Indirect Acting Solenoid Valves
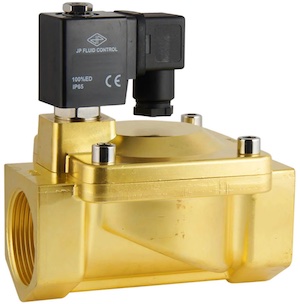
Figure 1: Indirect acting solenoid valve
An indirect acting solenoid valve uses the pressure difference across the valve ports to operate. The valve is suitable for applications with large pipe diameters, sufficient pressure differentials, and high flow rates, like irrigation systems.
The main advantages of pilot solenoid valves are:
- Higher flow rate capability compared to direct acting valves
- Pressure assists valve operation, resulting in lower power consumption
- Economical for applications with higher flow rates
- Can be frequently energized or operated for long periods without overheating
View our online selection of solenoid valves!
What is an indirect acting solenoid valve?
An indirect acting or pilot-operated solenoid valve uses a small pilot valve to control the flow of larger volumes of fluid. The valve has a rubber membrane or diaphragm that separates the inlet and outlet. The solenoid does not directly open or close this valve; instead, it controls the pressure that operates the valve. To lift the diaphragm and enable fluid to flow from the inlet to the outlet, there must be a minimum pressure difference of nearly 0.2 to 0.5 bar (3 to 7.2 psi) between the ports.
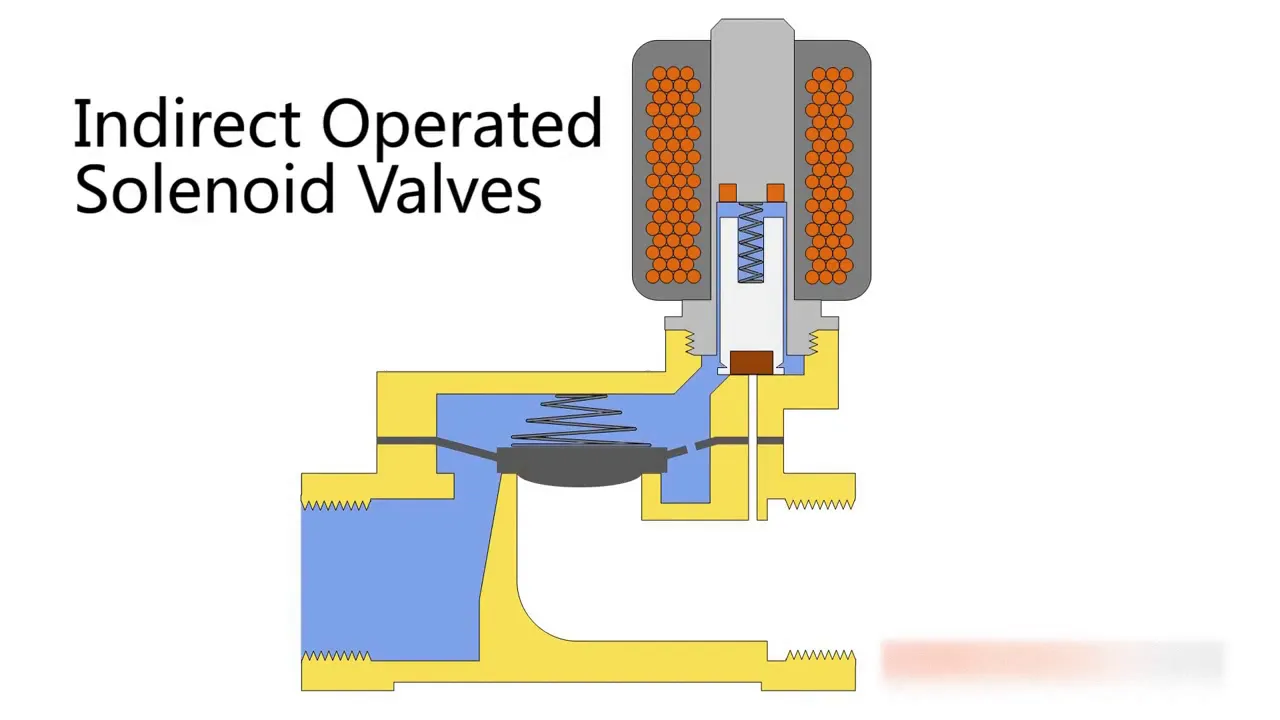
How an indirect acting solenoid valve works
A rubber diaphragm (Figure 2 labeled D) separates the inlet (Figure 2 labeled E) and outlet (Figure 2 labeled I) ports in an indirect acting solenoid valve. This diaphragm has a small hole that allows the medium to flow from the inlet side to the area above the diaphragm, balancing the pressure on both sides. However, the pressure above the diaphragm acts over a larger surface area, creating a downward force that keeps the diaphragm pressed against the valve seat, effectively closing the valve. A spring (Figure 2 labeled G) also assists in keeping the valve closed in a normally closed configuration.
When electric current flows through the solenoid coil, it generates a magnetic field that lifts the plunger. This movement opens a small pilot port, reducing the pressure above the diaphragm. As a result, the pressure from below pushes the diaphragm upward, lifting it off the valve seat. This action connects the inlet port to the outlet port, allowing flow through the valve.
Once the electric current stops, the pilot port closes, and the pressure above the diaphragm increases again, causing the valve to close. A normally open valve contains the same components but operates oppositely, where the diaphragm lifts to close the flow path when the solenoid is energized. Read our article on solenoid valve parts for more details on each solenoid valve part.
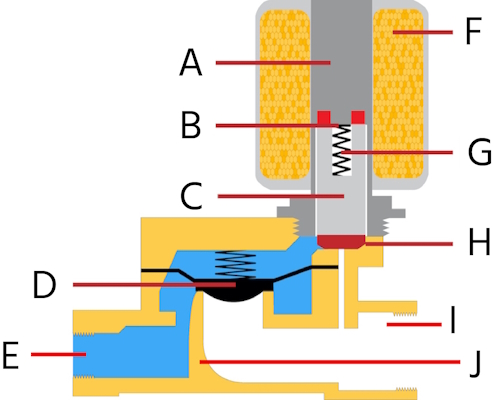
Figure 2: Indirect acting solenoid valve working principle and components: armature (A), shading ring (B), plunger (C), diaphragm (D), inlet port (E), coil (F), spring (G), seal (H), outlet port (I) and valve body (J).
Disadvantages
- Pressure difference: Indirect acting solenoid valves cannot operate without a pressure difference between the ports.
- Slow response time: Indirect acting valves rely on system fluid pressure to operate, which can take time to build up and actuate the valve.
- Leak-prone: The complex design with multiple components and sealing surfaces makes these valves more susceptible to leaks.
- Media purity: Impurities can block the pilot solenoid valve's smaller orifices, so pure media is essential to prevent clogs and malfunctions.
Read our articles on direct and semi-direct-acting solenoid valves for more details on their design, features, and typical applications.
Direct vs indirect and semi-direct solenoid valves
Direct acting solenoid valves are simple and fast-acting but limited to smaller flow rates and lower pressures. Indirect acting valves allow higher flow rates and pressures but slightly slower response times. Semi-direct acting solenoid valves balance the quick response of direct acting valves and the higher flow capacity of indirect types. Table 1 summarizes the various factors to consider when selecting solenoid valve types.
Table 1: Comparison between direct acting, pilot-operated, and semi-direct acting solenoid valves
Solenoid valve type | Pressure tolerance | Pressure difference | Speed | Typical power consumption | Coil life | Flow capacity | Purity of media | Cost |
Direct acting | Suitable for low-pressure, zero, and negative pressures | No required pressure difference | Fast | High | Less | Low | Can handle more fluid debris than indirect or semi-direct, but a strainer is still advised. | Low initial cost for low flow rate systems, cost increases as the flow rate increases |
Indirect acting | High-pressure applications | Minimum pressure differential of 0.5 bar (7.3 psi) | Slow | Low | Medium | High | Debris can clog the diaphragm. Using a strainer can increase back pressure and reduce efficiency. | Economical for large flow rate systems |
Semi-direct acting | Suitable for low and high pressures | No pressure difference required | Medium | Low | High | High | Debris can clog the diaphragm. Mounting a strainer before the solenoid valve can avoid clogging. | Economical for large flow rate systems |
FAQs
What is an indirect acting solenoid valve?
An indirect acting solenoid valve uses the solenoid to pilot a diaphragm or piston, controlling flow with the main valve. It requires a pressure differential to operate.
What is the difference between direct and indirect acting solenoid valves?
Direct acting solenoid valves use the solenoid to open/close the valve directly, working without pressure differential. Indirect valves need pressure to assist operation.