The Fundamentals of Tribology Part 2: An In-Depth Look At Lubrication
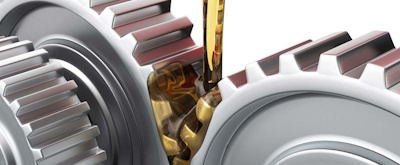
Figure 1: Lubrication
Lubrication plays a huge role in classical tribology. Not only does it protect from corrosion, helps to control temperatures in applications, and provides excellent sealing capabilities that protects equipment from damage. Most importantly, lubricants provide significant cost savings. By reducing wear and friction, they prevent or minimize surface damage such as surface fatigue, abrasion, adhesion, and tribochemical reactions. Lubricants, when chosen and applied correctly, extend the working life of machinery and save the end user money.
Lubricants offer this protection by forming a film between two surfaces that reduces friction. It doesn't necessarily have to be a liquid lubricant. Lubricants can be a solid, dry compound, a fluid such as oil but also water, a semi-solid such as grease, or even plastics and silicones.
In this three-part series we will look at three main parts of tribology and the application of tribology in mechanics:
- Part 1: The basics of tribosystems
- Part 2: An in-depth look at lubrication
- Part 3: Standards, testing, and classification in tribology
Note: Currently we do not sell any lubricants.
The function of lubricants in tribology
As late as the early 20th century, lubrication was done primarily with mineral oils, vegetable oils, and animal oils. Since then, the industry has made huge steps towards a vast selection of different lubricating agents, while the technology involved with these lubricants has changed significantly as well.
The Stribeck curve
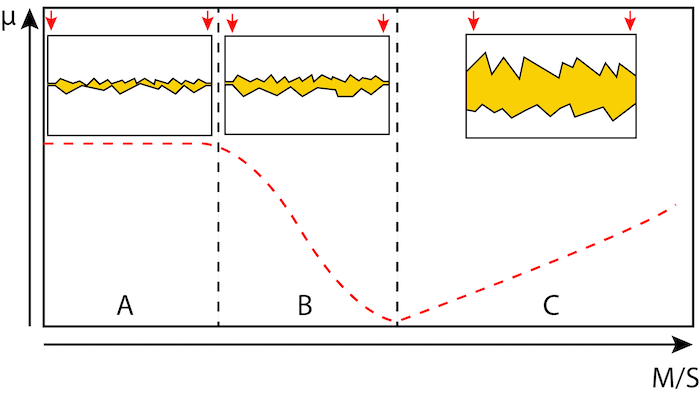
Figure 2: The stribeck curve
The Stribeck curve shows how friction (μ) changes with increasing speed (m/s). By using this we can identify three different lubrication regimes:
- Boundary lubrication (Figure 2 labeled A): Direct contact between solid surfaces, loads carried mainly by surface asperities, high friction.
- Mixed lubrication (Figure 2 labeled B): Some asperity contact, with the load carried by both asperities and the lubricant.
- Full film lubrication (Figure 2 labeled C): Very little asperity contact, load supported by hydrodynamic pressure.
Boundary lubrication
In simplest terms, boundary lubrication is the lubrication of surfaces by very thin fluid films, such that friction coefficients are affected by both the type of lubricant and the surface characteristics. In high-load and low-speed conditions, boundary lubrication is typically experienced by bearings, gears, piston rings, pumps, and transmissions. It results in a thin film varying in thickness from one to a few tens of nanometers between the rolling and sliding bodies.
Tribology considers boundary lubrication a crucial factor since friction is at its highest level during this process. Lubricants with the appropriate viscosity can help prevent boundary lubrication. When the lubricant has too little viscosity, it will not be able to keep the materials apart, resulting in high friction and wear. In contrast, using a lubricant with too high viscosity will increase friction, temperatures will rise, and layers of oil will slide past each other as a result of internal oil shearing.
In spite of that, boundary lubrication certainly has its place. It plays a significant role in minimizing chemical and adhesive wear. Boundary lubrication is also commonly used in low-speed, low-cost conditions such as door hinges.
Mixed lubrication
Mixed lubrication is often seen as an intermediary stage between boundary lubrication and full film lubrication (either elastohydrodynamic or hydrodynamic). During boundary lubrication the friction coefficient reduces dramatically once the sliding speed increases. This reduces the amount of contact between sliding surfaces and friction drops to a point which is known as mixed lubrication.
As the name suggests, metal on metal sliding still involves abrasive loading during mixed lubrication, while some loading also occurs on the lubricant. As the thickness of the lubricating film increases the regime moves towards elastohydrodynamic or hydrodynamic lubrication, also known as full film lubrication.
Full film lubrication
Full film lubrication consists of two different types of lubrication regimes, either hydrodynamic lubrication, or elastohydrodynamic lubrication.
Hydrodynamic lubrication:
This regime happens when a working clearance is created and supported by a full film of lubricant, for example between a rotating shaft and bearing. During operations the oil will lift the shaft off the bearing surface, ensuring there is little risk of wear. Hydrodynamic lubrication can be compared to hydroplaning in a car. A low viscosity media, water in this case, supports the full weight of a car due to the speed the car is traveling at.
For hydrodynamic lubrication to be fully successful, the sliding parts must be geometrically similar, and a low contact pressure should be maintained between the surfaces. The only notable friction that occurs during hydrodynamic lubrication comes from the friction within the oil itself. However, this regime does require that the oil's viscosity can maintain a hydrodynamic condition in all operating conditions. If the clearances are reduced too much, for example switching from high speed and high load, to low speed and high load, the sliding materials could touch, causing friction and wear.
Elastohydrodynamic lubrication
Elastohydrodynamic lubrication (EHL) works in a broadly similar fashion as hydrodynamic lubrication. However, under EHL the film is under extreme pressure which elastically deforms the counter rolling surfaces. Surfaces deform at a rate comparable to the thickness of the film separating them, measured in micrometers.
The discovery of elastohydrodynamic lubrication marked a major milestone in both tribology and the design and performance of machine elements. This regime is often used on mechanical elements such as ball bearings, gears, and cam shafts. Elastohydrodynamic lubrication is considered to be an enhancement of Hydrodynamic lubrication due to the surface elastic deformation and lubricant viscosity increase caused by high pressure.
In this three-part series we look at three main parts of tribology and the application of tribology in mechanics: