When To Use 304 or 316 Stainless Steel Ball Valves
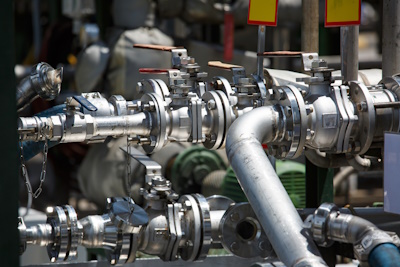
Figure 1: Stainless steel ball valves used in the chemical industry
Stainless steel ball valves, made from durable 304 or 316 stainless steel, control the flow of liquids and gasses across various industrial applications. Known for their robust construction and exceptional corrosion resistance, these valves are designed to perform efficiently under high-pressure conditions. This article explores the features, types, and applications of stainless steel ball valves.
Table of contents
- Stainless steel ball valve features
- What is a stainless steel ball valve
- Types of stainless steel ball valves
- Applications of stainless steel ball valves
- FAQs
View our online selection of stainless steel ball valves!
Stainless steel ball valve features
Stainless steel ball valves offer several key features that make them suitable for demanding environments:
- Corrosion resistance: Stainless steel can withstand corrosive media, including acids, alkalis, and saltwater. Stainless steel ball valves can handle aggressive acids in chemical processing plants, resist saltwater corrosion in marine environments, and manage alkaline solutions in wastewater treatment facilities.
- High temperature resistance: These valves maintain stable performance in high-temperature environments, making them suitable for industries such as petroleum refining, chemical processing, and power generation.
- Sanitary compliance: Stainless steel ball valves meet stringent sanitary standards, making them suitable for the food, pharmaceutical, and biotechnology industries. Their smooth surfaces are easy to clean and do not contaminate the fluid.
- High strength and durability: Stainless steel's high strength allows these valves to withstand high pressures and fluid flow rates, enhancing their lifespan and reliability.
- Ease of maintenance: The corrosion resistance of stainless steel reduces maintenance requirements, and its smooth surface facilitates cleaning and maintenance tasks.
However, stainless steel ball valves are heavy and costly, so they might be more than needed for simple applications. This can make the system more complicated and unnecessarily expensive. A simpler and cheaper material option (like brass or plastic) might be better in such cases.
Table 1: Comparing stainless steel ball valves with brass and plastic variants
Feature | Stainless steel ball valves | Brass ball valves | Plastic ball valves |
Material composition | Iron alloy with nickel and chromium (sometimes molybdenum) | Copper alloy with zinc and occasionally other metals | Typically PVC, CPVC, polypropylene, or polyethylene |
Cost | Higher than brass and plastic | Moderate | Generally low |
FDA approval | Approved for food and beverage use | Not FDA approved unless lead-free certified | Some plastics, like certain polypropylenes, are FDA-approved |
Softness | Harder, more challenging to seal | Softer, easy to seal, and machine | Soft, easy to machine, not suitable for welding |
Corrosion resistance | Excellent; ideal for corrosive environments | Moderate; better than plastic, less than stainless | Ideal for non-corrosive environments |
Pressure ratings | High (up to 130 bar/1886 psi) | Moderate (up to 80 bar/1160 psi) | Low (up to 10 bar/145 psi) |
Temperature resistance | High (220 𐩑C/428 𐩑F) | Moderate (160 𐩑C/320 𐩑F) | Limited (typically below 60 𐩑C/140 𐩑F, while some plastic variants can operate at higher temperatures) |
Durability | Very durable | Durable, but less than stainless steel | Less durable; prone to wear |
Applications | Chemical processing, marine, oil and gas, food processing, and high-temperature steam systems | Residential plumbing, HVAC systems, low-pressure gas lines | Irrigation systems, aquariums, low-pressure water applications; some FDA-approved plastics are used in food processing |
What is a stainless steel ball valve?
A stainless steel ball valve controls fluid flow using a spherical ball with a central hole. When the hole aligns with the pipeline, fluid can pass through; when the ball is rotated perpendicular to the flow, it stops the fluid. Stainless steel ball valves are primarily manufactured in two grades: 304 and 316. Both grades consist of at least 50% iron and 10% chromium, with additional elements that enhance their properties.
- 304 stainless steel: Comprising 18% chromium and 8% nickel, 304 stainless steel offers good corrosion resistance and is commonly used in the food and beverage industries and general-purpose applications.
- 316 stainless steel: In addition to 18% chromium and 8% nickel, 316 stainless steel contains 2% molybdenum, which significantly enhances its corrosion resistance, especially in marine environments.
Read our stainless steel 304 vs 316 article for more information on the characteristics of each steel type and their applications.
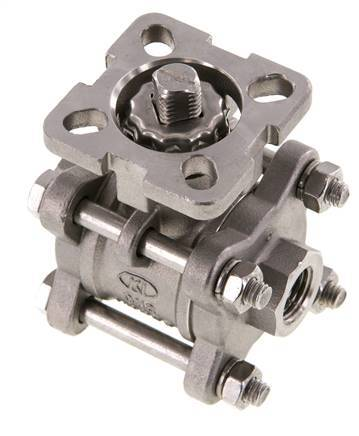
Figure 2: Two-way stainless steel 3-piece ball valve with ISO top
Applications of stainless steel ball valves
Stainless steel ball valves are used in various applications for their durability and resistance to harsh conditions.
Seawater environments
In marine applications like desalination plants, stainless steel ball valves are crucial for handling high pressures and extreme temperatures. The corrosive nature of seawater requires durable materials, and 316-grade stainless steel is ideal due to its excellent corrosion resistance. These valves ensure reliable performance in saltwater environments, making them perfect for desalination and offshore platforms.
Brewing systems
In breweries, stainless steel ball valves are crucial for controlling liquid flow during brewing. They are commonly used on kettles to manage the transfer of wort, a corrosive liquid produced during mashing. The high temperatures encountered in brewing necessitate using stainless steel, as plastic valves cannot withstand such conditions. Three-part stainless steel ball valves are used in brewing systems for their ease of cleaning and maintenance.
Chemical processing
Stainless steel ball valves handle corrosive chemicals like acids, bases, and harsh salts in chemical plants. Their corrosion resistance and durability make them ideal for chemical transfer, mixing, and blending. These valves provide precise flow control, ensuring accurate dosing and mixing. Their robust construction ensures reliability in demanding environments, making them a preferred choice for chemical applications.
Food and beverage industry
In the food and beverage industry, sanitary stainless steel ball valves are essential for maintaining strict hygiene standards. They are widely used in dairy and bottling processes due to their smooth surfaces, which prevent contamination and facilitate easy cleaning. These valves ensure high sanitation levels and are safe for food products, making them ideal for dairy, beer, beverage, and general food processing applications.
FAQs
Are stainless steel valves better?
Stainless steel valves are often considered superior due to their excellent corrosion resistance, durability, and ability to withstand high temperatures and pressures. However, they can be costly.
What is the use of a stainless steel ball valve?
Due to their robust construction and suitability for high pressures, stainless steel ball valves control the flow of fluids in various industries, including chemical processing, food and beverage, and water treatment.
Which stainless steel is more durable, 304 or 316?
316 stainless steel is more durable than 304 because it is more resistant to corrosion, especially in harsh environments, due to the addition of molybdenum.
What is a stainless steel 304 ball valve used for?
A stainless steel 304 ball valve is used for general-purpose applications. It is highly corrosion-resistant, making it suitable for industries such as food and beverage.
What is a high pressure stainless steel ball valve?
A high pressure stainless steel ball valve is designed to withstand high-pressure environments, ensuring safe and reliable fluid control in industrial applications.
What is a stainless steel motorized ball valve?
A stainless steel motorized ball valve uses an electric actuator for automated control, which is ideal for applications requiring remote operation and precise flow management.