Roller Bearing Guide
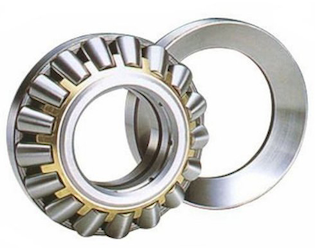
Figure1: Spherical roller bearing
Bearings come in handy in various industrial instances and enable individuals to carry heavy loads with little friction. Advancements in technology have produced precise roller bearings. These quality bearings provide an excellent balance between cost, size, load-carrying capacity, accuracy, longevity, and weight.
Table of Contents
- What are roller bearings?
- Why use roller bearings?
- How do roller-element bearings work?
- Configurations of roller bearings
- Types of roller bearings
- Bearing failure and lifespan calculation models
- Roller bearing selection criteria
- Applications of rolling bearing
- FAQs
View our online selection of bearings!
What are roller bearings?
Also known as roller-element bearings, roller bearings work under the same principle as ball bearings and serve one primary function: carrying loads with minimum friction. The difference between ball and roller bearings is shape and construction. The former use balls, while the latter use cylinders, such as cross roller bearings and linear roller bearings.
Roller-element bearings contain single or double rows of rollers. For instance, double-row roller bearings significantly improve radial load-carrying. Besides, the utility of these bearings in various shapes and sizes allow for transmissions of both radial and axial loads with reduced friction.
Single-row vs. double-row roller bearings
Single-row rollers have one row of rolling elements. They have a simple, non-separable design and angular roller bearings that can only handle axial loads in one direction. The main advantage of single-row bearings is that they are an excellent option for high-speed applications. The rolling body load action line and the radial load action line are usually not on the same radial plane. Therefore, single-row rollers must be mounted in pairs when subjected to pure radial load.
On the other hand, double-row rollers have two rows of rolling elements. They can carry bidirectional radial and axial loads. However, they can restrict the axial displacement of the shaft and the casing within the bearing's axial clearance. Compared to single-row angular contact bearings, double-row angular contact bearings provide improved rigidity enabling them to endure overturning moments or tilting effects. Besides their enhanced rigidity, other advantages of double-row bearings include high load capacity and compactness.
Why use roller bearings?
The primary reason for using roller bearings is to reduce friction for effortless applications. As a result, they produce less heat during operation and alleviate the need for repetitive lubrication. Other advantages of using roller-element bearings include:
- Reduces maintenance and servicing costs
- Separable design, enabling for straightforward mounting and dismounting
- Interchangeable procedure – users can easily exchange the inner ring
- Bearings can facilitate change in direction without technical modifications
- Allows for axial displacement
How do roller-element bearings work?
To appreciate how roller-element bearings function, first, it would be best to understand their design. A bearing may contain balls, ball rollers, tapered rollers, or needle rollers. They feature an inner and outer ring with raceways for the caged parts. They also include a lubricant to reduce friction and seals to prevent the entry of particles that might contaminate the oil.
The pockets within the cages separate the rolling elements and maintain constant spacing as the apparatuses roll in the race tracks. As aforementioned, roller bearings come in different configurations, including single- and double-row elements.
The cylinders between the inner and outer races enable the caged elements to roll in the raceways along a single axis. The rolling elements would slide out of position under operation without the cages, causing bearing failure. The cages don't handle any loads, and their purpose is to hold the rollers in place. There are also cage-free bearings called full complementary bearings (FCB). Usually, FCBs have more rolling elements, handling heavier loads. Another upside is that they can withstand sudden shock loads as the rollers evenly distribute the load throughout the raceway.
There's also a need to lubricate roller bearings. Whether or not to grease depends on the product you buy. Sealed roller bearings typically come pre-lubricated, and no additional greasing is required. Non-sealed ones need a lubrication plan called elastohydrodynamic lubrication and must adhere to the manufacturer's specifications.
In this greasing regimen, a lubricant, usually less than one micron, is applied with pressure levels reaching up to 34,500 bar (500,000 psi). The grease partially solidifies and elastically deforms the rolling elements and the contact surface. Any contamination of the oil can lead to significant degradation of the mating surface and can result in the build-up of more wear particles.
Configurations of roller bearings
Based on specific requirements, such as load directions and stiffness, a roller bearing may consist of one or two rows of rolling elements. The bearing configuration supports and directs the shaft or load radially or axially relative to other components like casings. Two support blocks, either mounted on both ends or intermittent, must clamp the shaft without using bolts.
Two-bearing-support rollers are the most commonly used and might have one of the following three arrangements:
- Locating or non-locating bearing configuration
- Adjusted bearing configuration
- Floating bearing configuration
Locating and non-locating bearing configuration
In a locating configuration, the bearing support touches the shaft axially. On the other hand, a non-locating bearing arrangement provides axial displacements due to the difference in thermal expansion or strain between the shaft and the housing. Furthermore, it offers higher component tolerance, affecting the distance between the bearings.
Adjusted bearing configuration
In an adjusted bearing configuration, the shaft moves back and forth; one bearing support allows for positive displacement while the other (cross-located) enables shaft location in the opposite direction. Users must first adjust the clearance when mounting the component. Examples of roller bearings with such a configuration are the tapered roller bearings (discussed below).
Floating bearing configuration
In a floating arrangement, cross-located bearing and the contact components freely move axially or radially over varied distances between the two endpoints. The difference in thermal expansion between the shaft and housing and the component's tolerances determines the floating distance. Spherical and deep-grooved bearings are examples of roller-element bearings with a floating configuration.
Types of roller bearings
There are many roller bearings in consumer markets used in various application requirements. Some of the common roller bearing types include:
Spherical roller bearings
The spherical bearing comprises an inner ring with two racetracks inclined at the angle of the bearing axis, an outer ring with a common spherical raceway, spherical rolling elements, cages, and, in some designs, internal center rings.
Their construction enables them to carry heavy axial and radial loads in any direction at high speeds, even with bearing misalignment or shaft deflection. Spherical rolling bearings are versatile and come with cylindrical or tapered bores ranging from 20 mm – 900 mm, allowing users to install them with or without a sleeve adapter.
Cylindrical roller bearings
These bearings feature cylindrical-shaped rollers in linear contact with the raceways but are not true cylinders. Instead, they have crowned or floating ends to relieve stress. You can find them in single- or double-row configurations. Still, regardless of your choice, their geometry gives them greater radial load capacity in high-speed applications. Nonetheless, they have moderate thrust load capacity.
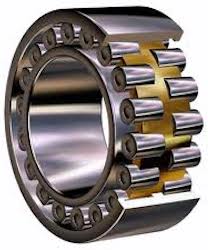
Figure 2: Cylindrical roller bearing
Tapered roller bearings
Taper rollers are designed under the principle that cones can roll over each other without slipping. They contain an inner and outer ring and rows of non-separable cone assemblies. Conical tapered roller bearings run on conical raceways corresponding to the bearings' tapered design. Due to their sizeable surface-area contact, tapered rollers can withstand heavy radial, axial, and thrust loads, usually in moderate-speed applications.
They closely resemble cylindrical bearings, but if you decide which one to purchase, here's the main difference: cylindrical roller bearings only handle limited thrust loads. At the same time, their tapered counterparts can manage significant thrust loads. Tapered roller bearings are usually available in inch and metric sizes.
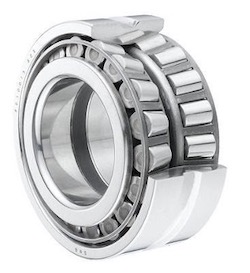
Figure 3: Tapered roller bearing
Needle roller bearings
These rollers feature thin and long bearings positioned horizontally in the bearing casing. They may have tapered ends to maintain the roller position or hemispherical ends for free bearing movement. Needle bearings are a variant of cylindrical bearings. Their cup-style designs enable them to withstand high radial load capacities in applications requiring high-speed rotational accuracy.
The primary advantage of needle rollers is their ability to use the mating surface as inner or outer raceways, or both. The construction also provides large oil reservoirs while maintaining a minimalistic cross-section design. You'll find needle rollers with or without an inner ring.
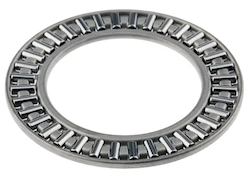
Figure 4: Needle roller bearings
Thrust roller bearing
Thrust bearings are specific rotary bearings used to handle high loads in hostile environments. They may feature various rolling elements, including needles, tapered, spherical, or cylindrical rollers, which divide the bearing rings. Thrust rollers handle axial and thrust loads parallel to the shaft's axis. Their speed rating varies based on the rolling element used. For instance, ball roller thrust bearings are excellent for high-speed applications, but cylindrical roller thrust bearings are limited to moderate speeds.
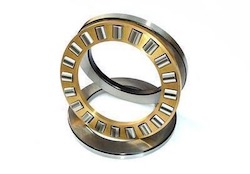
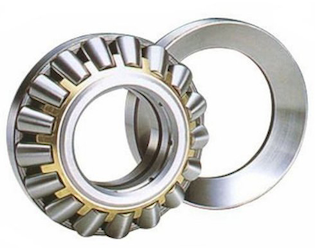
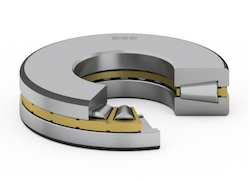
Figure 5: Thrust roller bearing (left), spherical thrust bearing (middle), and thrust tapered bearing (right)
Bearing failure and lifespan calculation models
Approximately 10 billion bearings are rolled out by manufacturers every year globally. Ninety percent of them outlive the machinery in which they are installed. Only 0.5% or 50,000,000 get replaced due to failure or damage.
Roller bearings get damaged or fail due to various reasons, which include:
- Fatigue
- Poor lubrication regimen or practices
- Contamination because of poor seals
- Improper handling, installation, and maintenance
- Utility in heavier loads or different loading than specified
The frequency and extent of damage vary from industry and application. For example, roller bearings fail in the pulp and paper industry due to contamination and poor lubrication, not fatigue.
These events usually leave a damaging imprint within the bearing raceways called path pattern damage. Examining the component enables users to determine the root cause of the damage. Consequently, they can use a bearing puller to take the bearing from the shaft, examine it, and take corrective action to ensure the problem doesn't recur.
Take, for instance, the case of contamination due to ineffective seals. Particles get lodged in the bearing pockets along the raceways. Continued over-rolling can cause sharp indentations in the race tracks. When normal functioning stresses the indented areas, it results in surface fatigue. The metal casings start breaking away from the raceways - a process called spalling. If users do not address the damage, spalling continues until the bearing becomes unserviceable.
Lifespan calculation model
Users can calculate the longevity of roller bearings using a formula called bearing dynamic capacity, C. It refers to the standard stationary radial load that a rolling-element bearing can withstand a life rating of a million cyclic revolutions.
Industrialists use bearing dynamic capacity to project the lifespan rating at specific load and rolling speeds. Manufacturers recommend subjecting a roller bearing to a maximum working load half the bearing capacity. The International Organization for Standardization (ISO) and the American Bearing Manufacturers Association (ABMA) define the calculation methods, which usually consider the raceways' internal dimensions and the rolling elements.
Bearing rating lifespan calculation
"Rating Life" is the bearing durability calculated for 90% reliability. It is defined as the amount of time that a group of identical rollers will complete before they develop fatigue spalls. The basic calculation formula for determining the bearing (L10) rating life is as follows:
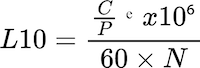
Where:
- C – Dynamic capacity (dN or Lbs.)
- P – Equivalent bearing load (N or Lbs.)
- N – Rotational speed (RPM)
- E – 10/3 (3.0 for ball bearings)
Roller bearing selection criteria
Although roller bearings are standardized components, the selection criteria for the correct bearing can only be established to a limited extent, usually based on the application requirements. Still, buyers must consider one of the main dimensions of the bearing, typically the bore diameter, based on the overall design and construction.
Today, computerization of the design process enables manufacturers to create bearings with optimal dimensions. That technology also aids consumers in picking suitable components for use in various pieces of machinery.
When searching for the suitable bearing for use in specific applications, project managers and designers should focus on the following factors:
- Load type and volume
- Mounting requirements – installation space and style of lubrication
- The bearing's functional lifespan
- The bearing's operating parameters (speed and thermal conditions)
- Accuracy requirements
- Maintenance and servicing
- Ambient conditions (vibrations, dirt, etc.)
- Requirements for assembly and disassembly
Applications of rolling bearing
Since there are different types of rolling bearings with different configurations, these components provide various properties, such as performance, speed, accuracy, and load capacity, at varying levels. Hence, they are fitted in various equipment and machinery in different industrial sectors. Examples of widely used applications of rolling bearings include:
- Aviation cargo systems
- Heavy-duty rotating equipment and machinery
- Automobile sector
- Medical equipment
- Power generation in hydroelectric power-plant turbines
- Solar panels
- Agricultural industry
- Pulp and paper manufacturing
- Petroleum refinement
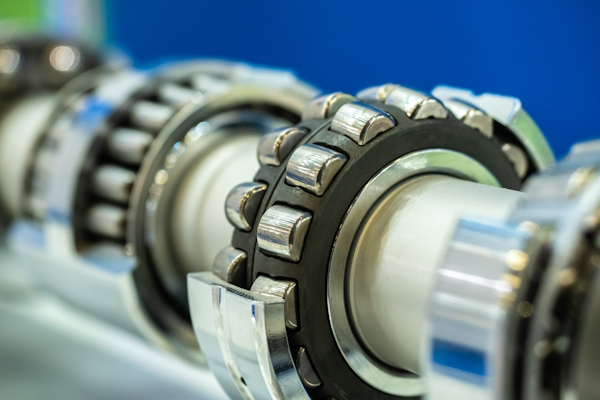
Figure 6: Roller bearings on a shaft
FAQs
Can roller bearings be refurbished?
Yes, but it depends. It's not economical to refurbish small bearings. However, larger ones with bore diameters above 6-inches can be refurbished with economic benefits.
How can I ensure I choose the right roller bearing for my application?
Manufacturers recommend consulting a bearing application engineer to maximize performance and ensure project success when choosing your design specifications.
Can stainless steel bearing prevent corrosion?
To a certain extent, stainless steel is not rust-proof but corrosion-resistant. That means it will rust in corrosive conditions but much slower than chrome alloy steel.
What is a cam roller bearing?
A cam roller bearing is a type of roller bearing with an outer ring that has been modified to include guide flanges. It is utilized in cam and follower applications to support high radial loads.
What is a caged roller bearing?
This is a roller bearing with a cage between the rollers to reduce friction, hold the rollers, and maintain them consistently spaced. It is designed to withstand modest radial and axial loads.