Solenoid Valves For Hazardous Applications
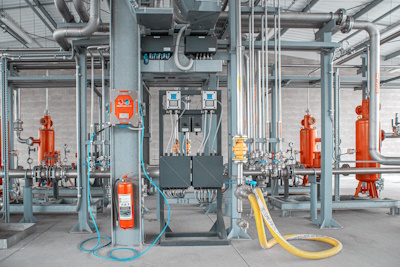
Figure 1: Solenoid valves help automate fluid flow in hazardous areas like petrochemical industries
Solenoid valves are vital for controlling fluid flow in hazardous environments such as chemical processing, oil and gas extraction, mining, and flammable fluid services. These applications, often containing flammable gasses, harmful vapors, corrosive fluids, and combustible dust, present significant risks due to the physical and chemical properties of the fluids, as well as the operating pressures and temperatures. Solenoid valves for these areas incorporate critical safety features to prevent explosions or media leaks while enabling precise and automated flow control. Key applications of solenoid valves for hazardous locations are:
- Regulating fluid flow in natural gas distribution systems
- Managing fluid flow in chemical processing plants, including the mixing and transfer of harmful chemicals
- Controlling volatile liquids in refineries, petrochemical facilities, and hydrocarbon storage tanks
- Chemical dosing in wastewater treatment plants
- Dust flow control in mining operations and grain storage silos
Table of contents
- Hazardous location classifications
- Solenoid valve issues in hazardous locations
- Design factors
- How to enhance the lifespan of solenoid valves in hazardous areas
View our online selection of solenoid valves!
Hazardous location classifications
Hazardous locations are areas where fire or explosion hazards exist due to flammable gasses, vapors, liquids, dust, or fibers. Different industries have specific standards and regulations, making it crucial to understand these guidelines to ensure the selected process equipment and valves provide adequate fluid control and conform to hazard classifications. For example, a solenoid valve designed for combustible dust may not be suitable for controlling hazardous vapors. Table 1 explains the main hazardous location classifications. Read our ATEX labeling article for more information on the safe selection and use of equipment in potentially explosive environments
Table 1: Hazardous location classifications for solenoid valves
Category | Type | Description | Examples |
Classes | Class I | Locations with flammable gasses or vapors | Refineries, gas plants |
Class II | Locations with explosive or ignitable dust | Grain elevators, flour mills | |
Class III | Locations with ignitable fibers | Textile mills, wood processing | |
Divisions | Division 1 | Hazard is expected | Hydrogen environment |
Division 2 | Hazard is unexpected | Leaking storage drum | |
Groups | Group A | Acetylene | - |
Group B | Hydrogen | - | |
Group C | Ethylene | - | |
Group D | Propane | - | |
Group E | Metal dusts | - | |
Group F | Coal dusts | - | |
Group G | Grain dusts | - |
Solenoid valve issues in hazardous locations
- Arcs and sparks: Solenoid valves can produce arcs and sparks during normal operation, which can ignite flammable atmospheres. This is particularly critical in hazardous locations where gasses, vapors, or dust are present.
- High temperatures: The coil of a solenoid valve can reach high temperatures. If these temperatures exceed the ignition point of the surrounding hazardous material, it can cause an explosion. The National Electrical Code (NEC) mandates special marking for solenoid valves with coil enclosure temperatures above 100°C (212°F).
- Electrical equipment failure: Failures such as burnouts or short circuits in the solenoid coil can also lead to ignition. Design standards for hazardous location equipment address these potential failures to prevent explosions.
Design factors
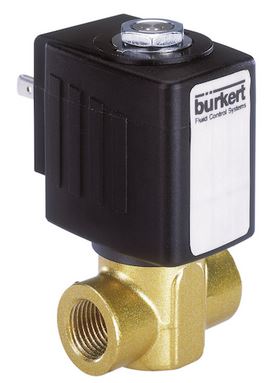
Figure 2: Burkert 6240 solenoid valve with explosion protection
-
Class I locations (Gasses/Vapors):
- Strength: The solenoid valve must be robust enough to contain an internal explosion. These valves feature explosion-proof enclosures for the coil and electrical components, sealed housings, or special venting mechanisms for added safety. The valve body walls must be thick to withstand internal pressure.
- Explosion-proof enclosure: The coil enclosure must be explosion-proof to prevent gasses or vapors from igniting if they enter the enclosure.
- Temperature control: The solenoid valve coil must operate at a temperature below the ignition temperature of the surrounding atmosphere.
- Flame paths: In some designs, there must be a way for burning gasses to escape the enclosure after being cooled to prevent ignition of the external atmosphere. This can be achieved through a ground surface flame path, where precisely ground and mated surfaces allow gasses to escape only after cooling, or through a threaded flame path, where gasses travel through threaded joints, cooling as they escape.
-
Class II locations (Dust):
- Dust sealing: The solenoid enclosure must prevent dust from entering to avoid internal explosions.
- Surface temperature: The enclosure's surface temperature must be below the ignition temperature of the dust.
- Dust blanket: The design must account for dust accumulation on the valve, which can cause it to overheat and ignite the surrounding atmosphere.
-
Class III locations (Fibers/Flyings):
- Fiber and flying prevention: The enclosure must minimize the entry of fibers and flyings and prevent the escape of sparks or hot particles.
- Temperature control: The solenoid valve must operate at a temperature that prevents the ignition of accumulated fibers.
- Multi-class suitability: Some solenoid valves are designed to meet the requirements of multiple classes. For example, a Class I solenoid valve that can contain an explosion must also prevent dust ingress to be suitable for Class II. The close tolerances required for flame paths in Class I valves can also keep dust out, eliminating the need for additional gaskets.
Other considerations
- Electrical considerations: Electrical circuits are designed to be intrinsically safe, using certified barriers or isolators to limit energy to non-ignitable levels, even in the event of a fault. Careful design minimizes electrical energy within the valve, reducing the risk of sparking, and addresses potential failures like burnouts or short circuits to prevent explosions.
- High quality materials: High-quality industrial solenoid valves feature corrosion-resistant valve bodies and internal components made from materials like Hastelloy, Inconel, or PTFE coatings. Robust external enclosures of stainless steel, plastic, or brass protect against environmental damage. Seals and gaskets made from Viton, EPDM, or Kalrez prevent leaks and ensure valve integrity, compatible with specific chemicals and temperatures in hazardous environments.
- Temperature and pressure ratings: Solenoid valves must operate reliably within a specified temperature range, using thermally insulated coils and temperature-resistant materials to prevent degradation. They are designed to withstand high pressures, including a safety margin, and are tested under real-world pressure spikes and fluctuations. The solenoid valve coil must operate below the ignition temperature of the surrounding atmosphere to prevent explosions. If coil temperatures exceed the ignition point of hazardous materials, it can cause an explosion.
- Fail-safe mechanisms: These valves are designed with fail-safe mechanisms, such as spring return or dual-coil configurations, to default to a safe position (open or closed) in the event of a power failure or fault. The electrical components are shielded to prevent electromagnetic interference (EMI) that could cause malfunction.
- Diagnostics and manual override: Advanced solenoid valves may include redundant coils or sensors to enhance reliability. Built-in diagnostics can monitor the health of the valve and provide early warning of potential issues, reducing the risk of unexpected failures. A manual override mechanism allows for manual operation of the valve in case of an electrical failure, designed to ensure that it does not compromise the explosion-proof integrity of the valve.
- Compliance with standards: The valve must meet industry standards and certifications for hazardous environments, such as UL, CE, ATEX, CSA, IECEx, NEMA, and IP ratings.
How to enhance the lifespan of solenoid valves in hazardous areas
To extend the lifespan of solenoid valves in hazardous applications, several measures can be implemented:
- Enhance surface finishes to prevent debris build-up and wear.
- Use additional surface finishes and material treatments to improve corrosion resistance.
- Perform rigorous compatibility and safety tests.
- Conduct regular inspections and maintenance to remove debris, identify worn seals, and replace damaged valves.