Semi-direct Acting Solenoid Valve
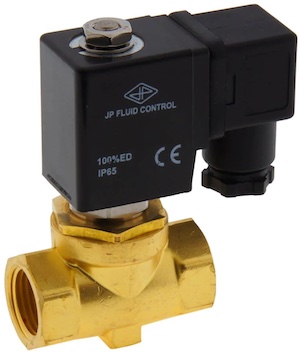
Figure 1: Semi-direct acting solenoid valve
A semi-direct acting solenoid valve can operate from zero bar and handle high flow rates, combining the features of both direct and indirect-acting solenoid valves. These valves are suitable for applications that require reliable operation across a range of pressures and flow rates. Semi-direct-acting solenoid valves are best suited for:
- Applications with varying pressures, starting from zero bar
- Situations requiring moderate to high flow rates
- Versatile applications due to their ability to handle different media
- Systems where a balance between quick response and high flow is needed
Read our article on solenoid valves for the construction, working, and applications of solenoid valves as a whole.
View our online selection of solenoid valves for fuel and oil!
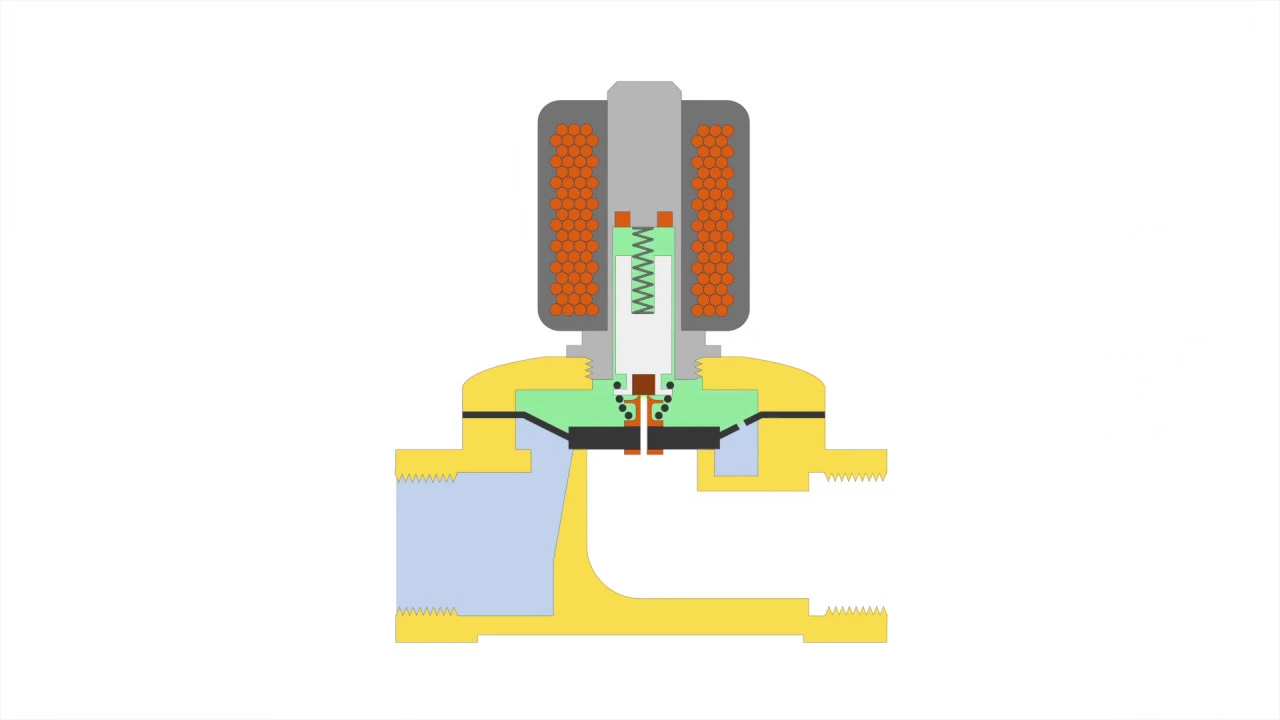
What is a semi-direct acting solenoid valve?
A semi-direct acting solenoid valve, also known as an assisted lift solenoid valve, combines the features of direct and indirect operated solenoid valves. The valve uses differential pressure to open and close, but unlike indirect acting valves, it can open from a zero bar differential pressure.
Construction
A semi-direct acting solenoid valve consists of two chambers separated by a flexible membrane (Figure 2 labeled E). A small hole in the membrane connects both chambers, resulting in equal pressure in both chambers. The surface area of the membrane in the upper chamber is larger than the surface area in the lower chamber. As a result, the membrane is pushed downwards against the valve seat, creating a reliable seal.
Working principle
When the solenoid coil (Figure 2 labeled F) is energized, a magnetic field is created that pulls the ferromagnetic plunger (Figure 2 labeled C) toward the center of the coil. The plunger connects to the membrane via a spring (Figure 2 labeled G), and this connected assembly lifts, opening the valve.
In addition, a small pilot port is opened, creating a connection between the upper chamber and the outlet, which lowers the pressure in the upper chamber. The resulting pressure differential on both sides of the membrane helps the membrane lift.
When the solenoid is de-energized, the plunger moves down, lowering the membrane and closing the pilot port. The pressure in the upper chamber rises, and the valve shuts off. Without the spring, the plunger would remain in the energized position, and the valve would be unable to function properly.
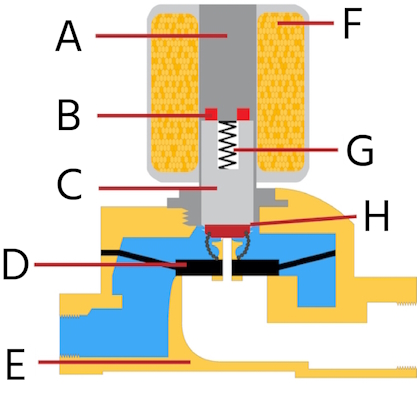
Figure 2: Semi-direct acting solenoid valve working principle and components: armature (A), shading ring (B), plunger (C), valve body (D), diaphragm or membrane (E), coil (F), spring (G), and seal (H).
Advantages
- Suitable for a broad range of pressure applications, from low to high-pressure systems, due to reliance on differential pressure.
- Energy-efficient design, as the valve stem is held in place by the valve seat, requiring minimal energy to operate.
- Powerful coils generate a strong magnetic field, allowing operation with shorter electrical pulses.
- Minimizes coil heating and extends the valve's service life.
- Ensures consistent performance even in fluctuating voltage conditions.
Disadvantages
A small opening in the diaphragm can cause clogging, especially if the working media contains debris. To prevent clogging, clean fluids or a y-strainer are required.
Comparison with other solenoid valve types
Choosing the correct solenoid valve type depends on the specific application requirements, such as the fluid type, flow rate, pressure, temperature, and environmental conditions. Table 1 summarizes the various factors to be considered while selecting between solenoid valve types.
Table 1: Comparison between direct acting, indirect acting, and semi-direct acting solenoid valves
Solenoid valve type | Pressure tolerance | Pressure Difference | Speed | Power consumption | Coil life | Flow capacity | Purity of media | Cost |
Direct acting | Suitable for low-pressure, zero, and negative pressures | No required pressure difference | Fast | High | Less | Low Kv from 0.2 to 6.4 |
Can handle more fluid debris than indirect or semi-direct, but a strainer is still advised. | Low initial cost for low flow rate systems, cost increases as the flow rate increases |
Indirect acting | High-pressure applications | Minimum pressure differential of 0.5 bar (7.3 psi) | Slow | Low | Medium | High Kv from 0.5 to 41 |
Debris can clog the diaphragm. Using a strainer can increase back pressure and reduce efficiency. | Economical for large flow rate systems |
Semidirect acting | Suitable for both low and high pressures | No pressure difference required | Medium | Low | High | High Kv from 0.6 to 41 |
Debris can clog the diaphragm. Mounting a strainer before the solenoid valve can avoid clogging. | Economical for large flow rate systems |
FAQ
What is the difference between a semi-direct solenoid valve and a direct-acting solenoid valve?
While both types of solenoid valves can perform without a pressure differential, semi-direct solenoid valves can operate at higher pressures than direct solenoid valves.