The Fundamentals of Tribology Part 3: Terms, Standards, and Testing in Tribology
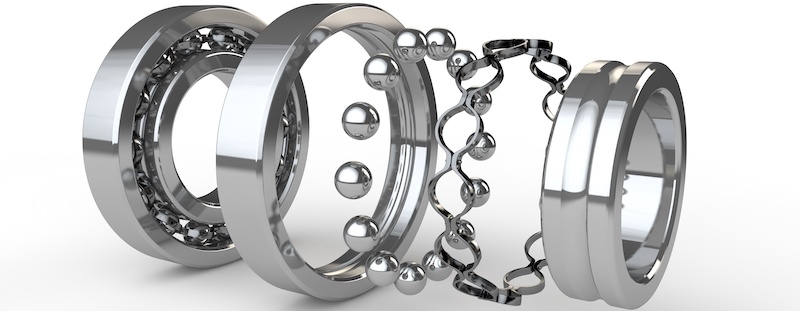
Figure 1: The design and maintenance of bearings is heavily influenced by tribology.
Over time, numerous testing methods and standards have been developed to understand which variables influence a tribological system. Understanding these variables help producers develop lubricants in a meaningful way that will allow them to assign the lubricant to a specific application such as bearings, gear systems, pumps, and more.
The article explores the testing methods used to determine the suitability of a lubricant for an application. We also cover a range of terminology used often in tribology that will help understand the various factors that come into play when working with tribological systems.
This is the third part of a three-part series where we look at three main parts of tribology and the application of tribology in mechanics:
- Part 1: The basics of tribosystems
- Part 2: An in-depth look at lubrication
- Part 3: Standards, testing, and classification in tribology
Note: Currently we do not sell any lubricants.
Table of contents
Test methods and standards
In order to ensure the quality and usability of a lubricant, various tests can be performed. These check how the physical and chemical properties of the lubricant respond to different influencing factors. The obtained data is used to determine the suitable application of the lubricant.
Viscosity testing
The viscosity of an oil is determined with different measuring instruments depending on the type of product. A falling-ball viscometer is used to fulfil the specifications to DIN 51562-1 or similar methods. The specification of the kinematic viscosity V (ny) [mm2 /s] is effected at +40°C. The value, for example at +100°C, is often also of interest, so that the drop in the viscosity at higher temperatures can also be assessed.
Flash Point Test
Essentially, the flashpoint refers to the lowest temperature at which enough flammable vapor will ignite upon contact with an ignition source. Combustible liquids can be assessed for fire danger using this method. The most common measurement methods depend on the type of product and the height of the flashing point. Two tests are available, closed crucibles (according to DIN ISO 2592) or open crucibles (according to ISO 1523:2002), also known as the open cup or closed cup tests. This test is important in Tribology as high friction will usually cause extreme heat development.
Thread friction test
A screw test bench is used to determine thread friction. ISO 16047 defines the coefficient of friction of a screwed connection as the force exerted when screws and nuts are tightened. The test will be influenced by the thread dimension, the material, and the surface type. Lubrication and coatings are also likely to affect the tribological characteristics of threaded joints. As such, a benchmark would be set and the influence of the various parameters can be measured.
Condensed water test & salt spray test
One of the most important tests, especially for metal components in applications, is how these are affected by corrosion. Lubrication offers a high degree of protection against corrosion, how much is determined with the condensed water test and the salt spray test. Both tests are aimed at seeing how long it takes before a component shows traces of corrosion. The condensed water test is defined in DIN 50017, the salt spray test is defined by ISO 9227.
In the condensed water test, moist air is condensed on the surface of a wet or dry lubricated test piece under defined ambient conditions in a protected environment. A specified period of time is required for condensed water exposure. As a result of these tests, precise conclusions can be drawn regarding the behavior and performance of corrosion protection. These tests can also identify any defects within a coating.
Salt spray tests are conducted under similar conditions. A salty climate is simulated by this test, wherein coated plates are exposed to a defined salt spray according to ISO 9227. A check is carried out after how many hours traces of rust arise and how much protection the lubricant offers against corrosion.
Consistency testing
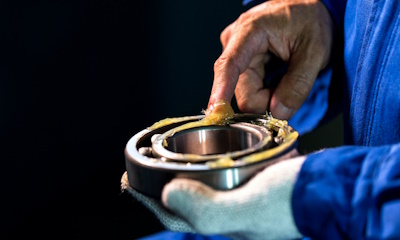
Figure 2: Soft lubricants are used on various kinds of bearings such as plain bearings, roller bearings, and ball bearings.
Penetrometers measure the consistency of lubricating grease in accordance with ISO 2137, where the grease is worked before measuring in order to simulate bearing stress. Based on the amount of penetration depth of a cone, the consistency class can be assigned according to DIN 51818. Classes range from very soft (Class 000) to very firm (Class 6). Refer to the following table:
NLGI grade | Worked penetration (1/10 mm) | Grease type | Application |
---|---|---|---|
000 | 445-475 | Fluid grease & oils | Centralised lubrication systems, Gear lubrication systems |
00 | 400-430 | Fluid greases & oils | Centralised lubrication systems, Gear lubrication systems |
0 | 355-385 | Fluid greases | Centralised lubrication systems, Gear lubrication systems |
1 | 310-340 | Soft greases | plain bearings, rolling bearings, water pumps |
2 | 265-295 | Soft greases | plain bearings, rolling bearings, water pumps |
3 | 220-250 | Soft greases | plain bearings, rolling bearings, water pumps |
4 | 175-205 | Soft greases | plain bearings, rolling bearings, water pumps |
5 | 130-160 | Hard greases | Sealings greases, blocking greases |
6 | 85-115 | Hard greases | Sealings greases, blocking greases |
Breakaway behavior test
This test is performed mainly for fastener and screw pastes used in high temperature applications. A fastener is lubricated and tightened to either 40 or 70 Newton meters. After this the fastener is subjected to temperatures between 200°C (392°F) and 650°C (1202°F)for 100 hours. The amount of loosening torque needed is compared to the tightening torque which determines the breakaway behaviour.
Pour point test
A lubricant's pour point is measured through parameters laid out in DIN ISO 3016. This method involves heating the sample up and then cooling at a specified rate. The flow characteristics of the sample are examined at intervals of 3°C (37°F). The pour point is the lowest temperature at which movement ('pour' or 'flow') of a sample is observed. Tests like this are particularly valuable for lubrication performed in cold storage areas, cold climates, etc.
Press-fit-test
A Press-fit test examines how solid lubricants behave and adhere under very high pressure and low sliding speeds. This test measures the coefficient of friction and determines whether stick-slipping occurs. This is crucial for mounting work (e.g. presses), as well as slideways and guides (e.g. machine tools).
Drop point testing
The dropping point of a lubricating grease is defined as the temperature at which the grease passes from a semisolid state to a liquid state when tested under the conditions defined by ISO 2176. In greases that contain conventional soaps as thickeners, this is the typical change in state. Grease containing thickeners other than conventional soaps may not liquefy, meaning they lack a drop point. The drop point is above the recommended maximum operating temperature.
Four-ball rig testing
The four-ball test rig is a lubricant testing device that is used for high surface pressures in the mixed friction range. According to ISO 20623, the four-ball test rig consists of a rotating moving ball that slides on three balls fixed into place.
When testing for the lubricant's maximum load-bearing capacity, a test force acts on the moving ball, which is increased in steps until the four-ball system is welded together as a result of the friction heat produced. The test is designed to test the maximum load bearing capacity of a lubricant.
Tribological linear-oscillation test
The test methods described in the ISO 19291 international standard are based on a linear-oscillation test machine. It determines tribological quantities like load carrying capacity, wear, friction, and extreme pressure behavior of oils and greases in ball-on-disc contact geometries such as ball bearings.
Anti-corrosive coating thickness test
Coating thickness is measured by rotating a ball at a preset speed on a single spot for a predetermined period of time, which erodes the coating. The radius is then examined under a microscope to determine the depth of penetration, thus determining the coating thickness. Values like these are quite important since they determine the lifetime of corrosion protection.Important tribology terminology
The table below terms that find their origins in tribology and lubrication.
Additives | Lubricants utilize additives to improve specific properties, like anti-corrosion properties. |
Aging | Refers to the change of the substances at a chemical level. Operating time, light, medium air, heat, etc. are factors that cause aging. |
Boundary lubrication | Lubrication between two rubbing surfaces that does not involve the formation of a full-fluid lubricating film. |
Bright stock | This heavy residual lubricant stock has a low pour point and is used in finished blends to provide good bearing film strength, to prevent scuffing, and to reduce oil consumption. |
Brookfield viscosity | Basis for ASTM Method D 2983; used for measuring low temperature viscosity of lubricants. Calculates the torque required to rotate a spindle at a constant speed in oil at a given temperature. |
Centralized lubrication | Lubrication via a central location that supplies a metered amount of lubricant. |
Circulating lubrication | A lubrication method involving a pump that recirculates the lubricant. |
Degradation | It is the gradual loss of performance of a machine or lubricant. |
Detergent | An additive or a compounded lubricant that keeps insoluble materials suspended, preventing their deposition where they would cause harm. |
Elastohydrodynamic lubrication | It is common for tribological interfaces to be subjected to very high loads and pressures. As a result, the bodies themselves deform elastically, which facilitates sliding at lubricated interfaces. Film thickness results both from elastic deformation of the bodies and from the hydrodynamic flow of the fluid. |
Evaporation loss | Resulted from exposing oil to high temperatures for a specified duration of time. Oil should evaporate as little as possible proportionally to its weight. |
Emergency lubrication | Solid lubricants are used when oil and grease do not provide adequate lubrication. |
EP lubricants | These lubricants are designed to withstand high pressures and wear. They are manufactured with specific additives. |
Extreme pressure (EP) additive | Additive that allows sliding metal surfaces to remain lubricated under extreme pressure. They are made from reactive compounds of sulfur, chlorine, or phosphorus. |
Friction | In simple terms, friction is resistance to motion. Materials, geometries and surface features of bodies in contact determine the degree of resistance, as do operating conditions and environment. In order to maximize a component's or process' efficiency, it is often desirable to minimize friction. |
Fretting corrosion | Micro-friction occurs on parts that are subjected to vibrations. This results in the formation of rust and abrasive steel particles, or fretting. |
Fire-resistant fluid | A lubricant used in high-temperature or hazardous hydraulic applications. The three most common types of fire-resistant fluids are water-petroleum oil emulsions, water-glycol fluids, and non-aqueous fluids of low volatility. |
Film strength | The ability of a lubricant to prevent metal parts from being scuffed or scored. |
Force feed lubrication | A lubrication system in which the lubricant is applied under pressure to the bearing surface. |
Full-fluid-film lubrication | A continuous lubricating film that completely separates two surfaces, as opposed to boundary lubrication. |
Graphite | A crystalline form of carbon with a laminar structure that is used as a lubricant. This can be a natural or synthetic type of material. |
Hydrostatic lubrication | A lubrication method in which lubricants are supplied under sufficient external pressure to form a fluid film between opposing surfaces. |
Hypoid gear lubricant | Gear lubricant with extreme pressure characteristics intended for use with hypoid gears, such as in differentials. |
ISO | International Standardization Organisation |
ISO viscosity grade | A number indicating the nominal viscosity of an industrial fluid lubricant at 40°C as defined by ISO Standard 3448. |
Journal | Describes the part of a shaft or axle that rotates or oscillates in or against a bearing or around which a bearing rotates or oscillates. |
Journal bearing | Bearings that move either rotatingly or oscillatorily in conjunction with journals. The bearing surface of a full or sleeve type journal bearing is 360° in extent. A partial bearing has a bearing surface that is less than 360° in extent. |
Kinematic viscosity | The time required for a fixed amount of an oil to flow through a capillary tube under the force of gravity. |
Lubricants | Lubricant is primarily used to reduce friction and wear between two sliding surfaces. In addition, they transport heat and contaminants away from the interface. Most lubricants consist of oil or grease and chemicals, called additives, which enhance the performance of the oil or grease. Lubricants may also be gases or solids depending on the application. |
Load-carrying capacity | The ability of a lubricant to form a film on a lubricated surface that resists rupture under certain load conditions. This is the maximum load the lubricated system can handle without failure or excessive wear. |
Lubricity | Efficacy of an oil or grease as a lubricant; also called film strength. |
Moly | Solid lubricant and friction reducer made of molybdenum disulfide dispersed in certain oils and greases or used by itself. |
Micron | One Micron is 0.0001 centimeters. Contaminant sizes are usually described in microns. A micron is exhibited as µm |
Newtonian fluid | The viscosity of a fluid at a given temperature is constant, regardless of the rate of shear. Single-grade oils are Newtonian fluids. Multigrade oils are non-Newtonian fluids since their viscosity changes with shear rate. |
Oiliness | A lubricant that produces low friction under boundary lubrication conditions. As friction decreases, oiliness increases. |
Oxidation stability | A lubricant's ability to resist natural degradation when in contact with oxygen. |
Polar compound | Compounds whose molecules display electrically positive characteristics at one end and negative characteristics at the other. A molecule's polarity gives it a high affinity for solid surfaces; these molecules act as lubricant additives (oiliness agents), forming a tenacious, friction-reducing film. They act as emulsifiers in lubricants, helping to form stable oil-water emulsions by being oil-soluble at one end and water-soluble at the other. Such lubricants are described as having good metal-wetting properties. |
Proactive maintenance | The routine detection and correction of root cause conditions that would otherwise lead to failure, a type of condition-based maintenance. High levels of lubricant contamination, alignment, and balance are among the most critical root causes. |
Ring lubrication | Lubrication system in which the lubricant is supplied to the bearing by an oil ring. |
Surface roughness | Surface roughness of two bodies can have a great impact on sliding interfaces. The roughness of a surface is typically measured using profilometry. Roughness affects friction and wear differently depending on the type of sliding. |
Stick-slip | Specifically, this occurs when the lubricant effect is insufficient for slow speed applications. During the early stages of the process, friction is higher, and as the speed of the process increases, friction decreases. |
Scuffing particles | Due to a complete breakdown of the lubricant film, twisted and discolored metallic particles result. |
Splash lubrication | In a lubrication system, parts of a mechanism dip into lubricant and splash it on themselves or other mechanisms. |
Synthetic lubricant | Chemically synthesized rather than extracted or refined from petroleum to produce a compound with predictable properties. |
Solvents | Substances that can dissolve other substances without changing their chemical composition. |
Synthetic oils | These oils are derived from chemical reactions. By increasing the chemical resistance or improving the temperature-viscosity relationship, their properties can be adjusted to suit the application. |
Thermal stability | Fuel or lubricant's ability to resist oxidation under high-temperature conditions. |
Thin film lubrication | An lubrication condition in which the friction between surfaces depends on both the properties of the surfaces and the viscosity of the lubricant. |
Thixotropy | The property of a lubricating grease manifested as a softening in consistency following shearing followed by a hardening in consistency after shearing is stopped. |
Tribology | Study of the lubrication, friction, and wear of surfaces in relative motion. |
Tribological wear | Tribological wear results from relative motion at the surface of an object. |
VCI (Vapour Phase Inhibitor) | Anticorrosive properties are improved with the use of this sustainable additive. |
Viscometer or Viscosimeter | Apparatus used to determine the viscosity of a fluid. |
Viscosity | A measure of a fluid's resistance to flow |
Viscosity- absolute | Ratio between shearing stress and shear rate of a fluid. Usually expressed in centipoises |
Viscosity- kinematic | It is measured as the difference between the absolute viscosity and the density of the fluid. Typically, it is expressed in centistokes. |
Viscosity- SUS | Saybolt Universal Seconds (SUS) are the number of seconds it takes for 60 milliliters of oil to flow through a standard orifice at a specified temperature. |
Viscosity- grade | A system of defining lubricants according to their viscosity for specific applications, such as industrial oils, gear oils, automotive engine oils, automotive gear oils, and aircraft piston engine oils. |
Viscosity- index (VI) | A measure of a fluid's change of viscosity with temperature. When the viscosity index is high, the relative change in viscosity with temperature is smaller. |
Viscosity index improvers | Viscosity-increasing additives for fluids throughout their useful temperature range. The additives are polymers with high molecular weight and thickening power, which are necessary for formulation of multi-grade engine oils. |
Viscosity modifier | A lubricant additive, usually a polymer with a high molecular weight, that reduces the tendency for an oil's viscosity to change with temperature. |
Viscous | A liquid with viscosity. A liquid with viscosity. Often used as a synonym for high viscosity. |
Wear | Wear is a loss of materials, usually caused by sliding. It is usually undesirable for wear to occur since it can increase friction and lead to component failure. Wear can be minimized by using a lubricant to separate the two bodies so that they don't directly touch. |
White oil | The oil is highly refined to remove the unpredictable components. Paraffinic mineral oil is its main component, and it is mostly used for medical purposes. |
ZDDP (Zinc dialkyldithiophosphate) | Usually found in hydraulic and lubricating fluids, this additive is used to prevent wear. |
This is the third part of a three-part series where we look at three main parts of tribology and the application of tribology in mechanics: