Guide to Steam Hoses: Uses, Types, and Maintenance
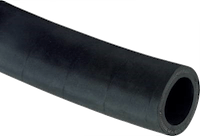
Figure 1: Steam hose
Steam hoses are specialized rubber hoses created to transport steam to and from different locations within a process. These hoses are typically constructed from synthetic Ethylene Propylene Diene Terpolymer (EPDM) rubber because of its outstanding resistance to heat, water, steam, acids and alkalis, ozone, and sunlight. This article discusses the various types of steam hoses, how to choose them for specific applications, and the common uses they serve. Discover more about using steam hoses in our recommendations for using steam hoses article.
Table of contents
- Types of steam
- Types of steam hoses
- Steam hose construction
- How to select a steam hose
- Points of attention
- Common applications
- FAQs
View our online selection of Hoses!
Types of steam
Steam is classified based on its temperature, pressure, and moisture content. There are three types of steam: dry steam, wet steam, and superheated steam.
- Dry steam: Also known as saturated steam, dry steam is when steam is at the highest possible temperature for a given pressure. It is used in power generation, sterilization, heat exchange, and food processing. Dry steam does not contain water droplets.
- Wet steam: Wet steam contains water droplets and has a lower temperature and pressure than dry steam. This type of steam is normal for heating systems, humidification, and applications that do not need high steam quality.
- Superheated steam: When heated above saturation temperature, steam becomes superheated steam. It is used in power plants, steam turbines, and high-temperature industrial processes due to its ability to transfer heat without condensing.
Types of steam pressure hoses
ISO 6134 has classified steam pressure hoses to convey saturated (dry) steam and hot water condensate into two types:
- Low-pressure steam hose
- Corresponding temperature: 164 °C (327.2 °F)
- Maximum working pressure: 6 bar (87 psi)
- High-pressure steam hose
- Corresponding temperature: 210 °C (410 °F)
- Maximum working pressure: 18 bar (261.06 psi)
These two types of hoses are further classified into hoses with an oil-resistant cover or non-oil-resistant cover.
Oil-resistant cover
Oil-resistant steam hoses (Figure 2) suffer little or no degradation when exposed to oil.
- Working temperature: These hoses are typically designed to withstand high temperatures up to 207 °C (406 °F) for saturated steam and 232 °C (450 °F) for superheated steam.
- Applications: Steam hoses with oil-resistant covers are used in chemical plants, refineries, and processing factories where there is a chance for the steam hose to be in contact with oil.
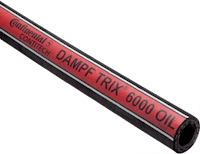
Figure 2: Oil-resistant cover steam hose
Non-oil-resistant cover
Non-oil-resistant steam hoses are prone to damage if exposed to oils.
-
Working temperature: Although the max working temperature varies by manufacturer, non-oil-resistant steam hoses typically have a lower max working temperature than oil-resistant steam hoses.
- This is especially true in processes exposed to hydrocarbons, like diesel-based inverted muds, lubricants, and cleaners. Under such exposure, these non-oil-resistant covers soften and swell, causing them to tear. As a result, the hose gets exposed to moisture, initiating corrosion and losing its ability to contain pressure.
- Service life: Non-oil-resistant steam hoses have a longer service life than oil-resistant steam hoses.
- Applications: Non-oil-resistant steam hoses are designed for general applications like moisturization and heating (discussed later in the article).
Steam hose construction
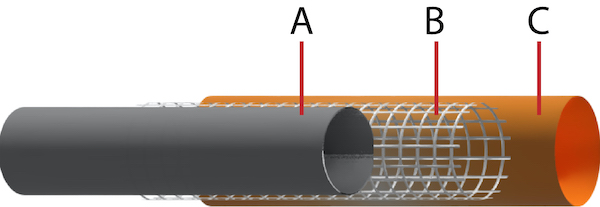
Figure 3: The parts of a steam hose: tube (A), reinforcement layer (B), and cover (C).
Steam hoses are suitable for transferring high-temperature steam due to their construction. A normal steam hose consists of three parts: tube (Figure 3 labeled A), reinforcement layer (Figure 3 labeled B), and cover (Figure 3 labeled C).
- Tube: The tube is the innermost layer and is often composed of EPDM due to its resistance to high temperature and additives. However, these tubes do not have resistances to many chemicals, such as petroleum products. To learn more about the chemical resistances of a steam hose's tube, read our hosing and tube material article.
- Reinforcement layer: The reinforcement layer is composed of one or two layers of braided or spiral steel wire. It ensures a solid structure, increases the hose's max operating pressure, and helps to eliminate static charges.
- Cover: The cover is made from EPDM or chlorobutyl and protects the hose from corrosion, aging, the environment, chemicals, and high temperatures. The cover also protects against mechanical damage such as bursting, cracking, and accidental exposure to flame.
How to select a steam hose
Selecting a steam hose for an application requires careful consideration. The main selection criteria are:
- Dimensions: Determine the desired length and inside/outside diameter required for the application.
- Operating range: The type of steam being worked with (dry, wet, or superheated) will determine the choice of steam hose.
- Temperature: Ensure that the steam hose can withstand the maximum temperature it will be exposed to.
- Pressure: Ensure that the steam hose can withstand the maximum pressure and, if necessary, additional pressure. Typically, a steam hose has a built-in factor of safety (usually 10:1), but this should not be considered when sizing a hose. The maximum pressure of the hose should never be exceeded.
- Material: Ensure that the material is resistant to heat, water, and steam and does not react with the fluid or chemicals it will be exposed to.
-
Other working conditions of the hose: Always select a hose that matches its working conditions:
- Frequency of use (whether the hose is used occasionally or continuously)
- Whether the hose requires manual handling or not
- The configuration of the hose (whether bent or straight) while working under pressure
- External working conditions of the site where the hose works (check for the possibility of mechanical knockouts or spilled chemicals in the vicinity)
Points of attention
Steam can be dangerous and costly to work with. However, as discussed later, it is also a vital driving force of many industrial processes. Therefore, special attention must be given when selecting, installing, and fitting steam hoses. The following points require attention to prevent damage, problems, and increase the life of a steam hose.
Superheated steam vulcanization
Due to its high temperature and dry nature, superheated steam may harden the inner rubber surface of the steam hose, known as vulcanization. Vulcanization reduces the service life of the rubber. Figure 5 shows saturated steam being transformed into superheated steam. A steam line at a pressure of 18 bar and 210 °C contains saturated steam. If the steam expands and its pressure reduces (but the temperature remains constant or increases), such as when the steam suddenly passes through a larger hose or the sudden opening of a steam valve, the steam becomes superheated. This condition does not last for long, but the superheated steam tends to deteriorate the tube stock in an ordinary steam hose intended for use with saturated steam. This results in steam hose failure in the long run.
.jpg)
Figure 4: Saturated steam (A) occurs when the temperature of saturated steam (B) increases past a certain point or the pressure decreases while the temperature remains constant or increases. Below the saturated steam line is hot water (C).
Popcorning
The inner layer of a steam hose may absorb water or water vapor during use. Once the hose cools down, the trapped steam condenses to water inside the rubber hose. When the hose is used subsequently, the trapped water expands considerably, creating air bubbles in the inner wall. As a result, blisters are formed on the inner wall, blocking and contaminating the steam with rubber pieces. The damage thus caused is called popcorning.
One of the measures to prevent steam hoses from popcorning is to blow dry them after each use. But it is time-consuming and rarely done, increasing the risk. Steam hoses with extruded inner walls can also avoid this problem. These extruded inner walls are made from gas-tight rubber and are seamless and homogeneous. So, the water vapor cannot penetrate the walls, thus preventing popcorning.
Rusting inlays
Steel inlays are fitted into steam hoses as a standard practice. Due to the porous inner wall in these rubber hoses, steam comes into contact with the steel inlays, leading to corrosion. Since the corrosion occurs beneath the surface, the damage may stay hidden, leading to dangerous consequences. The weakening and cracking create escape ways for the steam without any warning. In such a situation, if the pressure is increased to maintain a constant flow of steam, the risk of bursting a hose increases, which can be dangerous.
Galvanized steel inlays are used to avoid such a situation. They are resistant to rust, thus increasing the safety and service life of the steam hose. Other advantages of galvanized steel inlays include a reduction of the cost that may incur from steam loss.
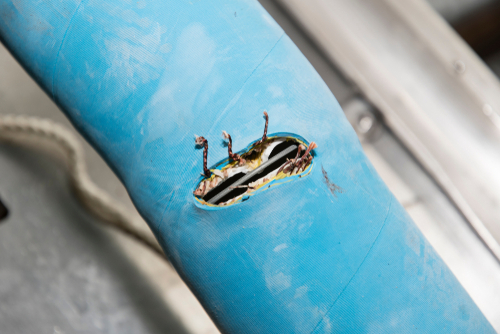
Figure 5: Rusting of steel inlays
Common applications
Steam is used for various applications in a wide range of industries. According to the requirement, steam hoses are used to channel dry, wet, or superheated steam for these applications. Some of the common industrial applications are discussed below.
-
Heating
- Food processing factories use steam as a heat source and for sterilization processes.
- Refineries use steam as a heat source for lubricating and increasing flow for tank and vessel cleaning.
- Process fluid heat exchangers, reboilers, reactors, combustion air preheaters, and other heat transfer equipment use saturated steam as a heating source.
-
Steam turbine
- Steam turbines (Figure 7) use steam as a driving force for propulsion applications. These turbines are used in thermal electric power plants to generate electricity.
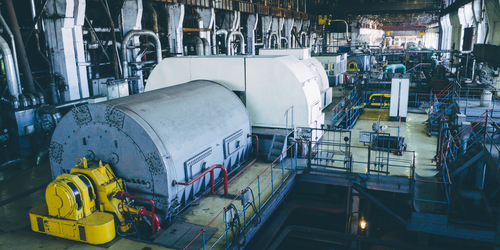
Figure 6: Steam turbines in a power plant
-
Cleaning
- Soot blowers, and other such steam cleaners, use steam for intensive cleaning.
-
Moisturization
- The paper production industry and pellet mills use steam as a source of moisture and heat.
-
Humidification
- Steam humidifiers inject dry saturated steam into spaces warmed by HVAC coils, which drop air humidity. This injection of steam balances the humidity in the space, providing comfort and infection control.
- Steam atomization: Steam atomization mechanically separates fluid using steam. Oil burners use this process to maximize combustion and minimize soot production.
-
Motive fluid
- Steam can force the movement of other fluids in piping.
FAQs
What is a steam hose used for?
Steam hoses transfer steam or hot water from one point to another. Many processes use this transfer for applications such as heating, cleaning, and humidification.
What are steam hoses made of?
It's common for steam hoses to be made of EPDM because of its high resistance to heat and pressure. Many steam hoses also have a steel inlay to provide tensile strength.