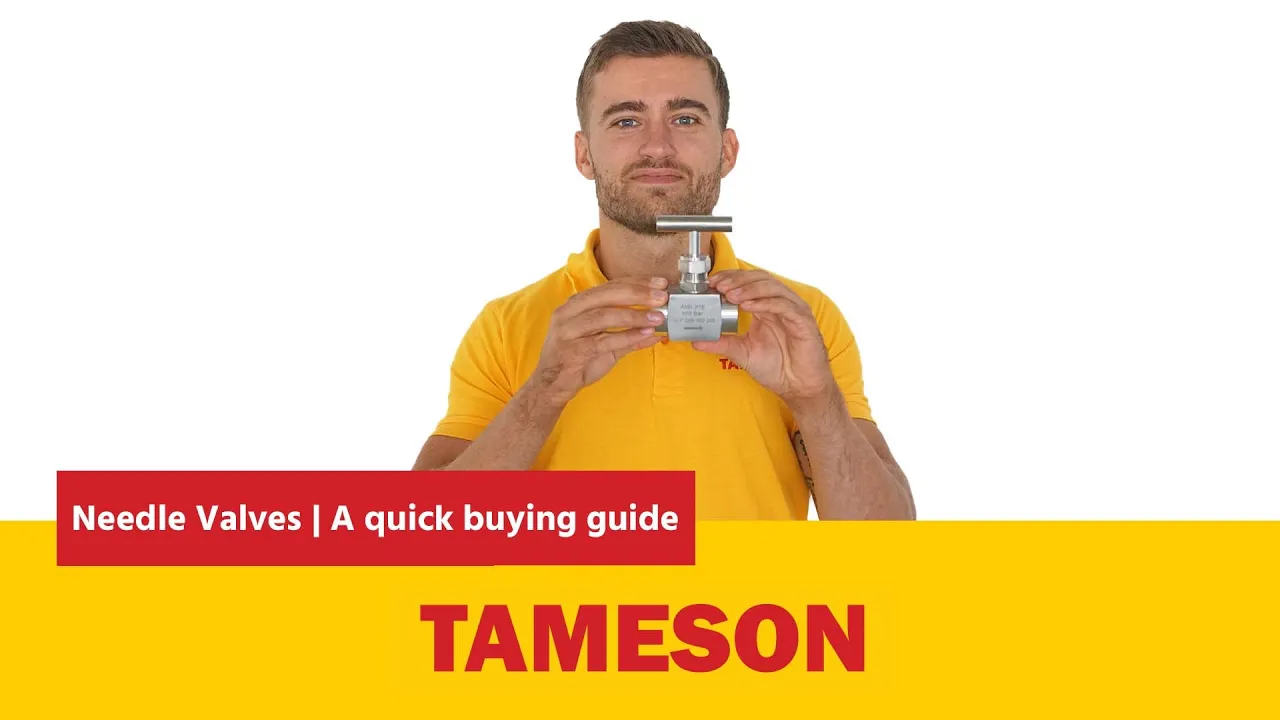
What is a needle valve?
Needle valves, also known as plunger valves, are used to precisely control media flow rates. Due to needle valves' relatively small size, they can be installed in smaller spaces and can control flow rates of even low flows. Needle valves are also reliable as shut-off valves.
Needle valves operate well in liquid and gas applications such as low-pressure hydraulic systems, flow-metering applications, chemical processing, water heaters, and more. For a more comprehensive understanding, read our needle valve article.
How to install a needle valve
Needle valves are suitable for horizontal or vertical installation. The correct procedure for installing a needle valve depends on the type of connection points: threaded, flanged, or soldered. However, among the installation methods, there are some common steps before and during installation:
- Ensure that the application conditions are compatible with the valve's specifications.
- The valve's specifications may be on the valve's body; if not, check the valve's operation manual.
- Specifications listed are:
- Part number
- Pressure rating
- Flow direction
- Material
- Heat code *
- Inlet and outlet dimensions
- Ensure the inside of the valve body and the piping is free of dirt, dust, and other particles.
- Make sure the valve seat is clean.
- Conduct a complete open/close cycle to ensure the valve's components function correctly.
- Ensure there is no pressure in the piping.
- Make sure there is enough space around the valve's installation location for it to operate correctly.
- Orient the needle valve correctly so that the arrow on the valve faces the same way as the flow direction.
*Heat code refers to Heat Code Traceability (HCT). HCT ensures a user can trace where the valve’s metal came from. Also, the user can ensure that the chemical and physical specifications of the valve metal are as they should be.
Connection-specific instructions
After taking the above steps, follow the steps below depending on the needle valve's connection type.
Threaded
- Use several wraps of Teflon (PTFE) for pipe joint sealant.
- Before threading the end of the pipe into the needle valve’s connection point, ensure that both are properly aligned to avoid cross-threading.
- Thread each end of the pipe into the valve's end connections. Screw the pipe ends in until they are hand tight, then use a wrench to tighten them one-half to one-and-a-half turns past hand tight.
- Tightening further can cause stress on the valve, which leads to failure.
Flanged
A good practice is to install a dismantling joint to one end of the valve (Figure 2).
- Dismantling joints simplify installation because, without them, the flanges must be perfectly distant from one another.
- The valve's manufacturer determines the distance.
- Without a dismantling joint, if the distance between the flanges is even a few millimeters off, cracking can occur during the tightening of flange bolts and nuts.
- Dismantling joints also make adding, replacing, or repairing valve flanges simpler without needing to uninstall the valve entirely from the piping.
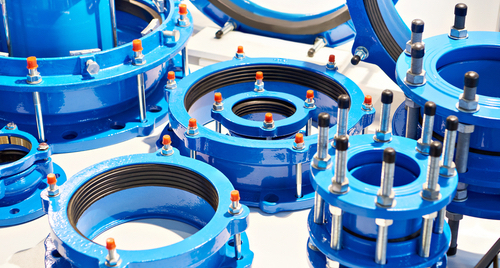
Figure 2: Dismantling joints
- Ensure that the pipe flanges are positioned in the centerline of the pipes and are parallel.
- Bolt the valve to the pipe flanges. As seen in figure 3, tighten the nuts crosswise to prevent gasket or seal damage.
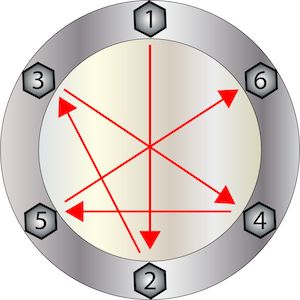
Figure 3: Crosswise tightening pattern
Soldered
- Prepare the pipe before installation. Cut tubing square, meaning use a pipe/wheel cutter to cut the pipe perpendicular to the pipe's surface and not at an angle.
- Deburr the inside of the pipe ends using a deburring tool (Figure 4).
- Deburr outside of pipe ends.
- Polish pipe ends with sandpaper.
- Clean pipe ends with solvent.
- Apply solder flux to the outsides of the pipe ends and inside the valve ports. Solder flux cleans the surfaces that will be soldered and prevents oxidation of the solder tip.
- Ensure pipes are supported to avoid stress on the valve.
- Install the valve onto one of the pipes ends.
- Many manufacturers instruct users to install a needle valve in the closed position, while others recommend the open position. Read the manufacturer's instructions before installation.
- Begin soldering. During this process, aim the torch flame away from the valve body to protect components within the valve. Continuously move the torch around the connection’s circumference to avoid heat concentration and damage. Some manufacturers recommend wrapping a wet cloth around the valve before soldering.
- Heat the pipe before heating the valve's connection point.
- Repeat the soldering process to connect the other valve end to the piping.
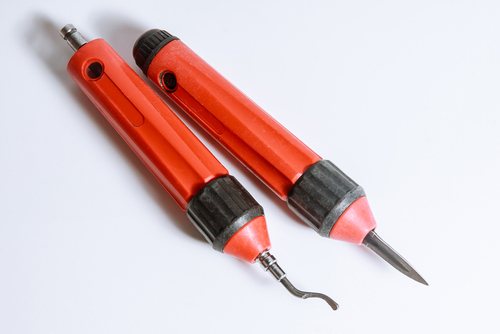
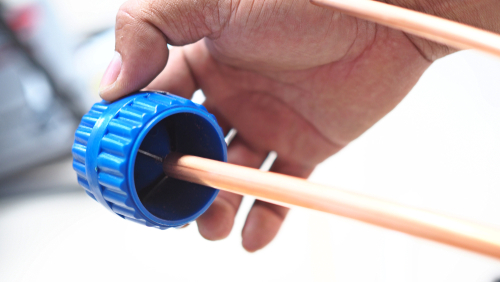
Figure 4: Deburring blades (left) and hand reamer (right).
Needle valve maintenance
Maintaining valves for smooth operation is a necessary part of valve usage; needle valves are no exception. The following information about needle valve maintenance is relevant for most needle valves. However, it's important to read a valve's manual or contact the manufacturer for any information specific to a specific valve. Most importantly, determine whether or not conducting maintenance on a valve will void the valve's warranty.
The following guidelines are best practices when conducting maintenance on a needle valve:
- Always depressurize the valve before disassembling it.
- If flammable or hazardous media flows through the valve, run inert gas (e.g., nitrogen) through the system before disassembly.
- Work on the valve should be done on a workbench, not the ground, to avoid dirt and dust getting into the valve.
Periodic inspection
How often to inspect a needle valve for maintenance depends on the fluid quality, environment, and the system's operating conditions. When examining an installed and operating valve, check for the existence of cracks, scratches, discoloration, or deformation.
- Cracks: Cracks can occur if water freezes in the valve. Small cracks on the ports may be soldered; however, soldering cracks on the valve body will likely damage internal valve components.
- Scratches: Scratches in the coating can lead to corrosion. Recoat the valve as soon as possible.
- Discoloration: Discoloration may indicate that the valve was too hot and internal components are damaged.
- Deformation: Deformation of the valve body requires needle valve replacement.
If your system uses flanged connections:
- Check flanges for tightness.
- Ensure the valve and actuator operate smoothly.
- Check for leakage from the valve.
- Conduct a complete open/close valve cycle to prevent the buildup of solids.
- Tighten any components that have loosened slightly since the last inspection.
Troubleshooting
Table 1outlines a needle valve’s common issues, their reasons, and how to solve them.
Table 1: Needle valve troubleshooting
Issue | Reason | Solution |
The needle valve cannot open or close | Solid particles have built up in the valve | Disassemble the valve and remove solids |
Fluid is leaking past the needle valve when it is in the fully closed position |
The media in the system has worn the plug | At a minimum, replace the stem. Consider needle valve replacement. |
Solid particles have built up, and the valve is stuck open | Disassemble the valve and remove solids | |
Fluid leaks from the valve |
The packing nut is loose | Tighten packing nut |
Packing is worn | Replace packing |
Packing gland adjustment
Follow the steps below to adjust a needle valve's packing gland:
- Depressurize the system.
- Open the needle valve completely.
- Use a torque wrench to apply torque to the packing nut according to the valve manufacturer's specifications.
- If a torque wrench is unavailable, tighten the nut approximately 1/16 turn. After following this step multiple times until the nut has been tightened 1/2 turn, replace the packing.
- Pressurize the valve to its maximum operating pressure and check for leaks.
- If leakage still occurs, repeat steps 1-5.
- After several attempts, if leakage still occurs, replace the packing.
Packing replacement
Follow the steps below to replace a needle valve's packing gland:
- Unscrew the valve's packing nut.
- Remove the packing gland and stem.
- If the needle valve has a large tipped stem, remove the packing washer, gasket, and anti-extrusion ring from the stem.
- If the needle valve has a small tipped stem, remove the packing from the valve body.
- Install the new packing in the valve body or on the stem if the valve has a large tipped stem.
- Replace the packing gland and stem.
- Use a wrench to tighten the packing gland to the tightness specified by the valve's manufacturer.
Disassembled valve inspection
During packing replacement, before reassembling the valve, use the opportunity to examine the following components inside the valve:
- Examine the wall to determine if there is a loss of wall thickness, which leads to decreased pressure capacity.
- Examine the valve bore, stem, and threaded connections for wear.
Needle valve lubrication
Valves are lubricated during production to ease assembly, improve the movement of components, and help preserve the valve if it is stored for a long period. However, if relubrication is necessary during the valve's lifetime, consult the valve's manufacturer. The specific lubricant required depends on the media flowing through the system and the system's temperature/pressure specifications.
FAQs
What is the function of a needle valve?
A needle valve precisely controls flow rates using a needle-shaped plunger. It can also function as a shut-off valve.
What are the advantages of needle valves?
Needle valves are small in size and take up less space in a system. They are also able to control the flow rates of relatively low flows.
Is a needle valve a shut-off valve?
Yes, a needle valve can be a reliable shut-off valve. It can also precisely control the flow of media.