Press Fittings - Working, Installation and Selection
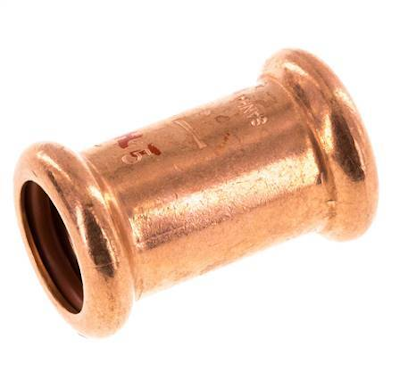
Figure 1: Straight press fitting made from copper alloy
A press fitting does not require heat treatment to join pipe or tubing; it only requires a specialized hydraulic press tool. This approach reduces the risks associated with high temperatures and allows for faster installation and a secure connection. This article discusses the design and selection criteria for press fittings and answers the common questions that a user may encounter.
Press fittings are ideal for use in situations where speed and safety are paramount, such as in residential plumbing, commercial buildings, and industrial applications. They are commonly used in systems that require quick installation and minimal downtime, including potable water lines, gas distribution, and HVAC systems.
Table of contents
- Press fitting design and working principle
- Advantages
- Disadvantages
- How press fitting works
- Selection criteria
- Press fitting vs soldering
- FAQs
View our online selection of press fittings!
Press fitting design and working principle
The design of a press fitting typically consists of two main components: the fitting body and the sealing element.
- Fitting body: The fitting body is the main body of the press fitting that connects to the pipe or tubing. Common materials are copper and stainless steel.
- Sealing element: The sealing element creates a watertight and leak-resistant seal.
Working principle
The sealing element is positioned within the fitting body. It acts as a barrier between the fitting and the pipe to prevent leakage. The o-ring compresses when the fitting is pressed onto the pipe using a hydraulic press tool, forming a secure and tight seal. This compression ensures the connection can withstand pressure and effectively prevents fluid leakage, enhancing the durability of the connection.
Advantages
Press fittings offer several advantages over traditional welding or soldering in some situations.
- Save time: Press fittings allow for quick connections, much faster than welding or soldering.
- Strong connections: Press fittings create secure joints. The connections are as strong as those made by welding or soldering.
- Improved safety: Press fittings enhance safety by eliminating the need for heat or flames, thereby reducing the risk of injury. Also, they require less safety gear.
- Versatile use: Press fittings are made of copper, stainless steel, and their alloys, making them suitable for many types of pipe systems, including gas, water, and steam.
- Easy repairs: Repairs can be done quickly, even if the pipes are wet, without shutting down the system. This is ideal for commercial and industrial settings where continuous operation is important.
Disadvantages
- Specialized tools and training: Press fit systems require specific tools, like a battery-powered hydraulic press and custom jaws or rings, for proper installation. Additionally, proper training is essential to avoid leaks, weak connections, or tool damage.
- Compatibility issues: Press fit tools and fittings are often specific to the material, requiring different jaws and rings for materials like copper, or stainless steel.
- Limited modifications after installation: Once a press fit connection is made, it is permanent and cannot be easily modified without cutting the pipe and installing a new fitting, which can be a drawback if adjustments are needed later.
How press fitting works
Press fittings create secure, leak-proof connections between pipes without the use of heat. This process utilizes a battery-powered hydraulic tool along with specialized jaws and rings designed for the specific material being used. Here is a step-by-step breakdown of how press fitting technology works:
- Cut: Begin by cutting the pipe to the desired length using a suitable cutting tool. Ensure the cut is straight and clean to provide an optimal surface for the fitting. A precise cut is crucial for maintaining the integrity of the connection.
- Deburr: Use a deburring tool to remove any sharp edges, burrs, or debris from the cut ends of the pipe, both inside and outside. This step is essential to prevent damage to the sealing element and to ensure a smooth, secure, and leak-free connection.
- Witness mark: Apply a witness mark on the pipe at the appropriate insertion depth. This mark serves as a visual guide to confirm that the pipe is fully inserted into the fitting during assembly.
- Assemble: Insert the pipe into the press fitting until it reaches the witness mark, ensuring it is fully aligned and seated. The fitting contains an o-ring, which will seal once the fitting is pressed.
- Press: Use the appropriate pressing tool, along with an adaptor jaw and collar for larger sizes, to securely press the fitting. This action crimps the metal sleeve tightly around the pipe, creating a strong, leak-proof connection. The press fitting uses an o-ring to create a watertight seal. This rubber seal is compressed onto the copper pipe, preventing leaks.
Selection criteria
1) Press fitting type
Choose the press fitting type based on the system requirements. A few examples are:
-
Reducing press fitting:
- Connects pipes of different diameters.
- Used in plumbing systems where a transition between different pipe sizes is needed, such as reducing the main supply line to smaller branch lines.
- Press fitting with male/female thread: Ideal for connecting press-fit systems to threaded fixtures or valves, commonly used in plumbing and heating systems.
-
Press fitting with inside press end:
- Designed to be pressed inside another fitting or pipe.
- Used in situations where a compact connection is required, often in tight spaces or when connecting to existing systems.
-
Elbow press fitting:
- Allows for a change in direction, typically 90 or 45 degrees.
- Used to navigate around obstacles or change the direction of piping in plumbing, heating, and cooling systems.
-
Tee press fitting:
- A T-shaped fitting that allows for the branching of a pipe into two directions.
- Commonly used in plumbing and heating systems to split a main line into two separate lines, facilitating distribution to different areas.
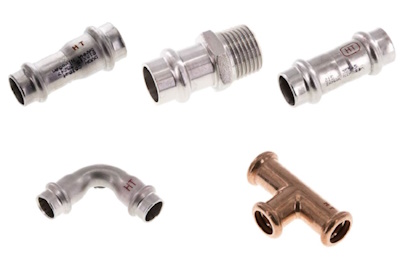
Figure 2: Press fitting types: Reducing press fitting (top left), press fitting with male thread (top middle), press fitting with inside press end (top right), 90-degree elbow press fitting (bottom left), and tee press fitting (bottom right)
2) Material
The fitting body is generally made of stainless steel or copper alloy.
- Stainless steel is ideal for corrosion resistance and strength in harsh environments.
- Copper alloy is preferred for excellent thermal and electrical conductivity in plumbing and heating systems. Copper alloy fittings are typically cheaper than stainless steel fittings of the same size.
The sealing ring is typically made from FKM.
3) Dimensions
The fitting's inner diameter (ID) is designed to accommodate the outer diameter (OD) of the tube it will connect to. This ensures a secure and leak-proof connection. Therefore, for a 20mm outer diameter tube, a press fitting with an inner diameter of 20mm is needed to ensure proper fit and sealing. The copper and stainless steel fittings are available in pipe diameters 15 - 54 mm and can be pressed using conventional die sets (i.e. Mapress, Viega, or SA).
4) Temperature and pressure
When choosing a press fitting, ensure it meets your system's pressure and temperature needs. Typically, most of the stainless steel fittings support up to 40 bar (580 psi) and operate between -20 to 200 š©C (-4 to 392 š©F). Copper fittings can operate only up to 16 bar (232 psi).
5) Additional features
Consider other features or specifications, like an integrated drain port. The drain feature enables the system to be emptied or flushed without disassembling the entire setup, which is particularly useful for repairs, maintenance, or winterization.
Press fitting vs soldering
Both press-fit and soldered fittings are common methods for joining copper pipes in plumbing systems, each with its own advantages and disadvantages.
- Cost: Press fittings require an expensive tool, whereas soldering does not.
- Skill level: Press fittings are easier to use and require less skill than soldering.
- Safety: Press fittings eliminate the risk of fire and exposure to fumes, which are concerns with soldering.
- Durability: Soldered joints use metal to seal, while press fittings rely on a rubber o-ring, which may raise concerns about long-term reliability.
Other considerations
While press fittings offer convenience and safety, some may prefer traditional soldering for its proven durability. Consider alternatives like push-fit fittings, which also use rubber seals but do not require expensive tools.
Read our articles on other fitting types like compression fittings, push-on fittings, and hose barb fittings for more details on the design and features of each type.
FAQs
What is a press fitting?
Press fittings are mechanical connectors for joining pipes in plumbing and piping systems without welding, creating a strong metal connection with a sealing element for watertight and airtight seals.
Which is better-copper press fitting or solder?
Copper press fittings allow for quick installation without flames or heat and work with various pipe types. Soldering can be cheaper for small projects but needs specific equipment and materials.
Are copper press fittings reliable?
Yes, copper press fittings are generally considered to be reliable. When installed correctly, they provide secure and leak-resistant connections.
What is the tolerance of a press fit?
Press fit tolerance refers to the allowable difference or gap between the fitting and the pipe that still ensures a proper and secure connection. It varies by manufacturer and fitting type.
What is interference in a press fit?
In press fittings, interference is the intentional dimensional difference between the fitting and the pipe, creating overlap or compression for a secure connection when pressed together.
How much interference does a press fit need?
The amount of interference required for a press fit typically ranges from 0.0254 to 0.1016 millimeters (0.001 to 0.004 inches).