Rotary Index Tables - How They Work
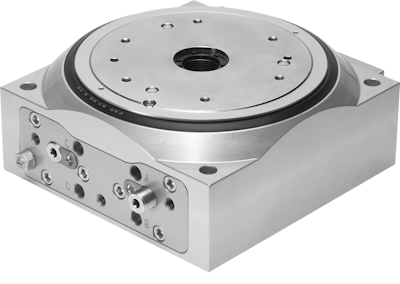
Figure 1: Festo DHTG rotary index table
A rotary index table is a mechanical device used to precisely position workpieces for machining or inspection by rotating them to specific angles. It enables accurate and repeatable positioning for operations such as drilling, milling, and quality control, enhancing efficiency and precision in manufacturing processes. These tables can be manually operated or integrated with CNC systems for automated control. They are widely used in industries like aerospace, automotive, and metalworking for producing complex parts with high precision.
Table of contents
- Rotary indexing table function
- Core components and design
- How does a rotary index table work
- Example
- General features of rotary index tables
- Applications
- Key selection criteria
- Festo rotary index table DHTG
- FAQs
Rotary indexing table function
The primary function of a rotary indexing table is to execute repeated angular displacements during a machine cycle, followed by a period of motionless dwell (dwell is the amount of time that the rotary index table remains in any particular position). This process allows for the precise positioning of parts at various workstations for machining, assembly, or inspection tasks. The dwell period is crucial as it provides the necessary time for operations to be performed on the part at each station before moving on to the next position.
Core components and design
Rotary indexing tables have motors, which can be powered by pneumatic, electric, hydraulic, or meanual means, tailored to the specific needs of the application.
- Pneumatic motors in rotary indexing tables are ideal for small to medium loads, utilizing pneumatic cylinders for rotation, with a pawl mechanism to lock the table in place during the return stroke.
- Electric motors offer speed and the capacity to handle heavier loads, making them suitable for tasks requiring high accuracy and repeatability.
- Hydraulic drives use pressurized fluid for powerful and smooth motion control, perfect for substantial loads.
- Manual rotary indexing tables can be adjusted by hand and are perfect for less frequent indexing needs, allowing adjustments by hand.
Mechanical power transmission devices transfer the power from the motors to the rotary table. Additionally, encoders, sensors, and controllers are integral for precise control and feedback on the table's position, enabling accurate and repeatable positioning.
Constructed around a circular steel plate, the table includes spindles, slots, or mounting holes for securing components, with fixed or adjustable indexing angles for task customization. Bearings support the table's rotation, maintaining load capacity and accuracy, with options like angular contact bearings, recirculating ball bearings, and cross-roller bearings available.
How does a rotary index table work
The operational mechanics of rotary indexing tables involve a base and rotating plate, where the base supports the rotating plate that holds the workpiece. The rotation is controlled by an indexing mechanism, which stops the table at predetermined intervals for operations at each station.
The drive system powers this rotation, which can be manual or motorized, with the latter being common in automated setups. A locking mechanism ensures stability by securing the table in place once it reaches the desired position, preventing any movement that could compromise precision.
In automated rotary indexing tables, a control system dictates rotation speed, angle, and dwell time at each position, allowing for complex operations with minimal human intervention. This system uses the feedback from encoders and sensors to manage the operation of motors and other components efficiently.
Integration and flexibility
The placement of drive mechanisms can vary, positioned above, below, behind, or to the side of the table surface, offering design flexibility to accommodate different spatial constraints and operational configurations. This ensures seamless integration into a broad range of industrial settings.
Example
Consider the manufacturing of a car's gearbox. The gearbox has multiple holes that need to be drilled and tapped (threads created inside the holes) at various angles around a cylindrical part. This process requires high precision to ensure that the holes are correctly positioned and angled for the gearbox to function properly.
Traditional method
Without a rotary index table, an operator would manually position and secure the part, drill one hole, then unclamp the part, rotate it to the next position, re-clamp it, and drill the next hole. This process is not only time-consuming but also prone to errors in alignment and positioning, leading to potential defects in the gearbox.
Using a rotary index table
The cylindrical part of the gearbox is secured onto the rotary index table. The table is programmed or set up to rotate the part to the exact angles needed for each hole. Here's how it simplifies the process:
- Setup: The part is clamped onto the rotary index table. The drilling and tapping tools are positioned above the table.
- Operation start: The operator starts the process, or if it's automated, the control system initiates the sequence.
- Drilling the first hole: The table is in its starting position. The drill comes down, drills the hole, and then retracts. The tapping tool follows, creating the threads inside the newly drilled hole.
- Indexing to the next position: The rotary index table then rotates the part to the next predetermined angle. The precision of the table ensures that the part is positioned accurately for the next hole.
- Repeating the process: The drilling and tapping process repeats for each hole, with the rotary index table rotating the part to each required position. The operator does not need to manually reposition the part, saving time and reducing the risk of errors.
- Completion: Once all holes are drilled and tapped, the part is unclamped from the table and inspected. The precision of the rotary index table ensures that all holes are correctly positioned and angled, meeting the strict specifications required for the gearbox to function correctly.
General features of rotary index tables
Rotary indexing tables have various features that enhance their functionality and adaptability to different applications:
- Adjustable table surfaces: Some tables offer surfaces that can be raised or lowered at a controlled angle, providing flexibility for complex machining or assembly tasks.
- Multiple rotating work surfaces: Tables with more than one rotating work surface allow for simultaneous processing of multiple parts, increasing efficiency.
- Computer numerically controlled (CNC) devices: CNC technology offers greater accuracy and repeatability, making it ideal for applications requiring precise movements and positioning.
- Rotary encoders: Used to relay the precise position of the table surface, rotary encoders are essential for applications where exact positioning is critical.
- Four-axis and five-axis tables: Four-axis tables enable movement along the X, Y, and Z linear axes plus rotation around the X-axis, facilitating complex machining tasks with a single setup. Five-axis tables add rotation around the Y-axis, allowing for even more intricate part geometries by enabling the workpiece to be positioned at almost any angle.
Applications
Rotary indexing tables are utilized across a broad spectrum of applications:
- Assembly: Streamlining the assembly process by accurately positioning parts for assembly operations.
- Equipment positioning: Precisely positioning equipment for optimal operation and efficiency.
- Automation: Enhancing automated processes by providing reliable and precise positioning.
- Inspection: Facilitating detailed inspection processes through precise part positioning.
- Machining: Improving machining accuracy and efficiency with precise positioning of workpieces.
These tables are particularly effective in environments requiring fast and straightforward vertical operations. They are commonly used in:
- Industrial presses
- Screwdrivers
- Riveters
- Dispensers
- Pick-and-place units
- Ultrasonic or resistance welders
Key selection criteria
When selecting a rotary indexing table, several important parameters must be considered:
- Maximum indexing increment: This specification refers to the smallest angle by which the table can rotate. It's essential for applications requiring high precision, as it determines the table's ability to position parts accurately.
- Work table diameter: The size of the work table is critical, as it must be large enough to accommodate the parts or assemblies being worked on. The diameter can vary significantly depending on the model and intended use.
- Maximum axial load: This is the maximum load that can be applied along the table's axis without causing damage or reducing performance. It's important for ensuring the table can handle the weight of the parts and any forces exerted during processing.
- Maximum radial load: Similar to the axial load, this specification indicates the maximum load that can be applied perpendicular to the table's axis. It's crucial for applications where forces are exerted sideways on the table.
- Resolution: This refers to the smallest increment the table can move or measure, which is critical for applications requiring high precision.
- Repeatability and accuracy: These parameters determine how consistently the table can return to a specific position and how close the actual position is to the intended position, respectively.
- Mechanical parameters: Factors such as backlash or hysteresis can affect the precision of movements.
- Loading: The table must be capable of handling the specific torque, axial loads, radial loads, and moment loads of the application, which influences the type and size of the indexer used.
Festo rotary index table DHTG
The Festo rotary indexing table DHTG (Figure 1) is designed for precision positioning tasks such as swiveling or separating, featuring robust mechanics and user-friendly operation. Key features include:
- Variable indexing and reversible rotation: Offers flexibility in operation with the ability to choose indexing angles and reverse the direction of rotation as needed.
- Sturdy mechanical system: Ensures durability and reliability even in demanding industrial environments.
- Easy planning and commissioning: Designed for straightforward integration into existing systems, simplifying setup and maintenance.
- Multiple diameter options: Available in diameters of 65, 90, 140, and 220 mm, accommodating a range of applications.
- Free control of rotational direction: Enhances operational flexibility, allowing for precise control over the movement.
- Integrated functions: Includes overload protection to prevent damage, sensor functions for monitoring, cushioning adjustment for smooth operation, speed setting for control over operation speed, and the ability to change the direction of rotation, all contributing to a versatile and efficient performance.
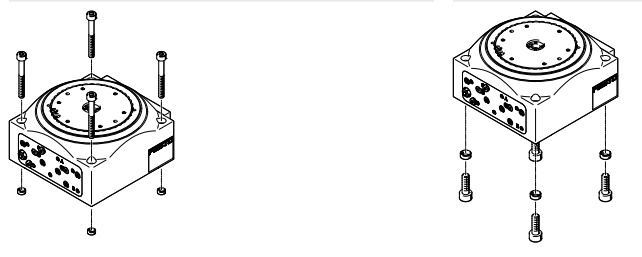
Figure 2: Festo rotary index table mounting options: Direct mounting from above (left) and below (right) respectively
Port connections
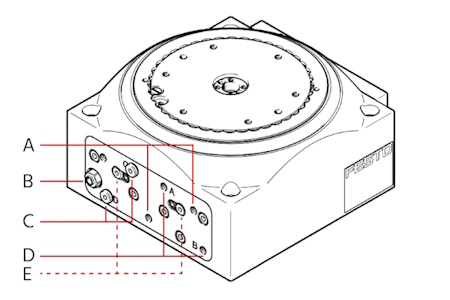
Figure 3: Festo rotary index table connections: thread for position sensing (A), one-way flow control valve (B), compressed air supply (C & D), and adjusting screw for cushioning adjustment (E)
The technology combines mechanical and pneumatic elements to control motion in automated systems (Figure 3):
- Thread for position sensing (A): Enables precise detection of part positions, crucial for accuracy in automated tasks.
- One-way flow control valve (B): Regulates the speed of pneumatic actuators by controlling air flow, allowing for precise speed adjustments.
- Compressed air supply port for reciprocating motion (C): Supplies air for back-and-forth motion, used in various industrial applications.
- Compressed air supply port for rotation (D): Allows air supply for controlled rotational movement in both directions, adding versatility.
- Adjusting screw for cushioning adjustment (E): Manages cushioning at the end of movements, reducing wear and ensuring smoother operation.
Operating mode | Valve requirement | Additional requirements | Description | Representation |
Clockwise rotation | One valve | None | Rotates the system in a clockwise direction. | ![]() |
Anticlockwise rotation | One valve | None | Rotates the system in an anticlockwise direction. | ![]() |
Reciprocating motion | Two valves | Reciprocating motion kit | Moves the system back and forth in a linear path. | ![]() |
Variable actuation (All Modes) | Two valves | Reciprocating motion kit | Allows the system to switch between clockwise, anticlockwise, and reciprocating motions. | ![]() |
Note: Festo rotary indexing tables are not designed for use in environments with machining, aggressive media, grinding dust, or welding spatter.
FAQs
What are the differences between rotary table and index table?
A rotary table rotates continuously, while an index table moves in discrete steps for precise positioning.
What are the advantages of rotary indexing?
Rotary indexing provides precise positioning, faster operation, and increased efficiency in automated processes.
What are programmable rotary index tables?
Programmable rotary index tables are advanced mechanical devices that can be programmed to rotate to any number of positions around a circle, allowing for precise and variable positioning of workpieces.