Anti-Corrosion Measures For Valves
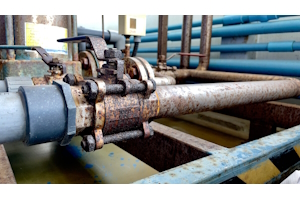
Figure 1: Rust on a stainless steel valve caused by proximity to acid fumes
Preventing corrosion is crucial to maintaining the integrity and longevity of valves. Corrosion can lead to significant problems, including leaks, reduced efficiency, and system failures. Good anti-corrosion measures ensure things work well, lower repair costs, and stop sudden breakdowns. This is important in factories where valves face tough, corrosive conditions and substances.
This article covers various anti-corrosion measures for valves, including material selection, protective coatings, environmental controls, and regular maintenance practices. Each section provides practical insights and recommendations to help extend the life of valves and ensure optimal performance.
Table of contents
- Understanding valve corrosion
- Materials for corrosion-resistant valves
- Common anti-corrosion measures
- Preventive maintenance and best practices
View our online selection of valves!
Understanding valve corrosion
Valve corrosion is the slow damage of the valve body and other parts caused by chemical reactions with their surroundings. This process can be accelerated by factors such as moisture, chemicals, and extreme temperatures.
- Chemical exposure: Valves often come into contact with corrosive chemicals, which can be highly corrosive when reacting with the valve material.
- Moisture: Water and humidity can accelerate corrosion, especially in valves made from metals susceptible to rust.
- Temperature extremes: High temperatures can increase the rate of chemical reactions, while low temperatures can cause condensation, both of which contribute to corrosion.
- Electrochemical reactions: Galvanic corrosion occurs when two different metals are in contact with an electrolyte, leading to accelerated corrosion of one of the metals.
Types of valve corrosion
Table 1 overviews the most common types of corrosion.
Table 1: Common corrosion types
Type of corrosion | Description | Common examples |
Chemical corrosion | Occurs when the valve material reacts directly with chemicals in the environment, leading to material degradation. (Figure 2 left) | Oxidation, acid attack |
Electrochemical corrosion | Involves an electrochemical reaction between two dissimilar metals in the presence of an electrolyte, causing one of the metals to corrode more rapidly. (Figure 2 middle) | Galvanic corrosion |
Physical corrosion | Includes wear and tear due to physical factors such as abrasion, erosion, and cavitation, which can remove protective layers and expose the underlying material to corrosive elements. (Figure 2 right) | Abrasion, erosion, cavitation |
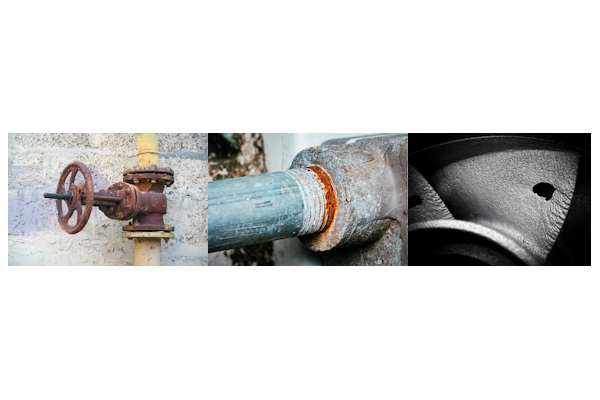
Figure 2: A rusty gate valve (chemical corrosion) (left), a galvanized pipe (electrochemical corrosion) (middle), and a cavitated propeller (physical corrosion) (right).
Materials for corrosion-resistant valves
Stainless steel
Manufacturers widely use stainless steel, particularly grades 304 and 316, for high corrosion-resistant valves.
- 304 stainless steel: This grade offers good corrosion resistance and is suitable for a wide range of applications. It contains 18% chromium and 8% nickel, which provide its anti-corrosive properties. However, it may not be ideal for environments with high chloride exposure.
- 316 stainless steel: This grade includes 2-3% molybdenum, which enhances its resistance to chlorides and other corrosive agents. Operators often use it in marine environments and industries where exposure to harsh chemicals is common.
Brass
Brass is a mix of copper and zinc that resists corrosion well, especially in water and mild chemicals. Brass valves are durable, easy to make, and popular in many industries. However, a common brass valve corrosion, dezincification, can occur, especially in brass with over 15% zinc. So choose brass components with less than 15% zinc, use special coatings, or control the environment (see below).
Plastic
Plastic materials like PVC (Polyvinyl Chloride) resist many chemicals, including acids and alkalis. PVC is lightweight, easy to install, and affordable. Operators often use plastic valves in water treatment, chemical processing, and irrigation systems. Because they are non-metallic, they do not suffer from electrochemical corrosion, making them durable in tough conditions.
Common anti-corrosion measures
Choosing the right material
Choosing the right material is key to reducing valve corrosion (see above section). Materials like stainless steel (304, 316), brass, and PVC resist corrosion well. The choice depends on the environment and substances the valve will face. For example, 316 stainless steel is great for marine environments because it resists chlorides, while PVC is good for chemical processing.
Surface treatments
Surface treatments are essential for enhancing the corrosion resistance of valve materials. Common options include:
- Hot-dip galvanizing: This process covers the valve with zinc by dipping it in hot, melted zinc. The zinc layer protects the metal underneath from rust. Hot-dip galvanizing works well for steel valves used outside or in the sea.
- Anodizing: This process thickens the natural oxide layer on metal valves, usually aluminum. Anodizing helps the metal resist rust and wear. It also allows adding color for identification or looks.
Coating methods
Coating methods are another effective way to protect valves from corrosion. Common coating options include:
- Epoxy coatings: Epoxy coatings create a strong, chemical-resistant layer that protects the valve from rust. They are applied as a liquid and then hardened to form a tough shield. Epoxy coatings are good for many uses, like water treatment and chemical processing.
- PTFE coatings: Polytetrafluoroethylene (PTFE) coatings, or Teflon coatings, resist chemicals well and have low friction. They work well in places with strong chemicals and high heat. PTFE coatings create a non-stick surface, which helps prevent deposits from building up on the valve.
- Polyamide coatings: Polyamide coatings protect valves from rust and wear. They form a strong layer on the metal, making it last longer. Polyamide coatings are good for cast iron parts and help them work well in different environments.
Preventive maintenance and best practices
Table 2 provides a comprehensive list of best valve maintenance practices that minimize the possibility of corrosion.
Table 2: Best practices for anti-corrosion valve maintenance
Preventive maintenance and best practices | Details |
---|---|
Routine inspections | Routine inspections are critical for identifying early signs of corrosion, wear, or damage in valves. |
Visual signs of corrosion | Look for rust, discoloration, or pitting on the valve surface. |
Leakage | Inspect for any signs of leaks around the valve seals and connections. |
Smooth operation | Ensure the valve operates smoothly without excessive force or resistance. |
Protective coatings and linings | Examine the condition of any coatings or linings for signs of wear or degradation. |
Effective cleaning methods |
|
Protective covers and environmental factors |
|
Corrosion inhibitors |
|
FAQs
What is valve corrosion?
Valve corrosion is the gradual degradation of valve materials due to chemical reactions with their environment, leading to leaks and failures.
How can corrosion resistant valves help?
Corrosion resistant valves are designed with materials and coatings that withstand corrosive environments, enhancing longevity and performance.
What causes brass valve corrosion?
Brass valve corrosion is often caused by exposure to chlorides, acidic environments, or dezincification, where zinc leaches out, weakening the valve.
How can you prevent valve corrosion?
Prevent valve corrosion by selecting appropriate materials, applying protective coatings, controlling the environment, and conducting regular maintenance.